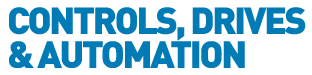
![]() |
Charlotte Stonestreet
Managing Editor |
1/8 (1 to 10 of 72)
Powering industrial strategy | 24/06/2025 |
---|---|
THIS WEEK has seen the government publish details of its much anticipated modern Industrial Strategy. Described as a 10-year plan to promote business investment and growth and make it quicker, easier and cheaper to do business in the UK, it focuses on eight sectors where the UK is already strong and there’s potential for faster growth: advanced manufacturing; clean energy industries; creative industries; defence, digital and technologies; financial services; life sciences; and professional and business services. One of the most eye-catching policies in the strategy is the reduction of energy costs for major electricity users. According to the Government, More than 7000 businesses in manufacturing sectors such as automotive, aerospace and chemicals are set to see their electricity bills slashed by up to 25% – but not until 2027. These firms, which support over 300,000 skilled jobs, will be exempt from paying levies such as the renewables obligation, feed-in tariffs and the capacity market. The intention is to help level the playing field and make them more internationally competitive. There will also be increased support for the most energy-intensive businesses – for example steel, chemicals, and glass – by covering more of the electricity network charges they normally have to pay through the British Industry Supercharger. These businesses currently get a 60% discount on those charges, but from 2026, that will increase to 90%. While these measures are undoubtedly welcome, they do seem to be somewhat in conflict with any sustainability ambitions. While I appreciate that making electricity cheaper is vital for growth and competition, I can’t help thinking that it will also have a detrimental impact on the drive for efficiency. Then there’s the fact that these price cutting measures are not due to come in for another couple of years, plus the fragile geopolitical situation that continues to push global energy prices higher. So however positive the measures are, they do not provide an instant cure-all. Commenting, on the strategy and its promised cuts in electricty costs, Barbara Frei, executive VP, industrial automation at Schneider Electric, said: "As global energy prices remain volatile, industrial firms face mounting pressure to protect margins. But the solution isn’t simply to wait for prices to fall. The real opportunity lies in redefining cost competitiveness through smarter resource management and automation. "To stay globally competitive, the UK’s industrial companies must go beyond traditional cost-cutting. They need to embrace open software-defined automation and industrial AI. Not as future investments, but as immediate strategic imperatives. These technologies are already delivering measurable gains in productivity, efficiency and emissions reduction across global markets." And that is a message that is well worth listening to. |
|
|
|
Increase automation, increase productivity | 30/04/2025 |
FOR ANYONE who stays informed about the UK's industrial sector, it will come as little surprise that there is still a huge issue when it comes to productivity. While this is far from ideal, the low starting point does in theory mean that vast improvements could be made possible by implementing relatively easy measures. It's no secret that one way to achieve this is through increased levels of automation – something that was highlighted by Mike Wilson, chief automation officer at the MTC, at a recent industry event. As Wilson pointed out, if the UK were to increase its adoption of automation to that of some of its major competitors, productivity would be improved by 20%; and is this something, asserted Wilson, that is increasingly being recognised within government. In fact, it is estimated in some quarters that if the productivity of the lowest achieving SMEs could be improved to levels similar to the top 25, it could be worth around £270 billion to the UK economy. In order to help achieve these goals, the MTC and The University of Birmingham founded the West Midlands RAS Cluster, a collaborative group comprising industry, suppliers, academic institutions, and local authorities to accelerate the adoption of robotics and autonomous systems (RAS). The organisation has carried out extensive research, part of which identified barriers to automation. Overall, the biggest factor putting businesses off automation tended to be the high initial investment costs involved. Other challenges highlighted included integrating new equipment with legacy systems and a lack of skilled personnel, along with a myriad of factors such as concerns about reliability, return on investment, impact on workforce and compliance issues. In addition to raising awareness of the benefits of RAS technology and addressing barriers to its adoption, the Cluster aims to ensure that the supply side is developed to deliver what UK industry needs, something which, said Wilson, could hopefully be developed to see such UK technologies exported overseas. If you are interested in finding out more about any of these issues, the MTC is hosting Robotics and Automation 2025: Powering Your Future in June, which will feature insights from the West Midlands RAS Cluster on best practices, innovation opportunities and collaborations. The event will include a keynote address from Dr Bernd Liepert, president of euRobotics AISBL – the European Robotics Association, about the opportunities for UK to forge a bigger robotics market with Europe. The Rt Hon Greg Clark - Chair of the Warwick Manufacturing Group and a member of the Industrial Strategy Advisory Council, which contributes to the development and long-term delivery of HM Government’s industrial strategy, will also be delivering a talk to attendees. To find out more visit : www.the-mtc.org/robotics-and-automation-2025 |
