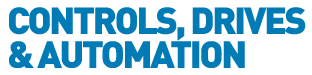
![]() |
Charlotte Stonestreet
Managing Editor |
Preventing production bottlenecks
11 August 2022
An ABB solution comprising motors, VSDs, servo drives, PLCs and robotics has automated the process by which embossed metal badges are affixed to bottles at a West Yorkshire glass manufacturer

A DECORATIVE glass manufacturer which manufactures bottles for some of the UK’s prestige whisky brands has dramatically increased productivity and efficiency by automating a key part of the bottling process. A machine which applies metal badges to the glass bottles was designed and built by Barnsley-based ABB Value Provider SMS Machine Automation.
To the human eye, each bottle looks identical, yet each one is unique at a microscopic level, affecting the quality of adhesion. Any human handling of the bottles would leave surface grease which affected the bond between badge and bottle. Refrigerating bottles also increased the likelihood of the badge coming loose.
SMS Machine Automation was asked to develop a bespoke machine to improve both throughput and quality of the badge application process. The machine performs a complete application of the metal badge to the glass bottle, including smart indexing of the bottle, cleaning of the bottle and badges, and orientation of the badge into position ready for application.
Meanwhile, the surface of the bottle is cleaned using plasma, and an adhesive then immediately applied to the glass. The badge is lasered to remove any oxide coating, and the adhesive is then cured using UV light. The system includes a rotary table, with its rotation controlled by an ABB motor and ABB E180 Servo Drive, while an ABB robot orientates the bottles into position. The overall process is governed by an ABB PLC. The machine is roughly 2.5m in diameter, with input and output conveyors for feeding bottles into and out of the machine.
The machine has reduced the amount of human interaction required, eliminating the chance of anything but a perfect application of badge to bottle. Where previously badges were applied by hand – a time-consuming and labour-intensive process – the machine can now affix one badge every three seconds, or 20 every minute. Personnel operating the machine can now concentrate more on quality, as even microscopic defects can be detected by the machine and removed from the production line.
Gordon Watson, director, SMS Automation, explains how the intricacy of the process, and the inconsistent nature of the glass surfaces, presented challenges in developing a reliable solution: “Glass bottles are not unique in dimensions, and have minor size imperfections from bottle to bottle, while residue from manufacture or handling can create issues when using adhesives. For this project we had to develop special processes to ensure maximum reliability, for instance cleaning the back of the badge prior to application, and using UV light to cure the glue once on the bottle. Since installation the machine has substantially increased both throughput and product quality, and the customer has since bought a second version of the machine to keep pace with rising product demand.”
Established in 1999, SMS has for the past 20 years provided engineering solutions for machine building, system integration and automation component distribution for a range of industry sectors. Simon Wakefield, marketing and communications lead, SMS, describes the company’s broad customer base: “We provide standard components and custom solutions for a wide range of industries, from nuclear fuel production and premium chocolate manufacturing to glass bottle embellishment, and even automotive and entertainment applications.”
According to Carl Eely, product manager industrial automation, ABB, providing a single solution was a major benefit for the customer: “ABB has historically had a strong relationship with SMS, but this was one of the first projects where we were able to introduce the company to our PLC portfolio. Having a single solution using a wide variety of components from one vendor makes maintenance very straightforward, and allowed for seamless integration throughout the system.”
Key Points
- SMS Machine Automation has developed a bespoke machine to improve throughput and quality of badge application process
- The system includes a rotary table, with its rotation controlled by an ABB motor and ABB E180 Servo Drive
- An ABB robot orientates the bottles into position, and the overall process is governed by an ABB PLC
- Protect your drive with ABB’s preventive maintenance service
- The water industry’s silent challenge
- Vitens selects ABB to develop new process automation system
- Driving smart manufacturing in China's automotive industry
- MPs learn how to leverage digitalisation
- Control system security in-demand
- Building cybersecurity through secure drives
- ABB acquires R&D engineering company
- ABB & Dassault Systèmes enter global software partnership for digital industries
- Virtual summit warns against cyber attack complacency