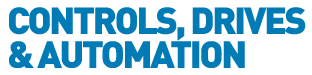
![]() |
Charlotte Stonestreet
Managing Editor |
Boulting joins MindSphere | 13/11/2018 |
---|---|
Leading industrial systems integrator, Boulting Technology has announced it has joined the MindSphere Partner Program, as Boulting continues to develop and deliver powerful applications and digital services to its growing client base. Developed by Europe’s largest industrial manufacturing company, Siemens’ MindSphere is a cloud-based, open IoT operating system that connects products, plants, systems and machines, enabling businesses to harness the wealth of data generated by the Internet of Things with advanced analytics. Using MindSphere, Boulting will work with its customers to develop powerful industrial applications, which are intended to optimise the entire value chain; from design, production planning and engineering to services. This in turn improve productivity and efficiency for individual machines, systems and globally connected plants. The software allows for immediate asset monitoring that can be configured quickly and efficiently. Once set up, users can locate connected assets at a glance on a geographical map, which is particularly beneficial for those operating multiple sites. “As the industrial sector continues to be transformed by IoT technologies, one of the biggest challenges plant managers are faced with is how quickly systems can connect, while remaining secure at all times,” said Nick Boughton, digital lead at Boulting Technology. “MindSphere helps us change this, dismantling the barriers surrounding industrial digital technologies (IDT) by allowing both Siemens and non-Siemens assets to connect, creating a direct and secure connection for data transmission. “With every piece of plant equipment providing a mountain of data, our partnership with Siemens will enable our customers to harness their own big data in a bid to improve operational efficiency in the plant. “Big data is not a new concept, however many manufacturers still fail to make the most of it. From collection to aggregation and analytics, we will be there every step of the way, advising on the best course of action to stay ahead of the competition.” Paul Kaeley, senior vice president, global partner ecosystem at Siemens PLM Software, added: “Boulting Technology is capable of delivering tremendous value to its client base through its vertically integrated solution. With Boulting as a partner in the MindSphere ecosystem, we can address operational challenges and support largescale business improvements using MindSphere. “Siemens is committed to creating partnerships that help customers realise the benefits of digital transformation with Industrial IoT. Working with Boulting Technology can help provide MindSphere applications that improve customers’ ability to get value from their currently unused, data.” The partnership with Siemens builds upon Boulting’s recent alliance with NETbuilder, a leading provider of software and IT consulting services, which allows Boulting to provide customers across manufacturing, process and other industries with a full suite of end-to-end digitalisation services. |
|
|
|
Retrofitting cyber security | 24/05/2018 |
In 1982, long before a cyber security threat to control system networks was widely recognised, a Trojan horse attack on control system software reportedly caused a huge explosion in a Siberian gas pipeline. Even now, many systems that have been retrofitted for compatibility with the IIoT are not well protected. Robin Whitehead, strategic projects director at Boulting Technology, explains the top considerations to ensure cyber security when retrofitting a system Connected devices have led to an increased value on data from real-time monitoring, as well as the creation of initiatives, such as the smart grid, digital oilfield and smart asset management in the water industry. However, these new technologies and applications have also led to a rise in potential security risks within a plant’s network. Because very few companies find themselves able to build a new facility from scratch, many plant managers and engineers are choosing to retrofit existing systems with smart sensors and communication packages to take full advantage of the benefits of IIoT. Many systems such as motor control centres (MCCs) and programmable logic controllers (PLCs) have an expected lifespan of decades and were originally designed to operate in isolation during a time of low cyber-attack risk. Connected devices can create vulnerabilities if substantial security systems aren’t in place. Threat Just one weak spot in a plant, such as an unprotected PLC can leave an entire network vulnerable to cyber-attack, especially as there are currently no regulations or clear rules about how these networks should be protected. Research agency Gartner estimates that more than 20 per cent of enterprise security attacks will involve the internet of things (IoT) connections by 2020 and it is safe to assume that many of these attacks will use weak points such as improperly secured MCCs and PLCs to gain network access. The Siberian pipeline attack is just one example of the devastating effects of control system vulnerabilities. Attack If a vulnerability is present, an insecure network can allow a threat such as a self-replicating worm to quickly become widespread throughout the facility. Legacy systems typically worked on closed, proprietary communication protocols and the migration to