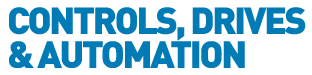
![]() |
Charlotte Stonestreet
Managing Editor |
1/2 (1 to 10 of 16)
Navigating the twin transition | 30/01/2025 |
---|---|
STEFAN REUTHER sheds some light on innovation, trust and the role of Independent Software Vendors (ISVs) for corporate sustainability IN THE ever-evolving landscape of technology and sustainability, the concept of the "twin transition" has emerged, highlighting the simultaneous journey towards digitalisation and sustainability. However, the concept of the twin transition encompasses far more than two simultaneous trends. It also signifies the integration of two areas that sit prominently at the top of the political agenda. The fusion of these areas has the potential to change the world. However, to succeed, a better understanding of the technologies that facilitate them is essential. The evolving role of ISVs in a digitalised world The European Commission’s (EC) report, Towards a Green & Digital Future argues that digitalisation cannot be achieved in technological siloes. “Technologies are not independent of one another. There are several connections and interdependencies between them. In fact, the combination of different digital technologies could in itself be an impactful innovation,” the report states. Data and data analysis are the backbone of the green transition. Independent Software Vendors (ISVs) have therefore become this mission’s indispensable protagonists, due to their agility and adaptability compared to proprietary technology. ISVs boast an ability to break down communication barriers between different equipment and systems, making the data capture necessary for environmental action more straightforward. This is particularly true of large global businesses. Given that many industrial companies grow through acquisitions, a common hurdle for data capture is the communication barriers of legacy systems and infrastructure. Consider AB InBev as an example. The multinational brewing company leads the way for digitalisation in breweries and highlighted the advantages of working with ISVs in a recent interview with COPA-DATA. “Legacy systems may require upgrades or replacements to enable a smooth digital transformation, which can be expensive,” explained Charles Tisdell, Global Director Connected Brewery IIoT & Automation at AB InBev. “This is where partnering with a company like COPA-DATA can help you build the IIoT and data layer while maintaining or migrating away from legacy infrastructure. It enables the use of other niche systems to deliver targeted solutions.” Balancing innovation and trust The advantages of independent technology for the digital and green transitions are clear. That being said, the role of ISVs extends beyond providing technological solutions. Many ISVs are small or medium-sized enterprises (SMEs), giving them a competitive edge over larger alternatives. In a WEF briefing paper, Data Unleashed: Empowering SMEs for Innovation and Success, these businesses are described as the foundation of the global economy, representing 90 per cent of all businesses and nearly 70 per cent of all global jobs and GDP. These organisations are also drivers of innovation. Without the shackles associated with large or listed businesses — pressure from investors, slow research and development and complex organisational structures — small to medium-sized ISVs have a high potential for growth and change. They can contribute fresh ideas and nimble approaches to digitalisation; and therefore, to sustainability goals too. Of course, sustainability is not a compulsory exercise. However, with high energy prices and the climate crisis, ISVs offer a timelier method of embarking on a sustainability journey. What’s more, independent vendors provide opportunities to start small on these journeys and scale over time. AB InBev recommended this model of scaled digitalisation based on their longstanding relationship with COPA-DATA. “Start small and focus on quick wins,” explained Tisdell. “Identify pilot projects or use cases that demonstrate the value and feasibility of digital technologies within your organisation. Learn from these initial experiences, iterate, and scale up gradually.” Choosing a project to improve a business’s environmental impact — for instance, reducing carbon emissions, water usage or waste — is an ideal first step in using technology for the green transition. And all of this can only be started by collecting the right data and its contexts. Open automation Transparency is as key to the success of ISVs as their agility. At COPA-DATA, we believe in open automation. Users of our automation software platform, zenon, are able to select whatever system, equipment or software they choose, and we have developed a system to ensure their ideal set-up communicates seamlessly. This is a stark contrast to the limitations and restrictions of proprietary software. Not only do we take our no-code-approach to provide customers with freedom of choice, but also to facilitate their digitalisation and sustainability goals. Moving away from silos and vendor lock-in, and towards open data sharing is the only way we can empower businesses to understand their data and take action to improve their environmental impact. Future challenges of sustainable digitalisation The twin transition is not simply concurrent digitalisation and sustainability efforts; it's also a delicate balancing act. Digitalisation can either support or impede the journey towards net-zero goals. According to the aforementioned EC report, the IT industry’s contribution to greenhouse gas emissions was estimated to be between 3 and 3.6%of total global emissions in 2020. That’s not to mention the colossal energy consumption of global data centres, consuming around one per cent of the world’s electricity already in 2018 – rising sharply. As developers of digitalisation platforms, we see it as the role of ISVs to initiate projects that provide added sustainability value. We cannot solely focus on the sustainability goals of our customers — many of which focus on firsthand economic outcomes — but we must also consider the environmental impact on wider society and the planet. ISVs play a crucial role in shaping the intersection of digitalisation and sustainability. As the twin transition converges these two areas of business transformation, it is crucial that organisations consider the potential of ISVs to provide innovation, adaptability and transparency during this significant business change. Stefan Reuther is member of the executive board at COPA-DATA |
