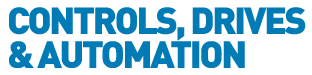
![]() |
Charlotte Stonestreet
Managing Editor |
Data – the heart of any Industry 4.0 operation
17 April 2019
Data is pivotal to any Industry 4.0 operation; data which comes from sensors. So it stands to reason that for a sensor specialist like SICK, Industry 4.0 in going to be at the heart of operations, not just in terms of the product that the company develops and makes available to the market, but also in its own production facilities.
At Sick recent global press event, senior vice president Industry 4.0, Bernhard Müller put this into context. “Everything that we do today has to do with sensors; it’s always from the perspective of a sensor manufacturer,” he said. “And we have the opportunity to look at it from two sides: one side is knowing what sensors are used for, what they do and what they have the potential to do, and on the other we also produce our own sensors, we have production lines where we can use the sensors ourselves.”
Taking the idea of ‘batch size one’ as a starting point Müller examined how sensors and Industry 4.0 are a perfect fit, so much so that’s it’s difficult to see how Industry 4.0 would be possible without today’s intelligent sensors.
“Knowing how the world is changing, we have to have a faster reaction time,” said Müller. “Everybody wants everything immediately, they don’t want to wait any more, they want it now and not tomorrow. And they don’t want a standard product, but an individual product that is exactly as they want it.”
Of course, Müller asserts, this means a high degree of flexibility is vital. In a connected operation, high transparency can help improve manufacturing lines, working towards not just achieving batch size one, but achieving batch size one at a competitive price.
Central to realising this model is efficiency. Eliminating waste, in terms of energy and materials, in production is paramount.
“Then there is the quality question,” said Müller. “Nobody wants to throw away anything that they have produced.”
Predictive maintenance, machine availability, human/robot collaboration, resource optimisation, track and trace, and robot guidance are all activities identified by Müller, which are supported by sensors, that can help make batch size one production achievable at a competitive price.
Suitable sensors are available for a large number of standardised applications, but there is increasing demand for customised products in response to the growing need for individual solutions. Now Sick is going even further in the direction of Industry 4.0 with its first sensor solution that operates on the basis of deep learning algorithms.
SICK uses the new deep learning technology in the industrial environment to specialise the functionality of its sensors. Here, the sensor learns to process information and thus develops new functions. New processes are also possible on the basis of adapted sensors; the sensor supplies, processes and analyses data using self-learning algorithms.
In one sensor solution, for example, sensors are trained with a large number of images to give an answer to a specific question. On the basis of this training, the sensor can then independently assign new unknown images to a result. “We are currently working with deep learning on a pilot project in the lumber industry, for example. The basis of our solution is a camera with deep learning functionality,” explained Müller.
In order to ensure optimum use of the raw lumber material, sawmills must know about the conditions in the logs: Where are the age rings? Where is the core? This is necessary to ensure good processing of the lumber.
“In order to find out how the lumber can be used best, we taught the camera this by means of deep learning. This task could previously be performed only by humans,” added Müller.
This technology makes it possible to realise new, previously inconceivable applications that make processes more efficient and more productive.
“In our pilot project, we were able to increase the material utilisation, improve the quality of the products and avoid wasting resources,” continued Müller. And sustainable use is possible not just with materials; employees no longer have to perform monotonous activities and are free for more complex tasks.
Indoor localisation
SICK is also taking another step toward Industry 4.0 by offering a new, comprehensive indoor localisation portfolio. Thanks to coordinated sensors and analysis tools, large amounts of data can now be evaluated purposefully and fields of action can be displayed in factory processes or logistics. This makes it possible to manage complex logistics networks, create transparency and ensure speedy deliveries. This portfolio makes SICK the first manufacturer to offer a comprehensive range of solutions along the entire value creation change from a single source.
With the growing need for flexibility and speed rigid continuous conveyors are being added to existing logistics solutions to support moving industrial trucks and other mobile resources. Going forward, the supply chain will more prominently feature a combination of automated and manual processes, more complicated logistics networks that require efficient management. Transparency beyond the limits of individual systems is required here more than ever; for conveying systems, for forklifts, for moving pallets in the warehouse or at the nearest handling depot—throughout the entire supply chain.
