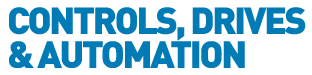
![]() |
Charlotte Stonestreet
Managing Editor |
1/84 (1 to 10 of 837)
Powering the possible | 12/08/2025 |
---|---|
TAKING PLACE 29-30 October 2025 at the NEC Birmingham, Advanced Engineering connects the entire industrial ecosystem, featuring an expanded Composites Pavilion, the SME Village, the ADS Pavilion, AM2 Forum and a focused Electronics Zone THIS YEAR'S event comes at a pivotal moment for UK industry, following the government’s announcement of a new 10-year industrial strategy. With measures that could reduce electricity bills by up to 25 per cent for over 7,000 manufacturing firms and billions earmarked for innovation, R&D and AI, the strategy signals a renewed focus on long-term industrial growth — a direction that will be reflected across the show floor at Advanced Engineering 2025. The show will also champion real-world problem-solving and high-value manufacturing, from net-zero composites to energy-efficient processes. By bringing engineers and innovators together, meaningful change and the industry’s most pressing challenges across all sectors can be addressed, including sustainability and skills development. A highlight for 2025 is the newly expanded Composites Pavilion, now in its fourth year and fully booked well in advance. Delivered in partnership with Composites UK, the pavilion offers smaller companies and SMEs turnkey exhibition pods, making it easy and cost-effective to showcase their innovations. Strategically located next to the Composites Networking Zone, the pavilion provides high visibility and attracts key OEM visitors. Hands-on demos Alongside the pavilion, the Composites Networking Zone will feature hands-on demos from PRF Composite Materials, showcasing cutting-edge prepreg systems including rapid processing RP570 presses and innovative recycled carbon solutions. Insights from end users across aerospace, automotive, marine and renewables will highlight how composites are driving high-performance applications and net-zero ambitions across sectors. Building on this, Composites UK has reimagined the Composites Forum for 2025, curating two full days of expert-led sessions focused on sustainability, material circularity and new product development, all aimed at strengthening the sector’s innovation and collaboration. Here, the Composites Networking Zone will be a key feature, with PRF Composite Materials hosting interactive demos and networking sessions designed to foster valuable industry connections. The event will also reinforce the role of SMEs and agile innovators through dedicated spaces such as the SME Village, platforming disruptive technologies across automation, embedded systems, semiconductors and more. These zones underscore the crucial role SMEs play in driving innovation and growth across the UK’s engineering and manufacturing sectors. “Advanced Engineering is the only UK event that connects every corner of the industrial ecosystem,” said Simon Farnfield, event director of Advanced Engineering at Easyfairs UK & Global. “With zones focused on composites, electronics and SME innovation, and forums designed to address the industry’s biggest challenges, the 2025 edition is set to deliver even more value for visitors and exhibitors alike. This edition will feature over 400 exhibitors, including more than 130 making their debut, meaning that a lot of the stands will offer something brand new to discover.” Key topics Over 200 expert speakers are also set to take stage across multiple forums to explore key topics including digitalisation, supply chain resilience, sustainability and government policy. The event will also continue its #MINDTHEskillsGAP initiative launched to help tackle the UK’s ongoing shortage of engineering and manufacturing talent. In addition, Composites UK will co-locate its prestigious Industry Awards Dinner on the evening of 29 October at the neighbouring National Motorcycle Museum, providing a prime networking opportunity for sector leaders. Register at: |
|
|
|
Technology adoption hubs and the future of UK manufacturing | 13/08/2025 |
JUST OVER a month after the release of the Government’s Advanced Manufacturing Sector Plan, the West Midlands Robotics & Autonomous Systems (RAS) Cluster is reflecting on how funding commitments should be allocated to shape the future of UK industry, as Mike Wilson outlines THE WEST midlands has long been at the heart of British industrial excellence. From the first Industrial Revolution to its dominance in automotive and digital innovation, the region has continually taken the lead in manufacturing. Like much of the UK, productivity remains the key weakness. By increasing the accessibility of robotics and autonomous systems, workforces can be supported, productivity can be optimised, and profitability can increase. The new Industrial Strategy alongside the dedicated Advanced Manufacturing Sector Plan provides the catalyst for change. For too long, small and medium-sized manufacturers have struggled to bridge the knowledge and capital gaps necessary to integrate robotics effectively. The initial investment of £40 million toward the creation of a new network of Robotics Adoption Hubs with the relevant expertise, equipment, and connections will harness existing UK resources to accelerate take-up of robotics on a nation-wide scale. This comes alongside