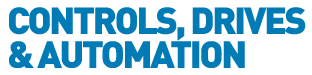
![]() |
Charlotte Stonestreet
Managing Editor |
Home> | IIot & Smart Technology | >Big Data | >New battlegrounds for machine builders |
Home> | AUTOMATION | >Condition Monitoring | >New battlegrounds for machine builders |
Home> | IIot & Smart Technology | >Connectivity | >New battlegrounds for machine builders |
New battlegrounds for machine builders
01 May 2024
Charlotte Stonestreet reports on the latest Controls, Drives & Automation webinar, sponsored by Schneider Electric, which took the form of a roundtable covering sustainability and servitisation

FOLLOWING INTRODUCTIONS and some general scene-setting, the webinar kicked into action with Mike Wilson who pointed out that here in the UK we are not really great users of robots and automation, and generally lag behind most competitors throughout the world. To put this into context, Wilson pointed to robot destiny figures, which give an indication of the number of robots in use per 10,000 workers and enable comparisons with other countries. At present the UK lies 25th in the world, despite being the eighth largest manufacturer.
“So if we were using robots at the same kind of level as other countries we should be somewhere more around the eighth to tenth sort of range,” said Wilson. “We (the UK) historically have not been very good at cap-ex investment throughout our manufacturing centre, but things are changing and it’s being driven by issues around sustainability in particular.”
Effective and efficient
Wilson asserted that using the latest automation technology is beneficial in terms of ensuring operations are as effective and efficient as they can be. Automation results in less waste, produces more consistent quality and helps achieve optimal energy use, as well as making sure that a piece of machinery is used as efficiently as possible
“A typical machine tool might be loaded and unloaded manually, and you will typically get 60-70% utilisation out of that tool, whereas if you can automate the load and unload you can increase that to about 90%,” said Wilson. “So you get a significant improvement in the efficiency of all the resources that you are putting into that process.
Wilson pointed to another global issue that the UK is well positioned to take advantage of, that of the trend for reshoring, which can also contribute to sustainability. It is important to consider not just the carbon emissions from the UK, but also the overseas emissions produced during the manufacture and transport of goods which are imported to the UK. Growing demand for mass customisation is also driving the desire to produce closer to the end consumer.
“That gives us an opportunity to bring things back to the UK,” said Wilson. “And to do that we need to be competitive, we need to do it without significantly increasing the amount of labour that we are using, so, therefore, we need to consider automation.”
As Wilson pointed out, automation and robotics give the potential to expand the UK’s manufacturing capability and ensure that it’s as sustainable as possible.
Different business model
Touching on servitisation, Wilson said: “Really, it’s just a different business model in terms of how people sell the equipment, and rather than purchasing the equipment, you are buying the ability to produce a certain number of parts an hour, or whatever it might be. Fundamentally, that makes it easier to invest in that equipment because it’s not necessarily coming out of cap-ex.”
Given that the UK has been historically poor at cap-ex, this gives the opportunity to take advantage of the latest technologies going forward.
In the context of sustainability, Wilson also talked about the recycling and refreshment of automation equipment, pointing out that in the past businesses might have simply discarded a piece of equipment once it had reached the end of its life. However, there is a second hand market for industrial robots and some of the bigger companies are starting to take robots back for refurbishment and resale back into the market.
“Those opportunities make it potentially less expensive for some of the smaller businesses to get into this technology.” said Wilson “So we start to develop a circular process that;’s beneficial for the whole of UK industry.
“We are just at the start of this journey, but there is a big opportunity for the UK to take leadership in this kind of approach, and then that will give us the chance to catch up, or even leapfrog our main competitors.”
Scoping out the complexities
The conversation then turned to the reasons behind the need for OEMs, and the wider market, to compete specifically on sustainability - a subject addressed by Mike Teller, global strategy and sustainability leader, OEM industry business, at Schneider.
“We do things for two reasons, I guess, at a basic level, either because we see a reason to do it and want to do it or because we have to,” said Teller. He pointed to regulatory requirements from both the UK and the EU (to where the UK exports) which mean companies have to comply in terms of sustainability, as well as the voluntary side where businesses see the growing awareness amongst both their customers and their competition.
“There are areas that we hear about from the greenhouse gas protocol, where we talk about scope 1, scope 2 and scope 3. A scope 1 emission is something we generate ourselves; so I have a gas boiler where I am which is heating the radiators which keep me warm so that’s my scope 1 emission. Scope 2 is an emission made on my behalf, so I’m running my computer at the moment on electricity which is made by the power station down the road, and that is an emission made on my behalf so I can purchase their electricity.” says Teller.
“Scope 1 and scope 2 are more or less within my control; scope 3 is far more complex. It’s everything upstream - so everything that we buy into Schneider Electric to put into a product – and everything downstream that goes to our customer. And scope 3 is by far the largest area. This is where – selling products and solutions to our machine builder partners who then sell them on to end users – we can have the biggest effect. So this is also where the biggest opportunity is.
Teller highlighted that 80% of a product's sustainability is determined at the design stage. As he pointed out, it is not possible to build a machine and then expect to fine tune it three years later; this is where Schneider uses digital twin technology to design in partnership with the machine builder.
The digital twin
Miklosh Bakos OEM offer manager UK&I at Schneider also talked about the importance of designing in sustainability right from the onset. He referenced a 2022 study from Gartner which analysed the whole machine building process; this determined that roughly 60% of the commission time is wasted with fault fixing.
“That’s a big number, 60%,” said Bakos. “To address this and to make it faster for the OEM to get through the whole process, the digital twin can be one pillar of success, speeding up commissions and making it more efficient.”
Bakos explained how the digital twin brings value beyond just the design, easing collaboration amongst the various parties working on a project, providing a detailed sales tool to showcase the machine itself, and enabling remote maintenance.
Responding, Chris Haines, marketing director, industry at Schneider talked about the huge potential for enhancing sustainability through predictive maintenance. This can, he said save end users’ time, energy, and resource by being more intelligent about what is maintained and how and it is maintained, based on the condition of the condition of the equipment rather than relying on manufacturer recommended maintenance intervals.
“If you are monitoring the actual condition of your assets, you can tell where and when they need maintaining and you can extent the maintenance intervals if it’s not being worked particularly hard, or if it’s in a clean environment, and you can save an awful lot of time, energy, resource, materials – and as a result carbon – by doing that,“ said Haines.
He also pointed out that if a piece of machinery is being worked particularly hard or is in a harsh environment, monitoring the condition can identify that maintenance is needed before the recommenced interval comes up, potentially averting catastrophic failure. “It’s another way of saving time, money and energy,” he said.
When it comes to repair and remanufacture, Haines feels that this is another aspect that can contribute to sustainability as a whole.
“There’s no silver bullet for sustainability, there’s no one big ticket item that you can go for, it’s really about aggregating marginal gains,“ said Haines. “It’s lot of little things that add up on your journey to net zero.”
Gain further insight
This article gives just a taster of what was covered in the webinar, so if you want to find out more details visit the website below and view the event on-demand at a time to suit you.
- More robots doesn't have to mean fewer jobs
- More digitalisation funding needed
- Family affair
- UK digitalisation spend looks to lag
- Manufacturing at increased risk of cyber attacks
- Cyber security wake-up call
- Industry FOMO has to be a good thing, right?
- Back to the future
- A far from fond farewell
- Don't waste the potential...