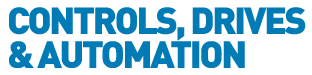
![]() |
Charlotte Stonestreet
Managing Editor |
1/3 (1 to 10 of 24)
Auto-mate: Why automation can be a business’s best friend | 10/01/2019 |
---|---|
Automation and the manufacturing/production industries are no strangers; they’ve been bosom buddies since the 1970s and have been quietly reshaping business for almost half a century. Few sectors have embraced automation so much and for so long. However, the world is changing and some within the sector are being left behind. Seismic advances in technology – from Artificial Intelligence (AI) and machine learning to the Internet of Things (IoT) and sensor technologies – have redefined what’s possible through automation, giving organisations renewed opportunity to transform processes, strengthen safety and increase efficiencies. Yet few are exploiting it – and of those that are, many aren’t leveraging it as much as they could or indeed should. It’s a curious case. Because in time-critical production environments where every second counts, automation can be a business’s best friend. It’s time to shake hands with the future. A recent Forbes survey suggests that a high majority (90%) of businesses recognise the importance of equipping workers with the best technologies to fulfil their roles – but only 36% of executives believe they are meeting these obligations. In the same survey, the potential automation of workforce tasks is highlighted as a positive opportunity, with 43% of respondents – the highest segment – believing it empowers workers and allows them to focus on ‘higher-value activities’. Yet too often it remains overlooked. The benefits of automation are particularly significant in high-risk production environments, where inefficient processes and poor communications can have a major impact on productivity, profitability and, crucially, workforce safety. Maintaining the ability to respond to critical alerts in a safe, timely fashion is paramount. In this vital area, automation isn’t a luxury, it’s a necessity. A large number of organisations believe they’ve addressed the challenges of operational visibility to ensure they’re better placed to respond to critical incidents. Many have invested heavily in sensor technologies that connect machine processes to sophisticated control centres and give central operators good visibility of operations across multiple sites and locations. However, too often, they fail to join up the dots and automate the final step of the process that connects a critical alert with an appropriate response. This piles pressure on central operators to a) pick out urgent alerts from the everyday fog of more routine warnings and b) mobilise a prompt, appropriate response. Often, the escalation of alerts is a human process that relies on manual contact and archaic communications mechanisms. As a result, the speed of response is, at best, sluggish and, at worst, a hostage to fortune. This need not be the case. The next generation of automation tools can relieve the pressure on central operators and trigger immediate alerts directly to the most appropriate response teams. Moreover, they can empower recipients with detailed information on the nature of the problem and provide a clear, auditable mechanism to show a job has been accepted and action to resolve it is underway. The good news is that these transformative automated tools are not only available today, they’re eminently affordable and simple to deploy. The progressive organisations that have already adopted them are unlocking major productivity and efficiency gains and increasing competitive advantage. What’s more, in industries where workers operate in ATEX zones, these automated processes can function via ATEX-approved devices, helping companies maintain a safe, productive and connected workforce. Modern technologies are providing production and manufacturing organisations with a great opportunity to increase workforce autonomy, strengthen workplace safety and drive efficiency. The downstream impact on productivity and profitability can be huge. To maximise the opportunity – and fuel the factories of the future, today – it makes sense to partner with a technology specialist who can examine your business and identify the areas where automating machine-to-machine and machine-to-human processes can significantly bolster your operations. |
|
|
|
Should robots pay taxes? asks Nigel Smith of TM Robotics | 10/01/2019 |
The world’s first robot tax was introduced in South Korea last year. The tax was created amid fears that a rise in automation and robotics was threatening human workers and could lead to mass unemployment in the country. But, this so-called robot tax was not actually a tax at all. Instead, the country limited tax incentives for investments in automation, lessening the existing tax breaks for automation. Calling it a tax was simply rhetoric delivered by its opponents. Essentially, it was just The world’s first robot tax was introduced in South Korea last year. The tax was created amid fears that a rise in automation and robotics was threatening human workers and could lead to mass unemployment in the country. But, this so-called robot tax was not actually a tax at all. Instead, the country limited tax incentives for investments in automation, lessening