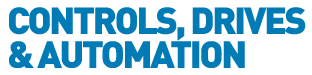
![]() |
Charlotte Stonestreet
Managing Editor |
1/2 (1 to 10 of 19)
Automate these processes for a fast ROI | 29/07/2022 |
---|---|
Looking to reap the benefits of automating manual processes in terms of cost reduction, quality improvement and increased safety? Neil Ballinger identifies tasks that, once automated, offer a particularly fast return on investment SINCE THE emergence of the term Industry 4.0 in 2011, the digital journey of most manufacturers has been characterised by a marathon-like approach — slow and steady. For manufacturers who are not blessed with an endless stream of cash and expert teams of in-house technologists, the gradual implementation of automation has been the safest and most effective way of digitalising their premises. However, the COVID-19 pandemic and its ripple effect on the global socio-political balance has forced manufacturers to digitalise at full throttle, effectively turning their Industry 4.0 journey from a marathon to a sprint. In this scenario, plant managers are under increasing pressure to make the best decision when prioritising processes to be switched from manual to digital. Although the needs of every production or assembly plant differ, when planning an automation project there are three key variables that plant managers should consider — the speed of the return on investment (ROI), the ease of implementation, and the impact of the project on the workforce. Let’s see a few examples of digitalisation projects that win on all three fronts. Pick & place The repetitive act of picking up a piece and placing it in the correct spot for further processing is enough to test the patience of even the most motivated employee. When parts are heavy, difficult to manipulate or in close proximity to hot surfaces and dangerous machinery, the task turns from tedious to hazardous. Luckily, pick and place applications are some of the easiest and most cost-effective to digitalise. There is a wide variety of robotic arms on the market that require little upfront investment, can be programmed with no coding expertise, and drastically facilitate employees’ work. For example, igus’ latest cobot, part of the igus Rebel family, costs less than EUR 5,000 and can be programmed remotely through an online integration service that offers fixed-price consultations. This plug and play cobot is up and running in just a couple of days and can lift up to 2kg. For heavier lifting, such as in palletising applications, prices are considerably higher — a standard solution handling one layer per minute starts at around EUR140,000, excluding integration and extra accessories. Programming and maintenance can also be quite complex and generally requires the assistance of a systems integrator. However, automatic palletisers can have a huge impact on staff wellbeing, since manual palletisation is a demanding physical task that can often lead to accidents and repetitive strain injuries (RSIs). Though capital recovery might be slower than in other automation projects, the benefits in increased safety and staff retention will be worth the investment in the long run. Quality assurance The strict standards of Industry 4.0 make quality assurance (QA) an essential step of the manufacturing process. However, the cost and complexity of traditional machine vision solutions mean that many factories still rely on manual inspection. Unfortunately, human inspectors cannot reliably check complex products for eight hours a day without missing defects. Think of a printed circuit board (PCB) — a single item can contain dozens of hardly visible sub-components, each of which can present defects that compromise the functionality of the whole board. Luckily, new solutions that transcend the limitations of traditional machine vision are reaching the market. For example, German-Israeli company Inspekto has developed a cost-effective Autonomous Machine Vision system, the INSPEKTO S70, that can be set up by the plant’s own personnel, without the help of a machine vision expert. The system comes pre-trained for a wide variety of use cases, which drastically reduces installation time. Machine vision solutions such as Inspekto’s lead to a quick ROI thanks to their ability to reduce the cost of defects, which can include material waste, re-working costs, late delivery fees, reputational damage and more. Moreover, automating quality assurance can free up personnel to perform more engaging tasks that add value. The wide variety of machine vision companies on the market and the many low-code and no-code solutions they provide ensure that manufacturers can find a QA system that matches their budget and technical skills. Data entry Fast and reliable data entry is essential for all processes that require accurate, up-to-date information, from monitoring sensor data for predictive maintenance, to processing bills of materials. Manual data entry can often become a bottleneck for businesses, as data entry