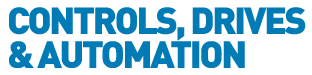
![]() |
Charlotte Stonestreet
Managing Editor |
1/3 (1 to 10 of 26)
It's time to embrace repairability | 30/07/2025 |
---|---|
IN A world grappling with climate imperatives, rising costs, and resource scarcity, one message is becoming increasingly clear from consumers: we want the right to repair, asserts Thomas Marks. ACROSS THE consumer market, we are seeing major brands wake up to a shift in public sentiment. People want products that last longer, and when they do break, they want to be able to fix them. One of the most compelling examples comes from Philips, which recently launched its "Fixables" programme. This initiative allows customers to download 3D-printable files for select parts of their products, such as a comb attachment for the OneBlade trimmer. Instead of waiting weeks for a minor replacement or discarding a still-functional product, users can print a new part themselves. It's a simple concept with profound implications: empower the consumer, reduce waste, and prolong product life. Other manufacturers are following suit. Logitech has partnered with the repair-championing website iFixit to provide spare parts and detailed repair guides, making it easier for consumers to fix their devices rather than replace them. Framework, the modular laptop company, has built its entire business model around repairability, offering laptops with easily swappable components. And Fairphone has long been a pioneer in this space, designing smartphones that allow users to replace batteries, screens, and cameras with basic tools. What unites these companies is a recognition of the growing consumer demand for sustainable, repairable products. They see the value in aligning with a circular economy – one that keeps products and materials in use for as long as possible, reducing waste and saving resources. And yet, when we turn our attention to the world of industrial equipment, this mindset is still relatively rare. There are manufacturers of industrial equipment who embrace repairability; those designing products with ease of repair as a consideration and improving after-sales support with documentation and spares availability. But the scale of adoption feels, to me, to be behind the consumer space. Cynics might point out that EU Right to Repair legislation, introduced as part of the European Green Deal and reinforced by the EcoDesign Directive, currently applies to a specific set of household and electronic appliances, suggesting this is a driver of the change we are seeing in the consumer space. But while the EU's Right to Repair legislation has primarily targeted household appliances and consumer electronics, there is a clear trajectory toward including industrial equipment such as electric motors and pumps. At the Association of Electrical and Mechanical Trades (AEMT), we work with a wide range of repair specialists who see first-hand how much valuable equipment is discarded simply because it wasn't designed to be repaired. This is not only wasteful but also expensive. Repairing industrial machinery can be more cost-effective than replacing it, particularly when considering downtime, installation, and integration costs. Designing for repairability in industrial equipment isn't just about making spare parts available. It's about embracing modular design principles, improving documentation, and supporting third-party repairers. It means moving away from closed systems that lock out end-users and toward open, collaborative ecosystems. The consumer sector is showing us the way. Philips' Fixables programme is just one example of what could be a broader transformation in product design and customer support. If individuals can 3D print a replacement part for a personal trimmer, why shouldn't a maintenance engineer be able to access similar files or guides for a faulty motor coupling or panel component? We must take inspiration from these developments. Industrial equipment manufacturers have an opportunity — and, I would argue, an obligation — to respond. By prioritising repairability, they not only reduce costs for their customers and help the environment but also future-proof their own businesses in an increasingly sustainability-driven world. The right to repair isn't just a consumer trend. It's a cultural shift. It's time our sector caught up. Thomas Marks is general manager and secretary at the AEMT |
|
|
|
Ex-rated equipment repair guide | 29/08/2024 |
THE ASSOCIATION of Electrical and Mechanical Trades (AEMT), which represents a membership of specialists in the repair, maintenance, and servicing of rotating electrical machinery and associated businesses, has published the latest in a series of guides for those working with electromechanical equipment. The 'AEMT Introduction to Ex Repairs' has been designed to help users of Ex-rated equipment understand explosion protection techniques, the complexities of repairing Ex-rated equipment, and the critical roles of responsible personnel. Initially created for member service centres to share with their customers to help educate and inform them on getting their ex-equipment repaired responsibly, the guide is freely available to download from the association's Resource Hub at www.theaemt.com The guide