|
|
|
Take a load off | 20/04/2023 |
When dwindling grid capacity meant West London was struck with a proposed ban on building new homes last year, a lack of technology also played a part. Martyn Williams explains why the UK must embrace energy grid technology to sustain the nation’s growing energy needs IN THREE West London boroughs, a large number of datacentres nearby has contributed to a significant drain of energy While there is no doubt the scale of energy consumption from these facilities is colossal, the question of where energy is being used is actually irrelevant. The real consideration should be how load consumption on the grid is being managed. Load management Load consumption simply describes the way in which energy is being used on the grid. Load management describes the active control of this consumption, and is sometimes referred to as demand side management (DSM). Load management is an essential component of any smart grid, but the technology is not always in place to oversee this effectively. In an area like West London where consumption is high, load management should be able to use sophisticated energy calculations to optimise consumption. In an area with a large number of data centres, for instance, this technology could analyse historical energy consumption data to estimate when energy use will be high, allowing operators to act accordingly. To facilitate this, the grid needs to invest in technology capable of analysing the huge volumes of data produced across it. Industrial energy software, zenon, from COPA-DATA offers a dedicated zenon Load Management module to collect, analyse and visualise this data for a grid operator. Crucially, the zenon software platform is deployable across number of drivers, and supports the energy standards IEC 60870, IEC 61850 and DNP3. As a result, a wide range of data sets can be included within the scope of the platform. Software-based load management Once this data has been analysed and visualised effectively, it can inform a number of energy saving strategies. This includes load shifting, the of moving energy consumption from peak to off-peak hours to ensure consumption is either precipitated or postponed. Load shifting, which sees load reduction performed in peak hours through direct control of customer loads, or valley filling, where the energy load is increased in response to either high production or low consumption. Achieving this is not possible without oversight of energy consumption across the grid and this requires investment in effective energy grid software. This technology is essential for the energy grids of the future. to manage the nation’s growing demand for power. The proposed ban on building new homes in West London is set to last until 2035, when the Greater London Authority (GLA) believe grid capacity could realistically be increased. However, waiting until 2035 simply isn’t feasible or necessary. We have the technology — and importantly, the energy — to deliver this today. BESS for renewables Another area of concern is the lack of investment into battery energy storage systems (BESS). A significant percentage of renewable energy generated in the UK is wasted due to inadequate storage. Between 2015 and 2021, the country lost 13 per cent of total wind power and between 2020 and 2021, £806 million of all renewable energy was lost. The so-called lack of capacity on the energy grid is not a production problem, but an investment problem. In instances like West London, a large scale BESS can help to cover demand without creating the need to reinforce or rebuild powerlines. These facilities can be located at strategic sites in the grid to create virtual powerlines — a method to describe transferring energy from generation to BESS during low-demand periods to build a pool of electrical energy closer to the user‘s location. In combination with effective load management technology, BESS can provide energy to homes in areas where usage is high to cover peak demand. Martyn Williams is managing director of COPA-DATA
Key Points
|
|
|
|
Weak links in smart factories | 18/01/2021 |