clerks might not be able to keep up with the need for real-time information and might introduce errors while reporting figures. This is where automated data entry systems can help. Using optical character recognition, data entry software can read information from a wide variety of sources, such as PDFs, e-mails and websites, and absorb it into a centralised data storage application, be it a database or simple spreadsheet. Automated data entry has a wide range of applications. The most common and well-known is automated invoice scanning, but data entry software can help in countless scenarios, such as preparing reports for audits and quality controls, managing business enquiries, processing the results of customer satisfaction surveys and more. On top of these benefits, data entry software is generally simple to install and manage and can be extremely cost-effective — Culverdocs, for example, offers an all-inclusive package for a monthly fee of only £20 per user. Cashflow, employee retention and a technical skills gap are some of the biggest challenges manufacturers are currently facing. By considering the ROI of their automation projects, their impact on the workforce and how easily they can be deployed and maintained, manufacturers can speed up their digitalisation marathon, taking the leap they need to gain a considerable competitive advantage. Neil Ballinger is head of EMEA at EU Automation
Key Points
|
|
|
|
How small manufacturers can implement digital technologies | 27/04/2022 |
DUE TO the large initial cost of creating a smart factory, many small manufacturers cannot keep up with their larger counterparts. Neil Bellinger discusses how small manufacturing companies can digitalise their processes to keep their competitive edge. Industrial digitalisation offers huge benefits to manufacturers – not only could it increase profits within a company, but also improve productivity by 25 per cent. However, the cost, risk, complexity and lack of applicable digital skills make it hard for smaller manufacturers to implement this revolutionary change. So, how can small manufacturing companies keep up with the competition? With many businesses feeling the strain of the COVID-19 pandemic and subsequent economic instability over the last couple of years, it has become clear that those that can adapt and respond quickly to changes are the ones with tools and processes that are flexible to change, digital tools offer that flexibility. There are many tips on how small manufacturers can overcome these obstacles, such as starting small and focusing on the small changes the business can make instead of the large, expensive and burdensome projects that can take years to make a profit. For example, companies can buy low-cost cobots like the Automata six-axis cobot arm for £5,000 or they can retrofit sensors on legacy equipment to keep costs lower. Implementing many small digital changes can have the impact of one large change without the added challenges that come with larger projects, such as integration issues, added training and extra maintenance. Other ways companies can lessen the challenges of digitalisation is by empowering their employees. The old command and control management style is obsolete, instead successful businesses use hybrid top-down and bottom-up approaches. This means that instead of going up the chain of command to solve issues, employers are empowering the individuals closest to the problem at hand to create a solution and think of new ideas that align with an overall mission set by executive leadership. This can help boost morale, productivity and lessen the strain on managers. The solution on a shoestring These tips are not the only way manufacturers can implement digitalisation. Professor Duncan McFarlane of the University of Cambridge founded a programme at Cambridge’s Institute for Manufacturing, aimed at educating small businesses on digital technologies for manufacturing. McFarlane has coined this programme ‘Digital Manufacturing on a Shoestring’. Digital manufacturing on a shoestring is said to be a low risk, low-cost approach to digital solutions. To create this programme, McFarlane's team surveyed and classified low-cost technologies that they then organized into a set of 59 digital solution areas that can be reused, adapted and combined. Some of the solutions in this programme include consumer-grade microcomputers, like the Raspberry Pi, and low-cost sensors. These low-cost alternatives can be placed in an industrial-proof casing, protecting them from the factory environment in a cheaper way. Using this programme, 14 industry partners have successfully started or completed a pilot with a Shoestring solution, giving overwhelmingly positive feedback. Although industrial digitalisation may be difficult for small businesses to implement, it is not impossible. With helpful tips and low-cost alternatives available, it is time for all manufacturing companies to move into industry 4.0. To keep up to date with the latest news impacting the manufacturing industry, visit the EU Automation Knowledge Hub. |