the existing tax breaks for automation. Calling it a tax was simply rhetoric delivered by its opponents. Essentially, it was just a revision of existing tax laws. Regardless of its name, South Korea’s announcement sparked several debates as to whether a robot tax would be advantageous in other countries. At the time, Bill Gates famously called for a technology levy, suggesting that a tax could balance the Government’s income as jobs are lost to automation. The levy was suggested to slow down the pace of change and provide money for Government to increase job opportunities in other sector. While most manufacturers and those operating in the robotics sector would disagree with the idea of a tax on robots, the debate does raise questions of how we tax employment in Britain — and how technology could affect this. The obvious fear at Government level is that if we replace people with robots, we reduce national insurance contributions, lessening a Government’s ability to support its people. As an alternative, perhaps the answer to this problem is switching to a system where, rather than paying tax per employee through national insurance contributions, NIC was formulated based on a company’s overall operating costs. Using this method, NIC could take account of the impact of all forms of advanced technology, not just robot.That being said, we are not tax experts at TM Robotics. However, we are experts in industrial robots. We sell industrial robots to manufacturers across the globe and advise them on how robots can increase productivity, efficiency and in turn, create new job. Much of the debate about the potential robot tax has focused on the threat that robots and automation pose to humans. However, we should remember that robots don’t always replace a human job, often they work alongside people to reduce the risk of injury — particularly in the supply chain. Consider this as an example. TM Robotics recently introduced a robot box opening cell to its range of industrial equipment. This type of automation would typically to be used by companies like DHL and UPS who are delivering product directly into manufacturing plants and retail warehouses to allow them to reduce the risk of injuries from knives. In this instance, a robot tax would undermine a company’s ability to deliver a safe environment for its workers. The bottom line is that robots create jobs, they don’t take them away. This is supported by the UK Government’s recent Made Smarter review on digitalisation in industry. The review concludes that over the next ten years, automation could boost UK manufacturing by £455 billion, with a net gain of 175,000 jobs. Robots are tools and they will create work, especially new kinds of work — taxing them would be a tax on net job creation. Instead of implementing a tax on robots, we should actually be providing tax breaks for companies investing in robotics. |
|
|
|
Predicting the future | 31/01/2018 |
The fourth industrial revolution is well underway and as state-of-the-art technology drops in price, many more industries are benefiting from smart factories. As a recent PwC survey found 72 per cent of companies expect to achieve advanced levels of digitisation by 2020, the reach of these technologies is only set to increase in 2018. Here, Nick Boughton, sales manager at systems integrator, Boulting Technology, shares his predictions for 2018. In November, the UK Government announced that 2018 would be the Year of Engineering. This coupled with the launch of the Government’s Industrial Strategy and Made Smarter Review has signalled a major vote of confidence in the sector as it pledges to help make the UK a world leader in the Fourth Industrial Revolution by 2030. With Industrial Digital Technology’s playing such a significant role in the transformation of the sector, what should manufacturers be investing in? Real applications of virtual reality Virtual reality (VR), which digitally simulates a product or environment and augmented reality (AR), where the digital product or information is projected on to a real-world background, have traditionally been consumer-focused applications, aimed mostly at gamers. However, with equipment such as the Microsoft HoloLens now being aimed purely at business applications, this is changing. Boulting Environmental Services uses virtual reality to provide its clients with a unique opportunity to immerse themselves in their projects, develop designs more clearly prior to beginning construction work and reduce mistakes. Virtual reality will become prominent during the design of a facility and it could even have applications for building information modelling (BIM). Inputting computer aided design (CAD) files into a VR application can allow the designer, engineer and client move around the product and facility, viewing it under a different light without the need to produce expensive prototypes. VR also has the potential to revolutionise training, particularly when working in hazardous environments. Engineers can explore and mange a range of scenarios without any risk to themselves or equipment. Maintenance is where augmented reality comes into its own. AR can instantly provide important information to maintenance engineers wearing AR headsets, while allowing them to keep their hands