As Reinhard Mayr explains, asset management is critical for ensuring security in industrial infrastructure and production plants For both sprawling energy grids and manufacturing facilities, ensuring industrial security is vital. However, managing security in established manufacturing plants is often very complex. Because the infrastructure has been in place for long periods of time, sometimes upwards of 20 years, its equipment is often lacking in modern security features. Older plant machinery is sometimes referred to as brown field equipment and is often designed and installed without consideration for cyber security. Let’s face it, at the time of manufacture, the concepts of machine-to-machine (M2M) communication and smart factories were still futuristic ideas. The problem is smart factories are no longer an aspiration, but commonplace. Securing legacy equipment Today, brownfield equipment is often intertwined with newer machinery on complex industrial networks. These networks are enriched with a plethora of smart devices and machinery — all of which can communicate between one other. I won’t go into the obvious advantages of smart factory equipment, but what are the risks of integrating these devices with their older, less secure predecessors? Unsecure devices provide a weak link in a network. While newer equipment may be protected against attacks, a weak spot will provide an infiltration point for an attacker to enter the network and gain further access. In the Ukraine power grid example, hackers spent several months conducting straightforward phishing techniques to gain access to the corporate network. This was managed by encouraging workers to open a Microsoft Word attachment. This initial intrusion provided limited access to the network, but it allowed hackers to orchestrate an extensive reconnaissance effort to identify further opportunities for advancements. Unprotected production equipment can provide a similar starting point for cyber attackers. To minimise the risk, plant managers must implement a security strategy that considers these older, non-secure assets. Asset management The first and most painful step of asset management is conducting an audit of equipment in a facility. Let’s face it, a plant manager cannot secure what they are not aware of. Thankfully, there are tools to simplify the process. Radiflow’s iSID Detection and Analysis Platform, for instance, can be used to identify vulnerabilities in OT networks. When integrated with data from an existing SCADA system, like COPA-DATA’s zenon, it can audit the entire facility with ease. Once all assets are visible, the next step is to define ‘zones’ of different devices. As defined in the IEC 62443 standard — the global standard for the security of Industrial Control System (ICS) network — a zone is a grouping of independent assets that possess a set of certain characteristics and security requirements.
By defining zones, plant managers can limit connection points to each zone as appropriate
By defining zones, plant managers can limit connection points to each zone as appropriate. For instance, limiting access points to the OT network or any areas in which there are high consequences for a security breach would be a sensible approach. As COPA-DATA is certified in accordance with IEC 62443, zenon offers a series of features that can speed up the asset recognition and zoning process. Using its Multiple Project Administration tool, an operator can determine several asset zones digitally and visualise these zones in a central control room. COPA-DATA is the only provider to offer this tool. Ongoing improvement It would be foolish to believe that once a cyber security strategy has been implemented, plants are completley protected against cyber attacks. This was a harsh lesson for the Ukraine power grid, when it was attacked for a second time in 2016. The second attack was more sophisticated and used automation tools to speed up the process. Using this technology, hackers programmed the system to send repeated commands to equipment to switch the flow of power. The attack performed blackouts more quickly, with less preperation and with fewer humans involved than the first instance. Ukraine’s example should be a stark reminder that, as the sophistication of hackers grows, cyber security strategies must advance too — that goes for national energy grids and manufacturing plants. Reinhard Mayr is head of information security and research operations at industrial software developer, COPA-DATA
|
|
|
|
Secure communication in the energy industry | 21/10/2019 |
Jürgen Resch, Energy Industry Manager at COPA-DATA, explains the importance of end-to-end secure communications in the energy sector and the need for the IEC 62351 standard Back in 2017, headlines reported that hackers had shut down monitoring systems for oil and gas pipelines across the United States. Alarmingly, insecure third-party systems in SCADA platforms were to blame. Unfortunately, the attacks on oil and gas pipelines case are not a rare example. The following year, cybercriminals also gained access to the United Kingdom's electricity system. The group phished its way into energy systems using a phony word document CV for a man called ‘Jacob Morrison’. Once infiltrated, the group took screenshots of the system, leading experts to believe the hackers were spying to learn how every aspect of the system works. Attacks like this continue to be a huge concern for the energy sector, particularly if the hacker manipulates data. For example, a cybercriminal could hack a business’s energy controller and change the threshold values of a reaction, or worse. They could maliciously lower the perceived voltage measurement of an energy customer, so the controller thinks the voltage is lower than what it really is. The controller would then increase the voltage at the customer site, exceeding tolerances and destroying power supplies. Where there is high risk, there needs to be high levels of protection. Time for change Many of the energy meters, switches and controls in power plants and substations were designed years ago and as such, only have basic password protection. Criminals know this, so the industry needs to react. Despite such high-profile attacks, energy security is a shockingly new topic for many in the sector. Even when LAN based technologies such as IEC 60870-5-104 or DNP3 TCP came into play in the late 1990s, concerns about data hacks or data protection were not prevalent.