covers several areas related to the repair of Ex-rated equipment, including proper maintenance and repair techniques and the consequences of not carrying them out, as well as an introductory overview of the key legislation and standards involved. Explosion protection techniques and some of the differences in design between Ex- and non-Ex-rated equipment are also explained. From a repair perspective, the guide outlines the complexities of repairing Ex-rated equipment alongside key roles and responsibilities of both the equipment user and the repair technicians. It also covers the importance of documentation and traceability, including what needs to be recorded and for how long. Finally, the guide explains the benefits of choosing a repair facility from the AEMT's Ex Register and outlines the requirements the repair facilities need to meet to be included on the register. The 'AEMT Introduction to Ex Equipment Repairs' joins previous guides, 'The AEMT Guide to Minimising Downtime', 'The AEMT Guide to Minimising Total Cost of Ownership of Motors', and 'The AEMT Guide to Ecodesign Regulations for Electric Motors (2021)', all of which are available to download at: |
|
|
|
Guide to reducing unplanned downtime in motor-driven systems | 28/02/2024 |
THE ASSOCIATION of Electrical and Mechanical Trades (AEMT) has produced a new guide designed to help motor-driven equipment users minimise unplanned downtime. Unplanned downtime can have significant direct and indirect costs on a business – lost production, wasted materials and ingredients, the high cost of reactive maintenance, reputational damage and even human safety risks. In some industries, the cost can be huge, but even when the cost is not so high, unplanned downtime is unwelcome. This comprehensive new six-page guide, which can be downloaded from https://bit.ly/AEMTmdg, outlines a range of steps that users of motor-driven systems can take to minimise the likelihood of unscheduled interruptions to the operation of their systems. The AEMT’s new guide covers five key areas. The first is installation, which highlights key factors to consider when setting up and implementing a new motor-driven system, all of which can ensure it starts with a sound foundation. Ongoing routine maintenance is also featured, with suggestions around key steps to take in the short, medium, and long term. The availability of spares and how they are stored, to enable a system to be promptly and reliably recommissioned when needed, is also addressed. While how motor repairs are carried out and their impact on the ongoing reliability of a motor-driven system, is also outlined. The final area covered in the guide is condition monitoring. This section explores the areas which can be monitored and busts a few myths surrounding the topic. Commenting on the publication of the new guide, Thomas Marks, the AEMT’s secretary and general manager, said: “Our members are experts in getting to the route of issues within electromechanical systems and repairing them quickly to the highest standards. However, a lot of the failures they see could have been avoided. This new guide has been produced to give users of motor-driven systems an outline of best practices they can implement to reduce the risks of financial and reputational damage being caused by unplanned downtime.” The guide is part of a series produced by the AEMT, which also includes a guide to motor efficiency legislation and one which looks at ways to reduce a motor-driven system’s total cost of ownership. Download the guide at: |
|
|
|
AI-powered navigation of electromechanical repair and maintenance standards | 04/01/2024 |
THE ASSOCIATION of Electrical and Mechanical Trades (AEMT) is working with the British Standards Institute (BSI) and UKRI’s Driving the Electric Revolution Challenge, delivered by Innovate UK, to develop an AI-powered tool to help electromechanical repair specialists ensure they repair hazardous area motors to the correct standard. The tool, which is being developed with some funding and support from Innovate UK, will enable engineers repairing rotating electrical equipment to clarify technical requirements through an easy-to-operate chatbot-style interface. Within the BS EN and IEC 60079 series of standards, various technical standards govern, among other things, the repair, overhaul, reclamation, installation, maintenance, and inspection, plus the design, testing and marking of equipment designed for use in explosive atmospheres. Navigating and interpreting this complex range of standards can be time-consuming and open to error. In addition, these standards are reviewed and updated periodically; however, it can be a challenge to ensure the right standard is used in conjunction with the age of the equipment being repaired. The tool under development by the AEMT and BSI aims to vastly simplify interpreting and complying with these complex standards while reducing the potential for error. Users of the system will be able to ask questions about the repair they are working on and be provided with the technical guidance and information required to ensure compliance and safety. The chat-based interface draws on large language model technology, which allows for further detail or clarification where needed. This