clear intent to support SMEs through the extension of the Made Smarter programme. It is important that industry is aligned on how this investment of £40 million is spent. The UK industrial sector does not need to spend money on new buildings, robotics adoption hubs should instead use existing facilities and online networks. The available funding can then be directed toward joining together existing resources, facilitating collaboration and developing training programmes in order to create a greater impact. Why now? The urgency of adoption The global race for manufacturing competitiveness is intensifying. Data from the International Federation of Robotics (IFR) reveals that the UK currently ranks 23rd globally in the adoption of robotics and autonomous systems technologies. Without rapid action, the UK risks falling further behind countries such as Germany, Italy, France, Spain and Poland that together accounted for about 70% of all industrial robots installed within the EU in 2022. The Industrial Strategy specifically identifies the West Midlands as a high-potential area for investment in advanced manufacturing. With strong automotive and digital sectors, established, research organisations such as The MTC, further education facilities, and a history of industrial success, the region is uniquely positioned to pilot and scale robotics-adoption hubs. National policy has now set the intention and made clear its support for local initiatives to foster collaboration between academia and industry. The West Midlands RAS Cluster plans to leverage these national initiatives to support SMEs on their automation journeys. This can be supported by apprenticeship, funding and reskilling initiatives in both the private and public sectors. The 2025 Industrial Strategy is ultimately aiming to ‘make the UK the best country to invest in anywhere in the world’. With competitors moving fast and adopting robotics and automation technologies to increase productivity and output the urgency is clear. UK industry must embrace a collaborative ecosystem led by adoption hubs in order to make automation more accessible. Start your journey now and access expert advice on funding, training and business plans by visiting: Mike Wilson is chief automation officer at the Manufacturing Technology Centre (MTC) |
|
|
|
Physical AI framework enables rapid learning of complex skills in robotics | 07/08/2025 |
DESPITE SIGNIFICANT advancements, robotic automation can struggle with reliably performing delicate, tactile tasks like inserting connectors or handling flexible materials. A new breakthrough – Tactile Skills – claims to be changing this. Sami Haddadin, VP for Research at Mohamed bin Zayed University for Artificial Intelligence (MBZUAI) has worked with his former PhD student Lars Johannsmeier and colleagues Yanan Li from the University of Sussex and Etienne Burdet from Imperial College, and led the work behind the paper published in Nature Machine Intelligence in June. The paper introduces the groundbreaking embodied AI framework coined Tactile Skills as a theoretically sound, practical and scalable framework, inspired by the human neural system and human vocational training. Their method uses a clearly structured taxonomy based on expert-defined process specifications. In simple terms, it’s like giving robots their own specialised curriculum, helping them rapidly learn and master new physical tasks.“Our framework bridges the gap between human expertise and robotic capability. It’s rewarding to see robots now reliably mastering intricate tasks with precision and adaptability – this isn’t just incremental progress; it’s a meaningful leap forward for practical automation in everyday life,” said Sami Haddadin, VP for Research and Professor of Robotics at MBZUAI. This approach has been tested extensively on 28 distinct industrial tasks, including complex operations like plug insertion and precision cutting. Remarkably, the robots achieved nearly 100% success and industrial grade performance, even when encountering unexpected changes in object positioning or environmental conditions. These robots not only performed reliably but did so quickly and with minimal error. A crucial advantage of this method is that it doesn’t rely solely on extensive trial-and-error or massive datasets, as traditional machine-learning methods often do. Instead, it blends expert process knowledge with reusable tactile control and adaptation components, significantly simplifying and speeding up the robot’s learning process. This reduces energy consumption and increases performance dramatically compared to current deep-learning-based approaches. One of the framework’s standout achievements was successfully assembling a complex industrial device used in bottle-filling plants, demonstrating its practicality for real-world manufacturing scenarios. By bridging expert process definitions and robotic learning in a structured way, this method empowers operators who may not have deep robotics expertise to effectively deploy robots on diverse tasks, greatly reducing setup times and costs. “This research represents an important leap toward widespread automation, transforming robots from specialised tools into adaptable, skilled assistants and ultimately physical AI agents. Industries can now envision greater automation of complex, tactile tasks, unlocking new potential for efficiency, safety, and scalability. Ultimately, this breakthrough doesn’t merely improve how robots handle specific tasks—it reshapes what’s possible for automation, making versatile and reliable robotic skills broadly accessible for industries and everywhere, and ultimately our homes,” said Haddadin. |