older communication protocols are out of date and must be retrofitted with security features
Today, these older communication protocols are out of date and must be retrofitted with security features that can prevent modern security threats. To make security even more challenging, the energy grid is no longer confined to its physical structure. The ever-developing smart grid takes energy systems into the cyber-physical world. With data sent trough and stored in the cloud, energy data could become even more vulnerable if security standards are not updated. IEC 62351 IEC 62351 is the current standard for security in energy management systems and the exchange of energy-related data. It focuses on the major requirements for secure data communication and processing, including confidentiality, data integrity and authentication. The arrival of the IEC 62351 filled a huge void for energy security, bringing the existing non-secure communication protocols up to speed. The standard was defined by the IEC TC 57, the technical committee responsible for the development of standards for information exchange. By applying the IEC 62351 security standard to protocols 60870-5-101/-104, DNP3 and IEC 61850 among others, it is possible to achieve end-to-end security for energy data systems. The standard series dictates the need for encryption and access control through authentication and authorization. For example, Transport Layer Security (TLS) encryption is defined by IEC 62351-3. However, applying IEC 62351 is not a one-time task. Once implemented, the security mechanisms need to be maintained and updated continuously, in line with changing security threats. Building readiness Engineers can now create energy automation applications in accordance with IEC 62351, using the zenon software platform for energy automation. COPA-DATA is continuously implementing the standard step by step in its software platform zenon, and it is already possible to harden the communication by TLS. Improved security doesn’t change the user experience of the fully secured zenon application, although additional password changes and certificate renewal will be required — a small price to pay for optimal security. |
|
|
|
Three advantages of IT/OT convergence | 20/05/2019 |
Engineers and academics have been extolling the benefits of IT and OT convergence as far back as the early 1980s, but many businesses are still reluctant to adopt platforms that combine the two. Here, Martyn Williams, managing director of industrial software provider COPA-DATA UK, explains the advantages of IT and OT convergence. In a 1982 paper published by the US National Institute of Standards and Technology (NIST), the authors proposed a new control system architecture for use in an Automated Manufacturing Research Facility (AMRF). In a diagram reminiscent of a castle, the shapes that make up the control system appear to create two fortified tower-like structures joined by a flat wall-like section in the centre. The tower on the right depicts a hierarchical database that contains the control programs that define how to manufacture parts — think of this as the operational technology (OT) of today. The tower on the left makes up the hierarchical database that contains the management information system and data on the state of the parts — think of this as information technology (IT). Finally, the wall in the middle is made up of I/O lines and feedback control loops connected to boxes that represent robotic workstations and machine tools. While these structures were symptomatic of their time, they have historically separated IT and OT teams both figuratively and literally, with staff often working in different departments or even different facilities. In contrast, today’s control architectures have broken down the rigid structures, replacing them with highly integrated and free-flowing systems that are flexible and easy to change based on business needs. Advantage one: Profit Whether you call it digital transformation, the Internet of Things (IoT) or Industry 4.0, the primary driver for businesses seeking automation improvements is to bolster the bottom line. At a time when political uncertainty is driving up the cost of doing business, many organisations are looking inward, searching for those all-important marginal gains. The convergence of IT and OT not only benefits from the resource sharing of connected devices, but it also promises to boost productivity. Better scheduling, production planning, material allocation, product tracking and real-time access to process data are quick and easy with the two realms working in sync. This is why COPA-DATA developed zenon, a manufacturing and automation software platform that provides a single, integrated environment, combining data recording, machine operation and business intelligence. Using zenon, manufacturers can eliminate the redundancy and cost associated with running two separate overlapping IT and OT systems, delivering better performance and productivity. Advantage two: People The second major benefit of combining IT and OT is to allow staff on both sides to overcome their differences. Cybersecurity, decision-making, scalability and downtime are just some areas that can put IT and OT staff at odds with each other. Take downtime, for example. In mission critical applications such as food and beverage production, where unexpected downtime could result in spoiled produce, OT staff may be responsible for getting the line back up and running as quickly as possible. IT staff, on the other hand, may be responsible for ensuring data integrity for traceability purposes and will therefore prioritise this task. In this situation, a software platform such as zenon can help IT and OT staff collectively solve their problems. zenon’s network technology features seamless and circular redundancy and high availability, so that downtime is eliminated. For engineers, it also offers post-event fault analysis and allows operators to reload modified functions without having to restart the system. Similarly, data