|
|
|
UK digitalisation spend looks to lag | 25/02/2025 |
DIGITALISATION IS a subject that I keep returning to in Controls, Drives & Automation, not just in terms of covering the latest technologies, but also to cover the myriad of benefits it offers and how harnessing these gains is vital to UK industry if it is to be competitive. Against this backdrop, I was somewhat perturbed to see that a recent report from Siemens has found that in the UK, a lack of planned investment in digitalisation is potentially putting infrastructure modernisation and decarbonisation at risk. Titled Digital Transformation, Sustainable Returns: The New Pathway of Infrastructure, the study looked at how 650 senior executives from 13 countries believe digitalisation can be harnessed to accelerate decarbonisation and transform the world’s infrastructure. The survey revealed that just 38% of UK businesses plan to increase investment in digital technologies over the next year, significantly trailing the global average of 58%. This puts the UK behind countries including Canada (72%), China (70%), Italy (64%), and Germany (54%), in terms of expected digitalisation investment. Siemens warns that limited adoption of digital technologies in infrastructure could further widen the UK’s productivity gap. Despite slower investment rates, UK businesses recognise the benefits of digitalisation. Respondents highlighted productivity (68%), workforce health and safety (66%), and decarbonisation (64%) as key advantages for their organisations. Regarding decarbonisation, UK firms identified energy storage technologies (44%), electric vehicle charging networks (34%), and remote sensing and monitoring (34%) as the most impactful innovations for the next three years. However, depite seemingly understanding concerns over implementation costs (46%) and integration complexity (38%) remain significant barriers to adopting digital business platforms. The Climate Change Committee has stressed the need for faster progress in decarbonising infrastructure and industry to stay on track for the UK’s 2050 Net Zero targets. With the Government’s industrial strategy forthcoming, Siemens is urging stronger initiatives to drive digital investment and enhance the UK’s global competitiveness. If the UK fails to invest in digitalisation, its industries risk falling behind global competitors, widening the productivity gap, and struggling with higher operational costs. Without modern technologies, businesses will become less efficient, making the UK a less attractive place for investment; thus potetnially could slowing economic growth, limiting job creation, and hindering innovation. Outdated infrastructure and legacy systems will also lead to inefficiencies and rising costs, making it harder for UK firms to compete internationally. Addtionally, without digital advancements, the UK may struggle to meet its 2050 Net Zero targets, missing key sustainability goals and facing regulatory challenges. As is so often the case, it's not a question of whether businesses can afford to invest, it's whether they can afford not to. Charlotte Stonestreet Editor |
|
|
|
Strategy makes a wecome return | 16/10/2024 |
WHATEVER YOUR thoughts about the new labour government, the fact that the UK is to once again have an Industrial Strategy should come as good news to those across the sector. In contrast to most other developed economies, in recent years the UK has failed to acknowledge the role that such a strategy has in ensuring long-term economic stability, growth, and global competitiveness. Now, outlining its vision for a modern Industrial Strategy, the Government has published a comprehensive green paper titled "Invest 2035:The UK’s Modern Industrial Strategy". The intention is to foster long-term economic growth by targeting eight key sectors: advanced manufacturing, clean energy, creative industries, defence, digital technologies, financial services, life sciences, and professional and business services. The strategy aims to tackle barriers to growth and create more supportive environments for these sectors, working closely with businesses, regional governments, and industry experts to develop sector-specific plans. These plans are expected to be finalised in the spring of 2024 alongside a multi-year spending review. Unsurprisingly given the "Invest 2035" moniker, one of the key focuses of the new strategy is to attract significant private sector investment. Recently, the government announced it had secured £63 billion of private funding for a range of projects including airport expansions, data centres, and green infrastructure. And maintaining this level of investment is crucial. An essential aspect of the strategy is to make the UK more competitive in emerging industries such as clean energy and digital technology. For instance, supporting