|
|
|
Real-time visibility | 29/08/2025 |
MANUFACTURING AND supply chain software specialist, Nulogy, will debut its new Smart Factory solution to the UK manufacturing sector at the PPMA Total Show in September. Under the theme “Don’t Lose Sleep Over Your Factory Floor", Nulogy will showcase to operations directors and production managers, amongst others, how its cloud-based platform helps manufacturers move beyond constant firefighting and uncertainty. By delivering real-time visibility into production metrics, equipment status, and workforce allocation, Smart Factory empowers teams to identify issues early, eliminate inefficiencies, and optimise labour allocation. The result is fewer disruptions, smoother shift changes, and improved overall equipment effectiveness (OEE) – all while controlling costs and maintaining quality output amid rising labour costs in the UK manufacturing sector. Visitors to Stand A92 can see live demonstrations of Smart Factory and speak with Josephine Coombe, chief commercial officer at Nulogy Europe, who will explain how the software helps manufacturers move beyond ‘gut feel’ decision-making to run their operations with trusted, actionable data. “Production managers are all too familiar with the anxiety caused by unexplained downtime, fluctuating output, and unplanned overtime. Often, critical issues remain hidden until the end of the shift or day, meaning problems escalate before they can be resolved,” said Coombe. “For senior executives such as operations directors, this lack of clarity translates into uncertainty around margins, capacity, and ROI for future investments, creating a barrier to scaling operations profitably and ultimately keeping them up at night.” Increasing costs are putting unprecedented pressure on manufacturers, making economic savings more critical than ever. Nulogy’s Smart Factory solution provides plant and production leaders with clearer, faster insights for confident decision-making, helping them navigate shifting market demands while cutting waste, reducing costs, driving growth and ending sleepless nights “Smart Factory is designed to bring clarity and calm to chaotic factory environments,” concluded Coombe. “For businesses under pressure to do more with less, it gives teams the visibility they need to hit targets, hold each other accountable, and sleep better knowing production is under control.” Visitors attending The PPMA Total Show can book an appointment to learn more about Smart Factory at: |
|
|
|
Specialist dairy sector control systems | 28/08/2025 |
LEADING PROVDER of intelligent drive and control systems, Technidrive, has delivered of its 1000th bespoke control solution to the dairy sector. With advanced technologies like TechniVac and TechniFlow, the company has been transforming dairy operations across the UK and Republic of Ireland (ROI), helping farmers enhance energy efficiency, product quality and overall performance. This latest milestone underscores Technidrive’s growing role in an industry where precision, hygiene and reliability are essential. Designed and engineered in-house, the company’s flagship systems have become widely recognised as a benchmark for energy-efficient milking and milk transfer. TechniVac is Technidrive’s vacuum pump system, intelligently adapting output to meet real-time demand during milking. By significantly reducing energy use by up to 60% and delivering quieter, low-maintenance operation, TechniVac ensures consistent vacuum performance in a compact hygienic design. Meanwhile, TechniFlow optimises milk transfer using true variable speed control. Its gentle, controlled flow helps maintain milk quality, reduce refrigeration costs and minimise water usage. With compatibility across 95% of existing dairy setups and installation time of under six hours, TechniFlow is proving to be a favourite among dairy farmers and processors alike. “Reaching the 1000-systems milestone reflects the consistent demand for more intelligent, energy-efficient solutions in dairy operations,” said Andrew Ritchie, technical sales manager at Technidrive. “Farmers are facing increasing pressures from rising energy costs and the need to adapt to ever-evolving industry standards. “TechniVac and TechniFlow have been developed in close collaboration with farmers and processors to solve real operational challenges — from energy consumption to milk quality and uptime. This kind of feedback-led engineering is what drives continued adoption across the UK, Ireland and further afield.” The milestone follows a series of successful installations that have demonstrated the real-world value of Technidrive’s approach. Across UK and Irish farms, the systems have delivered energy savings of up to 55 per cent, enhanced milk cooling, reduced equipment wear and improved milk quality. The technology has proven especially effective on farms facing unreliable power supplies or using legacy fixed-speed systems. “We’re saving approximately £100 per month on electricity and the noise reduction compared to the old system is impressive,” explained Barry Armstrong, a dairy farmer from Cumbria. Similarly, Paul Kinch from Co. Wicklow noted, “The biggest thing for us is the reduction of noise. We’ve also seen a reduction in running costs.” Technidrive’s success is built on its close relationships with regional partners, who provide installation, training and ongoing technical support. This model ensures that dairy farmers not only receive high-quality products but also benefit from expert guidance throughout the lifecycle of the system. As a WEG Premier Distributor and Bonfiglioli BEST Partner, Technidrive also offers customised motor and automation solutions to meet specific dairy processing needs, from vacuum systems to pumps, agitators and beyond. |
