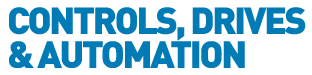
![]() |
Charlotte Stonestreet
Managing Editor |
1/2 (1 to 10 of 15)
Chokes and filters in HVAC applications | 27/03/2025 |
---|---|
THE UK HVAC market is projected to grow rapidly, increasing from USD 6.68 billion in 2024 to USD 10.28 billion by 2030. This growth is driven by urbanisation, construction, climate change, and a focus on energy efficiency. Variable Speed Drives (VSDs), commonly used in modern HVAC systems to control fans and pumps, can introduce electrical harmonics, voltage spikes, and electromagnetic interference (EMI), which reduce reliability and increase operational costs. To address these issues, harmonic reduction chokes, motor chokes, and sinewave filters are vital. Line chokes minimise total harmonic distortion (THD), improving energy efficiency and helping installations comply with EMC standard EN 61800-3. Motor chokes and sinewave filters reduce electrical stress on motors by converting VSD pulse-width modulation into a near-sinusoidal waveform. This improves motor life, lowers bearing currents, reduces EMI, and cuts noise — especially beneficial in hospitals and offices. The rise of IP65/66-rated VSDs presents integration challenges due to the limited internal space for chokes, often necessitating the use of additional enclosures with thermal management capabilities. Compact, high-IP-rated external chokes are needed to ensure compliance and performance in harsh environments. Long cable runs, common in large HVAC installations, increase dV/dt stress and EMI. Sinewave filters and line reactors help manage these issues by reducing voltage spikes and EMI emissions, potentially eliminating the need for shielded cables. Chokes and filters are crucial for maintaining the efficiency, reliability, and compliance of HVAC systems. Manufacturers should provide tailored solutions, particularly for compact, high-IP-rated drives used in conjunction with extended cable runs. |
|
|
|
Food on the move | 11/03/2025 |
Increasingly, the food industry relies on efficient and precise material handling solutions to maintain productivity, quality, and safety. Steve Hughes reports TWO PRIMARY types of conveyors dominate the food sector: motor-driven conveyors and electromagnetic conveyors. While both are essential in food processing and packaging, their operational efficiency, energy consumption, and suitability for specific applications differ significantly. This paper explores the distinctions between these conveyor technologies, focusing on the latest advancements in energy-efficient control solutions for electromagnetic feeders. Motor-driven conveyors Motor-driven conveyors utilise electric motors to move food products along belts, rollers, or modular plastic surfaces. They are commonly found in high-volume food production environments requiring continuous transport. Advantages: - High Capacity: Suitable for bulk transportation of food products over long distances. - Versatile: Can be used for various applications, including primary processing, packaging, and end-of-line logistics. - Automated Integration: Easily integrated with robotic pick-and-place systems and other automated solutions. Limitations: - Higher Energy Consumption: Continuous motor operation and friction in the drive system result in increased power usage. - Maintenance Requirements: Moving parts like belts, gearboxes and rollers require frequent servicing, increasing process downtime. - Potential Contamination Risks: Crevices in belt systems may trap food particles, requiring strict sanitation procedures. Electromagnetic conveyors with energy-efficient controllers Electromagnetic conveyors, also known as vibratory feeders or conveyors, use electromagnetic drives to create controlled oscillations that move food products forward. They are widely used in the food industry for applications requiring precise product handling, such as seasoning, inspection, and sorting. Advantages: - Energy Efficiency: Operate intermittently, reducing overall power consumption. Advanced controllers optimise energy usage using Active Front End (AFE) technology. - Gentle Product Handling: Ideal for fragile food items such as chips, nuts, and confectionery, with customisable vibration settings. - Hygienic Design: Typically constructed from stainless steel with smooth surfaces, making them easier to clean and maintain. - Improved Process Control: Modern controllers allow accurate adjustments, ensuring consistent feeding rates and optimised throughput. Limitations: - Limited Distance Capability: Best suited for short-to-medium distances rather than long transport runs. - Lower load capacity: Not ideal for handling heavy food products in bulk. - Vibration Considerations: Can cause dispersion of lightweight products if not adequately controlled, though advanced controllers help mitigate this by allowing precise adjustments and regulated throughput. Industry applications Motor-driven conveyors are commonly used in large-scale food production environments, such as bakeries, frozen food processing, and meat packaging lines where high throughput is required. Electromagnetic conveyors with energy-efficient controllers are ideal for applications that require gentle handling, precise control, and reduced power consumption, such as seasoning potato crisps, metering nuts into packaging, and inspecting confectionery products. Choosing between motor-driven and electromagnetic conveyors depends on a food processing operation's specific requirement. While motor-driven conveyors are best suited for high-capacity transport over long distances, electromagnetic conveyors offer superior energy efficiency, gentle handling, and enhanced hygiene for applications requiring precision. The latest generation of energy-efficient controllers has further improved the viability of electromagnetic conveyors, making them a compelling choice for food manufacturers looking to reduce energy costs, improve consistency, and ensure precise material handling. Understanding these differences allows food processors to enhance their production lines while maintaining sustainability and cost-effectiveness. Steve Hughes is director at REO |