free. For example, when combined with remote monitoring and dashboard user interfaces, the status of a drive or motor control centre can be visualised next to the system in question. This type of technology is already being employed by companies with multiple sites, allowing for the comparison of key performance indicators (KPIs) between plants, learning from one-another to improve process efficiency and asset lifespan. Similarly, when combined with a risk based maintenance schedule such as Boulting’s BRISK, each piece of machinery can be colour coded according to the risk it poses to the plant. The rise of artificial intelligence Machine learning is a concept that has been around for decades, where the computer doesn’t rely on rule-based programming, but instead operates using algorithms that can adapt and learn from data. Closely related to this is artificial intelligence (AI), a branch of computer science aiming to build machines capable of intelligent behaviour. One of the major benefits of AI is advanced data analysis, where data is collected, stored and analysed automatically. Dependant on the results of the analysis, processes can be automatically altered, increasing productivity, reducing costs or even preventing production downtime. Combined with trend prediction and predictive maintenance schemes, efficiency and yield rates can be greatly increased across a manufacturing plant. Smarten up your factory Legacy systems were traditionally designed to operate in isolation and are often unable to connect to the wider network and the internet. However, since the advent of Industry 4.0, many plant managers are keen to connect systems and take advantage of the benefits of the Industrial Internet of Things (IIoT), including enhanced data collection, interpretation and use. The answer for many is to retrofit their systems to enable IIoT capabilities. Smart sensors, data analysis systems and connectivity to the IIoT are just some of the benefits promised by the range of retrofitting options on the market. The popularity of retrofitting existing equipment with these technologies using a maintenance budget is only going to increase. As equipment wears and requires replacement, the best choice for many will be a smart sensing motor or motor control centre which can connect to IIoT. The introduction of Industry 4.0 technologies has left no stone or industry untouched over the past few years, particularly given recent price drops. 2018 is shaping up to be the year where new and exciting technologies such as VR and AI make their way onto the plant floor, making it truly a factory of the future. |
|
|
|
Three industries disrupted by automation | 11/01/2018 |
The term, ‘disruptive innovation’ was coined by Harvard Business School professor, Clayton M. Christensen in his 1997 bestseller, The Innovators Dilemma. It refers to a new technology that disrupts an established product, shaking up or creating a new industry, writes Jonathan Wilkins, marketing director at industrial obsolete automation equipment supplier, EU Automation. There are examples of disruptive technology across every industry sector. In consumer technology, the personal computer and the smartphone permanently changed the way we do things. Not only can new technologies create new markets, they can also have a huge impact on industry. Industrially, technologies like additive manufacturing are changing the way products can be manufactured. But it is not just manufacturing and consumer technology that have been affected. Three industries that have been forever changed by automation are: Automotive The automotive industry was quick to adopt automated technology and automotive production lines already feature some of the latest industrial robots. Automation has been a useful technology in automotive manufacturing as it is flexible and able to respond to the dynamic needs of the industry. Of all manufacturing sectors, industrial robots have made some of the biggest waves in automotive manufacturing. As well as automation being used in automotive manufacturing, vehicles are getting smarter. Many already offer partially automated functions, for example predictive emergency braking and parking-related functions. There are a number of technologies in the pipeline to improve the driving experience and fully automated systems are expected to be implemented after 2025. Construction Companies are combining emerging technologies to build complex structures. Robots can now be used to construct beams, lay bricks or drill. In fact, nearly any job in the process can be automated. In future, this means construction could be planned and coordinated remotely, performed on site only by robots. Construction environments are less structured and more unpredictable than most manufacturing facilities, which can make it more difficult to integrate autonomous technologies, particularly if they are mobile. However, vision and inspection systems are proving extremely popular in the industry. Healthcare In the healthcare industry, many of the skills needed in certain roles are impossible to automate, especially those involving human connection. However, there is still a role for robotics in this sector. One area where automated technology is booming is the surgical robot market, which is currently worth approximately $4 billion a year and is expected to grow to $20 billion by 2024. Surgical robots allow doctors to perform complex procedures with improved precision and control than was previously possible. Automation is common across a number of manufacturing sectors, but it has branched out to a range of industries. Companies operating in the construction, automotive and healthcare sectors are certainly being shaken up and there is more innovation to come. |
