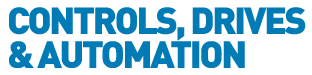
![]() |
Charlotte Stonestreet
Managing Editor |
Editor's Pick
Full Sail Brewing taps manufacturing intelligence
16 December 2019
America's thirst for craft beers is growing. In fact, the craft-brewing industry grew by nine percent in volume in the first half of 2009, while overall U.S. beer sales dropped by 2.7 percent. Full Sail Brewing Company is at the forefront of this growth. The Oregon based brewery produces three core varieties of craft beer, along with a number of seasonal and specialty brews.
Taking malt, hops and yeast from surrounding local sources in Oregon, Washington and Idaho, Full Sail brews the ingredients with water that originates from a deep granite well on Mount Hood. The results are beers with a signature taste – and a small environmental footprint.
Full Sail is a top-25 beer producer in the U.S. by volume, but the company is focused more on creating a beer that ranks high in terms of taste and quality. The company is also committed to its culture as an employee owned enterprise, which values work-life balance.
That work-life balance – and the company's efficiency and potential profi tability – were being hampered by its traditional brewing process. Like nearly all craft brewers, Full Sail used a manual brewing vessel, called a lauter tun, to filter the slushy “mash” of water and crushed grain that forms the foundation of beer.
Mash filtration
Mash filtration is a core element of the beer-brewing process. After barley grains have been malted and milled, the milled grain and hot water are mixed to create a cereal mash. The mash is held at a constant temperature to allow starches released into the mash from the malt to be converted into sugars that can be fermented.
The malt sugar-rich water, now known as wort, is then separated from the leftover spent grain husk. After separation, the wort is pumped into the brew kettle for boiling. Hops are added during the boil to create the bitterness and aroma of a particular brew, balancing the sweetness of the malt sugars. The wort is then chilled and blended with yeast and sent to fermenting, conditioning and filtration before it is packaged and shipped.
This classic system had served the company well. From 2005 to 2010, Full Sail increased production by more than 15% annually. However, the company realised that not only would future production demands strain their manual mash filtration system, efforts to increase efficiency, cut costs, and further improve quality were limited under the existing system.
The mash filtration system at Full Sail required continuous manual data-testing and reporting. In addition, the lauter tun spent grain – a byproduct the company sold as livestock feed – contained 82% moisture content. That meant valuable liquid was going out the door with the byproduct. At the same time, transporting the heavy waste was expensive. The company was losing money on the transaction, essentially paying farmers to take the spent grain off their hands.
Full Sail considered upgrading to a fully computerised brewing system, popular among many large U.S. beer producers. However, in order to see a return on the investment (ROI), Full Sail would need to operate this system 24/7, and the employee-owned company was unwilling to compromise its culture and employees' work-life balance.
The goal at Full Sail was to upgrade the process to improve product quality, increase filtration efficiency, capacity and throughput. The company wanted to minimise operator dependency through automation, create a scalable solution and decrease the overall environmental impact of each brew, all while retaining its 4/10 (four days a week, ten hours a day) work schedule for an attractive work-life balance.
To achieve these goals, Full Sail decided to upgrade its traditional, manual lauter tun to a fully automated, networked mash filtration system.
Full Sail brought in Aurora Industrial Automation out of Portland, Ore. to design and implement the new system. An Information Solution Provider within the Rockwell Automation PartnerNetwork program, Aurora implemented a control and information solution that would enable Full Sail to apply a manufacturing intelligence strategy across its operations.
The new mash filtration system leverages the PlantPAx Process Automation System from Rockwell Automation. As part of the PlantPAx system, Aurora incorporated the PlantPAx Logix Batch and Sequence Manager (LBSM).
LBSM is compliant with the ISA-S88 set of standards and terminology for batch control. The system allows Full Sail to configure sequences directly into the Allen-Bradley ControlLogix controller through the FactoryTalk View human-machine interface software without the need for a server-based batch software application.
If at any point batch requirements grow, Full Sail can easily migrate the LBSM into a comprehensive software solution, like FactoryTalk Batch, without costly re-engineering and testing.
Manufacturing intelligence strategy
To gain insight into the new system, Aurora implemented a manufacturing intelligence strategy based on FactoryTalk software from Rockwell Automation.
Through an EtherNet/IP network, FactoryTalk Historian identifies and gathers data tags directly from the PlantPAx system for real-time, granular production data. With more than 60 steps in the filtration process, the mash filter produces copious amounts of data.
With the old system, Full Sail was only grabbing four to five data points from each brew in the lauter tun. The new mash filter – enabled with FactoryTalk software – can now pull up to 250 data tags.
Full Sail then uses FactoryTalk VantagePoint software to aggregate this data goldmine into predetermined dashboards. The dashboards provide role-appropriate, real-time key performance indicators – manufacturing intelligence – Full Sail can use to improve operations.
Moving to an information-enabled, automated mash process immediately produced results.
Real-time data is now retrievable over variable time spans, helps achieve optimum functionality of the system and catches discrepancies or problems that may have occurred during a batch.
Reporting and dashboard software can immediately draw from the new historian as well as legacy systems to create a virtual, homogeneous data source for reporting. Information from single specialty batches to larger trends can be immediately accessed to guide future brews. If a brew were to experience a serious problem, the exact metrics for that brew could be traced and analysed.
“We make about 20 varieties of beer,” said James Emmerson, Full Sail executive brewmaster. “Now brewers of each batch benefit from the information available from the previous brew, whether a variety was brewed yesterday or last year. The brewers can now go back and see the exact metrics that produced a successful batch and optimise the new brew based on that information.”
With the new PlantPAx system, brewing capacity has increased by 25 percent, plus the time of each brew cycle has been cut by almost half. The visibility operators now have into their brew process allows them to optimise ongoing brews in real time. Full Sail has already used this insight to cut raw material costs by five percent annually.
The company has been able to remove significantly more moisture from the spent barley grain and the byproduct is now sold at a profit.
Additionally, Full Sail estimates it will decrease water use by one million gallons annually helping to augment its sustainability goals.
A million gallons of water will not be paid for, piped, pumped, heated and cooled in the new system. The environmental effect of not using the water in the first place is invaluable.
Key Points
- Full Sail wanted to minimise operator dependency through automation, create a scalable solution and decrease environmental impact
- Aurora implemented a control and information solution enabling a manufacturing intelligence strategy across operations
- Real-time data is now retrievable over variable time spans and helps achieve optimum functionality of the system
- Rockwell & US Embassy host summit on business value of I4.0
- Advanced light curtain system improves flexibility & safety
- Unlocking the potential of modular enclosure systems
- New state of smart manufacturing study
- Rockwell launches new open architecture industrial computers & thin clients
- Wiring & Enclosure Size Cut
- Micro PLCs Optimise StandAlone Performance & Cost
- Stay ahead of the curve with Rockwell Automation's CUBIC modular enclosures
- Rockwell opens EV innovation centre in Silicon Valley
- Rockwell Automation acquires Odos Imaging
- No related articles listed