|
|
|
What is driving demand for ultra-low voltage motors and drives? | 01/08/2025 |
INTERACT ANALYSIS has published its new Ultra-Low Voltage (ULV) Motors and Drives report, delivering a data-backed view of current market size, technology adoption, and growth outlook. In this article, Clara Sipes draws from the research to highlight the factors expected to drive demand across industries. The proliferation of mobile robotics, automated storage and retrieval systems (AS/RS), automated sortation, surgical robotics, and early-stage humanoid platforms has pushed ultra-low voltage (ULV) motors and drives into the spotlight. These components now demonstrate the precision, energy efficiency, and compact form factors required by next-generation automation systems. Rather than isolated technology swaps, these shifts signal a broader transformation across the motion control industry. As we look ahead, structural market trends and technical advancements are converging, setting the stage for new growth. Our analysis indicates the next phase of market expansion will be driven by five factors:
The rest of this insight explores each driver and its implications for ULV motors and drives suppliers, OEMs, and integrators. 1. Growth of mobile robotics The proliferation of AGVs and AMRs across logistics, warehousing, and industrial environments is driving increased demand for ULV motors and drives. These robots rely on compact, battery-powered motion systems that balance efficiency, torque, and safety in human-centric settings. Suppliers that focus on providing integrated safety functionality within compact integrated designs are likely to capture a share of this expanding mobile robotics segment. 2. Warehouse automation recovery After a short-term downturn caused by macroeconomic headwinds and investment delays, warehouse automation is expected to rebound sharply from 2026. This recovery will be driven by the need for flexible, scalable solutions, including AS/RS, automated sortation systems, and mobile robotics. These next-generation systems increasingly rely on ultra-low voltage motion components to meet requirements for safety compliance, energy efficiency, and compact integration. The resurgence will be particularly strong in sectors such as e-commerce and retail logistics, where adaptability and operation time are critical. Vendors offering scalable ULV solutions and simplified safety integration will be well-positioned to capture market share as facilities modernize, and new greenfield projects accelerate. 3. Semiconductor manufacturing expansion With governments and private sector stakeholders investing heavily in the development of semiconductor fabrication plants (fabs), the semiconductor electronics and machinery industry is emerging as a key growth sector for ULV products. Motion control solutions used in wafer handling and photolithography require the precision, reliability, and compact footprint that ULV motors and drives are well-suited to deliver. To capture opportunities in semiconductor manufacturing, suppliers must deliver ULV solutions that combine compact design with extreme precision and reliability. Products optimized for cleanroom compliance, ultra-low vibration, and that include absolute encoders will be critical to meet the stringent performance requirements of semiconductor electronics and machinery applications. 4. Increasing automation of small axes As automation becomes more affordable and scalable, OEMs are increasingly automating small subsystems that have traditionally been left manual. ULV motors and drives make this transition viable by offering a modular, lower-cost, and compact solution. This trend is evident in packaging and electronics assembly, where adding automated secondary axes improves adaptability and throughput. This will result in a greater number of ULV motion systems emerging, spurring demand for these components over the long term. Vendors that develop modular product families and user-friendly personalization tools will benefit as machine builders seek cost-effective, quick-to-implement solutions. 5. Continued replacement of pneumatic systems Pneumatics has long been a staple in automation, but its limitations, poor energy efficiency, lack of precision, and higher maintenance demands are increasingly untenable. Falling costs and enhanced performance of ULV technology have strengthened the business case for ULV systems. The result is a continued migration away from pneumatic actuation in industries where electric automation is viable. Suppliers that can demonstrate lifetime cost savings and simplified installation for ULV alternatives will accelerate pneumatic displacement in both new installations and retrofit scenarios. Looking ahead: The next wave of motion control innovation The forecast period will be defined less by a single breakthrough and more by the convergence of multiple trends. Electrification is fuelling smarter automation, while the proliferation of mobile robots and the continued growth in warehouse automation provide new opportunities for ultra-low voltage vendors. Stay tuned as we unpack data from the new ULV report and analyse the strategic implications for suppliers, OEMs, and end-users navigating an industry in transition. Clara Sipes is a market analyst at |