|
|
|
System Integrators are the vanguard of new technology adoption | 02/05/2017 |
‘When the client has explained what the goals of a project are then it is up to the System Integrator to translate those (usually function, price and performance) goals into a physical structure and a control platform - one that will not only deliver what the client is looking to achieve, but more often than not, also fit neatly into an existing control and management structure’. The above is by definition ‘system’ and ‘integration’. It also underlines why the role of the integrator is often at the crux of the adoption curve for new technology, writes Chris Evans, Marketing and Operations Group Manager at Mitsubishi Electric Europe. In order to deliver, the SI has to be aware of the very latest technology solutions, be that in terms of hardware: PLC, Servo, Sensors, HMI, Robot technology etc. or communication technology and software platforms. The aim is to be cost competitive from a build point of view, effective from a function point of view and provide easy, intuitive, reliable control for the manager and operator. Most SIs have preferred technology vendors that allow them to achieve this; manufacturers they have worked with over the years that provide great products, but also crucially good technical support. If an SI has been to a robot training session such as those regularly provided by Mitsubishi Electric for example and has seen, say, a clean room robot in action, or a collaborative robot example, they will be aware of the opportunities to use this technology. They will usually take the lead role in explaining to the customer how the latest technology will benefit them. Adoption of the technology therefore comes down largely to the trust between the SI and the customer. Sometimes buzzwords and high concepts are useful, they allow the SI to put a simpler label on what could be a complex technology and subsequently drive adoption. Being aware of concepts such as Industry 4.0 can make a client more receptive to a higher level of integration for systems for example. However, the main driver for introducing new technology such as a switch to using mobile devices for plant interaction, using a robot for palletisation, changing over from fieldbus to Ethernet networks, or using a PLC where before processes were not connected and fully synchronised for example, comes from awareness. This is where the role of the manufacturer is vital - good education provision and an active, open channel of communication between the automation component vendor and the SI is essential in order to enable the filter-down of new technology from the vendor to the end user. This may be better hardware integration solutions that save time in programming and actually reduce purchase costs such as adding safety management or robot control functionality as an option on a PLC, or, introducing a mobile app that allows you to control inverter drives and HMIs while on the move which benefits the end user with added convenience and faster response times. The world is becoming increasingly digitised and the role of the SI will continue to be at the forefront of adoption in the industrial sphere. |
|
|
|
Big data and the IoT do not require deep pockets – are you ready? | 20/04/2017 |
Big data is having a big impact further up the tree, so even the smallest traditionally dumb component has be given a modicum of connectivity capabilities, says Heiko Luckhaupt, Industry Sector Marketing Manager, RS Components. The fourth industrial revolution is happening, there really is no escaping it; and this time it is being driven by data. We are seeing it in some of its guises in consumer applications, where connected refrigerators can reorder our milk or our digital assistants and mobile phones can turn on our heating – all thanks to the connectivity enabled by the Internet of Things. It is also making significant headway in industry, from the smallest single-machine applications all the way through to massive industrial complexes, with thousands of I/O nodes. In both cases the primary protagonists are the ones and zeros that make up these digital signals. But it’s not just the data, it’s the data pathways that these ones and zeros exploit and then it’s the software that collects, collates, deciphers and presents them in order to complete and present the bigger picture. Finally, it’s the humans at the end of the chain, who make the decisions based on what their software is telling them. This huge interconnected network is called many things. To the consumer it is the Internet of Things, but to engineers and industry professionals this is a catchy name given to the iterative forward step from the communications systems that have existed for a few decades, but can now piggy back on the World Wide Web – taking