|
|
|
Enclosure solution for REO chokes and inductors | 11/12/2024 |
AS INDUSTRIES look to lower operating costs and minimise environmental impact, Variable Speed Drives (VSDs) have become essential components in the modern factory. However, complex electronics within VSDs lead to electromagnetic interference (EMI) and harmonic currents, which require components like chokes and sinewave filters to reduce. An unfortunate by-product of these components can be heating, but REO has solved this problem. REO's innovative vented enclosures for chokes and sinewave filters are designed to provide exceptional safety and performance in industrial applications. These enclosures safeguard against accidental contact and meet IP20 requirements. The vented design optimises airflow, allowing heat dissipation to maintain optimum operating temperatures. This solution saves valuable space while enhancing equipment reliability by reducing the need for external cooling systems or larger enclosures. This approach reinforces REO's commitment to delivering innovative, practical, and space-saving solutions that address the challenges of modern industrial environments. It also adds a useful option to augment its industry-standard IP54 and IP66 solutions. |
|
|
|
Input choke use with VFDs | 22/08/2024 |
Steve Hughes explores the role of input chokes in VFD applications, their benefits, and critical considerations for their implementation VARIABLE FREQUENCY Drives (VFDs) are pivotal in modern industrial applications, offering precise control over motor speed and torque. Despite their advantages, VFDs generate high-frequency radio frequency interference, which must be filtered to adhere to legislation, and harmonic distortion, which compromises power quality and system performance. Input harmonics can cause significant Power quality (PQ) issues, and mains chokes, or line reactors, are instrumental in mitigating these issues. VFDs control electric motor speed by varying the frequency and voltage of the power supplied. They consist of a rectifier, DC bus, and inverter. VFDs convert AC power to DC and back to a variable-frequency AC. This process, particularly in the rectifier and inverter stages, introduces significant harmonics and electrical noise. The role of input chokes Input chokes are passive inductive components connected between the power supply and the VFD. They provide an impedance to incoming AC power, thus reducing harmonic distortion and limiting inrush current. - Harmonic mitigation: VFDs produce harmonics due to their non-linear nature. These harmonics can cause overheating and interference with other equipment. Input chokes increase line impedance, reducing harmonic currents and improving power quality. - Inrush current reduction: VFDs can draw large inrush currents upon startup, causing voltage dips and stressing components. Input chokes limit the rate of current change (di/dt), reducing the magnitude of inrush currents and protecting system components. - Transient protection: Voltage spikes can damage VFDs and motors. Input chokes absorb and dampen these transients, providing additional protection. Benefits of using input chokes The inclusion of input chokes in VFD systems offers several benefits: - Improved power quality: By mitigating harmonics and transients, input chokes help maintain a cleaner power supply, enhancing system stability and efficiency. - Extended equipment life: Reduced thermal and electrical stress on VFDs and associated equipment prolongs operational life. - Enhanced motor performance: Smoother current and voltage profiles produce more efficient and reliable motor operation with less noise and vibration. - Regulatory compliance: Input chokes help ensure compliance with industrial standards such as IEEE 519, avoiding penalties and operational issues. - Reduce RMS current and energy consumption: Input chokes are crucial in reducing the root mean square (RMS) current in systems utilizing Variable Frequency Drives (VFDs). Design considerations Selecting and implementing input chokes requires careful consideration: - Inductance value: Choose inductance based on VFD power rating and desired harmonic mitigation, typically rated to give a line voltage drop of between 2% and 4%. The difference in these ratings can significantly affect the reduction of harmonics and RMS input current to the drive. For example, Figure 1 shows the harmonics of a 22kW VSD without choke and with 2% and 4% chokes for comparison. Total Harmonic Current Distortion (THDI) reduction at full-rated load reductions is approximately 19% and 36%, respectively. - Voltage and current ratings: Ensure the choke can handle maximum voltage and current. Undersized chokes may overheat, while oversized chokes can be costly. Chokes can be chosen for the reduced RMS current, allowing further