|
|
|
Pets versus cattle: cloud computing in manufacturing | 27/01/2022 |
NEIL BELLINGER, head of EMEA at global automation parts supplier EU Automation, delves into the native cloud and why it is the future of manufacturing. The cloud-native approach is often conceptualised using the 'Pets vs. Cattle' DevOps concept, which compares traditional server systems, which are unique and cared for, to pets and cloud systems to cattle. Cattle are identical, assigned, scalable systems where if one of the systems were to be unavailable or fail, the whole network would not be affected. Given the value of the cloud, one wonders why the manufacturing industry is resisting the move to cloud-native systems, especially with companies already using various cloud-based applications. Until recently, manufacturing industries have been up to date with the latest innovations, from production tracking systems to artificial intelligence. Although financial and retail sectors have followed business giants like Netflix and Spotify, many still resist the switch to cloud-native. While 83 per cent have a strategy for cloud implementation established, many still struggle to visualise the business value and cost savings of the cloud-native approach. However, forward-looking businesses are making the first steps in this direction. For example, one company currently implementing cloud-native applications is Volkswagen, training more than 200 specialists for its cloud-innovation centre. Cloud-native is the term used to describe software and services that run on the internet instead of a local computer system, allowing businesses to be faster and more agile. Cloud-based applications, however, are not created in the cloud but instead transferred from an in-house web application to a cloud server. This cloud-based system allows for the availability and scalability of cloud-native applications without redesigning current applications. Cloud-enabled is similar to cloud-based, with the migration of the traditional application to the cloud. However, it does not have easy availability and scalability of cloud-based or cloud-native. Some examples of cloud computing in the manufacturing industry are cloud-based marketing, product development, production and stock tracking, and productivity management. The responsiveness, innovative features and zero downtime deployment of the cloud-native model provide businesses with a database needed to succeed in modern times. Successful examples of this implementation are Netflix and Uber. Netflix currently operates using over 600 services, with an update rate of around 100 times per day. The structural design of the cloud-native enables the rapid response, scalability, and selective deployment observed in companies such as Uber, Netflix and Spotify. The cloud-native revolution Cloud-native is the clear future of all businesses, including manufacturing. As seen in the last two years, implementing changes to aid when mass disruption like the pandemic occurs is extremely important for business survival. With accessibility possible from across the globe via the internet, the cloud-native approach is the best change companies could make. The restriction of large on-premise systems has held back the manufacturing industry for years, but cloud-native applications enable companies to use small, reusable and independently deployable microservices. It can also allow the automation infrastructure, application delivery, recovery and scaling to increase, providing a more resilient and high performing system. The cloud-native model can also aid in lessening the strain of managing back-end software and infrastructure. Cloud-native apps also enable the sharing and analysing of data across the organisation by being the central repository for data flowing from sensors, machines, programmable logic controllers (PLCs), and more. At EU Automation, we value the importance of keeping with the times and understanding the cost of downtime. Cloud-native is the next step in lessening the impact of failures in company systems. To stay informed about the developments of the cloud-native approach and how to unlock Industry 4.0, visit EU Automation’s Knowledge Hub. |
|
|
|
Top three automation trends in 2022 | 05/01/2022 |