|
|
|
First robotic-assisted BiVAD implantation | 30/07/2025 |
KING FAISAL Specialist Hospital and Research Centre (KFSHRC) in Riyadh has successfully performed the world's first implantation of two artificial pumps for biventricular support (BiVAD-HMIII) using robotic technology on a patient with advanced heart failure. This groundbreaking procedure is reportef to open new horizons in circulatory support techniques for patients with complex cardiac conditions and marks a medical achievement that culminated in the patient’s recovery within a short period following the surgery. The procedure represents a major advancement in the treatment of bilateral heart failure, which was traditionally performed through full sternotomy, an approach associated with higher surgical risks and prolonged recovery. However, the cardiac surgery team at KFSHRC, led by Prof. Feras Khaliel, successfully performed the operation through small incisions using remotely controlled high-precision robotic arms, resulting in reduced blood loss, lower risk of infection, and faster patient recovery. The 61-year-old patient was admitted after spending over two months bedridden, suffering from end-stage heart failure unresponsive to medical therapy, in addition to multiple chronic conditions including diabetes, stroke, and renal impairment. After a comprehensive clinical evaluation, the patient was deemed ineligible for a heart transplant, making robotic implantation of the artificial pumps a vital and unique solution suited to his health status. This milestone reflects the integration of expertise across multiple departments at KFSHRC including cardiac surgery, cardiology, anesthesia, critical care, biomedical engineering, and advanced life support. The procedure was meticulously planned and benefited from 3D imaging technologies, real-time surgical navigation, and innovative solutions for safely securing the mechanical assist devices. KFSHRC aims to publish the results of this procedure in peer-reviewed medical journals and present them at global cardiology conferences to promote knowledge exchange and establish innovative partnerships with leading international centers in robotic care and advanced heart failure management. This achievement adds to KFSHRC’s track record in robotic surgery which includes the world’s first fully robotic heart transplant and the World's First Robotic-Assisted Artificial Heart Pump Implantation. These milestones serve as evidence of its leadership in adopting cutting-edge cardiac technologies and managing critical conditions with the highest standards of precision and safety, further reinforcing its position as a leading academic medical center both regionally and globally. |
|
|
|
Strategic nuclear robotics partnership | 30/07/2025 |
LEADING ENGINEERING services and nuclear company, AtkinsRéalis and Canadian robotic developer Kinova have announced the extension of their global strategic partnership for a further three years. The collaboration will help advance the integration of cutting-edge robotic technology in the nuclear sector globally, building on the successful deployment of Kinova's robotic arm within the patented AtkinsRéalis Remote Glovebox Operation (ARGO) system in the United Kingdom, with demonstration units also operating at the AtkinsRéalis Technology Center (ATC) in Richland, US, and in Montreal, Canada. The ARGO system was recently used in a world-first deployment at the Sellafield site in the UK, retrofitting a nuclear glovebox with a robotic arm in a successful demonstrator project that proves viability to use at scale across nuclear decommissioning sites. The next phase of the partnership will focus on further refining and expanding the technology for use in nuclear world-wide to improve safety and unlock efficiencies, including the use of Kinova’s Gen3 robotic arm for remote glovebox operations and decommissioning using ARGO at selected nuclear licensed sites. Plans include the development of additional tools and functionalities, enabling the system to perform a wider range of tasks for remote handling and treatment of hazardous materials in gloveboxes across the nuclear sector. Christian Pilon, head of nuclear robotics at AtkinsRéalis, said: "Robotic and automation technology is already improving safety and speed of delivery in the nuclear sector but the full extent of its potential is still to be realized. Our work with Kinova is proving how commercial technology used successfully in other sectors can be integrated into nuclear systems through close collaboration and combining engineering expertise and industry knowledge.” “We are proud to extend our collaboration with AtkinsRéalis