is particularly valuable in interpreting a range of cross-referenced documents, where identifying the pertinent parts of various standards is not straightforward. By understanding the year in which the type of hazardous area equipment was certified, which can be established from the first two digits of the certificate number, the chatbot will be able to establish which version of the relevant standard applies. For example, in the 2000 version of the Ex d standard BS EN 50018, the dimensions relating to flame paths differ from those in the 2004 version, IEC 60079-1. However, where IEC 60079-19, which covers the repair, overhaul, and reclamation of equipment designed for use in explosive atmospheres, is concerned, the chatbot will only give information from the latest version. The tool will initially cover ten versions of four different BS EN Hazardous Area standards and is due to be tested by AEMT members and rolled-out from quarter 2, 2024. |
|
|
|
Pump maintenance – ignore it at your peril! | 07/12/2023 |
Thomas Marks looks at several issues that poor pump maintenance can lead to and outlines some of the key steps that can be taken to minimise the chance of them emerging FAILING TO adequately maintain industrial pumps can lead to various issues that can compromise the safety, efficiency, and longevity of the equipment and the wider systems the pumps are part of. One of the most immediate risks is the failure of the pump itself. Worn-out parts, clogged systems, or misalignments can cause a pump to break down, leading to potentially costly unplanned downtime. In addition, further unnecessary costs can be incurred when a poorly maintained pump consumes more energy to deliver the same output. Inadequate maintenance can also accelerate the wear and tear of pump components, leading to more frequent parts replacement and higher maintenance costs. And pumps that are not adequately maintained tend to have a shorter operational lifespan, leading to more frequent pump replacements. Frequent breakdowns, reduced efficiency, and the need for replacement parts can significantly increase operational costs. Leakages Worn-out seals or corroded parts can lead to leakages, resulting in the loss of valuable fluids, environmental contamination, and safety hazards. Without proper lubrication or cooling, pumps can overheat, damaging internal components and reducing their lifespan. Other issues, such as misalignment or imbalance, can cause excessive vibrations, damaging the pump and its supporting infrastructure. While cavitation, which can be a symptom of poor maintenance, can damage a pump's impeller and other components as vapour bubbles in the pumped liquid collapse, causing destructive shock waves. Of course, without regular cleaning, contaminants can enter the pump, affecting the quality of the fluid being pumped and potentially damaging the pump. Reputational damage Leakages, overheating, and equipment failures can pose safety risks to personnel working around the pumps. This can lead to accidents, injuries, or even fatalities. While leaks or spills due to poor maintenance can also lead to environmental contamination, which can result in regulatory penalties and damage to a company's reputation. And for companies that rely on pumps for critical operations, frequent breakdowns or safety incidents can also damage their reputation and customer trust. Indeed, in some industries, ensuring that equipment like pumps are adequately maintained is a regulatory requirement. Failure to comply can lead to financial penalties or legal actions. Good maintenance practices Regularly inspecting pumps for signs of wear, damage, or corrosion is essential. This helps in identifying potential issues before they escalate. Proper lubrication is also vital for the smooth operation of pumps. It's essential to use the correct type of lubricant and to ensure it is applied at the correct intervals. Regularly checking and replacing worn-out seals is crucial, as is ensuring that cooling systems are working efficiently to prevent overheating. Vibration analysis Vibration can indicate misalignment, imbalance, or other mechanical issues. Regularly monitoring and analysing vibrations can help with the early detection of problems. Ensuring that the pump and its motor are properly aligned is also essential to prevent wear and tear and to ensure efficient operation. As part of condition monitoring solutions, vibration sensors can now continuously monitor a pumping system to identify vibration-related issues as they emerge, and other types of sensors can track a pump's performance and help to identify problems like reduced flow or increased energy consumption. Systems such as these can also monitor the state of bearings to enable them to be replaced as soon as any performance issues are indicated. Ensuring the maintenance team is well-trained and updated with the latest maintenance practices is crucial. This ensures that they can identify and address issues promptly and are fully up to date with and following necessary safety protocols during maintenance activities to prevent accidents and injuries. Keeping detailed records of maintenance activities, parts replacements, and performance metrics can help plan future maintenance and