cost reductions. - Thermal management: Provide adequate ventilation or cooling to prevent overheating during operation. Water-cooled units can be utilised in areas with controlled ambient temperatures or space issues. - Installation location: Install chokes close to the VFD to minimise impedance and maximise effectiveness. High ingress units, >IP54 allow units to be combined with modern standalone drives and mounted in control rooms without enclosures. Energy consumption When placed between the power supply and the VFD, chokes provide impedance that limits the harmonic currents generated by the drive's non-linear load, reducing the overall RMS current. RMS current is the practical value of the varying current over time; the system consumes less power to deliver the same performance, leading to lower energy consumption and operational costs. See Figure 2, which shows the input current reduction for 2% and 4% chokes. For 2%, the reduction is 8.7%, and for 4%, the current is reduced by 17.2% Input chokes are vital in VFD applications, offering significant benefits such as harmonic mitigation, inrush current reduction, and transient protection. By enhancing power quality, extending equipment life, and improving motor performance, input chokes contribute to industrial electrical systems' overall efficiency and reliability. Careful selection and implementation are essential to maximise these benefits and ensure compliance with industry standards, and in certain circumstances, they can mean input current reductions of up to 17%. Steve Hughes is director at REO UK |
|
|
|
UK MedTech suffering from market uncertainty | 29/03/2018 |
The UK’s medical industry is being overwhelmed by market uncertainty, cost restraints and technological advancement. This is the worrying diagnosis according to a new medical technology (MedTech) industry whitepaper by power quality specialist REO UK. The whitepaper, which is available to download from the company’s website, analyses the state of the industry and suggests that engineering will be key to overcoming these challenges. In particular, REO UK suggests that design and electrical engineers in the MedTech and healthcare industries are pivotal to ensuring safety as modern hospitals become more technologically advanced. The company says that power quality issues created by new devices and equipment can be mitigated by improved electrical infrastructure and even prevented by using more efficient components during device design. The whitepaper explores in detail the ways that engineers can ensure this in their projects. “The UK healthcare industry is in a transformative period,” explained Steve Hughes, managing director of REO UK. “There are many external pressures, such as budgetary constraints and growing service demand from an ageing population, that are forcing the sector to adopt new MedTech quicker in the hopes of easing the strain on the industry. “These technologies present a wealth of new possibilities for the sector, but bring with them the challenges of equipment safety, power quality and system continuity. These can only be safely overcome with the expertise of design and electrical engineers, as well as power quality specialists. “For example, electrical engineers can reduce the problems faced by existing systems by installing effective electrical equipment such as network isolators. These provide effective electrical isolation of devices in copper wire-bound ethernet networks and protect both equipment and people from the impact of electrical voltage spikes.” The whitepaper suggests that engineering expertise will be the cornerstone of a successful future for UK healthcare in light of tightening budgets. While new technologies will ultimately provide a solution to many of the industry’s problems, engineers are necessary to ensure the equipment and power networks can facilitate these solutions. |
|
|
|
How well is your smart farm running? | 22/08/2017 |
Steve Hughes, managing director of power quality specialist REO UK, explains how many farmers, especially those operating small and medium sized farms, might be overlooking a critical aspect of power quality in their automated livestock farming systems. The smart agriculture market is currently growing at a compound annual growth rate (CAGR) of 13.8 per cent and is expected to be worth $18.45 Billion by 2022, according to research firm MarketsandMarkets. The main factors driving growth include an increased adoption of technology in agriculture generally, a higher demand for food globally and assistance in monitoring livestock performance and health. The types of automation technologies farmers now use is hugely varied, ranging from automatic feed control, milking systems, electronic identification and herd tracking, automatic drafting and gate control as well as in all areas of health, treatment, breeding and farm maintenance. These complex systems, made up of IoT sensor-enabled devices connected to industrial computing systems provide a wealth of data for farmers to maintain the welfare of their animals while maximising yield. Automatic milking Take automatic milking systems in the dairy industry for example. Here, radio frequency identification (RFID) tags are attached to a cow’s ears. Used in everything from warehousing and logistics to fridges and washing machines, RFID tags have found a useful home in the farming sector where the RFID tag communicates with a base station to provide an up to date location for each animal.