and to see Kinova’s robotic technologies contribute meaningfully to innovation in the nuclear sector,” said Rodolphe Rosset, sales director at Kinova. “This partnership is a powerful example of how our versatile and precise robotic arms, such as the Gen3, can adapt to meet the highest safety and performance standards in demanding environments. Together, we are pushing the boundaries of what's possible in remote operations.” AtkinsRéalis is a leading provider of digital services and technologies in nuclear, with a focus on solutions that reduce risk and unlock the cost, carbon, safety and productivity benefits of digital for the nuclear sector. This includes the development and implementation of advanced robotic technologies; AI-enabled platforms to automate processes, streamline major project delivery and incorporate technology and robotics for the remote access and monitoring of sites; and digital design and engineering methods for projects across the lifecycle. |
|
|
|
How robots can make manufacturing plants more efficient | 30/07/2025 |
Buddharatn Ratawal takes a closer look at how robots can make your manufacturing operation more efficient, along with other key benefits of businesses making the switch to robots THERE IS increasing pressure on manufacturing businesses to streamline processes, reduce costs and keep product quality at an all time high, despite rising costs and ever-decreasing access to top manufacturing talent. With that in mind, manufacturers are turning to autonomous solutions to improve production, accuracy and reduce costs over time, there’s never been a better time to invest in robots for manufacturing firms. From assembly and material handling to welding, painting and quality control, robots play a vital role in automating a whole host of tasks in the manufacturing industry. From increased productivity and cost reductions to enhanced data collection and employee safety, robots come with a whole host of benefits for manufacturing businesses. Increased productivity, quality and throughput A key challenge for manufacturers is to ensure consistent quality of product, while also maintaining and optimising workflows to improve productivity. There’s a fine balance between potentially sacrificing quality for increased production, but with the integration of robots, this doesn’t need to be a problem. 24/7 operation: Robots play a key role in allowing businesses to work continuously without any breaks, vacations or shift changes. This obviously increases the output significantly. When paired with a human who can keep a close eye on things, and be on hand to carry out any maintenance or repairs, robots are a no-brainer for making your manufacturing plant run more smoothly. Consistent precision and repeatability: Robots are capable of performing repetitive tasks with extremely high accuracy, which leads to reduced product variability and defects. They’re also able to replicate the exact same motion hundreds of thousands of times without the need for human intervention – which enables your manufacturing business to greatly increase output and lower quality issues. Cost reductions In today’s economy, there’s a consistent squeeze on businesses across all sectors to reduce costs, which is increasingly difficult with increasing overheads and material prices. While the initial investment in robotics can be hard to justify, the longer-term savings and flexibility offered by integrating autonomous technology into your existing workflow can be a gamechanger for manufacturers. Lower labour costs: A reduction in human workers required for repetitive, dangerous or simple tasks, means your company’s labor costs will be significantly reduced thanks to the investment in robots. You’ll need to look at upskilling or investing in staff who can help keep things running effectively and understand and interpret data processed by robots, but this will inevitably mean you’ll need less manpower in your manufacturing plant. Reduced time and material waste: Robots optimise workflows and reduce inefficiencies helping to reduce the amount of time required to create products. Along with this, their vastly improved accuracy vs humans ensures that material wastage is much lower. Pairing these two benefits reduces costs and improves your overall ROI. Enhanced plant safety Manufacturing related injuries in the US came in at a staggering 326,400 in 2023, and while this is a 6% year on year drop, more needs to be done to protect the safety of our skilled workers. Robots are a great way to automate especially dangerous tasks in the manufacturing plant, helping our manufacturing workforce to keep fit and healthy. Handling Dangerous Tasks: One of the core tasks that robots can take on is high-risk jobs, such as welding and handling hazardous chemicals – which can pose significant risks to the workforce when tasks are carried out by a human. By offloading tasks like this to robots, your manufacturing business can vastly reduce workplace injuries, whilst also benefiting from improved accuracy and reduced downtime. Taking on Physically Demanding Tasks: Robots are also capable of taking on physically taxing tasks, which most employees will actively look to avoid carrying out, especially on an ongoing, long-term basis. Having autonomous robots on hand to carry out such tasks is a huge benefit, improving