AUTOMATION HAS always been characterised by rapid growth, constant innovation and new work patterns. However, the events of the past two years have amplified the need of businesses across every industry for automation technologies to help them respond to global trends and stay competitive. Neil Ballinger explains what trends will impact automation in 2022. If automation had to be summarised in one word, that would be agility. The field’s speed in introducing disruptive ideas, innovative technologies and new concepts is surprising, but can also be hard for manufacturers to keep up with. While it might be difficult to know what technologies are worth investing in 2022, here are the top three trends that are most likely to change the face of automation. Cloud native In 2022, cloud native is predicted to become the most popular application of cloud. Cloud native technologies are a new approach to designing and operating workloads that are built into the cloud. Their main role is to decompress software into more manageable pieces and scale up small areas of a complex infrastructure when needed, without full redeployment. According to the Cloud Native Computing Foundation, these technologies, when coupled with robust automation, allow engineers to “make high-impact changes frequently and predictably with minimal toil”. Cloud native can increase operational efficiency while shortening time to the market for new services because the software is more decoupled from the main hardware and decompressed in smaller pieces, which allows for faster automated updates. Low-code platforms Low-code automation platforms allow users with little coding knowledge to automate processes using graphical interfaces instead of traditional computer programming. They also allows teams of engineers and IT professionals to reduce manual labour and instead focus on core strategies to promote business growth. This trend has seen a steady increase and is predicted to make up more than 65 per cent of all app development functions by 2024, according to Gartner. Similarly, around 66% of big companies will use at least four low code platforms. Some of the benefits of using low-code automation platforms include increased agility by cutting on app development time, reduced costs from hiring talented developers and more compatibility with other third-party modules and application programming interfaces. Digital twins It is no surprise by now that technologies that facilitate remote working and maintenance will be best received by manufacturers and automation professionals. Digital twins will be widely adopted, with more than 70 per cent of manufacturers predicted to implement them by the end of 2022 to perform scenario evaluations and process simulations. According to simulation solutions pioneers CADFEM, digital twins can lower maintenance costs by 30 per cent, reduce technical defects by 75 per cent and bring about 45 per cent less downtime. This technology is pushing augmented reality and virtual reality to a new level by allowing manufacturers to monitor their operations in real time and take action to prevent downtime. A digital twin can be connected to a machine’s sensors to indicate its parameters throughout its lifecycle and signal faults. On top of this, digital twins can be used to simulate programmes for new processes and equipment before investing resources in implementing them. This saves on costs and time, and also reduces material waste to help develop smart, sustainable factories. In 2022, technologies that tap into the industry’s need for digitalisation, remote working and faster implementation will see a significant growth. At EU Automation, we strive to play an essential role in the development of automation technologies by delivering automation parts for companies’ ecosystems as fast as possible, as well as educating professionals in their automation journey. To keep up to date with automation news, innovative technologies and market predictions, visit EU Automation's Knowledge Hub. Neil Ballinger is head of EMEA at EU Automation |
|
|
|
Why do you need a soft starter? | 21/10/2021 |
The increasingly serious energy crisis and rising energy costs mean that technologies for reducing motor power consumption have become even more essential. Neil Ballinger explains the benefits of soft starters IMAGINE YOU are sitting in traffic. When the traffic light turns green, it’s usually a good idea to not stamp on the accelerator to reach full speed, because this may cause mechanical wear on the vehicle and could be rather inefficient, on top of being dangerous. The same is true for electronic equipment, where a slow start helps reduce energy consumption and excessive wear. This is why by using soft starters in electric motors, manufacturers can boost energy efficiency and improve the machine’s performance. Soft starters are used to limit the initial inrush of current and provide a gradual ramp up to full speed or to stop gradually where a sudden halt may damage the connected equipment. They help reduce the mechanical stress on the motor and shaft as well as the electrodynamic stresses on the attached power cables and electrical distribution network. Soft starters use three pairs of silicon controlled rectifiers (SCRs), one for each phase of power. Each pair of SCRs is used. They are applied gradually for the portion of each voltage phase, controlling the voltage provided to the motor and thus temporarily reducing the motor’s terminal voltage. Accordingly, current is reduced proportionally to the reduction in voltage. As torque is proportional to the square of the