and delivering these operational ones and zeros globally, or at the very least further away from the machines. The great news is that you don’t have to be a big company making big machines for big customers to collect and exploit this big data. You don’t even have to leverage the big data yourself; you just have to have the means in place, or the capabilities on your machines, so your customers can. Connectivity to these bigger networks, whether in-house or external, is the key; and the ideal situation would involve some form of Ethernet-based protocol and connection (wireless or hardwired) as the link point. Even if your machines use lower-level control networks, all is not lost. There are plenty of ways to make them IoT enabled; and many of these approaches are certainly not out of reach from a budgeting perspective. The first and most obvious approach is to exploit an Ethernet-capable PLC, which can not only act as an incredibly capable machine controller, but also offers all the necessary Ethernet communications capabilities. RS has a number of devices and bundles/starter kits that will allow users to connect existing legacy systems to wider networks, including controllers from well-known brands such as Siemens and Schneider Electric. Other types of intermediary devices can also be deployed to bring legacy systems into an Ethernet environment, such as the ED-204 Ethernet Media Converter from Brainboxes, which can link PLCs with PC-based data acquisition and analysis solutions. From a purely software-based approach, solutions are also available that give operators a web-based interface system that connects to all manner of shop floor devices. And it’s not just restricted to higher-level controllers or intermediary devices; many traditionally ‘dumb’ line-side products, such as sensors and meters, are being supplied with Ethernet capabilities; and for remote or hard-to-reach applications these often use wireless protocols. Carrying on with the wireless theme, RFID is also being widely exploited for track-and-trace and monitoring, with the IoT connection finally being provided by the readers that scan the RFID devices. Although the benefits of IoT connectivity might not be immediately apparent, especially when you look at the data being generated by a single machine, what you have to do is look at the bigger picture. Imagine that your machine or device in amongst a sea of others, all generating bespoke data sets and being used by a company that lives or dies on the basis of process improvements and throughput gains. In this context, the amount of information being generated and collected may be huge, but it is all useful; and with the correct software and analysis, a single second shaved off a single production cycle from a single machine could propagate into minutes or hours’ worth of savings over the course of a working shift, day or week. In the industrial world, proprietary mid- to high-level networks are reaching the end of their usefulness as more and more global end users move to open, scalable, common-software platforms. And you can guarantee that Ethernet capabilities are in the mix somewhere. With wireless and hard wired off-the-shelf Ethernet technology hitting lower price points, there is now no excuse to not deliver this type of connectivity by any of the means discussed above. Even if your machine or product is a very small fish in a very big pond, its capability to communicate with the wider enterprise is still essential. Maybe not now or tomorrow, but with the way things are heading the near future is going to be even more connected than it is now, so there is no better time to start exploiting the IoT – for your customers’ sakes. Find out more here |
|
|
|
Is AI all it is cracked up to be? | 28/03/2017 |
If planet Earth had been created one year ago, the human species would be just ten minutes old. Putting this into context, the industrial era would have kick-started a mere two seconds ago, writes Stephen Parker, CEO of Parker Software. Thanks to human influence, the pace of technological advancement on Earth is astonishing. However, we are already on the verge of the next change. The potential of artificial intelligence has been discussed by scientists since the 1950s and modern technological advances are finally bringing this technology to the masses. Research suggests that artificial intelligence could be as ‘smart’ as human beings within the next century. Originally, human programmers were required to handcraft knowledge items painstakingly. Today, however, one-off algorithms can teach machines to take on and develop knowledge automatically, in the same way a human infant would. Artificial intelligence has reached a critical tipping point and its power is set to impact every business, in every industry sector. Already, 38 per cent of enterprises are using artificial intelligence in their business operations and this figure is set to grow to 62 per cent by 2018. In fact, according to predictions by Forrester, investments in artificial intelligence technology will increase three-fold in 2017. These figures mean that the market could be worth an estimated $47 billion by 2020. One of the most notable applications of AI from the past few years is the creation of intelligent assistants. Intelligent