the clean energy sector aligns with the country's broader push towards achieving net-zero carbon emissions, while advancements in digital and technology are pivotal for modernising infrastructure and ensuring global competitiveness. Overseeing the strategy will be the Industrial Strategy Advisory Council, chaired by Clare Barclay, CEO of Microsoft UK, which will inform the development of the Industrial Strategy through its expertise and latest evidence, working with business, trade unions, devolved governments, local leaders, academia and stakeholders. Reactions have been widely positive: Make UK CEO Stephen Phipson said: "We live in a world which is massively different to a decade ago and simply leaving the economy and, industrial strategy, to the free market is an ideology which is long past its sell by date. This is a welcome first step in addressing the achilles heel of the economy which has left the UK an outlier among advanced countries. It sets out a clarity of vision for how the resources of Government and, in particular, each department can be convened towards a single objective of long term growth across all regions." President of the Institution of Mechanical Engineers, Dr Clive Hickman OBE, said: “The Government’s plan for a new Industrial Strategy is a positive step towards fostering innovation and growth across the UK. However, to truly realise the strategy's potential, it is essential to invest in the development of engineers who will drive the scale-up and deployment of these initiatives nationwide. Aligning skills programs with industry needs will be critical to ensuring we have the right talent to meet future demands. "The Green Paper rightly states that a successful industrial strategy can only be delivered by working in partnership with all sectors of our economy. Taking a long-term view, with a stable regulatory environment and funding mechanisms, is also essential." Charlotte Stonestreet Editor |
|
|
|
Looking beyond a temp solution | 02/09/2024 |
ANYONE FAMILIAR with the UK industrial sector already knows that the nation lags behind its competitors when it comes to automation. According to the International Federation of Robotics figures released in September 2023, in 2022 the UK had 2534 industrial robots, and while this marked a 3% increase, it was still less than a tenth of those in Germany. At the time of writing 2023 figures have not been published, and while I live in hope of great or even moderate improvement, something tells me that once again the UK figures will be lacklustre. While I am of course aware of the facts, writing for CDA and lreaning about all the exciting innovation that is out there, i do find it all too easy to forget about the somewhat sorry reality of industrial automation in the UK. Walking around any of the numerous trade shows that serve the sector, I get caught up in the knowledge and enthusiasm of the exhibitors, not to mention the benefits that the equipment being showcased can bring. However, the reality that many businesses continue to rely on human labour when some level of automation could be of huge benefit was recently brought home to me in real life, rather than through the lens of industrial sector publishing. Home from university for the summer, my son recently picked up some temp work at a local business, which specialises in packaging and packing fast moving consumer goods. It’s an apparently successful company, working with a plethora of household names, the type of business that surely must be investing in automation to increase productivity? Suffice to say, I was somewhat taken aback when I discovered that the job had entailed manually unpacking Freddo frogs (other chocolate bars are avaialable) from a box, counting out five, and then putting them into a smaller boxes, which were then manually counted into a larger box. On another day they were tasked with unboxing packaging sleeves, placing them on a conveyor that fed them through an automated labeller, and then counting the sleeves back into a box at the other end of the conveyor. I simply cannot figure out why this type of task is still being carried out manually. Are funds for investment not available? Are the people in charge not aware of the automated solutions that could be used? Or are they just so used to the current business model that changing it seems like a huge task? I was half joking when I told my son that he should take copies of CDA into work and leave them lying around in the hope that the business could see what it was missing. He was so horrified by this suggestion that he found a job elsewhere. To be fair, he also found the work so monotonous and boring that even the pretty good wage - well above most temporary jobs - wasn't enough to keep him there either, which makes me think that in this case, automation would defintely be a good option. |
|
|
|
Industry 5.0 - coming to an industrial facility near you soon | 14/06/2024 |