voltage, even a smaller reduction in voltage leads to a large reduction in torque. For instance, a 50% reduction in voltage results in a 50% reduction in current and a 75% reduction in torque. Reduce energy consumption Electric motors used in industry are responsible for two thirds of the entire industrial electricity consumption in the UK. The energy cost to run an electric motor over ten years is at least 30 times its original price. Since accelerating up to the required speed needs a lot of power, the startup of motors could consume vast amounts of energy. To control the energy consumption during this period, manufacturers could consider using soft starters. With a normal start, the motor immediately starts consuming the maximum amount of energy and continues to do so for the whole operation. With soft starters, the voltage gradually rises to the maximum, leading to a smooth acceleration of the motor and coupled load. In this way, less overall energy is used. Improve motor performance Besides reducing energy consumption, a soft starter helps protect the motor and connected equipment from damage by providing a gradual acceleration of the drive system and thus reducing the mechanical shock associated with motors’ startup. The reduced mechanical wear on motors and other components such as belts and pulleys, gears and chains as well as couplings and bearings, could significantly extend the system’s lifetime, contributing to shorter downtime and less maintenance. Moreover, soft starters only cost up to one-tenth of the price of high-power drives. Therefore, for applications where only the control of speed and torque during motor startup is required, a soft starter could be an economical choice. Another benefit of soft starters is that they usually take up less space than variable speed drives (VSD). By adopting soft starters, manufacturers can boost energy efficiency while also improving motors’ performance. Owing to the colossal energy consumption of electric motors, it is necessary to apply cost-effective and energy-saving products, like soft starters, from the beginning of the operation of electric motors. EU Automation provides a large supply of automation parts for electric motors, servo drives, PLC systems, HMIs and other industrial applications. Neil Ballinger is head of EMEA at EU Automation
Key Points
|
|
|
|
Remote working in engineering | 01/09/2021 |
While for many occupations a suitable work environment requires no more than a desk, a PC and an Internet connection, maintenance engineers often require innovative technology. Neil Ballinger discusses the requirements of remote working maintenance engineers CHALLENGING WORKING conditions require innovative and effective solutions, one being remote condition monitoring (RCM) for industrial equipment. Remote condition monitoring is the ability to view the performance, status and behaviour of a machine from a distance in real time. This is achieved with a combination of Internet of Things (IoT) technology and cloud computing that allows an on-site machine to be tracked by maintenance engineers wherever they are. How does RCM work? To be effective, RCM uses three key components — stable connectivity to collect data, a platform to process and store them, and tools to present them to engineers. Firstly, sensors are being attached to the plant equipment to continuously relay vast amounts of data. The latest machinery comes equipped with such sensors, but for older assets, these sensors can be added into the existing structures. Collecting data requires a standardised industrial connectivity that can support an Industrial IoT platform. The platform establishes a secure connection between the machines and the sensors and provides real-time notifications alerts and cloud storing services. After data is collected, it needs to be stored and processed accordingly. The metrics are sent to the cloud and stored on the IoT platform to be transformed into actionable information. Finally, this information is delivered through dashboard applications or mobile notifications to a maintenance engineer. Remote monitoring solutions using the latest applications will also leverage additional features, such as intelligent queuing or routing of notifications, geospatial directions of the asset or even service instructions. From here onwards, if engineers detect a problem in one of the machines, they can perform root cause analysis, order replacement parts, and direct the maintenance team, all from the comfort of their own houses. Added benefits In recent months, large corporations have trialled virtual reality headsets for meetings to give people the impression they sat next to each other. The challenge for maintenance engineers is not only to find a suitable remote working environment, but also to train future engineers for the growing demand in the field. Augmented reality (AR) could replace face to face training and deliver innovative experiences for workers to develop their skills.