RFID tags have found a useful home in the farming sector
As the cow is drafted in for milking, the system logs the cow’s identity and, as the robotic milking system automatically begins to milk the cow, it continues to track real time yield against a historical record, which is then used to tailor the cow’s feed characteristics. The data generated from an entire herd is sent to a centralised system where a single farmer overseeing the entire process can manipulate the data to forecast trends relating to yield, feed demand, breeding and medical treatment, among other things, to make informed decisions on best practice. This level of traceability afforded by smart systems is helping the farming industry to overcome years of stigma associated with many high profile incidents such as the horsemeat scandal of 2013. However, despite the benefits provided by all of this big data, the rising complexity of automated systems is resulting in power quality problems for many farmers. Automatic milking systems for example are made up of a large network of motors, actuators, pumps and variable speed drives (VSDs), often connected using miles of power cables on a commercial farm. These networks typically use power line communication (PLC) otherwise known as ripple control technology. Power line communication offers a cheap and readily available method of using the same electricity grids and power cables to transmit data. It is typically used to control smart meters, street lighting and WiFi range extenders. The problem is that this is a very inefficient transmission that results in high levels of mains and airborne sources of electromagnetic interference (EMI) and radio frequency interference (RFI). Combine this with inadequately earthed equipment, often installed in close proximity, and it’s not difficult to see why many highly automated farming systems are plagued with power quality problems. What’s worse is that typical output mains filters designed to eliminate electromagnetic compatibility (EMC) problems are simply not effective for networks that employ power line communication. For example, one of our customers, a large US-based manufacturer, was using tagging in its automated milking systems. During routine operation, the company was facing a variety of electromagnetic and radiofrequency interference (EMI/RFI) issues and couldn't quite figure out what was causing the problem. They had tried everything from using EMC filters on the input and output to their variable speed drives as well as reconfiguring the system to try to eliminate these problems. It wasn't until a REO engineer suggested that they try using a power line communication filter, that the problem was solved. The company subsequently eliminated its power quality issues and made efficiency and operational gains as a result.
Key Points
|
|
|
|
When water & electricity do mix | 13/10/2016 |
Misconceptions can often lead to a fear of new developments, especially in the world of technological innovation. Using water-cooling for electrical devices, for example, has a stigma due to the combination of liquid and electricity. Steve Hughes, MD of REO UK, reports It is common knowledge that mixing electricity and water is generally a recipe for disaster. So often, we are warned that the two together are a fire hazard that, when suggested, the idea of using water-cooling for power supplies makes many electrical engineers understandably apprehensive. Although there was once significant risk involved with water-cooling, the practice is now safe and used in many industrial applications in place of air cooling. The threat of leakage has been subdued as most critical water-cooling now operates in self-contained housing systems so that – in the unlikely scenario of a leakage – there is no risk of electrical fire. Liquid coolants also offer a number of advantages to businesses. For some the biggest benefit could be a streamlined product design, while others will be more interested in the industrial circular economy that they can implement. Compact versatility One of the most straightforward benefits of water-cooling is a more compact overall design. This is because, traditionally, most electrical devices use air-cooling technologies and therefore enclosures have to be larger to accommodate for the bulkier size of fans.