employee well-being and reducing the likelihood of employees being off sick with injuries sustained from physically demanding tasks. Flexibility and scalability There’s an ever-increasing reliance on manufacturers being agile to new changes and customer demands, which can be particularly difficult with older workflows. Robots allow businesses to seamlessly retool for various tasks, giving manufacturers who have futureproofed the upper hand over competitors who have not. Reprogramming speed: Modern robots are capable of being reprogrammed or retooled for various tasks. This enables manufacturing businesses to be agile and quickly adapt to any product changes, or the addition of new lines. There’s an ever-increasing requirement that manufacturing firms remain agile to the needs of their customers, and robots’ ability to quickly be reprogrammed into carrying out a totally different task can be a gamechanger for manufacturing firms of all sizes. Modular integration: A key selling point for robots is their ability to be seamlessly integrated into specific parts of a new or existing production line, scaling up as required. The ability to scale as much as needed is a big selling point for manufacturing businesses that are going through periods of growth, equally, the ability to scale back on robots if production slows down too is useful. Data collection and analytics Data collection and analytics are an exceptionally important part of modern manufacturing, as it gives manufacturing managers access to insights to improve performance, outputs and quality – which inevitably improves overall costs and profits. Real-time monitoring: Monitoring the performance of your assembly line, or general production can give some extremely interesting and potentially operations-changing insights to manufacturing plant managers. With insights available on cycle times, downtime and errors, there’s an added layer of data on hand to make informed decisions on. Predictive maintenance: Reducing downtime of machinery is essential to the smooth operation of manufacturing. With robots integrated into workflows, data is available on when machines are likely in need of servicing, along with insights on when a machine might be on the brink of breaking down or becoming inefficient. This allows manufacturing managers to make informed decisions on when to decommission machinery and ensure that there’s no unplanned downtime in the plant. Buddharatn Ratawal is senior manager, strategic business development for the DELMIA brand at Dassault Systèmes |
|
|
|
Can machine learning make it in medical? | 28/07/2025 |
IN A highly litigated and tightly regulated industry like medical device manufacturing, where processes demand strict validation, is full integration of machine learning into production truly feasible? Generative AI, and by extension machine learning (ML), offers manufacturers the promise to predict and react autonomously to a wide range of production situations. But if an automatic adaption involves algorithmic changes to a validated process, does it risk undermining or even invalidating the fully tested and authorised production process? Despite numerous advances in AI and ML, valid concerns relating to safety, transparency, explainability, trust, security, data privacy, interoperability, ethical biases and accountability persist. Several specialists from Sumitomo (SHI) Demag expand on where AI and ML can be usefully applied and why, for process validations in particular, there is still much deep learning to be done. In medical manufacturing especially, robust validation protocols are critical throughout the product lifecycle, including any changes that could impact a product’s quality. There is no wiggle room – zero defects is always the target. Processors cannot simply shift the parameters to suit. When manufacturing a medical device or a sterile implant, nothing less than 100% quality is acceptable. In accordance with ISO 13485 standards, ongoing documentation of the validated injection moulding process needs to be maintained. It is a continuous and scientific process. When machine settings are adjusted to compensate for changes in the environment or to address moulding issues e.g. pulling, distortion, or aesthetic defects, it will trigger a re-validation exercise. So too would major repairs, changes, or improvements to the mould tool and machine. The cost and time implications each time a moulder repeats this validation process can be extensive. Side effects of machine learning Medical business development director Andreas Montag expands: “One of the biggest obstacles to ML in medical manufacturing remains the altering of processing parameters. This is currently referred to as Black Box ML. If the processing algorithm is changed autonomously and it isn’t clear how a machine arrived at this decision, who is held accountable? Although the risk might be minimal, failure to detect any processing errors may cause harm to end users, resulting in a legal investigation.” Altering a validated process using ML is still a long way off suggests the company’s UK and Ireland managing director Dave Raine. “Clear and practical regulations for this type of automated validation, while ensuring medical processes and products continue to meet regulatory and quality standards, do not yet exist. The EU and the FDA is