identify recurring issues. While having a well-stocked inventory of essential spare parts, which can be informed by historical requirements, can reduce downtime in case of failures. And understanding the expected lifecycle of a pump and planning for eventual replacement or upgrades can help in budgeting and ensuring continuous operations. Industrial pump maintenance is a comprehensive process that involves a combination of regular checks, timely interventions, and proactive measures to ensure the longevity and efficient operation of the pumps. But it is essential, if the risks that can lead to wide-ranging consequences, from increased operational costs to safety hazards and environmental damage, are to be avoided and the smooth operation of industrial pumping systems is to be ensured. Thomas Marks is general manager at the Association for Electrical and Mechanical Trades (AEMT) |
|
|
|
Total cost of ownership guide | 22/08/2023 |
THE ASSOCIATION of Electrical and Mechanical Trades (AEMT) has published a new guide designed to help users calculate their industrial motors' total cost of ownership (TCO). With a focus on assisting organisations to reduce costs and improve their motors' environmental impact, the free guide can be downloaded from the AEMT website bit.ly/AEMT_TCO Despite a slight improvement in recent weeks, today's energy prices are more than double the pre-2021 historic average, and forecasts suggest they will remain so for some years to come. As a result, the lifetime cost of running an electric motor is an increasing focus for many users. However, we are still some way from a motor's TCO becoming a standard factor in most purchasing decisions. The purchase price of a typical industrial motor can be just 2% of its lifetime cost. So, to help end-users benefit from a greater focus on a motor's TCO, the AEMT's new guide outlines the variables which need to be considered when calculating the overall cost and offers recommendations for how it can be reduced. Areas covered in the guide include using variable speed drives, higher efficiency motors and improving motor reliability. Commenting on the AEMT's new guide for industrial motor users, Thomas Marks, the Association's secretary and general manager, said: "We have produced this guide to encourage a focus on the total cost of ownership of electric motors, to help users reduce their costs and improve their environmental impact. From initial system design right through a motor's operational life, there is a range of ways the total cost incurred can be optimised. "Our members are experts in advising motor users on the most efficient and effective solutions for their applications, and we want to highlight the positive impact users can have on their bottom lines and the environment." According to research from the World Energy Council, electric motors and electric motor-driven systems are estimated to account for almost 50% of all global electricity consumption. Alongside the potential for significant financial savings, if that consumption dropped by just 10%, that could reduce the global demand for electricity generation by 1,425TWh, equivalent to the total amount of electricity used by India, the world's third largest consumer. Focusing on a motor-driven system's TCO can help realise these benefits, and this new guide from the AEMT has been designed to support the process. |
|
|
|
AEMT Awards deadline approaching | 05/07/2023 |
TIME IS running out to prepare and submit nominations for the 2023 AEMT Awards Programme. With the final entry date set as 5.00pm on Friday 8th September, the AEMT again looks forward to recognising and rewarding business and professional excellence across the electrical and mechanical repair sector. Building on its past successes, the fifth outing of this sector specific awards scheme will culminate in a gala presentation ceremony to be held on the evening of Thursday, 23 November, at the Doubletree by Hilton Hotel in Coventry. The venue will also play host to the supporting AEMT Conference taking place throughout the day. The full programme is currently being finalised, but its focus will again be on providing AEMT members with help and guidance on a range of topics of primary interest to the development of their businesses. Staff recruitment, development and retention, the adoption of smart technologies, the commercial value associated with circular economy and sustainability initiatives, and the support networks that can be accessed by those operating in the sector will all be featured. The complement of speakers will share their knowledge and expertise in a series of talks and presentations specifically designed to be of tangible value and relevance to all those companies operating across the engineering service and maintenance arena. Industry-wide Engagement Operated by the AEMT and produced by Touchwave Media, the awards programme will again acknowledge the skill, effort, and dedication of the people and businesses serving this important industry sector. With sponsorship provided by a host of leading industry names, including ABB, DFA Media Group (publisher of Drives & Controls and Plant & Works Engineering magazines), EMIR Software, TEC Electric Motors, Megger, Sulzer, Menzel, and Preformed