AT THE recent Smart Manufacturing and Engineering Week event, one of the more popular buzzwords I heard being bandied around was Industry 5.0. While it might seem only a short time since Industry 4.0 was all the rage, the concept was first coined over ten years ago so it stands to reason that things are moving on. So what is Industry 5.0 and what does it mean for the industrial sector? Well, much like its predecessor Industry 4.0, Industry 5.0 will mean different things to different people and enterprises. At the most basic level Industry 5.0 can be defined as representing the next evolutionary step in the industrial sector, building upon the foundations of Industry 4.0. However, while Industry 4.0 focuses on automation, digitisation, and the integration of cyber-physical systems, Industry 5.0 can be seen as having an altogether more human-centric ethos, shifting the focus towards a harmonious collaboration between humans and machines, emphasising the personalisation of products and protecting the element of human creativity in the manufacturing process. Industry 5.0 has been described as seeking to enhance human skills by leveraging advanced technologies, allowing workers to focus on creative and complex tasks while machines handle repetitive and mundane activities. This is intended to improve job satisfaction, reduce errors, and foster innovation. Another hallmark of Industry 5.0 is the ability to produce highly customised and personalised products using advanced manufacturing technologies such as 3D printing, AI, and machine learning. Fitting nicely into the overall movement towards sustainability, Industry 5.0 prioritises environmentally friendly practices, aiming to reduce waste and energy consumption through more efficient production processes and the use of sustainable materials. Industry 5.0 leverages cutting-edge technologies to create intelligent and adaptive manufacturing systems. These technologies enable real-time monitoring, predictive maintenance, and autonomous decision-making, leading to increased efficiency and reduced downtime. Quoted as a defining feature of Industry 5.0 is collaboration between humans and robots. At a basic level, this can be achieved by choosing from the plethora of cobots (collaborative-robots) designed to work alongside human operators, enhancing their capabilities and assisting with tasks that require precision, strength, or endurance. This collaboration improves productivity and can help create a safer and more ergonomic working environment. Positive as all the defining features of Industry 5.0 are, I can't help looking at the concept and wondering whether it is offering anything really different to Industry 4.0. I'm sure that regular readers of CDA will be already more than familiar with batch-size one, cobots, AI, sustainability – indeed any and all of the touted elements of Industry 5.0. Automation in general has long been viewed as a tool to take on the 'three Ds' - dirty, dull and dangerous tasks - freeing-up people to do more meaningful and fulfilling roles. And while it is undoubtedly more nuanced than I have indicated here, to me Industry 5.0 seems to be the natural evolution of this – albeit with a more natty label! Charlotte Stonestreet Editor |
|
|
|
Invest to be the best! | 02/05/2024 |
ANYONE FAMILIAR with the UK industrial sector will no doubt be aware of the relatively low levels of investment in the UK when compared to, for example, our European counterparts. Indeed, the finger is often pointed at under-investment when it comes to figuring out the reasons behind the UK’s perennial issue of low productivity. Add to this the growing need for sustainability – which simply cannot be achieved without investment in the latest technologies – and the need for investment has never been greater. So why is the UK so reluctant to invest? Of course, there is a myriad of reasons – from short term-ism to a traditional attitude of if-it-aint-broke-don’t-fix it – but what many of them boil down to is a lack of knowledge, not just about the technology and potential benefits, but also about the available finance opportunities. This has been highlighted in a recent report from Make UK, NatWest and Lombard, which found that investment levels amongst the UK’s manufacturers could be boosted by up to £10 billion in the next year if they were to take advantage of the range of public and private finance options available to them. Such a boost would, asserts Make UK, raise the investment potential of the sector overall by up to a fifth and help address the UK’s long-term productivity weakness. Furthermore, the report shows that more than a quarter of companies (26%) would increase their investment by up to a fifth if access to finance was improved, while more than one in ten (12%) would increase their investment by up to half. However, the report also showed that more than half of companies (54%) are unaware of the range of public sources of finance and government schemes tailored towards manufacturers. Boosting investment is critical to the sectors’ efforts to improve productivity and innovation performance given the top priorities for investment are capital equipment (62%) while access to finance will be required for investment in automation and energy efficiency by a third of companies (32% and 31% respectively). Furthermore, the report also shows almost three quarters of companies (70%) said that investment would not take place without access to finance, while just under a third (30%) said their investment would have taken place without any access to finance. The report shows that, as well as improved awareness of private financial options available to manufacturers, there needs to be far greater awareness of the public sources of finance and Government schemes. More than two thirds of companies (67%) have not heard of the Horizon