Traditionally, most electrical devices use air-cooling technologies
While it might not initially sound like much more than an aesthetic benefit, a sleeker design means that devices are able to fit into tighter spaces. Power controllers, for example, are often integrated into transformer control cabinets and can therefore benefit from the smaller footprint that water-cooled power controllers provide. The same is true for space-restricted applications such as industrial ovens and heating equipment. It isn’t just the size of the device that changes when fans are removed. All electrical devices that use air cooling have vents in the housing to allow the circulated air to escape and prevent condensation from forming over electrical components. However, these vents also give harmful contaminants access to the internals of a device that would not occur with water-cooled systems. Even seemingly innocuous particles such as dust can devastate electrical and electronics equipment. The ambient temperature of a device increases as more dust accumulates, which in turn raises the risk of overheating. This also elevates costs for businesses as fans work harder to reduce temperature. Likewise, certain businesses will find that vented enclosures are simply unsuitable for use in their factories. In copper electroplating plants, for example, there is a high volume of copper sulphate particulates that are corrosive to electrical components and internal wiring. Alternatively, these particles can clog up fan filters and drive the need for more regular maintenance and replacement. This not only takes hours of manual work for engineers, but can even require a temporary shutdown in applications to ensure worker safety. Eliminating vents also reduces maintenance downtime and prolongs product life. Increased energy efficiency Interestingly, water-cooling is also more energy efficient than air-cooling. As air has a lower heat conductivity than water, it takes a higher volume to effectively cool devices to optimum temperature. This means that more energy is used in order to generate that air flow, leading to higher operating costs and energy bills. Water-cooling, on the other hand, benefits from water’s increased capacity to remove heat as well as the ease of circulation. Whereas air-based systems may require as much as six fans to provide adequate cooling, just one pump is required for water. This minimises energy consumption and, subsequently, business expenditure. These advantages go a long way to explaining why water-cooling is becoming increasingly popular among electrical engineers. As industrial systems become more complex, it is likely this trend will continue for the foreseeable future — with businesses coming to the realisation that the fears were unfounded.
Key Points
|
|
|
|
The future is (almost) now | 26/11/2015 |
Buzzwords fly around in industry like wasps at a picnic. Industry 4.0 is one of these hugely popular concepts, particularly when it comes to manufacturing. Here Steve Hughes, managing director of REO UK, gives further insight into Industry 4.0. The first industrial revolution saw the development of mechanisation using water and steam power. The second was the introduction of electricity in manufacturing environments, which facilitated the shift to mass production. The digital revolution happened during our lifetime, using electronics and IT to further automate manufacturing. Industry 4.0 is the fourth in this series of industrial revolutions. Although it is still, relatively speaking, in its infancy, the idea relies on sophisticated software and machines that communicate with each other to optimise production. In Industry 4.0, strong emphasis is placed on the role of intelligent factories. They are energy efficient organisations based on high-tech, adaptable and ergonomic production lines. Smart factories aim to integrate customers and business partners, while also being able to manufacture and assemble customised products. Industry 4.0 is more about machines doing the work and interpreting the data, than relying on human intelligence. The human element is still central to the manufacturing process, but fulfils a control, programming and servicing role rather than a shop floor function. The Siemens (IW 1000/34) Electronic Works facility in Amberg, Germany, is a good example of the next generation of smart plants. The 108,000 square-foot high-tech facility is home to an array of smart machines that coordinate everything from the manufacturing line to the global distribution of the company’s products. Despite the endless variables within the facility, a Gartner industry study conducted in 2010 found that the plant boasts a reliability rate of more than 99 per cent, with only 15 defects in every million finished products. Thanks to the data processing capacity of Industry 4.0-ready devices, it is possible to generate the information, statistics and trends that allow manufacturers to make their production lean and more fuel efficient. If you work in the