Windings, well deserved industry-wide recognition will be given to those businesses which are excelling in their commercial endeavours. Award Categories The seven categories that make up the 2023 awards programme are: Call for Nominations Entries are being sought for any company, product, application, or individual involved in the supply, installation, service, maintenance and repair of industrial machinery technology such as electric motors, drives, pumps, fans, gearboxes, generators, transformers, switchgear, and ancillary equipment. Individuals can put forward entries for themselves and their own company or nominate others that they believe merit recognition. The online entry process is quite straightforward, and anyone wishing to play their part in highlighting engineering excellence should visit the AEMT Awards website – www.aemtawards.com. Closing Date The closing date for all entries is 5.00 pm on Friday 8 September 2023, so those wanting industry-wide recognition for a job well done, be it for product innovation or project management, application knowledge, or service and repair, should be making a note of this key date. It is free of charge to enter the awards, but the promotional value associated with being selected as a finalist is worth many hundreds of pounds. But for those individuals and companies fortunate enough to be announced as one of the seven winners during the presentation ceremony, the promotional benefit is even greater. For further info call 07785 290034 or email [email protected] |
|
|
|
Navigating hazardous area safety requirements | 16/02/2023 |
PETER RAWLINSON looks at the key requirements you may come across concerning hazardous environments, what they cover and how they relate to each other Where safety and compliance in hazardous environments are concerned, there are a lot of acronyms relating to standards, directives, and regulations. To those unfamiliar with how the whole legislative landscape operates, it can easily and quickly become confusing. Before we get into specifics, it might be helpful to outline how different types of requirements compare briefly. - A Standard is a technical specification covering aspects such as dimensions, capacity, ratings etc. It is not a legal requirement but is widely considered best practice. - A Regulation in EU terms is a piece of law universally applicable to all EU member states. - An EU Directive is a legislative act outlining objectives that all EU member states must translate into their national legislation. - A Statutory Instrument is similar to an EU Directive and is the principal form in which delegated legislation is made in Great Britain. - Certification is the process of certifying that products, processes and people pass performance and quality assurance tests outlined in relevant standards and legislation. Compliance in hazardous areas The first acronym we will look at is IECEx, (International Electrotechnical Commission System for Certification to Standards Relating to Equipment for Use in Explosive Atmospheres). This aims to 'facilitate international trade in equipment and services for use in explosive atmospheres, while maintaining the required level of safety'. The IECEx system started as a product certification scheme but has since expanded to cover personnel certification offering competence training for people working in explosive atmospheres. IECEx has a broad global reach and is sometimes referred to as a passport scheme in so far as it is accepted by many countries prima facia, while some may accept it but require signing up to a local scheme. Indeed, the IEC scheme is the starting point for the development of the standards for EX equipment, and use. Because of its international scope, the Ex Repair training offered by the Association of Electrical and Mechanical Trades (AEMT) follows unit Ex 005 of the IECEx Recognised Training Provider Programme (RTPP), which focuses on the BS EN IEC 60079-19 standard on repair, overhaul and reclamation of Ex equipment, alongside the BS EN IEC 60034-23 standard “Rotating electrical machines - Part 23: Repair, overhaul and reclamation”. The ATEX directives are two EU directives describing the minimum safety requirements for workplaces and equipment used in explosive atmospheres, which must be applied in law by EU member states. There are, in fact, two directives. The ATEX 'equipment' Directive 2014/34/EU covers equipment and protective systems being used in potentially explosive areas. The ATEX ‘workplace' Directive 1999/92/EC covers the minimum health and safety measures that need to be in place to protect people working in hazardous areas. UKEX is a UK Statutory Instrument. This is a direct transposition of the ATEX equipment directive into UK law under the new post-Brexit regime. This is driven in the UK by the UKEX AB (Authorised Body) group. The members of this group are also ATEX and IECEx certification bodies. It is in their interest for there to be ongoing alignment between the directives, and so it is unlikely that there will be a divergence between UKEX and ATEX despite the pending Brexit Bill and its impact on UK legislation. DSEAR is also a UK Statutory Instrument and is a direct transposition of the ATEX workplace Directive into UK law. However, it