Europe programme, while a lack of awareness of domestic schemes such as the Government’s flagship management Help to Grow scheme (61%) and British Business Bank (58%) is also alarmingly high. By contrast, just 2% of companies have successfully accessed the Horizon programme, 14% accessed the Help to Grow scheme and 12% accessed the British Business Bank. According to Make UK, this means Government must be cautious before scrapping schemes that companies are unaware of. To improve manufacturers’ awareness of the range of public and private finance available Make UK is calling for a centralised database which would signpost both public and private provision. Could this be the magic bullet that will get UK industry investing? Probably not, but there's no doubt that it would make a positive contribution. Charlotte Stonestreet Editor |
|
|
|
New battlegrounds for machine builders | 01/05/2024 |
Charlotte Stonestreet reports on the latest Controls, Drives & Automation webinar, sponsored by Schneider Electric, which took the form of a roundtable covering sustainability and servitisation FOLLOWING INTRODUCTIONS and some general scene-setting, the webinar kicked into action with Mike Wilson who pointed out that here in the UK we are not really great users of robots and automation, and generally lag behind most competitors throughout the world. To put this into context, Wilson pointed to robot destiny figures, which give an indication of the number of robots in use per 10,000 workers and enable comparisons with other countries. At present the UK lies 25th in the world, despite being the eighth largest manufacturer. “So if we were using robots at the same kind of level as other countries we should be somewhere more around the eighth to tenth sort of range,” said Wilson. “We (the UK) historically have not been very good at cap-ex investment throughout our manufacturing centre, but things are changing and it’s being driven by issues around sustainability in particular.” Effective and efficient Wilson asserted that using the latest automation technology is beneficial in terms of ensuring operations are as effective and efficient as they can be. Automation results in less waste, produces more consistent quality and helps achieve optimal energy use, as well as making sure that a piece of machinery is used as efficiently as possible “A typical machine tool might be loaded and unloaded manually, and you will typically get 60-70% utilisation out of that tool, whereas if you can automate the load and unload you can increase that to about 90%,” said Wilson. “So you get a significant improvement in the efficiency of all the resources that you are putting into that process. Wilson pointed to another global issue that the UK is well positioned to take advantage of, that of the trend for reshoring, which can also contribute to sustainability. It is important to consider not just the carbon emissions from the UK, but also the overseas emissions produced during the manufacture and transport of goods which are imported to the UK. Growing demand for mass customisation is also driving the desire to produce closer to the end consumer. “That gives us an opportunity to bring things back to the UK,” said Wilson. “And to do that we need to be competitive, we need to do it without significantly increasing the amount of labour that we are using, so, therefore, we need to consider automation.” As Wilson pointed out, automation and robotics give the potential to expand the UK’s manufacturing capability and ensure that it’s as sustainable as possible. Different business model Touching on servitisation, Wilson said: “Really, it’s just a different business model in terms of how people sell the equipment, and rather than purchasing the equipment, you are buying the ability to produce a certain number of parts an hour, or whatever it might be. Fundamentally, that makes it easier to invest in that equipment because it’s not necessarily coming out of cap-ex.” Given that the UK has been historically poor at cap-ex, this gives the opportunity to take advantage of the latest technologies going forward. In the context of sustainability, Wilson also talked about the recycling and refreshment of automation equipment, pointing out that in the past businesses might have simply discarded a piece of equipment once it had reached the end of its life. However, there is a second hand market for industrial robots and some of the bigger companies are starting to take robots back for refurbishment and resale back into the market. “Those opportunities make it potentially less expensive for some of the smaller businesses to get into this technology.” said Wilson “So we start to develop a circular process that;’s beneficial for the whole of UK industry. “We are just at the start of this journey, but there is a big opportunity for the UK to take leadership in this kind of approach, and then that will give us the chance to catch up, or even leapfrog our main competitors.” Scoping out the complexities The conversation then turned to the reasons behind the need for OEMs, and the wider market, to compete specifically on sustainability - a subject addressed by Mike Teller, global strategy and sustainability leader, OEM industry business, at Schneider. “We do things for two reasons, I guess, at a basic level, either because we see a reason to do it and want to do it or because we have