archiving allows IT staff to immediately retrieve and store traceability data. Advantage three: Place Business theory dictates that if you want to make it difficult for your competitors to enter your market, you need to put up barriers to entry. This includes technological, regulatory or economical hurdles that you’ve spent years overcoming, and ones that make it unattractive for new entrants to replicate. Take sugar refining for example. Because the harvesting window for sugar cane is so narrow — typically three months from December to March — manufacturers are under pressure to ensure that they can quickly setup the plant for seasonal production. What’s more, the process of turning raw sugar cane into the processed sugar we’re familiar with is a complex one. This involves many steps including shredding, milling, juice extraction, clarification, evaporation, syrup production, crystallisation, centrifugation, drying and packaging. All these processes need to be carefully co-ordinated as any downtime can be critical to the success of the final product. If the refining process doesn’t align perfectly with the harvesting window manufacturers may suffer from perished crops and lost revenue. Here, the integration of IT and OT is essential in democratising automation, levelling the playing field and facilitating business growth. To allow customers to achieve this, we’ve ensured zenon supports open standards such as OPC UA, as well as being built with over 300 open interfaces and native drivers. The platform runs on common industrial clients and operating systems and offers visualisation using standard HTML5 web technology. Take advantage now As the industry breaks down the rigid barriers of traditional engineering structures, we’re seeing how powerful digital platforms can be in underpinning the sustainable convergence of IT and OT. The advantages are clear, it’s time for businesses to act. Maybe in another forty years, engineers will look back and wonder why industry was so reluctant to topple the figurative IT and OT castles. |
|
|
|
The end of the automation pyramid? | 18/03/2019 |
Stefan Reuther Chief Sales Officer at COPA-DATA, explains why IT/OT convergence will lead to the collapse of the automation pyramid As a pictorial example of the different levels of automation in a factory, the automation pyramid has long been used as a visual aid to understand how layers of technology communicate. Starting from process and field levels, working up to the corporate level of manufacturing processes, the traditional pyramid illustrates how devices, actuators and sensors on the factory floor are distinctly separate from other areas, such as process control, supervisory networks and enterprise systems. The automation pyramid was theorized in the 1980’s, when comprehensive control software was practically unheard of. Today however, this software is becoming ubiquitous to the operation of manufacturing facilities. So, where does this leave the automation pyramid? Put simply, the traditional concept is collapsing. Traditional practices Comprehensive control software is a relatively new addition to manufacturing plants, but that is not to say software was completely absent from historical factories. Human Machine Interfaces (HMIs) were the first example of using software to visualize data on a factory floor. However, because each piece of equipment and relative HMI operated a standalone device, the insight was limited. For an overview of production in its entirety, Supervisory Control and Data Acquisition (SCADA) systems were implemented to collate data from multiple HMIs. Usually, these systems generated a graphical interface to help operators understand and control multiple systems. However, this still leaves a space between the SCADA level and enterprise systems, the final level of the automation pyramid. As a result, Manufacturing Execution Systems (MES) were deployed to bridge the gap. The automation pyramid was born. The automation pyramid is a widely understood manufacturing concept. However, it would be absurd to suggest this 30-year-old approach to managing automation levels fits today’s manufacturing climate. Today, managing these processes in a single, comprehensive software platform is not unrealistic. In fact, COPA-DATA’s zenon , a software which enables data exchange between all layers of automation, has been demonstrating this ability since the software’s inception. The traditional automation pyramid is no longer necessary. However, many manufacturers are reluctant to abandon the traditional concept. Technically speaking, manufacturers can still choose to manage their levels of automation using this traditional pyramid method. However, there are scenarios where it makes no sense to stick to this model. Collapsing the pyramid IT/OT convergence is just one example. Manufacturers are widely practicing IT/OT convergence to integrate enterprise systems, such as Enterprise Resource Planning (ERP) and Customer Relationship Management (CRM) applications, with operational technology like MES and SCADA systems. Traditionally, these areas have remained separate layers of the pyramid, but their ability to influence a company’s performance means it makes business sense to allow these layers to communicate and inform one another. Consider automotive manufacturing as an example. There are huge planning benefits of integrating CRM data with both ERP and car production. If an engineer can identify the fault in the manufacturing of the product, by analyzing CRM and maintenance data, production can be automatically adjusted to correct the error. Of course, this is just an example, but IT/OT convergence is occurring in almost every sector. The traditional automation pyramid doesn’t allow for fluid communication between its different levels, importantly, the control level as it might be possible today. Considering that logic can be placed practically everywhere in a manufacturing facility, such as PCs, PLCs, edge devices and in the cloud, it makes no sense to separate this area. Egypt’s pyramids may be ancient in comparison to the engineering concept of the automation pyramid. However, considering the rapid pace of change experienced in the manufacturing industry, it could be argued that the concept is equally outdated. To reap the benefits of the technology available in industry, manufacturers must look beyond rigid and traditional pyramid structures. |