food manufacturing industry, you probably know that many production lines today operate at less than 60 per cent efficiency, which means there is considerable room for improvement. Saving electricity and water are also key requirements for modern plant managers, who can achieve their eco-friendly goals by using smart plant connectivity. The great news is that a lot of the technology associated with Industry 4.0 already exists. The not so great news is that implementing it will probably cost your company a pretty penny, especially if you aim to be an early adaptor. What the future holds For most automation companies, the move will be a gradual one, an evolution rather than a revolution. This is why continuity with older systems will still be essential for manufacturing in the years to come. Industry 4.0 will ultimately represent a significant change in manufacturing and industry. In the long run, the sophisticated software implanted in factory equipment could help machines self-regulate and make more autonomous decisions. Decentralisation also means tasks currently performed by a central master computer will be taken over by system components. In years to come, geographical and data boundaries between factories could become a thing of the past, with smart plants joining up sites located in different places around the world. Industry 4.0 is an excellent opportunity for UK industries to apply their skills and technologies to gradually start the shift towards smarter factories. New technologies will also lead to more flexible, sustainable and eco-friendly production and manufacturing lines. The first step is taking the Industry 4.0 concept from the land of buzzwords, to the land of research and development. |
|
|
|
Behind the motion of motor control | 17/06/2015 |
With the market for variable-speed drive (VSD) based motor control is growing rapidly, there is a concerted effort by leading VSD manufacturers to undergo collaborative development for further product innovation A result of increasing global consumption, rising electricity prices and frantic infrastructure development in newly industrialised countries (NICs), the global market VSDs is expected to witness a compound annual growth rate (CAGR) of 6.4 per cent from 2014, reaching a total value of $22.7 billion by 2019. Today, most industrial sectors now have access to commercial off-the-shelf (COTS) components that are designed to fulfil a purpose. Industries the world over, from food and beverage and packaging to maritime and offshore applications, make use of these components in applications from conveyors, compressors and elevators, to pumps, fans and extruders.Case in point Invertek has made a name for itself by going beyond the status quo and has a reputation for delivering only the best. With a focus on energy saving of up to 50 per cent and reduced maintenance and downtime, the Wales based company has become one of the world's fastest growing VSD manufacturers, with a CAGR of 25 per cent. Specialising in the areas of pumps, building heating ventilation and air conditioning (HVAC) in addition to combustion, marine and elevator applications, Invertek certainly understands the inherent challenges of the industrial market. It was research conducted in its state of the art innovation facility that prompted Invertek to create a new product, the Optidrive E2. The findings showed that there was demand for a high powered VSD for use in a variety of applications; from dry to humid conditions with temperatures between -20 and +50˚, to environments ranging from mild atmospheric salinity to aggressive ammonia exposure in chemical plants, certainly not something that could be built with off-the-shelf components. It was with this in mind that Invertek turned to power quality specialist REO UK for support. REO is an original manufacturer of high quality power equipment, including electronic controllers, components and electrical regulators. With 90 years' experience as a global brand, the company was an obvious choice when it came to wound components and toroidal cores. Enduring design "The brief given to REO was to create a potted DC link choke that was both electrically and thermally efficient," explained Glyn Jones, technical director at Invertek. "As well as this, the unit was required to diffuse heat effectively into the air stream, provide ingress protection from water and humidity, be easy to install, cost effective and capable of being produced for a worldwide supply chain. It was without a doubt, a tall order for any manufacturer but one which REO embraced." The first prototype developed by REO consisted of an aluminium wound choke. Although it's not yet a material that's widely used in power drive systems, aluminium offers significant material cost savings over copper as a result of the rising commodity price of copper in international markets. Although the prototype worked electrically, sustained thermal performance could be improved further, for use in continuous production environments.