to,” said Teller. He pointed to regulatory requirements from both the UK and the EU (to where the UK exports) which mean companies have to comply in terms of sustainability, as well as the voluntary side where businesses see the growing awareness amongst both their customers and their competition. “There are areas that we hear about from the greenhouse gas protocol, where we talk about scope 1, scope 2 and scope 3. A scope 1 emission is something we generate ourselves; so I have a gas boiler where I am which is heating the radiators which keep me warm so that’s my scope 1 emission. Scope 2 is an emission made on my behalf, so I’m running my computer at the moment on electricity which is made by the power station down the road, and that is an emission made on my behalf so I can purchase their electricity.” says Teller. “Scope 1 and scope 2 are more or less within my control; scope 3 is far more complex. It’s everything upstream - so everything that we buy into Schneider Electric to put into a product – and everything downstream that goes to our customer. And scope 3 is by far the largest area. This is where – selling products and solutions to our machine builder partners who then sell them on to end users – we can have the biggest effect. So this is also where the biggest opportunity is. Teller highlighted that 80% of a product's sustainability is determined at the design stage. As he pointed out, it is not possible to build a machine and then expect to fine tune it three years later; this is where Schneider uses digital twin technology to design in partnership with the machine builder. The digital twin Miklosh Bakos OEM offer manager UK&I at Schneider also talked about the importance of designing in sustainability right from the onset. He referenced a 2022 study from Gartner which analysed the whole machine building process; this determined that roughly 60% of the commission time is wasted with fault fixing. “That’s a big number, 60%,” said Bakos. “To address this and to make it faster for the OEM to get through the whole process, the digital twin can be one pillar of success, speeding up commissions and making it more efficient.” Bakos explained how the digital twin brings value beyond just the design, easing collaboration amongst the various parties working on a project, providing a detailed sales tool to showcase the machine itself, and enabling remote maintenance. Responding, Chris Haines, marketing director, industry at Schneider talked about the huge potential for enhancing sustainability through predictive maintenance. This can, he said save end users’ time, energy, and resource by being more intelligent about what is maintained and how and it is maintained, based on the condition of the condition of the equipment rather than relying on manufacturer recommended maintenance intervals. “If you are monitoring the actual condition of your assets, you can tell where and when they need maintaining and you can extent the maintenance intervals if it’s not being worked particularly hard, or if it’s in a clean environment, and you can save an awful lot of time, energy, resource, materials – and as a result carbon – by doing that,“ said Haines. He also pointed out that if a piece of machinery is being worked particularly hard or is in a harsh environment, monitoring the condition can identify that maintenance is needed before the recommenced interval comes up, potentially averting catastrophic failure. “It’s another way of saving time, money and energy,” he said. When it comes to repair and remanufacture, Haines feels that this is another aspect that can contribute to sustainability as a whole. “There’s no silver bullet for sustainability, there’s no one big ticket item that you can go for, it’s really about aggregating marginal gains,“ said Haines. “It’s lot of little things that add up on your journey to net zero.” Gain further insight This article gives just a taster of what was covered in the webinar, so if you want to find out more details visit the website below and view the event on-demand at a time to suit you. |
|
|
|
Does this give much needed certainty? | 05/03/2024 |
AS I write this on the eve of what is in all probability the final budget before the next election, Chancellor Jeremy Hunt has as you will no doubt be aware announced a £360m boost to UK manufacturing and R&D. Brandished as part of the government’s plan to grow the economy, boost health resilience and support jobs across the UK, the funding will go to companies and projects making cutting edge technology in sectors key to economic growth and forms part of wider government support which aims to ensure the UK is the best place to start, grow and invest in manufacturing. This latest announcement follows publication of the government’s 47-page advanced manufacturing plan last November, setting out its long-term proposals for increasing manufacturing output. It is backed by £4.5bn in funding over the next five years, which was announced in the autumn statement. Of the funding, £7.5m has been earmarked to support two pharmaceutical companies: Northern Ireland-based Almac, which produces drugs to treat diseases such as cancer, heart disease and depression; and Ortho Clinical diagnostics in Pencoed, Wales, which is expanding its facilities producing testing products used to identify a variety of diseases and conditions. The Chancellor also indicated that