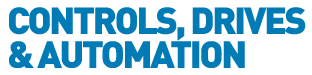
![]() |
Charlotte Stonestreet
Managing Editor |
Quality upgrade with unchanged application properties
29 June 2021
In the subminiature circular connector market, binder has a strong portfolio of high-quality products that are constantly being refined. By optimizing the manufacturing process of the 712 and 702 series in terms of quality and safety, binder is taking another step toward state-of-the-art customer needs.
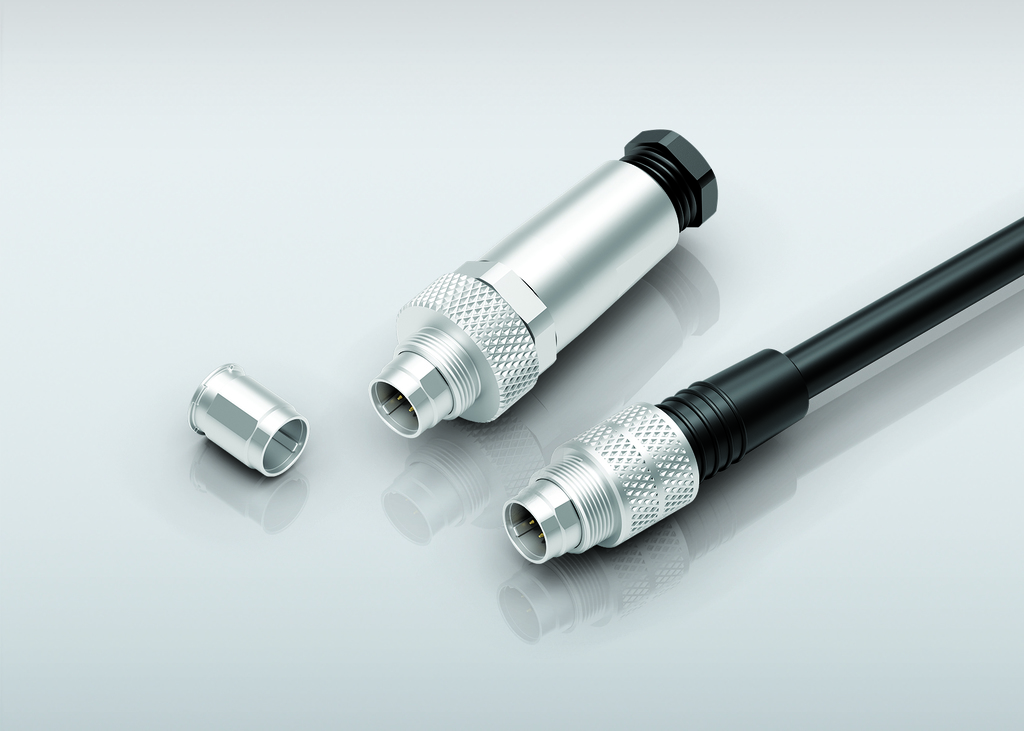
Converting from the currently available, M9 connectors with a drawn sleeve binder changes over to cast ones in the future. The conversion should be completed by the 4th quarter of 2021. The new die-cast sleeves improve the safety and quality features while leaving the application properties unchanged for our customers. The improved connectors are 1:1 compatible with the previous M9 IP67 subminiature circular connectors.
Increased safety seamlessly implemented
The product change has already taken off in the production department of binder and affects all connectors of the 712 and 702 series cable connectors and flange connectors from 2 to 5 pins. The M9 subminiature circular connectors are used in many application areas – from camera systems and pneumatic control systems to sensors.
In the current manufacturing process of these connectors a drawn tube was pressed into shape. This method is now being completely replaced by the new zinc die casting process. This process, which provides an increase in the safety and quality standards for 2-pin to 5-pin connectors, has proved successful for many years in the production of connector versions with 7 and 8 pins.
Optimized properties in the usual application scheme
Users of the 712 and 702 series circular connectors will benefit from this optimization and can rely on a die casting process that has been established for many years and which provides reliable properties in practice. The new manufacturing process brings many advantages, in particular in terms of engineering and dimensions. Even the safety during installation is improved.
So using these connectors in customer applications will remain the same. For current users of the M9 IP67 subminiature circular connectors, there are no changes because of the 1:1 compatibility. The greatest impact of this product improvement happens in the binder manufacturing department. This is created by the combination of the new material and the new manufacturing process of these connectors.
About binder
Franz Binder GmbH & Co. Elektrische Bauelemente KG is one of the market leaders in the area of circular connectors for automation technology. It is a traditional family-owned business, run by the owners, that still holds to its values.
Worldwide, binder has 1800 employees with 1000 of these located at the company headquarters in Neckarsulm. The binder group is comprised of the binder headquarters, 16 affiliated companies, two system service providers as well as an Innovation & Technology Centre.
- The right connectors for the IIoT
- Sensor connectors
- Binder products now available in EPLAN Data Portal
- Binder UK adds Genalog to UK distribution network
- Panel mount connectors
- Eight-pole angled receptacles
- Comprehensive corrosion protection
- High levels of EMC
- Single wire sealing
- The high pin count solution
- No related articles listed