Aluminium offers significant material cost savings over copper
"One of the challenges we faced was fitting the traditionally heavy-duty, large electrical components into a VSD designed for precision motor control," explained Steve Hughes, managing director of REO UK. "Because our DC link choke is the last component to be fitted into the drive there is a very low mechanical tolerance. We had to ensure that it was easy to integrate into Invertek’s existing infrastructure, otherwise the whole drive would require redesigning." The solution was two-fold, for the second prototype copper was used as the winding and terminal material. Because the purpose of a DC link choke is to provide smoothing of the current waveform, reducing the DC bus voltage-ripple and minimising current harmonics, copper exhibited lower losses and ran cooler as a result. After this, REO optimised the installation of the choke, using its sophisticated production tooling to customise production-jigs and secure the choke in the right position onto the bus bar. Preserving position It’s this attention to detail that sets the two manufacturers apart from their competitors. In the same way that a chain is only as good as its weakest link, even minor component failure can have lasting consequences for both the reputation of the drive manufacturer and OEM supplier.
Even minor component failure can have lasting consequences
"If the choke used in our drive failed, the drive would also fail,” continued Glyn. "Because it’s a high-powered element, the choke failing can cause a lot of damage to the drive. It would almost certainly result in the circuit breaker clearing the fault but causing alarm to the customer if smoke started coming out of the drive. Although this isn’t in itself very dangerous it causes a lot of embarrassment for us as a drive manufacturer and we can't accept this. "Our reputation as a reliable drives maker is very valuable to us and a drive failure rate, due to the failure of the choke, of even 1 in 1000 would not be acceptable. We expect absolutely zero failures if we want to be taken seriously and I’m happy to report that, to date, no REO products have failed.” Challenges It wasn’t all plain sailing however. Fulfilling the next part of the brief involved ingress protection and suitability for worldwide use. Although headquartered in the UK, 90 per cent of Invertek’s products are exported for use around the world. Part of the challenge of manufacturing a VSD for general use is overcoming the challenges posed by countries like India where high humidity levels, in addition to supply issues and an often underdeveloped engineering infrastructure, can quickly push components to their limits. Using a potted design, REO enclosed the DC link choke and was able to make the unit waterproof to an ingress protection rating of IP55. In conjunction with the keymount holes on the VSD, the entire drive can be mounted onto the wall of a control room. This is an improvement on the typical setup which involves installation into a drive cabinet on the production floor, which raises problems of effective thermal management, increased chance of ingress and terminal corrosion. REO was able to pass these challenges by not only demonstrating its installation expertise but also testing capability, using its state of the art test laboratory. It was here that various voltage, temperature and installation options were performance tested under rigorous conditions before being sent off for type testing and external regulatory validation. This process allowed REO to achieve the Invertek specification requiring terminals on the DC link choke to be rated between 690-1000V. Had a typical off-the-shelf choke been used in this installation, the inadequate standard terminal rating of 500V would most certainly have caused a failure of the terminals by short-circuiting, resulting in possible fire and subsequent injury. At the very least, considerable wear and increased energy use would have significantly raised costs. Future innovation Despite the numerous challenges posed by a stringent brief, the collaborative approach between Invertek and REO produced not only a reliable product but also a sustainable partnership between the two companies. Research and development conducted in both organisations is being used to continue innovation in product development. "We always aim to use a consultative approach,” said Steve. "Having finished this project we’re already working on a cold weld process that will realise material cost savings by using aluminium windings on the core and copper on the terminals. This will eliminate any contact corrosion and benefit from cheaper aluminium prices and better thermal dissipation. "We are also looking at the possibility of providing these chokes using plastic housings. We have had good results of this in other applications and it can provide weight and cost benefits We can easily make prototypes using our 3D printing capability to demonstrate the principle.” The relentless effort to pursue perfection, demonstrated by these experts in motor control, continues to show that greatness is not achieved by never failing but rather a continuous process of improvement, even if it means another 10,000 tries.
Key Points
|
|
|
|
Think tank adds new member | 27/02/2014 |
Industry think tank Power Electronics UK has added a new member in the form of electrical OEM REO (UK). The company hopes to help in the trade body’s stated aim of creating sustainable growth strategies for the industries it serves. Amongst the key aims of Power Electronics UK is to create a sustainable supply of high quality, industry prepared graduates. One of the strategies outlined in the plan involves increased collaboration between academics and key businesses, which can offer core competencies such as access to intellectual property. The addition of REO UK strengthens the think tank's portfolio of existing members, which includes Mclaren, Rolls Royce, Siemens and Schneider (UK). |
|
|