|
|
|
ROI as a goal in the smart factory | 21/08/2018 |
Research from Barclays Corporate Banking shows over half of manufacturers are reporting improved productivity thanks to the adoption of I4.0 technologies; yet two thirds state they are yet to experience a return on investment. Here, COPA-DATA UK's Lee Sullivan explains the steps manufacturers can take to boost ROI ROI is a priority for manufacturing. However, making radical changes to a factory is not always a feasible option. A complete systems overhaul, for instance, could be the quickest and most straightforward way to optimise production. However, it can be incredibly costly and comes with high risk, and possibly long periods of downtime — not to mention cultural challenges that accompany a shift in how a factory operates. Instead, most factories will choose to make small incremental changes to increase their overall equipment effectiveness (OEE) and, in turn, improve their ROI. The process of improvement usually begins by recognising limitations in the factory or within certain processes. This could be related to plant production time or plant performance management, equipment failures, product defects or even a lack of human skills to manufacture. However, without hard data, identifying these constraints can be time consuming, if manually completed, and complex. Therefore, software is recommended to simplify the process. Monitoring and data acquisition software can quickly identify baseline figures for major losses in throughput across the production plant or the product manufacturing process. This data should be collected over a set period of time. From here, manufacturers can identify the most critical or valuable place to start improvements. CI, of course, is not a new phenomenon, but digitisation of lean manufacturing losses is. This would enable easy analysis and correlation with productions figures, showing potential areas for improvement in a factory which in turn will help to increase ROI. Reducing waste Being able to monitor OEE, total productive maintenance (TPM) and CI would highlight potential areas for improvement, but also identify whether improvement projects established have facilitated the manufacturing process. For example, a measurable indicator which can lead to improved ROI. Waste reduction is an example of CI. This term describes the non-value-added wastages that absorb time and money. Eliminating waste is a vital part of the lean manufacturing methodology and is often the first step to improving processes. Using monitoring software, these wastages can be digitalised and monitored, offering manufacturers the knowledge to minimise poor quality. In fact, a COPA-DATA customer in the automotive industry was able to save 5 per cent on man hours per employee using digital fault logging. Take the waste of waiting as an example. In a manufacturing facility, this could describe a halt in production due to a delivery delay, unplanned system downtime or wasted minutes or hours due to poorly planned production schedules. Using software, this waste can be digitally recorded and reported, identifying the reasons why a delivery has not arrived, why certain machines are not hitting their cycle times or when pieces of equipment are entirely idle. Waste reduction can also be achieved by using software for statistical process control (SPC) reports, a method of measuring and controlling quality during manufacturing. Naturally, well defined production and product processes will reduce scrap waste. Cutting down variability will not only improve quality in assembled parts but could reduce customer complaints and improve sales through customer satisfaction. COPA-DATA’s industrial software, zenon, can generate SPC reports automatically, recording process capabilities which, in turn, shift factories towards boosting ROI. Increasing ROI may be a priority for manufacturers but investing heavily in a software overhaul can be daunting. A dramatic overhaul not only generates risk but could create cultural challenges for the plant. zenon is fully scalable. This means that end users do not need to jump straight into the deep end and deploy the software on every value stream area. They could begin with a smaller system, such as capturing downtime and throughput. Upon analysing the results of this metric, manufacturers can begin to measure other areas for improvement, such as production quality, CI projects, mobile connectivity, recipe groups, or even begin vertical integration by linking the software to enterprise resource planning (ERP) systems and cloud solutions. Manufacturers expect to experience a rapid ROI after adopting new technologies — whether it be robotics, automation, sensors or enterprise software. According to Barclays Corporate Banking research, these investments are reaping productivity rewards for manufacturers. However, without identifying areas for improvement, how can manufacturers optimise their facilities to their full potential? The answer is in their data.
Key Points
|
|
|
|
HMI design in the age of the Smart Factory | 04/04/2017 |
The concept of user-defined HMI, which adapts itself to a specific user or situation, makes information handling easier and speeds up process reaction time. Zenon screen & interaction designer Anita Perchermeier explains briefly how it works Companies must make many adjustments to transform a manufacturing site into a smart factory - one of which is with the HMI. The demand for a variety of data and information is constantly changing. Different users have different needs. A good HMI will have taken this into account and have the ability to amend itself according to the user, context and requirements.