assistants are interactive systems that can communicate with humans to help them access information or complete tasks. This is usually accomplished with speech recognition technology; think Apple’s Siri, Microsoft’s Cortana or Amazon’s Alexa. Most of the intelligent assistants that we are familiar with today are consumer facing and are somewhat general in the tasks they can complete. However, these applications are now making their way into more advanced customer service settings. While there is certainly a space for these automated assistants in the enterprise realm, there is a debate as to whether this technology could fully replace a contact centre agent. Automation is widely recognised as a valuable tool for organisations to route the customer to the correct agent. However, completely handing over the reins of customer management to a machine could to be a step too far for most businesses. Even the most advanced AI platforms only hold an IQ score equivalent to that of a four-year-old, and naturally, businesses are unlikely to entrust their customer service offering to a child. Automated processes are invaluable for speeding up laborious processes and completing monotonous customer service tasks. But as any customer service expert will tell you, the human touch is what elevates good service to an excellent experience for the customer. Simple tasks will no doubt be increasingly managed and completed using automation and AI-enabled agent support systems, whereas complex issues will still require the careful intervention of a human agent. During a TED Talk on artificial intelligence, philosopher and technologist Nick Bostrom claimed that “machine intelligence is the last invention that humanity will ever need to make.” However, contact centre agents needn’t hang up their headsets just yet. Artificial intelligence won’t be replacing the call centre agent any time soon. The only guarantee is that the role of a call centre agent will continue to evolve — after all, the industrial revolution was only two seconds ago. |
|
|
|
What we can learn from robot ethics | 02/02/2017 |
The British Standards Institute (BSI) recently released a new set of standards for the ethical design of robots and robotic devices, says Graham Mackrell, managing director of robotic gearing specialist Harmonic Drive UK. The standards highlight the growing need for guidelines on robotic safety, contact with human beings, robotic deception, addiction and possible sexism or racism exhibited by self-learning artificial intelligence (AI) systems. When science fiction writer Isaac Asimov wrote about the three laws of robotics in his book Runaround in 1942, little did he know they would one day become a reality for a world filled with robots. From automated manufacturing plants, medical and pharmaceutical applications to military, agricultural and automotive systems, robots are everywhere in our modern world. Asimov's laws outline that a robot must not injure a human being, must obey humans and must protect itself. The new BSI standard BS 8611 builds on Asimov's laws and aims to help designers and manufacturers consider the ethical hazards of robots. The new standard states that, "robots should not be designed solely or primarily to kill or harm humans; humans, not robots, are the responsible agents" and that "it should be possible to find out who is responsible for any robot or its behaviour". Lessons to learn Here are the top three things industry can learn from the new standards for robot ethics: 1. Industry needs to focus on robot safety In large part, the new standards cater for the rise in artificial intelligence (AI). Although this is one of the most exciting developments in robotics, it is not currently where the majority of robots are used. The industrial robots sector is the principal driver in the general robotics market, accounting for a 33 per cent rise in 2015 according to a report by the International Federation of Robotics. The new standards make it clear that a robot needs to be, "safe, secure and fit for purpose". As such, the introduction of the new standards will have far-reaching implications, particularly for industrial users where hazardous robotic environments can pose serious risk of injury to human workers. Many of the deaths caused by industrial robots in recent years may have been avoided if their design considered smart algorithms and programming that was aware of human presence. 2. OEMs need to change the way they design robots for the future To date, the majority of industrial robots have been used in traditional applications including factory automation, automotive, metalworking and electronics assembly. The rise of smaller and lighter robots capable of delivering higher payloads with very high accuracy means that original equipment manufacturers (OEMs) need to rethink their approach. Industries including aerospace, pharmaceutical, food and medical manufacturing are increasingly demanding specific requirements for each application. Whether its aerospace robots that need to use lightweight, high torque gears for the vacuum of space, pharmaceutical and food robots that need to offer ingress protection for easy cleaning or collaborative robots used for small electronics assembly alongside human workers, the traditional approach to robotics simply will not work. For example, Harmonic Drive gears have been used on NASA's Mars Rovers. Because the system was remotely controlled from Earth it was vital that the gearing system provide smooth, zero backlash, repeatable movements with absolute accuracy in a low weight design. Our strainwave gear has teeth that form the outside edge of a flex spline, leaving the central area to be bored into a hollow shaft to allow data cables and other services to pass through, while allowing continuous rotation. By considering the variety of new applications and choosing the right components for each application, design engineers can successfully embrace the new wave of robot developments. 