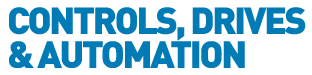
![]() |
Charlotte Stonestreet
Managing Editor |
Home> | AUTOMATION | >Robots | >Competitiveness makes the cut |
Editor's Pick
Competitiveness makes the cut
27 April 2022
THANKS TO collaborative robot solutions, leading manufacturer of outdoor power products, Husqvarna has increased flexibility and become more cost-effective across its manufacturing line

For over 60 years, Husqvarna has established a reputation for high performance, user-friendliness and safety, for its range of chainsaws for forestry, agriculture and horticulture.
To ensure its continued success and enable it to keep ahead of its competitors, Husqvarna constantly looks for new ways to manufacture its products. In 2018, the company decided to upgrade the part of the production process where the chainsaw starter is mounted to make it faster, more flexible and less prone to errors that could result in disruption and potential wastage.
To achieve this, the company made the decision to add collaborative robots to work alongside production operators on its manufacturing line, providing added flexibility and allowing the workers to be deployed to higher level tasks.
"We wanted a flexible collaborative solution that we could run relatively quickly whilst providing the flexibility to expand our operations or change tasks in the future," says Jimmie Sollén, technical manager at Husqvarna.
Production improvement
After analysing alternative solutions, Husqvarna chose ABB’s YuMi dual-arm collaborative robot, which now works side-by-side with operators on the assembly line, handling the task of picking screws and screwdriving them into the chainsaw to attach the starter.
Now being used to help produce over 400 chainsaws per shift, YuMi has brought several benefits, including higher repeatability and fewer deviations in the assembly process. In addition, the robot has improved operators' working environment, as it reduces ergonomic problems due to repetitive screwing.
"This is a much better and more reliable solution than the one we had before,” says Sollén. “The robot helps to relieve our operators from handling what can be a very tedious task. If a problem does occur, it is also quite easy for our production line team leaders to intervene and reset the process. Thanks to YuMi, we get much more flexible production."
“Using YuMi for the screwing part is one of the best decisions we have made,” says Johan Håård, production technician and team leader at the assembly line, Husqvarna. "In particular, using YuMi reduces much of the monotonous work of the operators. We want to remove as much manual screwing as possible for them, because it is a boring task that does not bring any customer benefit.”
Industrial-scale collaboration
The successful introduction of YuMi to its production led Husqvarna to investigate additional ways of using robots to improve its chainsaw production. As a result, a second collaborative solution was installed on the same assembly in 2020 to handle another stage in the chainsaw production process, involving screwing in the chainsaw handle device at the same time as attaching a chain catcher. Featuring an ABB IRB 1600 industrial robot with SafeMove software and laser scanners, the solution allows safe collaboration with workers without the need for extensive safety fencing operators and partly without fences.
"When we started looking at our second collaborative solution, we saw that with this ABB robot and traditional improvement work, we were able to further reduce our cost per product produced, enabling us to increase our competitiveness," says Sollén.
With YuMi now accepted as one of the team on the assembly line, Husqvarna will continue to invest in sophisticated robot solutions to further increase its manufacturing flexibility and cost efficiency.
"We are constantly looking for new ways to automate and have very ambitious plans for more collaborative solutions, either using pure cobots or collaborative solutions. In this way, our factory will become even more competitive," says Sollén.
"In our future investment journey, we really see ABB as a strategic partner. We are very pleased with our cooperation: We always get the support we need from ABB, and we get it at the right time.”
Key Points
- Husqvarna added collaborative robots to work alongside production operators on its manufacturing line, providing added flexibility
- An ABB YuMi dual-arm collaborative robot selected picks screws and screwdrives them into chainsaws to attach starters
- Additionally, an ABB IRB 1600 industrial robot with SafeMove software and laser scanners screws in the chainsaw handle device
- ABB acquires R&D engineering company
- ABB acquires innovative optical sensor company
- The importance of being serviced
- Aquaculture agreement catches real-time data
- Firstco achieves ABB Value Provider status
- World's first liquid-cooled IE5 SynRM motor
- It’s time to think differently about circularity
- ABB to acquire ASTI Mobile Robotics Group
- Eni selects ABB as main automation contractor for one of the UK’s first industrial CCS clusters
- ABB expands modular large robot portfolio
- Balls to Gravity
- ROBOTS GIVE FASTER CELL TOOL CHANGE TIMES
- ROBOT FOR DELICATE ASSEMBLY
- NUMBER OF ROBOTS IN UK ON THE RISE
- The future is bright - The future is automation!
- High Demand For Grant
- More Capacity, Less Space
- FREEBIRD - THE THIRD DIMENSION
- PRECISION ROBOT CELL FOR THE PHARMACEUTICAL INDUSTRY
- ROBOT SALES REACH ALL TIME HIGH