Augmented reality could replace face to face training and deliver innovative experiences
Regardless of their location, workers can come together in a virtual setting and share information, while also tracking their work progress in real time. Not only could workers step into a virtual training session, but their work on analysing large amounts of data can be simplified by presenting the data in a visual form, regardless of where they are and what they are doing. For example, as the workplan appears before their eyes, it can be analysed while walking the dog or enjoying a sunny day in the garden. Thanks to RCM and augmented reality, potential problems can be spotted early on and replacement parts can be ordered before failures can cause downtime and generate financial loss. EU Automation supplies new, reconditioned and obsolete automation and control parts quickly anywhere in the world. This way a maintenance engineer in the United Kingdom could, for example, assist a machine in a plant in Australia in the quickest time. Not only would this reduce downtime, it would also mean experts all over the world could help each other and share knowledge. While solutions like remote condition monitoring and augmented reality may seem farfetched, the changing conditions of remote working could make them a reality in the near future. For maintenance engineers, such solutions could ensure they are able to do their job from the comfort and safety of their own houses. Neil Ballinger is head of EMEA at EU Automation
Key Points
|
|
|
|
PLC vs embedded control — which one’s best? | 11/08/2021 |
PROGRAMMABLE LOGIC controllers (PLCs) are at the core of almost any automated system. They’ve been used in manufacturing for decades and are known for their reliability and ability to withstand harsh operating conditions. However, embedded systems can perform the same function for a fraction of the price. So, why aren’t manufacturers rushing to replace their trusted PLCs? Here Neil Ballinger explains the pros and cons of both options. As the old slogan taught us, power is nothing without control. Even the most sophisticated industrial automation equipment will be useless without a reliable controller to monitor input/output activities and gather data from sensors. However, there’s more than one option to achieve the same result.
A PLC is a stand-alone unit that can control one or more machines and is connected to them by cables. On the other hand, in an embedded control architecture the controller — which is almost always a printed circuit board (PCB) — is located inside the machine it controls. This leads to several advantages, such as having less hardware and no cables to worry about. An embedded architecture also means shorter distance between the machine and the controller. This can positively impact the quality of the signal, as well as reduce chances for electromagnetic interference. In turn, this results in improved motion control and more precise data from sensors. However, the biggest reason why some manufacturers opt for embedded control is cost. Less hardware also means less initial capital investment — an embedded controller can be purchased for just about 20 per cent of the price of a PLC from a reputable brand. When PLCs are best With all these advantages, one might wonder why manufacturers haven’t all moved to integrated controllers. PLCs still play a critical role on the shop floors of most factories worldwide, and with good reason. One of the main advantages of PLCs is their ease of maintenance. Being located outside the machine they control, PLCs are easier to access than embedded systems. Moreover, PLCs have a modular structure which makes them easy to fix if a specific module fails. On the other hand, embedded controllers are designed as a single board, which makes them cheaper, but harder to repair. Another reason to prefer PLCs is regulatory compliance. Branded PLCs usually come with CE marking, and can also be found pre-certified for more specific standards such as the Restriction of Hazardous Substances (RoHS) certificate. Certified embedded controllers can also be found, but the final integrated solution might have to be further assessed for conformance. In the end, the cost of this process can easily match or surpass the difference in price between an embedded controller and a PLC, making the latter the more convenient option. Another major challenge of replacing PLCs with integrated systems is the programming language. PLCs are usually easier to programme, since they use ladder logic and functional blocks diagrams, while embedded systems are usually encoded in programming languages such as C or Java. The shift in programming can be a big cultural barrier to overcome, especially in smaller organisations. Finally, one of the main reasons why manufacturers may wish to stick to PLCs is their reliability. Their ruggedness and ability to withstand the rough environments of many industrial sectors have made PLCs the equipment of choice when vibrations, humidity, contaminants and temperature fluctuations might impact the functionality of more delicate components, such as microcontrollers. Embedded controllers have undeniable advantages, but PLCs still represent an excellent choice when manufacturers need a controller that is reliable and easy to maintain. In case of failure, PLCs can be quickly and easily replaced by contacting a trustworthy supplier like EU Automation, who will be able to assist you in sourcing new, reconditioned and obsolete PLCs from all major original equipment manufacturers (OEMs). Neil Ballinger is head of EMEA at automation parts supplier EU Automation |