3. Humans will remain responsible for a robot's actions As robots become more sophisticated, our perception of their traits such as deception, addiction, sexism and racism will only grow. Despite this, a responsible human being will always need to be accountable for the robot's actions. Although this raises many legal and ethical questions, we can reduce the risks by improving transparency in the robotics supply chain, by choosing the right component manufacturer at the outset, setting high standards for the design engineering and product testing of new systems and better recycling obsolete systems. By changing our approach to the way we design and use robots, engineers, manufacturers and users can embrace, rather than fear, robot ethics. |
|
|
|
Changing bad gear oil habits | 05/09/2016 |
Benjamin Franklin once said, “it is easier to prevent bad habits than to break them.” This rings true for the industrial sector, where it is easier to form a habit of good predictive maintenance than to recover from machinery breakage or downtime says Mark Burnett, VP of the Lubricants and Fuel Additives Innovation Platform at NCH Europe However, this is easier said than done. Predictive maintenance requires constant vigilance in order to be effective, ensuring that maintenance engineers know when it is the right time to lubricate bearings, apply a rust-preventative coating or treat their water supply. These tasks will vary in frequency, so there can be a steep learning curve to getting it right. Unfortunately, we all know that problems do not wait until you're ready and, especially with gear oil changes, failure to get it right often leads to problems. Changing oil too soon, for example, leads to higher costs as more changes will be needed than necessary. Conversely, forgetting to change the oil at the right time increases the likelihood of machine damage and breakage, which itself leads to elevated operational costs. Despite both extremes leading to increased business costs, only 20 per cent of oil changes happen at the right time. This is not surprising when considering the fact that many variables can determine how regularly oil needs changing. While many engineers may fill up a machine and expect it to require a change after a certain amount of time, it is actually the quality of the oil itself that must be measured. This is understandably difficult without a comprehensive approach to industrial gear oil analysis. In order to reliably measure the quality of the oil and when a change is due, engineers must identify the quantities of external contamination and metal wear, as well as the general condition of the oil. For example, oxidation is a naturally occurring process that affects oil over time. In the presence of oxygen, the oil begins to break down and this reduces the service life of the oil itself. In addition to this, it also produces sludge that makes equipment work harder and drives up operation costs. If left long enough, the acidity of oxidised oil will steadily increase and result in corrosion and pitting. While this is problematic if left for extended periods of time, this acidity allows more accurate assessment of oil condition. By measuring increases in the system’s total acid number (TAN), maintenance engineers and plant managers can identify when the oil acidity is reaching the maximum acceptable level and act accordingly. However, TAN only accounts for one part of overall gearbox system condition and there are many other considerations such as the operational health of the machinery itself. It is crucial that engineers consider all aspects to ensure optimum performance. To this end, NCH Europe has developed the NCH Oil Service Program (NOSP) to help businesses keep their machinery in working order and their oil changes timely. Samples of gear oil are analysed and user-friendly reports are generated so that plant managers can see accurate results at a glance, giving a clear overview of equipment condition and the TAN of the oil. Accurate analysis helps to prevent engineers falling into the bad habit of incorrect oil management. By combining this insight with an effective cleaning solution and a suitable gear oil, further bad oil-change habits and breakages can be kept at bay. |
|
|
|
Seizing the opportunity for UK industry | 10/06/2016 |