open protocols including TCP/IP means security flaws are likely to be found quickly and patched before potential attackers discover the risk. When connecting a legacy system to an open protocol security, patches can be vital in reducing potential cyber-attacks, however many manufacturers forgo their roll out due to high costs and concerns about potential downtime. Just one missed patch can make it impossible to ensure a legacy system is protected. Preventing vulnerabilities Retrofitting existing equipment is the ideal way for many plants to take advantage of IIoT, but care must be taken when implementing older technologies into networks. Continual risk assessments are essential to determine potential points of attack and take all connections into account, predicting the worst-case scenario of a security breach. Boulting Technology has a thorough understanding of industrial cybersecurity and works closely with partners to advise plants on the best way to improve cyber security for their unique network. For a few plants, a complete overhaul of network security may be necessary, for example updating a protocol to one with continued security patches. However, the majority of plants will find that installation of additional software, security patch updates or a top down study of network connections will be sufficient to bring cybersecurity to the necessary levels. Cyber security is an ongoing concern for any plant as the threat of cyberattack is growing year-on-year and is now significantly higher than during the Siberian pipeline attack in 1982. Additional care must be taken when integrating legacy systems into existing networks. |
|
|
|
Full OT/IT coverage | 18/04/2018 |
Industrial systems integrator, Boulting Technology, has announced a new alliance with NETbuilder, a leading provider of software and IT consulting services, enabling it to provide UK clients across manufacturing, process and other industries with a full suite of end-to-end digitalisation services. Boulting Technology, which has partnerships with leading industrial vendors including Siemens, Rockwell, ABB and Mitsubishi, has enjoyed a long working relationship with NETbuilder for fifteen years. NETbuilder’s partnerships include Microsoft, Amazon Web Services, Adobe, VMware, Veeam and other leading vendors. The evolution to a formal alliance is a natural progression for the two companies, which work towards the same goal of secure, integrated digitalisation in industrial environments across a variety of sectors. The alliance will offer customers a seamless solution by marrying information technology (IT) and operational technology (OT), which are traditionally managed separately. With investments in Industry 4.0 capabilities expected to reach 5 per cent of annual revenue by 2020, the management of IT/OT convergence will be imperative to ensure quality and secure data storage and usage. Boulting Technology, which continues to assist its clients in taking advantage of the Industrial Internet of Things (IIoT), understands the need for small and medium businesses to be able to purchase a complete, reliable, expert service. “The UK Government’s Made Smarter review revealed that the UK is behind most developed countries in overall manufacturing productivity, partly due to lower levels of adoption of digital and automation technology,” explained Ian Oliver, managing director of Boulting Technology. “The report speculated that this is partly due to a confusing landscape of business support and significant barriers to industrial digital technologies (IDT). Partnerships and alliances such as ours will allow more businesses to take advantage of these benefits, including increased productivity. “Our partnership with NETbuilder allows us to enhance our current offering and evolve to meet market needs. The new services that we will provide will greatly benefit customers looking to implement digitalisation techniques, taking advantage of the IIoT to improve efficiency and profitability.” “Industrial networks have traditionally been isolated,” added Dan Gregg, director of NETbuilder. “This collaboration with Boulting Technology will allow us to help bring clients up to date with cloud and digital technologies. “The technology used within industrial plants is quite different to the type of network most IT companies are used to working on, so experience of working on similar networks is essential. Although we have worked together on industrial projects for many years, the combination of NETbuilder and Boulting Technology’s experience will be extremely beneficial to our customers across the board.” |
|
|
|
New MD at systems integrator | 16/06/2016 |
Established systems integration expert, Boulting Technology, has appointed Ian Oliver as its new managing director to oversee operations at its four UK locations. Having worked at the organisation since 1999, Ian has clear objectives for the company. These include maintaining Boulting Technology as a market leader in the UK for the delivery of low voltage (LV) panels and control systems and growing the company's reputation as an employer of choice for experienced engineers. Previously the process control director of Boulting Group, Ian’s technical expertise lies in electrical control systems and system integration utilising off-the-shelf automation products. Furthermore, Ian specialises in the implementation of systems into live works; a skill that Boulting Technology has become known for in recent years.