|
|
|
End-to-end intelligent automation | 28/06/2021 |
NEIL BELLINGER explains how to achieve intelligent automation by combining process automation with artificial intelligence Intelligent Automation (IA) combines Robotic Process Automation (RPA) with artificial intelligence (AI) to accomplish rapid end-to-end business automation and empower owners to boost their digitalisation. IA supports all processes of the automation cycle and develops them in line with new digital requirements without pre-set instructions and structured data inputs. It also allows businesses to reimagine their possibilities in term of workflows, by optimising the relation between robots, humans and work processes. Assigning mundane and repetitive tasks to robots liberates human workers and lets them use their unique human abilities. Here is how end-to-end intelligent automation is structured. Robotic Process Automation The starting point to achieve intelligent end-to-end automation of your workflow is RPA. Its main purpose is to reduce human input in computer applications to allow workers to focus on more valuable tasks for the company, such as improving customer interaction or developing business strategies. It is not meant to replicate human-like intelligence, but to mimic rudimentary human tasks. RPA is a software program which runs on a worker’s computer or mobile device and generates a sequence of commands that will then be executed by bots under defined sets of business rules. These bots can work 24 hours without compromising on accuracy and efficiency, which is important for reducing the risk of errors that humans are prone to. The software can be used to automate workflow, infrastructure and back-office processes which are labour intensive. This tool interacts with the existing IT infrastructure and does not require a complex system integration. This provides a quick and cost-effective solution for companies to start their digitalisation process. Furthermore, RPA is scalable, meaning that when a process changes, the software can be adapted by changing a few lines of software code. Intelligent automation While RPA works by mimicking human activities, artificial intelligence simulates human behaviour to make smart decisions and respond to more complex tasks. AI-powered tools automatically observe the work activities people are doing, identify optimal workflows, and propose an automation path. For example, AI-powered platforms can extract useful information from unstructured data in the form of chat conversation, audio and video, which is crucial to making end-to-end automation possible. On top of that, integrating machine learning can contribute to deductive analytics and predictive decisions that increasingly approximate the outcomes that can be expected from humans. Machines learn from past experiences using historical data and different algorithms that will inform future decisions. By combining RPA with cognitive technologies such as machine learning and AI, companies can automate higher-order tasks that in the past required the judgement capabilities of humans. RPA complements AI by generating useful insights that are then used to handle complex cases. This type of intelligent automation will not only help businesses optimise processes and manage their workflow more efficiently, but it will also help them stay competitive in an ever-changing digitalised environment that requires the most innovative solutions. |
|
|
|
Are you too small for industrial robotics? | 22/02/2021 |
THERE IS a misconception that the benefits of industrial robots are reserved for few manufacturing giants. However, according to the Robotics Industries Association (RIA), enterprises with less than 100 employees and less than ten robots represent a growing segment of the robotics market. Neil Ballinger explains what to consider when implementing robotics in small and mid-sized manufacturing businesses. Small and medium-sized enterprises (SMEs) are the economic backbone of some of the most industrialised countries in the world. In Germany, for example, they generate about 37 per cent of total corporate turnover. SMEs represent a very attractive market for robot manufacturers, who are adapting their offer to add flexible, user-friendly and cost-effective solutions to their portfolios. These can be a real asset for smaller businesses, but to choose the best one for their needs, manufacturers should ask themselves the right questions. Why do we need it? Manufacturers might fall victim to the pressure to digitalise without a specific strategy in mind, but assessing the plant’s real needs is key to investing in the right tools. Ask yourself what kind of challenges your company is experiencing, and whether or not they can be tackled by industrial robotics. Are you struggling to fill positions for repetitive manual tasks? Are dangerous operations impacting workers’ safety? Would you like to add night and weekend shifts without increasing labour costs? These issues can be successfully tackled with robotics. Indeed, if a task doesn’t require thinking on the spot, creativity, or human dexterity, it can probably be automated. Can we afford it? SMEs are usually characterised by small production runs, but thanks to the latest innovations in collaborative robotics, manufacturers no longer need huge volumes to build a solid business case for investing in robotics. According