continuing to work on classifications. This could take several years or more to materialise. For medical especially, with its entrenchment in risk mitigation, there is likely to be continued resistance to the adoption of ML automatically adjusting processing parameters.” That being said, for many manufacturing markets, including consumer or packaging, where the focus is on high volume inputs and outputs, the opportunities for reactive autonomous ML are much more extensive. Here, projects have already been undertaken by Sumitomo (SHI) Demag in collaboration with industry partners and academics to calculate the optimal process settings on an IntElect manufacturing cell. One pre-study project proved that the use of automated processing parameters on a non-medical application resulted in 4.5 times faster machine set up times and generated 78 percent less start-up waste. Transferrable technologies The development of activeMeltControl is another example of how adaptive technology is being applied by the company. Integrated into the machine control system, aMC works by continuously monitoring for variations in holding pressure and changeover position. Once a parameter is detected as drifting towards the tolerance limits set by the user, aMC automatically adjusts the set parameters to compensate for the variation. “This is a superb example of how AI can solve a particular processing challenge,” notes Dave. However, even here some human intervention is required as the adjustment bandwidth still needs to be defined by the processor. Montag also notes that AI has accelerated the development of customised medical production cells through more accurate simulations and generative design. AI models and digital twins can help medical processors test concepts before machine builds and installations. “There will always be nuances in every line and every customer production environment. Rather than starting from scratch with each moulding cell, Sumitomo (SHI) Demag draws on our industry expertise and leverages AI to more accurately simulate and predict machine interactions. This ultimately supports design optimisation, accelerates development, factory testing and installation, helps minimise risk and reduce bespoke R&D costs. For time-critical projects, this insight and added context can be invaluable for customers,” explains Montag. AI can also assist with ensuring any URS design requests are both feasible and warranted. This can include adapting tried and tested documentation blueprints to assist customers with scoping out their URS, artwork design, software and functional specifications, ensuring costs and budgets are carefully controlled. Although the sharing of these processes can assist the wider medical community, no secure intel or intellectual property is ever transferred between clients, assures Montag. The initial URS phase is critical, as medical customers rely on it to validate that the injection moulding machine is equipped as specified in the preliminary stage and performs as expected. “There has been much progress in this area too. Machine qualification files, which were once heavy paper documents, are being transferred to digital. Many of these have transportable sections, which can be tailored to each medical application a machine is being commissioned for, without compromising sensitive information,” adds Kris Thacker, the company’s medical technical specialist in Ireland. Additionally, for AI to truly imitate human behaviour, deducing why and how much its changes impact process stability, it needs complete connectivity between all machinery assets. This requires a single data source. Here, interoperability and connectivity between different technologies is a critical stepping stone that enables complex interactions between part quality and machine process parameters, as well as other fluctuating and influential factors, such as cooling, temperature and de-moulding. Rather than focusing on the current limitations of machine learning, the Sumitomo (SHI) Demag team prefers to utilise its more creative and enabling qualities. Montag concludes: “For medical moulders, AI and ML extends way beyond automating changes to prescribed processing parameters. There are many excellent examples of how it drives product development, accelerates decision making, supports scalability and is a catalyst for further process improvements. The disruptions to traditional models, including validated processes, will come. We shouldn’t view this as an existential threat, but an opportunity that assists processors in all sectors with continuous improvement.” |
|
|
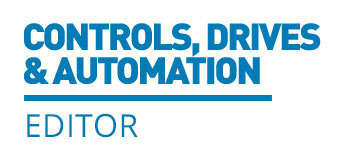
Controlsdrivesautomation.com is filled with carefully selected editorial content that complements the journal and delivers a greater amount of information in its online format with topical and expanded features/articles already showcased in the journal.
All the latest product and application stories will feature online and will be regularly updated with up to the minute news, views and discussion in the areas of motion engineering, power transmission and automation.
Visitors to the site can use the search facility to find exactly what they are looking for or browse a selection of the best and most up to date articles that are highlighted on the home page.
Advertising Contacts:
Sidney Houliston
01342 333737