demand for a variety of data and information is constantly changing
Data requirements, the type of information and the amount of information, change ever more quickly. As a result, the context in which a machine is operated also changes. In addition, different users have different requirements. For example, a manager may like to have an overview of the production figures, but a machine operator needs information from sensors. A person who is colour bind needs higher screen contrasts. A user-defined HMI thus offers the best way to work with such varied requirements. Zenon is an open-design, object-oriented industrial automation application developed by the Austrian company COPA-DATA. It is used by many companies around the world for process visualisation, as a Human-Machine-Interface (HMI) and as a Supervisory Control and Data Acquisition (SCADA) system. Its openness makes fast, efficient interfaces with any hardware or software possible. Process gateway Zenon communicates via standard interfaces such as COM, ActiveX, XML or its own process gateway. It can also communicate with many proprietary interfaces, including RFC/BAPI (as used by SAP). All the control connections are programmed in-house at COPA-DATA, fine-tuned for the target system and then exhaustively tested. Zenon also has a process gateway, to allow other systems to address it as a PLC; this, for instance, enables direct communication via Modbus or OPC UA. Different user level privileges allow locking to be set up and control the visibility of elements. This is not just for security, but can also be used for individual user support: a beginner is instructed with more explanations and buttons, while an expert prefers a “short cut” for frequently-used actions, without explanations being shown. Experts also have advanced operating options available, which are not visible for beginners. Different filter profiles (such as time filter, AML filter or trend display settings) can be created for each user and thus optimally display relevant information according to each user and each task. In addition to context-based user support, general ergonomic requirements should also be kept in mind, which differ from user to user. A user-defined HMI helps here too: different colour palettes can be created, depending on the time of day, lighting conditions or personal preferences. Zenon Chameleon Technology allows switching between different skins with a single click. This enables, for example, various colour sight deficiencies or the corporate identity of a company to be taken into account. Screens can be configured with the help of free-form templates and freely positioned using Touch. If they are not required at a particular moment, they are hidden at the edges of the monitor. Depending on whether the user is right-handed or left-handed, windows and dialogues can be arranged as desired, according to the process and the task. The user interface settings can be saved individually with the help of Runtime profiles.
Key Points
|
|
|
|
IT/OT convergence: challenges & benefits | 13/09/2016 |
The convergence of industrial automation and communication is an integral part of the growing Industrial Internet of Things (IIoT). Martyn Williams, MD of COPA-DATA UK, explains the changing responsibilities of IT and OT. IT and OT convergence describes the integration of IT systems, such as Enterprise Resource Planning (ERP) and Customer Relationship Management (CRM) applications, with OT systems, such as Manufacturing Execution Systems (MES) and Supervisory Control and Data Acquisition (SCADA). Traditionally, IT and OT have remained two separate silos, maintaining independent protocols, standards and governance models. However, for companies pursuing operational effectiveness, increased profits and growth, the convergence of these two systems is a no brainer. Reaping the rewards As IT and OT independently influence a company’s performance, bridging the gap between these technologies allows for easier performance management. Regardless of whether a manufacturer wants to increase operational effectiveness or generate growth, there is a strong case for pursuing IT and OT convergence. Creating a common platform for both information and operational data means businesses can generate more relevant key performance indicators (KPIs) and pursue common objectives while also benefitting from company-wide visibility. Greater transparency of operations means harmonising business strategies across geographical sites and departments is much simpler. For the food and beverage industry, for example, a cider producer would benefit from integrating third party IT, such as weather data and consumer marketing activities with internal IT systems and OT on the factory floor. Cider producers will want to know if there’s a sunny weekend on the horizon, as customers are likely to buy more alcoholic beverages. By integrating this data with an ERP or MES connection, intelligent SCADA software can download the required production plan and ingredient quantities and communicate exact control parameters to the connected process equipment to begin production. Not only does this speed up time-to-market and reduce costs, but also allows for on-demand manufacturing that business to consumer manufacturers experience on a daily basis. There are many notable benefits of IT and OT convergence, but in the manufacturing world, this transition is not without its problems. Challenging the status quo Manufacturing is not always the quickest sector to embrace technological change, especially where OT and hardware are concerned. On the other hand, IT departments usually have a positive approach to embracing new technology. When outlining a common governance model, these cultural differences can cause friction. Successful implementation of IT and OT convergence requires a substantial change management effort so that the entire workforce is on board with the project. In most cases, this often involves remodeling and retraining the workforce or changing processes and procedures. Another worry for manufacturers is the changing security risks the merger of IT and OT brings. For industrial control systems, security cannot be an afterthought. However, by following standards and best practices of IEC 62443, companies can significantly minimise their security risks. IEC 62443 is a standard that