|
|
|
|
Choosing the right critical power supply | 11/11/2015 |
The process of identifying the right critical power supply for individual applications is becoming exceedingly tricky. Pat McLaughlin, Boulting Technology’s Operations Director, discusses what companies should keep in mind when choosing a switchboard. Fault capacity & ruggedness Before commissioning a low voltage switchboard, consider what kind of external fault you can expect to have in the application. Usually this means choosing a fault rating higher than the maximum supply capacity. The rule of thumb is: fault rating = (transformer VA /700) * 20. This way, your system should be safe even in the event of an external fault. Another thing to consider is the product’s lifespan. Switchboards generally have relatively long lives and can last anywhere between 25 and 40 years, perhaps even more if you treat them right and ensure the regular maintenance they deserve. However, this also means they need to be rugged and durable, so they can withstand the occasional knock and abuse life throws their way. Location & security Industry has a tendency to leave the electrical room layout to the very end of the building design and adapt it to suit whatever space is left over. Try to avoid this approach if you can. Ideally, you want your electrical room to be spacious and well ventilated. If possible, there should be enough space to allow repair and replacement work to take place as smoothly as possible. Switchboards are only installed once, but there’s a good chance you will need to add cables or modules as time goes by. Devices may have shrunk, but the laws of physics and the size of cables haven’t changed. Access to your building’s power centre boards should only be granted to authorised personnel, rather than allowing just anyone to walk in and out. Ideally, the switchboard should be located in a secured room, out of the way, so visitors don’t just stumble in while looking for the rest rooms. In addition, electrical gear is a tempting target for thieves, so it’s important to protect it accordingly from malicious attacks or vandalism. Futureproofing Because of their long lifespan, switchboards should be designed to last a few decades. One way of future proofing a low voltage assembly is by using a modular design. There’s a chance that as you grow, you will require more capacity. You can easily achieve this by putting a bus coupler on the end, so you can extend and modify the switchboard without shutdown. Modularity also means that if a section of the power centre breaks down it can be easily replaced without having to turn off the whole thing. Speaking of growth, another thing you might need if you want your switchboard to be future proof is a few spare distribution and motor control feeders. They might add to the final cost, but they might also be a lifesaver a few years down the line. You can’t predict the future, but you can make it easier for those who follow you. Keeping it simple To make sure sources can’t be cross-connected, even if the electrical control fails, all the switches should be mechanically interlocked. Interlocking switchgear ensures personnel are safe and equipment is operated according to the correct procedures. Labelling in large switchboards can be very confusing, so colour coding is a good way of keeping track of supplies. Sometimes special symbols can also be used for multiple sources of supply, but colour coding is the simplest and best method. It offers an ‘at a glance’ view of the system and minimises the risks of mistakes. Very few switchboards these days will operate critical processes manually, so remote signalling and switching is something you should consider when choosing a switchboard. It’s important to make sure that if the main power goes down in the middle of the night, or over the weekend, the generator needs to be on and fully functional. Testing Speaking of generators, you need to ensure that you test them regularly using a load bank. You should design the switchboard in such a way that testing is easy; otherwise excuses will appear and testing will be delayed. Make sure this doesn’t happen and you won’t be left in the dark when the power goes out. Switchboards need constant attention to always be at the top of their game. |
|
|