also covers the requirements of the Chemical Agents Directive. So, in essence, as far as regulation of hazardous area equipment and environments is concerned, IECEx is the starting point that enables the ease of gaining ATEX and now UKEX. As such, if IECEx is amended, the amendments will automatically be adopted by the ATEX Directive and UKEX regulations by means of the acceptance of such amendments being “state of the art” for explosion protection. Finally, you may come across CSA, UL or FM certification. This is a broad system to ensure the safety of products used in North America, including Canada, whereby an OHSA or SCC-accredited Nationally Recognized Test Lab (NRTL) can certify that a product complies with specific North American safety standards. There are several standards which apply to hazardous areas under the North American system; for example, FM 3615, UL 1203, and CSA C22.2 No. 30 are the standards for Explosion-Proof Equipment, while UL 674 and CSA C22.2 No. 145 cover "Electric Motors and Generators for Use in Hazardous (Classified) Locations". Some N American explosion protection standards are harmonised with the IEC, ATEX and UKEX systems, and others are not. In addition, the North American system follows a different environment classification system. Competency in hazardous areas (CompEx) While not a mandated safety standard, CompEx, (Competency in Ex atmospheres) is an exam-based competency certification scheme set up in the aftermath of the Piper Alpha disaster. Developed initially for operatives in the oil and gas sector, the scheme now operates globally, covering all personnel operating in potentially explosive atmospheres. CompEx currently offers 13 qualifications spanning a range of roles and environments. Peter Rawlinson is a safety compliance expert and AEMT lecturer
Key Points
|
|
|
|
Can a repaired motor be more efficient? | 19/01/2023 |
THOMAS MARKS, general manager and secretary at the Association for Electrical and Mechanical Trades, looks at how a motor's efficiency can be improved as part of a repair or refurbishment and highlights some things you should consider. Against a backdrop of increasing energy costs, significant savings can be made by upgrading old motors to more efficient modern alternatives. However, simply swapping a motor for a modern equivalent is not always practical or even possible. Indeed, a study carried out jointly by the Association of Electrical & Mechanical Trades (AEMT) and the American Association, the Electrical Apparatus Service Association (EASA), has shown that motor efficiency can widely be maintained when a repair is carried out to a defined set of standards. The findings of the 2019 study, which have been published in a paper entitled ‘The Effect of Repair/Rewinding on Motor Efficiency’, established that efficiency was maintained on repairs to current machines up to IE3 efficiency. This guide has been incorporated into the latest international repair standard IEC 60034:23:2019 and the latest American ANSI/EASA standard, AR100. There are, however, some circumstances under which the efficiency of a motor can actually be improved by refurbishment and rewinding. This generally applies to older, less efficient motors and the decision to repair rather than replace typically involves a broader range of factors than simply to improve efficiency. Generally, the most effective way to improve a motor's efficiency is to add more copper to its coils. It is often possible to add more copper to a set of coils, or, more specifically, increase the copper cross-sectional area. This is achieved through the very tight tolerances modern coils can be manufactured to and the ability of state-of-the-art CAD systems to optimise coil design. This has several benefits, such as reducing the coil's resistance, increasing the potential output, and reducing the operating temperature of the machine, which can increase an asset's life. It is, however, important to understand that adding more copper will affect other characteristics in a motor which may require the wider system to be adapted. Adding more copper into a machine will affect not only efficiency but also other parameters. For example, an increased inrush-current – which might be in conflict with existing protective measures – should be expected. The ability to increase the amount of copper in a motor has been supported by advancements in insulation materials' which means that less insulation is required, and therefore space in the motors' slots becomes available. The thickness of insulation needed for various voltage systems has significantly decreased over the years, and modern insulation systems can offer 15% reductions in thickness. As this is on the outside of the coil, the effect on the copper cross-sectional area can be greater still. Furthermore, these thinner insulations assist with heat dissipation and can again offer both an increased asset life and improved efficiency of the coils. It is worth noting, however, that care is needed when comparing pre- and post-repair efficiency levels in a motor. Efficiency should not be compared simply by looking at a motor's datasheets. Before a 2007 update of the IEC / EN 60034-2-1 standard, which defines methods of determining a rotating