firms will soon be able to apply for a share of the £520 million funding for life sciences manufacturing announced at Autumn Statement, with competitions for large scale investments opening for expressions of interest this summer and medium and smaller sized companies in the autumn. On top of this, the government has announced almost £73m in combined government and industry investment for cutting-edge automotive R&D projects to support the development of electric vehicle technology, delivering, says the government, highly skilled jobs and cementing the UK’s position as a global hub for EV manufacturing – good news even given the fact that the ban on the sale of new IC engined cars has recently been delayed by five years. It is hoped the funding will unlock investment from the private sector and give certainty to investors, something which has – anecdotally and seemingly otherwise – been lacking in recent years. And while any investment in UK manufacturing is to be welcomed, let’s not pretend that the latest announcement represents some kind of panacea for the sector and more action is needed. Indeed, as Chris White, director of the Industrial Policy Research Centre at the Manufacturing Technology Centre, has pointed out: “R&D underpins the innovation and productivity needed to boost economic growth and reduce our reliance on overseas manufacturing. The UK’s investment in this area has lagged behind other countries for too long. By setting out more substantive details, The Chancellor has sent an important message of confidence which will help secure more private funding for cutting-edge projects. Charlotte Stonestreet Editor |
|
|
|
Driving sustainability through digitalisation | 23/02/2024 |
Charlotte Stonestreet reports on the last Controls, Drives & Automation webinar, where Nikesh Mistry and Francois Disch explored the role digitalisation can play in helping businesses meet growing demand for environmentally responsible practices while simultaneously improving their bottom line SETTING THE scene, Nikesh Mistry, sector head for industrial automation at GAMBICA referred to the UK Government’s legally binding commitment to reduce the nation’s greenhouse gas emissions by 68% compared to 1990 levels by 2030, asserting that unless stronger action is taken this target will be missed. “If stronger action isn’t taken by industry, manufacturers and end-users alike it doesn’t look as though we will actually reach our goals,” he said Addressing this, GAMBICA has created Environmental Impact Champions, whereby the association has sent out a survey to all its members, which allows them to benchmark their performance against industry standards for CO2 emissions, as well as identify their main emission sources and come up with a reduction plan. GAMICA then uses the data collected to monitor trends and produce reports to be shared with members so that they can then demonstrate their approach to customers and tenders. Each company can compare their data with industry standards, with the intention of then achieving year-on-year improvements – individual company data is not shared with other businesses. Different mindsets One of the benefits of being a sizeable organisation is that GAMBICA is able to have a range of groups addressing similar things, but involving different individuals and mindsets. “We’ve got the university group who might influence sustainability, we’ve got the wider GAMBICA members in all sectors and we’ve got our GAMBICA Young Council,” said Mistry. “This is 16 professional in the first ten years of their careers spread across all the GAMBICA industries.” The group is currently concentrating on STEM, sustainability and professional development, which is particularly pertinent. “The younger generation sees sustainability from a different point of view,” asserted Mistry. “Sustainability is in the media, it’s at the forefront of what’s going on, and it’s personal to them.” As part of their remit, members of the GAMBICA Young Council are creating a ‘jargon buster’, helping to decipher the buzzwords that get used around sustainability, as well as coming up with a guide for sustainability best practice. “They want to create initiatives to help businesses, not just ticking boxes,” said Mistry. “They are working with companies like My Green Lab and other sustainability focussed businesses to help them go into our members and help on the sustainability side of things.” So, once the groundwork has been laid in terms of completing the surveys and discovering where carbon emissions are, what are the next steps that a business can take to reduce their carbon footprint and begin their journey to becoming a smart sustainable enterprise? Four focus areas Mistry outlined four areas of focus to help businesses on their sustainability journey, the first of which was optimisation of resource use and economic decoupling whereby the environmentally negative impact of resource consumption is minimised and the processes are optimised. The second focus highlighted was that of energy usage, an area which, said Mistry can be overlooked. As he pointed out, while it is vital not to ignore energy saving technology, simply improving energy waste can bring about huge benefits in terms of a reduced carbon footprint. Examples cited by Mistry include something as basic as turning off machines when not in use and not running them to full capacity