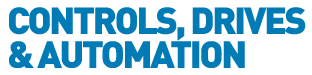
![]() |
Charlotte Stonestreet
Managing Editor |
In the age of circularity, there’s more to drive servicing than repair vs replace
22 July 2024
Steve Hughes explains how circularity is opening up more options to extend asset lifetime and improve energy efficiency

Until recently, as a drive became older or no longer functioned correctly the decision for whether to repair or replace it generally came down to a combination of running hours, cost of repair vs cost to replace, and total running costs. However, in this age of circularity, things are not quite so clear cut.
Circularity is a term that’s been around for some time, and means different things to different people. In fact, a global survey conducted by ABB Motion in October 2023 of 3304 senior industrial decision-makers found that no single definition of the word was accepted by more than half of the respondents. This begs the question: if no one can agree on what circularity is, how are organisations supposed to go about achieving it?
Carbon cost
One thing that many people can agree on is that it involves minimising waste, and maximising resource utilisation. This applies equally to products that themselves can help companies to improve their environmental performance. Variable speed drives are a good example. Variable speed drives are one of the most important technologies we have in industry to reduce carbon emissions and save energy. However, they don’t just appear out of thin air. The materials used to manufacture them have to come from somewhere, and this has an inherent carbon cost. Likewise, disposing of a drive at the end of its life can also have an environmental impact. Realistically, the energy a drive will save throughout its lifetime will offset its carbon footprint many times over, but in a circular economy we should nevertheless strive for better.
Taking a circular approach and applying it to drive servicing holds great potential to open new avenues for saving energy, carbon and costs. Not so long ago, if a drive was no longer working as it should, or was approaching the end of its useful life, then you typically had two main options: repair or replace. In recent times, techniques for maintaining and monitoring drives both on and off-site have grown increasingly sophisticated. As well as repair and replace, there are now a wide number of options in between, ranging from preventative maintenance and reconditioning all the way up to hardware upgrades. With so many more options available, the right solution can be tailored to the individual drive, taking into account its life cycle status, service history and operating environment.
Reconditioning
For instance, Reconditioning (for functioning drives) and Premium Repair (for non-functioning drives) are now options in the UK that weren’t widely available until recently. These involve replacement of all age-sensitive components according to the relevant maintenance schedule, as well as any others that may need replacing early due to the drive’s environment and load characteristics.
An additional option may be to retrofit, whereby the complete drive module within a panel is replaced. This can be carried out on site. In the case of retrofitting, internal components can be upgraded, taking the drive out of its classic life cycle phase and putting it back into an active phase. In ABB’s case, this can quite literally mean taking an older ACS800, ACS600 or SAMI drive and replacing the drive or module to turn it into a newer ACS880.
Extending the useful life of a drive asset can delay the carbon impact of replacing it. ABB estimates that Reconditioning or Premium Repair services use between 55 and 80% less carbon compared to buying a new drive and disposing of the old one.
Knowing what level of service your drive needs at a given time isn’t always easy. Many drives are installed and then left to run for long periods without being regularly inspected. As such, it can be difficult to know their condition. Without this knowledge, any undetected issues can turn into sudden failures and unexpected downtime further down the line. This is why lifecycle management goes hand-in-hand with maintenance. The first step may be to have a simple spreadsheet cataloguing your assets, their age, and when they were last serviced can give you a much better understanding of what your drives need in the way of servicing at a given time, or what they are likely to need in the future based on typical preventive maintenance schedules linked to their duty levels. This data can then be used with ABB’s Life Cycle Audit tool to prepare a detailed report allowing for financial and project planning.
Embracing data
Data should also be embraced as part of any circular approach, and this can provide additional insights into the performance and condition of a drive asset. Monitoring assets digitally is now easier than ever. The data generated can help you understand what’s going on inside your drive and provide useful insights to aid decision-making on repairs and upgrade pathways.
There are now more options than ever to find the right level of service to make sure your drive’s needs are met throughout its life. ABB’s newly refurbished drive service workshop in Coalville is accredited to factory standard and can provide a wide range of repair services for both functioning and non-functioning drives, from preventive maintenance and lifecycle management to comprehensive Premium Repair services, as well as end-of-life services.
For more information about the services offered at ABB’s drives workshop in Coalville, or to make a service enquiry, visit the website below.
Steve Hughes is strategic marketing and sales manager – motion service at ABB
- ABB urges greater adoption of high-efficiency motors & drives
- Register for the webinar: Energy efficiency in hazardous areas
- Automated robot charger for underground mines
- It’s time to think differently about circularity
- ABB achieves IE6 hyper-efficiency with magnet-free motors
- ABB acquires Codian Robotics
- ABB and CERN identify energy-saving opportunity
- ABB & Formula E partner
- ABB to support new H2 Green Steel plant
- Vitens selects ABB to develop new process automation system
- No related articles listed