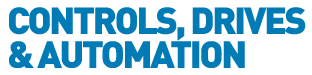
![]() |
Charlotte Stonestreet
Managing Editor |
Teaching the fundamentals of a greener future
05 December 2023
ABB's David Bowers and Roy Tanner explain how ABB automation and measurement technologies are being used at Imperial College London to create new skillsets that will help to achieve cleaner, greener and more efficient industrial processes.

WHY DID ABB become involved with Imperial College London’s carbon capture facility?
We saw the project as an ideal opportunity to raise awareness among chemical engineering graduates of the benefits of a career in control and instrumentation engineering.
Since it opened in 2012, the plant has proven to be a great shop window for presenting the opportunities available not just in chemical and process engineering, but also within ABB itself. In the same way as other industrial companies, one of our biggest problems is finding enough suitably qualified engineers to fill the ever-growing range of opportunities we can offer. Today, our team includes people who were educated at the Imperial College facility and came to us as a direct result of their experience of using our technology.
Filling the skills gap was a key part of our decision to get involved in the project and forms a continuing justification for our decision to extend our involvement with Imperial College for a further 10 years. Recent estimates from EngineeringUK indicate that the UK still faces a yearly shortfall of 203,000 skilled engineers. If this is not addressed, it will potentially have a widespread impact on everything from innovation through to economic growth.
Part of the problem is that the contribution that engineering makes to society often gets taken for granted and goes largely un-noticed. If we are to rebuild the manufacturing base of the UK, we need to re-establish the awareness of the important contribution that engineering makes to people’s everyday lives. The UK needs to increase its base of skilled engineers if it is to grow its manufacturing sector towards its potential. We believe that the pilot plant supports education by giving tomorrow’s engineers hands-on exposure to real-life technology. This pilot plant really brings the real world into the classroom for the first time.
Which ABB technologies are used at the plant?
The plant uses an extensive array of the same ABB products and systems that can be found in use across a broad range of industrial applications. From a measurement perspective, around 250 instruments and analysers measuring parameters including temperature, pressure, flow, level, and pH, are fed to ABB’s System 800xA control system, which forms the heart of the plant’s control room. Combining the functions of a Distributed Control System, Electrical Control System, Safety system and a collaboration enabler, the System 800xA provides students with an environment from where they can monitor and access real time data on all aspects of the plant.
The plant has been deliberately designed to use more instruments than you’d find on a typical industrial plant in order to give students a fully rounded understanding of different measurement techniques and the impact they can have on measured values. For example, electromagnetic and swirl flowmeters are used in one part of the plant to enable students to compare the different techniques and the impact this can have on assessing plant performance.
In a similar way, the plant also uses a variety of communications protocols, including Foundation Fieldbus, Profibus DP, Profibus PA and Wireless HART, to relay data from the instruments to the plant control system. Again, the aim here is to provide students with a full understanding of the variety of options they may encounter in their future careers and enable them to evaluate the merits and potential drawbacks of each one.
The plant also reflects recent developments in digital service technology, with the addition of our digital service software tools including ABB Ability Verification for measurement devices and our new ABB Ability SmartMaster verification and condition monitoring platform. Together, these tools are used to teach students about the extended possibilities for device optimisation and maintenance. Using the software, they can access and interrogate data on instrument status and identify in advance any potential issues that could affect measurement performance or result in unplanned downtime.
How are these technologies being used to teach students?
The Imperial College courses make full use of the ABB technology on the plant to provide students with knowledge covering everything from running different experiments and process scenarios through to handling alarms and responding to process emergencies. Students are able to work with the technologies, using the same functions and interactions as engineering teams responsible for the operation and maintenance of real-life process plants.
While the plant is primarily used as a way of teaching about carbon capture, many of the fundamental aspects of its operation can also be used to provide students with the skills needed to run other types of process plants.
By providing a realistic environment for students to both observe and operate process technologies such as our instruments, control system and other products including motors, variable speed drives and process controllers, the plant provides a valuable way of equipping them with the skills they will need in an engineering career.
Can you give examples of some of the ABB digital technologies that are used at the plant?
A key challenge for process operators will often be around managing the sheer volume of instruments that are likely to be installed on any given plant. Many plants will typically feature hundreds or even thousands of devices, some of which may be installed in hard to reach or hazardous areas.
To teach the skills needed to handle device management, the plant uses ABB’s digital service tools to demonstrate the possibilities for remote monitoring and optimisation of instrument performance.
ABB Ability Verification for measurement devices is the next generation verification tool suite for use with a range of ABB devices. It was developed to meet the growing desire for a way to verify instrument performance, which is key for ensuring continued accuracy and reduced downtime, as well as meeting regulatory and quality management system requirements.
The tool verifies the condition and performance of the device under test, comparing its current performance against the original fingerprint of the device taken when it was shipped from our factory. In this way, all verifications performed in the field can be compared with the fingerprint data and any previous tests to ensure device performance has not degraded.
An added complication in many applications will also be the diversity of the instruments being used. Devices will often be of different makes and ages and will frequently use different operating principles, making gathering and analysing data difficult. This can particularly be the case when trying to assess the maintenance status of a particular device or group of devices.
ABB Ability SmartMaster verification and condition monitoring platform is an asset performance management (APM) tool that is used to teach students how to gather and analyse diagnostic data from instruments. SmartMaster is a solution which verifies device diagnostic data remotely via a developed platform, without interrupting current measurement tasks.
Based on a prescribed schedule, it collects data remotely from field devices to conduct condition monitoring. Using the tool, students can gain an insight into how the data can be used to plan service operations, as well as order spare part orders and device replacement.
Another example of a digital tool used by the plant is the QR code on the CO2 gas analyser. By scanning this code with a smartphone, an operator can send diagnostic data to an ABB expert who can analyse it and advise on potential fixes, opening new possibilities for troubleshooting and fault resolution.
Key Points
- Filling the skills gap was a key part of ABB's becoming involved with Imperial College London’s carbon capture facility
- The UK needs to increase its base of skilled engineers if it is to grow its manufacturing sector towards its potential
- The plant uses an extensive array of the same ABB products and systems from a range of industrial applications