unnecessarily. Another factor that Mistry looked at was waste treatment and recycling. GAMICA works with a number of companies such as B2B Compliance, a not-for-profit organisation set up to help businesses with Waste Electrical and Electronic Equipment recycling (WEEE). The fourth area of focus, that of technology, is particularly important. "I cannot stress how important it is to use technological advances to maximise your efficiency," said Mistry. It's about taking the digital technologies that we have – which in many instances are not new technologies, but have been available for many years – and getting started on the journey to use them. "The pandemic was a catalyst of technology. Companies need to remotely access their data, their machines, they need to do machine maintenance from wherever they may have been because they couldn't go on site," said Mistry. As he pointed out, technology proved essential in maintaining productivity throughout the external shocks of the pandemic; and this is also pertinent to the current situation with global unrest and the continuing ripples of Brexit to contend with. "Digitalisation isn't just about manufacturing, it's about logistics, the warehouse, transport, labour, scheduling, quality systems – these are all areas that technology can have an influence in," said Mistry. And for those unsure of what technology might be right for them, there are many companies that can help. It is also good to be part of an association like GAMBICA where competitors can come together to discuss the wider challenges. Existing technologies Next up was Francois Disch, digital transformation delivery lead at Schneider Electric UK&I, who put forward the assertion that 70% of CO2 emissions currently produced can be eliminated using existing technologies. "There's a lot to do currently, and there's going to be a lot in the future too, but really we can say that we've got everything in our hands to break this curve and get down to the 1.5 degrees that we need to," he said. Disch looked at electricity consumption and how it has more or less doubled each decade in the recent past, something that he attributes partly to the drive towards electrification. This, said Disch, doesn't necessarily mean 'green', but it does mean 'clean' - in other words, the electricity may be produced from a number of sources, which may or may not be sustainable, but the point at which the electricity is consumed is clean. "The goal is to use electrification, use green energy, and then go back to the source of the production of electricity and get it cleaner in parallel," said Disch. Being at the forefront of energy management and industrial automation, and understanding how they are interwoven, Schneider Electric is ideally placed to address the challenges around electrification and the transition to sustainability. Indeed, Schneider is consistently recognised as one of the most sustainable companies in the world and since 2014 is the largest independent broker of renewable Power Purchase Agreements (PPA). "We are managing our own CO2 emissions and we are connecting our expertise with our clients," said Disch. "We have experts in digital energy and sustainability pathways across the world." Three logical steps Disch outlined three logical steps to optimising a company's carbon footprint, the first of which is to strategise. This step includes measuring current carbon output, creating a decarbonisation roadmap, providing structure and governance, and communicating the commitments both internally and externally. "At the is point we haven't changed the output, the carbon footprint, but we have a way forward," said Disch. The next step is to digitise, which involves monitoring resources use and emissions to provide live data which is then used to identify savings opportunities. Progress should be benchmarked and reported. The third step, decarbonisation, is about electrifying operations, reducing energy use, replacing the energy source, and engaging with the value chain with the aim of impacting the overall carbon footprint. These steps are eased by applying a degree of common sense and Disch outlined some basic actions that businesses can take including replacing inefficient machinery, using green energy, and even simply raising awareness. Grow your knowledge This article gives just a taster of what was covered in the webinar, so if you want to find out more details visit the website below and view the event on-demand at a time to suit you. You can also sign up for the next webinar on 14 March, brought to you in association with Schneider Electric, titled 'Sustainability & Servitisation: The New Battlegrounds for Machine Builders', which promises to drill down into how regulations and emissions calculations will impact buying decisions, how to use sustainability credentials to win new business, and how to leverage 100% tax breaks for capital expenditure. www.controlsdrivesautomation.com/webinars
Key Points
|
|
|

Charlotte Stonestreet is an experienced b2b editor and has worked across a range of industrial titles including Handling & Storage Solutions, Factory Equipment and Materials Handling News.
She has also contributed to the 'Energy Procurement essential guide to excellence'.
Having gained a degree in English with Media Studies, Charlotte started out her publishing career on a voluntary basis, producing a newsletter for Mencap.