With has many years of experience SICK is recognised as a market leader in the area of object tracking on conveying systems. Read rates for barcodes or RFID at stationary read locations determine the performance of the system and are the core of many logistics systems. Whether the application involves camera, laser or RFID technology, SICK offers the perfect high-performance solutions.
The goal is always to ensure the efficient use of all necessary transport and loading equipment and management of the entire supply chain, known as “asset management.” However, once goods leave the conveying system, the location of each object can often be unclear.
Logistics assets can be tracked continuously using localisation solutions—known as indoor GPS—and their space-time coordinates can be continuously recorded and stored. Having this data means complete transparency about all the important movements on the shop floor. Today's analytics tools can already use this data to make connections between different events, presenting an unfiltered look into actual factory or logistics processes.
All the established technologies—ultra wide-band tags, LIDAR Contour Mapping, line guidance sensors, infrastructure sensors—record either their own position or the position of the desired objects. Depending on the application as well as the positioning accuracy and update rate required, the right technology is selected or various technologies are combined with each other. SICK is the first manufacturer to offer all technologies for individual customer applications. SICK can cover the entire solution scope from sensors to the cloud-hosted smart data service.
Localisation technology is one of the key factors in achieving the type of networked production and logistics needed for Industry 4.0. It can be used to boost optimisation potential in several areas by allowing for agile planning of production and logistics processes. Localisation data gives companies a high level of transparency and understanding of all production-related assets, load carriers and loading equipment.
As a result ravel paths can be optimised and adapted dynamically and setup times prepared or scheduled flexibly. The material flow can be planned and controlled based on consumption. All of this boosts delivery quality and on-time delivery.
Easy sensor integration
The latest members of the SICK Sensor Integration Machine product family - SIM1004 and SIM1012 - collect and aggregate data for individual solutions and integrate them in Industry 4.0 processes. The development of sensor apps within the SICK AppSpace eco-system offers benefits for logistics and factory automation in the areas of quality control, process analysis and predictive maintenance.
With SICK AppSpace and the programmable sensors, SICK provides users with a powerful tool for edge computing solutions. The new Sensor Integration Machines SIM1004 and SIM1012 now combine intelligent sensors into powerful multi-sensor systems. The extend and scale the SICK SIM product family portfolio in terms of processing power and number of sensor connections. In the SIM1004 basic model, four connections allow combined data processing from 2 cameras or a laser scanner, for example. With correspondingly higher scaling, the SIM1012 has twelve connections for the next level of complexity. Both variants are equipped with Ethernet interfaces with OPC-UA and MQTT communication protocols and make the processed data available using edge computing. This permits intelligent data networking for digital factories.
SICK sensor engineering allows connection of practically any sensor type when using SIM1004 and SIM1012. Sensor data can be merged into a point cloud, evaluated, archived, and transmitted. This opens up completely new application possibilities and with them enormous creative potential. This in turn permits realisation of completely new solutions in mechanical engineering and for integrators.
The customised multi-sensor integration can be made available as a sensor app in the SICK AppPool and thus reduces additional development effort thanks to the high global reusability of the sensor apps on all programmable devices from SICK.
Intelligent safety system
Sick’s Safe EFI-pro system from is an innovative, intelligent safety system for automated guided vehicles (AGVs) and collaborative robots (cobots). It combines safe sensor and control technology with open Ethernet network technology. This allows realisation of application-specific safety concepts for AGVs and cobots that also improve their performance and productivity at the same time.
The Safe EFI-pro system sensors monitor the working environment, while the integrated safety controller activates the appropriate safety functions depending on the situation. The standardised network technology of the Safe EFI-pro system minimises cabling between components. It also guarantees simple integration of the safety system into the control environment of AGVs and cobots.
In addition, the EFI-pro interface based on EtherNet/IP-CIP Safety offers optimum connectivity: it permits exchange of safe and non-safe process and diagnostic data across all machine communication levels. In the environment of Industry 4.0 and Industrial Internet of Things (IIoT), the safety system therefore offers all the prerequisites for seamless integration of AGVs and cobots in autonomous production and logistics applications.
- Achieve more with mobile robots using SICK modular sensor solutions
- Rugged safety light curtain
- Get Your 15 Minutes
- Smart sensor technologies
- Flat out for sub-miniature performance
- 2nd generation smart motor sensors
- Keeping safety in the loop
- Compressed air energy monitoring
- Temperature Transmitters For Liquids & Gases
- Fast track to 3D vision
- No related articles listed