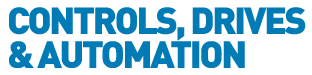
![]() |
Charlotte Stonestreet
Managing Editor |
Editor's Pick
Compressors in the cloud
02 December 2019
Automated air compressor energy saving tech is available, but is industry ready? Graham Coats looks at the issues
It’s no secret that one of the largest costs currently facing manufacturers is escalating energy prices. On a commercial level, manufacturers must keep costs down in order to keep profit margins up. From an environmental standpoint, wasted energy represents a wasted opportunity to address a plant’s sustainability levels, a pressure that is only likely to grow as society attempts to address another issue that is escalating, that of climate change.
Take the PET bottle blow-moulding sector, for example. It uses reciprocating air compressors, which, by today’s standards, are less sophisticated than what the modern day compressor is capable of offering.
Of course, there is a reason these compressors are the most widely used compressor to provide the 40 Bar of air required to blow bottles. Despite high costs associated with maintaining them, they are still the most effective compressor for the job. However, if the drive to improve on the status quo didn’t exist, we’d still be without mobile phones and using trains powered by steam.
Real time data
And this was behind CMC’s decision to launch Airmatics – a simple cloud-based air compressor monitoring, performance and control solution that provides real time data, analytics and insights at the push of a button.
The solution, which takes the very best elements of its predecessor, Metacentre, and incorporates Industry 4.0 capabilities to deliver a cloud-based performance and monitoring package, is not only pushing the boundaries of air compressor efficiencies (regardless of the compressor’s age and the sector it serves), but also providing a viable way in which to marry yesterday’s air compressor technology with the performance and monitoring technology of tomorrow.
Staying with the bottling sector, Princes Soft Drinks provides another good example. It was looking to reduce cost across seven of its large air compressors used for PET blow moulding, each of which require 2.275MWh of power per year. Following a feasibility study, which was carried out in partnership with Maziak Compressor Services, it was established that optimising its compressors by reducing the dramatic state change from on to off would deliver huge cost savings.
Having already achieved success with Britvic at its Beckton plant, where a previous generation of Airmatics made a net annual saving of 1,797,131kWh and cut carbon output by 772 tonnes, Princes commissioned an installation that would reduce the need to run unloaded air compressors whilst simultaneously enabling the compressors to operate in a tighter pressure band.
Now, situated in the plant room is a touchscreen that provides full oversight of the entire air compressor system – as a group and on an individual basis – at any given time. Feedback from the Princes team suggests that its installation has saved somewhere in the region of £80,000 a year, reducing the unit cost of each bottle produced. Furthermore, by ensuring that each compressor only runs when required, the service and maintenance costs associated with wear and tear have also decreased.
In keeping with the earlier train analogy, Airmatics has evolved even further to incorporate remote monitoring capability and a brand agnostic approach, so that any fixed or variable speed compressor, regardless of its age and manufacturer, can be added to a network and automatically controlled via Airmatics.
With a number of successful UK installations operational in other high profile bottling brands such as Britvic, Coca-Cola and RPC Promens, it’s worth questioning why all manufacturers - regardless of sector - aren’t adopting technology like this as a matter of course. After all, the benefits are clear and the operational savings compared with initial investment costs are substantial.
The good thing is that technology such as Airmatics isn’t solely reserved for bottling plants. It can benefit any plant in any sector that uses air compressors. Interestingly, when it comes to its application, the stumbling block is often the plant’s engineer’s unwillingness to adopt new technology and human nature’s desire to opt for a safe and familiar course, even if that course isn’t particularly effective.
The ability to save substantial amounts of money and improve environmental efficiency is now available to manufacturers that use air compressors, whether they produce bottles or build cars. However, in order to realise the benefits associated with the technology, manufacturers, as well as their support engineers and contractors, must be ready to embrace new technology.
Graham Coats is Sales Director at CMC
Key Points
- Airmatics is a cloud-based air compressor monitoring, performance and control solution that provides real time data
- Any fixed or variable speed compressor, regardless of age or manufacturer, can be added to a network and controlled via Airmatics
- By ensuring each compressor only runs when required, service and maintenance costs associated with wear and tear are decreased
- No related articles listed