According to recent Hennik Research in their Annual Manufacturing Report, released in November, 84% of respondents said they have multiple job vacancies. It leaves me under no illusion that the skills gap is upon us, writes Dave Nicholl, Country Director, United Kingdom and Ireland at Rockwell Automation But it’s easy to talk down UK industry. What that also says to me, especially in the light of some other key statistics from the same report, is that the UK has a huge opportunity. The work is there and 81% of companies listed “new product development” as a key business focus, while 85% of UK Manufacturers are either “very” or “quite” optimistic about the British economy over the next one to three years. So industry is looking forward – and well it should. An example of this was recently covered in an article which appeared in the Financial Times online. One of the strongest sectors for UK industry is Food manufacture. And it’s a reliable one, too. Regardless of “onshoring” trends and opportunities, it is hard to envision a future where staple food products are imported wholesale from cheaper manufacturing economies – as Norman Soutar, chief executive of William Jackson Food, put it, “food manufacturing is more protected, you cannot ship it here from China. It has to be local”. As an employer of 2000 people who is implementing the national living wage by April of this year, the company is set to add around £1m to its overheads. Mr Souter points out “We just have to become more efficient”. This isolated example is also indicative of UK industry in general. It simply must become more efficient to remain sustainable and to grow. Again, it would be easy to talk industry down, but again, this is also about opportunity. It’s entirely possible as well as necessary for UK industry to meet the challenge and it’s not something that should be feared, but rather an opportunity to be seized. Pleasingly, The Annual Manufacturing Report gives a few clues about a general acceptance in industry of how it can happen, too. Almost half of respondents claim to be in the process of implementing a major automation project, with a further fifth saying that they had done so in the past 12 months. That’s two-thirds of UK manufacturers who have shown a commitment to automation recently. Moreover, 60% said that working conditions and job satisfaction had improved as a result of recent automation projects; 44% that jobs had been safeguarded; and 18% that new jobs had been created as a direct result. So if the work is there, the sector has a positive outlook and we know how we can become more efficient and competitive, could the UK actually be a leading player in the so-called fourth industrial revolution? I believe it can – for a couple of very good reasons, but not without a concerted and coordinated effort. The concerted effort needs to come in the form of updating existing industrial infrastructure. At a private level, more manufacturers, particularly in the F&B sector which is widely known to be under-automated, need to invest in their medium and longer term future and start to feel the benefits of the Industrial Internet of Things sooner. At a public level, we need sustained investment and incentives for companies to continue to innovate, continue to invest in their future and continue to make the UK a better place for industry. Government is an important part of the process – it can influence policy, regulations, export opportunities, infrastructure projects and, of course, STEM initiatives. That’s to say nothing of minimising the risk and uncertainty surrounding a possible “Brexit”. It is also an important consumer and should look to support UK industry directly where possible, such as with the recently announced trials of British designed and built driverless cars. For UK industrial enterprise to seize the opportunity, simply saying “invest in automation” is rather simplistic. And it’s just not an option for most businesses to stop production and build flashy new plant. However, taking a strategic and structured approach to rapid evolution can set any enterprise on the road to becoming much more efficient and agile – the two key constituents of a successful and sustainable industrial sector for the next ten years and into the future. The information revolution, the industrial application of which is at the heart of the nascent industrial revolution, relies on a highly connected and automated approach to business. At Rockwell Automation, we call this The Connected Enterprise. The concept is remarkably simple but the effect is very powerful. The Connected Enterprise is about bringing people, processes and technology together through the convergence of information technology and operational technology into a single unified industrial business architecture. And because it’s a continuous process of strategic, systematic evolution, the benefits begin with first phases of implementation and can continue long into the future. The lifeblood of the Industrial Internet of Things revolution is information. It is about the data that is increasingly available from every internet connected element of any industrial process - from a confectionery line to an oil pipeline. But in order to turn that data into usable intelligence it must be collected, collated and processed. That’s a question of making enterprises smarter and more connected, and it can start now. It must start now, in fact, if we’re to seize the opportunity. So let’s not talk down UK industry, let’s get connected and bring the future closer, quicker. |
|
|