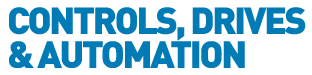
![]() |
Charlotte Stonestreet
Managing Editor |
Extending the value of automation & control
30 June 2020
As impressive as they are, the current wave of innovation centred around intelligent systems such as artificial intelligence, machine learning and edge computing, are not enough on their own, asserts Jason Chester
Automation has been the workhorse of manufacturing productivity and efficiency, probably as far back as when the Soho Manufactory in Soho, Birmingham, England pioneered mass production on the assembly line principle from 1766 and ever since then manufacturing has been locked in a cat and mouse game. This has been between the opportunities and competitiveness of the markets they serve versus the quest for faster, cheaper, better products produced in ever greater volumes.
Throughout that time, innovations in technologies and production methods have given rapid improvements in performance before those gains level off as they become mainstream. Think steam, electricity and the integrated circuit as those epochs in innovation, or more recently, vision systems, anomaly detection algorithms or robotics.
In the field of automation and control, the current wave of innovation is centred around intelligent systems such as artificial intelligence, machine learning and edge computing. By leveraging innovations in cloud computing, Industrial Internet-of-Things, embedded microprocessors, ubiquitous high-speed wireless communications and advanced algorithms, manufacturers continue to make great strides in increasing the volume of output from these automated environments.
The dimensions of cost, value & risk
Yet as impressive as they are, these innovations are not enough on their own. Manufacturers face increasingly challenging and competitive global markets. Consumer trends and demands continue to change at an ever-increasing pace, while volatility in supply and demand chains is causing increasing uncertainty and risk. Global logistics, online e-commerce channels and social media all tear up the rule book on competition. Throw into the mix major disruptions to markets and operations like Brexit (remember that?) and of course the global coronavirus pandemic, we then realise that automation alone isn’t going to cut it.
Instead, we need to look more holistically and apply the same level of innovation across the broader context of manufacturing operations by optimising those operations across the three dimensions of cost, value and risk. It is a fine balancing act and we can continue to reduce costs, but only up until a point where the quality of the product begins to decline beyond what the market will sustain, or that consumers will accept. On the flip side, we can continue to increase quality up until a point where the cost becomes uneconomical or uncompetitive in the market.
Then we have risk, the enemy of manufacturing. Risk can come in the form of operational risks - such as a machine failure or downtime, or more strategically such as a fast and dramatic shift in supply chain availability or consumer demand (as we have seen recently in spectacular fashion). Risk is inevitable and unavoidable but we must be able to mitigate the impact of those risks as much as possible without putting a strangle hold on operations. Optimising manufacturing operations by minimising risk while maximising value can only be achieved effectively when it envelops the whole of our manufacturing operations.
The true value of automation & control
So how can we extend the value of automation and control environments to drive greater levels of manufacturing optimisation? While automation and control has seen, and continues to see, great levels of innovation, it has two significant characteristics. The first is that they are data centric, with data collected by a myriad of sensors and processed locally through embedded microprocessors and programmable logic controllers. Logical, pre-programmed decisions are made automatically in order to control the process according to defined parameters and thresholds. Human operators then have supervisory monitoring and control via SCADA and HMI interfaces.
The second characteristic is that they are largely isolated like an archipelago. The production islands work on the task they are designed for and only that. The machines (governed by the data) operate within a closed loop ensuring that the rules are followed. It is far from uncommon to have production operators, supervisors or quality engineers regularly traverse the archipelago, taking a record of key parameters, settings and conditions. Likewise, they regularly take samples from the production line and perform either line-side, or lab-based, quality checks on characteristics that are critical to quality.
If these automated environments are icons of perfection, then why do we not trust them to produce perfectly good products all the time? Because despite the sophisticated nature of the automation, they are still occasionally unpredictable and subject to a broad source variability. This may be caused by equipment failure, calibration issues, wear and tear, failures in the application of logic, or variability in the inputs of raw materials or components, or even by good old operator error.
It is these supporting, yet vital, processes where innovation tends to lag far behind that of automation. Many of these checks and records are captured manually and recorded either on paper (yes, that is very common) or in some instances may benefit from being transcribed into an electronic master record, such as a spreadsheet. And then if you are lucky, some manufactures may endeavour to use that information for analysis purposes by producing reports and graphs to show trends over time or to try and understand why things are just not working out as they should. It’s a time and labour-intensive process.
Yet that information contains valuable insights into the operation and performance of our islands of automation and all of the actives that surround them. Creating an information-based architecture across our manufacturing operations provides us with a level of real-time operational visibility that gives us a holistic view of our production operations.
Data centralisation will be key to success
Capturing the critical data points from all of our automation systems, augmented with quality inspection data, lab check results, raw material checks, and other sources of fact, into a single centralised repository is a fundamental step. We can then begin to leverage those valuable operational insights to make faster, highly efficient, and more effective decisions. We can then discover causal inferences that help us fine tune our automation systems or identify sources of suboptimal performance.
Why is Line 1 producing more waste or defects on Product X vs Line 6 running product Y? Why do we have more yield on Shift B in Cell 3 than we do with Shift A on Cell 2? Why is Process C displaying more variation than Process F? Where do we need to focus our Continuous Improvement teams? Where do we need to prioritise equipment upgrades? The answers to these questions provide valuable opportunities for ongoing improvement that cannot be easily gained, if at all, from process-isolated data.
From physical automation to automated decision-making
As we have discussed, our main focus of automation has been physical automation. Minute-by-minute, hour-by-hour, day-by-day decision making is a major part of manufacturing operations, yet it is still a largely manual oriented process. Just as automation is great at taking on the task of performing rote physical tasks with far greater efficiency and accuracy, so technology is great at constantly monitoring a myriad of data streams and identifying trends or anomalies that require human intervention.
The real-time nature of an integrated information-centric environment makes our operations teams more productive. Instead of monitoring our automated systems in anticipation of anomalies or other issues, they can rely on a different kind of automation - decision automation. By extending the scope of factory innovation beyond just automation and control to the information and processes surrounding them, we can not only extend the value from our automation and control investments, but we can, perhaps, even multiply that value significantly. With that, in the continuous game of cat and mouse, maybe we replace the cat with a tiger!
Jason Chester is Director of Global Channel Programs, InfinityQS
Key Points
- No related articles listed