directly addresses IT security for industrial automation and control system (IACS) networks. Under this standard, manufacturers must address both the technical and organisational aspects of how employees access and use the network, therefore enhancing security against external threats. Finding a native language Bridging the worlds of IT and OT could provide manufacturers with the competitive advantage needed to gain both marketspace and market share, but it is no easy feat. Successful implementation requires a deep understand of each system involved, including the industrial and IT systems, devices and networks. Independent and flexible automation software, like COPA-DATA’s zenon, provides a native language to connect these systems in an efficient and seamless manner – while still providing production monitoring, data arching and reporting throughout the production process. Native communication also has the benefit of being independent of any hardware manufacturer, ensuring easy integration for both new and legacy systems. Over the last few decades, manufacturers have approached IT and OT as entirely separate domains. However, the convergence of these two manufacturing layers is rewriting the industry rules. By finding a native language between both processes, manufacturers are reaping the rewards of enhanced performance and increased manufacturing flexibility. |
|
|
|
Cloud computing for smart manufacturing | 26/04/2016 |
The analytic advantages of cloud computing in industry are no secret with many users actively pursuing cloud-based analytics to gleam greater insights and efficiency in order to achieve business goals, says Martyn Williams, managing director at COPA-DATA UK. For the manufacturing industry, the benefits of migrating to cloud computing have been heavily publicised, but in an industry that has been slow to embrace new technology, a mass move to the cloud can feel like a leap in the unknown. Despite an increased adoption of smart manufacturing technologies, some companies may still feel hesitant. Instead, many decide to test the water by implementing a cloud storage model in just one production site. However, this implementation model can only provide limited benefits in comparison to a mass, multi-site migration to the cloud. So what should companies expect to undertake during their cloud migration? Define business objectives Before migrating to the cloud, companies should first consider how it can help them achieve -and in some cases refine - their business objectives and plan their migration with these objectives in mind. For businesses that want to improve collaboration and benchmarking across multiple locations, for example, the cloud plays a significant role. A company with multiple production sites operating in several locations will be familiar with the complications of cross-facility benchmarking. Often, business objectives or key performance indicators (KPIs) are only set for single site locations. In an ideal situation, the business objectives have to be coordinated across all locations to offer a clear, company-wide mission. To achieve better collaboration and transparency across sites, companies can resort to using a cloud storage and computing application that gathers all available production data (from multiple production sites) in one place. Certain individuals or teams in the company can be granted access to relevant data sets and reports, depending on their responsibilities within the organisation. Determine the ideal status Once a business objective is clear, companies should identify what the ideal status of each process is. By using production data and energy information stored and analysed in the cloud, a company can gain insight on productivity, overall equipment effectiveness (OEE), energy usage and more. This insight helps companies make changes that will bring the existing production environment closer to the ideal status. Combined with the right SCADA software, the cloud unlocks rich company-wide data sets. By bridging information from different facilities in real-time, the software generates a bird’s eye view of company-wide operations and detailed analysis of energy consumption, productivity and other operational KPIs. This makes it easier for a company to monitor progress against the original business objectives and scale up or down when necessary. Already, a large number of manufacturers are using industrial automation to speed up production and increase efficiency. With the large scale adoption of intelligent machinery, cloud computing is poised to become the obvious solution to store and manage the complexity of data this industry connectivity creates. Unlike the restrictions associated with on-premises storage, cloud based models provide unlimited scalability, allowing companies to store both real-time and historical data from all production their sites and integrate any new production lines or sites to their cloud solution in a seamless manner. When accompanied with data analytics software, like zenon Analyzer, cloud computing can help companies prevent potential problems in production and even ignite entirely new business models. Continuous improvement For manufacturers with strict energy efficiency and productivity targets, easy access to company-wide data is invaluable. However, the knowledge provided by the cloud does not end with past and present data, but also gives manufacturers a glimpse into the future of their facilities. By using the cloud, companies can implement a long-term continuous improvement strategy. Often, continuous improvement will follow the simple Plan-Do-Check-Act (PDCA) model often used in energy management applications. This allows companies to make decisions based on data analytics and to evaluate the effectiveness of those decisions in the short and medium run. Using data collected from industrial machinery, companies can also employ predictive analytics technology to forecast why and when industrial machinery is likely to fail, which also means they can minimise costly downtime. Predictive analytics allows manufacturers to identify potential problems with machinery before breakdowns occur. Avoiding expensive overheads for production downtime and costly fines for unfulfilled orders, the priceless insights predictive analytics can provide is the obvious solution to such costly problems.
|
|
|