to robot supplier RobotWorx, an industrial robot typically cost between £50,000 and £80,000. However, small and flexible alternatives, which are ideal for low-volume production, are available at a fraction of that price. For example, US-based Automata recently launched on the market Eva, a robot priced at just £8,000 and programmable in under 30 minutes. Eva is ideal to automate a variety of repetitive tasks, such as pick and place, machine tending, sorting and dispensing. Another low-cost option for pick and place applications is Delta Robot, developed by igus. The cost for a Delta Robot ranges from £10,000 to £15,000, including integration costs, and its typical ROI period is estimated at just six months. These small, flexible robotic arms are accessible to most businesses and add substantial value by freeing up human workers from tedious, repetitive tasks and allowing them to focus on jobs that require decision making and problem solving. Do we have the technical skills? A typical challenge for SMEs is the perceived need to hire a specialist to programme the robot and fix technical issues. In reality, most robot manufacturers have user-friendly options that don’t require any specific technical background to be set up and programmed. Eva, for example, is the protagonist of several YouTube unboxing videos where users explain how they assembled the robot and trained it to perform several tasks, in as little as 20 minutes. Other robots, like Delta, come pre-assembled and are ready to be programmed in a few easy steps. In addition, all robot manufacturers and integrators offer training to their customers. For example, the Universal Robots Academy is a free platform that teaches core programming skills to all UR cobots users, large or small. Replacing parts to fix or customise your robot can also be relatively easy. With the help of a reliable automation supplier like EU Automation, manufacturers can get the parts they need in as little as 24 hours. Too many businesses assume that robots are not for them and miss out on the benefits of automation. By embracing robots, SMEs can futureproof their operations and gain a substantial competitive advantage. Neil Ballinger is head of EMEA at EU Automation |
|
|
|
How to fix excessive servo motor noise & vibration | 18/12/2020 |
It’s easy to dismiss unusual noise and vibration in a servo motor as a small nuisance — after all, a certain level of both in rotating equipment is to be expected. However, when these exceed a critical threshold, they become a clear signal that something is not working properly and that action should be taken before the motor is irreversibly damaged. First of all, it’s useful to distinguish vibration from noise. Although strictly related, they are the symptoms of different malfunctions. It is the general rule that, in normal operating conditions, one kHz is what separates vibration from noise — if the measured frequency is one kHz or less, the problem is vibration, while anything above that should be treated as noise. A chattering or rattling noise can indicate a positioning error, especially if the model you’re working with has an auto-tune feature. It might be that the drive has been accidentally reset and if this is the case, following the set-up procedure again should fix the problem. If this doesn’t stop the noise, there’s probably a failure in the feedback unit and you will need the assistance of an authorised repair centre. On the other hand, a high-pitched noise usually indicates a bearing problem, such as a lack of lubrication or a worn bearing. Usually, servo bearings are protected in an enclosure, but dust can still creep in and dry out the lubricant. If the level and quality of lubricant are correct, then the servo probably needs a bearing change. Vibration Measuring the vibration levels and frequencies of your servo motor is an effective and affordable way of detecting potential issues. Depending on the problem, vibration data can be taken from different parts of the servo with different tools — for example, for vibrations that originate from the motor frame, you should gather housing vibration data with an accelerometer. On the other hand, for vibration coming from the rotors, you should collect shaft vibration data with a shaft stick or proximity probe. Vibration can be caused by several mechanical problems, such as loose or unlubricated bearings. if action is not taken, the vibrations can accentuate the original problem and cause indentations on the bearing raceways. Vibration can also be caused by misaligned gears, which can happen when a gear’s teeth are worn down and lose contact. Another common reason of excessive vibration is a weight imbalance in one of the rotating components of the servo motor. This can be caused by a manufacturing fault such as a casting flaw, or by maintenance issues such as dirt build-up on the fan blades. Finally, excessive vibration can happen when a servo motor is not securely attached to its foundation. This can lead to motor wear and fatigue and ultimately to flaking or cracking of the external material. Ensuring that the servo is aligned and securely fastened to its foundation will minimise not only vibration but also the resulting extra mechanical loading that can result from it. Stradivari violins have stood the test of time — after several centuries, the quality of their sound is still undisputed. Your servo motor won’t last that long, but with proper maintenance and prompt repairing it might serve you for decades. |
|
|