machine's efficiency, efficiency figures were more generous due to how certain effects could be calculated out. Efficiency levels could previously be calculated with smaller additional losses than today – a standard 0.5% of absorbed power, regardless of the motor output. Since the 2007 update, the methods have become much stricter. Now stray load losses have to be determined by a factor that reflects the motor's output, ranging from 0.5% (≤1MW) to 2.5% (≥10MW). So, to avoid potentially misleading comparisons calculated from individual losses, efficiency should be measured directly at nominal load. The decision on whether to repair or replace a motor typically involves several factors. These can include cost, the availability of a suitable replacement, system compatibility and, of course, efficiency. So, while increased efficiency is possible in certain circumstances, it is not often the only reason to carry out a motor repair. If efficiency is one advantage you are looking for from your motor refurbishment, it may well be available, but you need to take care when calculating the actual benefits you are set to gain. |
|
|
|
Ensuring a quality motor repair | 22/09/2022 |
KARL METCALFE, technical support at the Association of Electrical and Mechanical Trades, explains what to look for when commissioning a motor repair. With growing financial and supply chain pressures, repairing a motor can be an increasingly viable alternative to replacement. But for a repaired motor to perform as well as, or in some cases better than, when it was new it is essential that you get a quality repair from your motor repair partner. There are several ways that a poor-quality motor repair can impact a business. Firstly, there could be issues with the energy efficiency of a badly repaired motor which can lead to unnecessary increases in costs. However, if repaired well, a motor should be at least as efficient as when it was new. This was demonstrated by a study carried out by the Association of Electrical and Mechanical Trades (AEMT) and the US-based Electrical Apparatus Service Association (EASA), which used independent testing facilities to confirm higher efficiency IE3 units are unaffected by a repair that uses good practice procedures. A motor that has not been well repaired can also be prone to failure earlier than expected. Winding faults can lead to premature insulation breakdown, while poorly fitted bearings can fail sooner than expected. If these unexpected faults occur, the cost of unintended downtime could be massive for some businesses. There are ways to identify a good quality repair, and this can start before the repairer even sets eyes on the motor. The repairer should take the time to understand what the client needs. They should talk to the customer to find out about the motor, where and how it is being used, and what the customer wants from the repair. When inspecting a repaired motor, generally, if the motor looks like it has been well treated on the outside, it is likely that it will have been well treated on the inside. For example, when the motor is returned, are the mounting faces free of paint? If they have been well masked when the motor was painted, the motor will be much easier to mount accurately. Equally, if the terminal box looks nice and clean and there are new nuts and washers on the terminals, that would be a sign that care has been taken. Other small but notable signs include the fitting of new grease nipple caps. They cost a few pence but can make a big difference. Also, look for mesh wrap or some form of protection on the shaft. While silica gel packs inside the terminal box and anti-corrosion coatings can make a difference, especially if the motor may not go straight into service and is in storage for any time. International repair standard One way to ensure a quality repair is to ask your provider if they follow the international repair standard (IEC 60034-23). The standard establishes the benchmarks for repairing rotating equipment, maintaining efficiency levels, high standards of quality control and improving efficiency in associated pieces of equipment. The standard covers many other aspects of the repair process. It sets out requirements for the maximum temperatures used in an oven to burn off old windings to prevent damage to the steel laminations. It covers which insulation grades should be used, the approach to rebuilding bearing seats, the selection of replacement bearings and grease, and a range of other factors. IEC60034-23 also sets out what tests should be carried out on a motor before and after it is repaired and how the test equipment should be maintained and calibrated. In line with the repair standard, a good motor repairer should have a repair specification they can give customers, showing what will be done. And when the motor comes back from repair, there should be an accurate record of what has been done, including certificates covering aspects such as balancing, vibration measurement, tolerances, and surge test results. So, to ensure you get levels of reliability and efficiency from your next motor repair, ask your repair provider if they work to the international repair, overhaul and reclamation of rotating equipment standard, IEC 60034-23. |
|
|