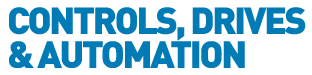
![]() |
Charlotte Stonestreet
Managing Editor |
Packaging with planetary precision
15 January 2020
As a consumer, it’s easy to overlook the feat of automation that packaging represents — it’s the product of thousands of components and calculations designed to deliver repeatable precision. Stephen Hayes explores how precision is assured in packaging.
It's rather easy to anecdotally say that packaging is one of the biggest industries in the world. Whether it’s to keep food fresh or to protect delicate electronic devices, packaging is common in everyday life. To assign a figure to it, research group McKinsey & Company noted in May 2019 that packaging solutions is a $900 billion market.
Not only does this show the size of the market, but also the stakes for packaging businesses and processes. For a packaging business, production is constant and output targets are high. Everything must be manufactured and finished rapidly, with clear uniformity in every product. Any deviations are unacceptable.
For packaging operations in industry segments such as food manufacturing, the pressure is equally high. Food products need to be packed promptly to ensure quality and maximise freshness, especially of quickly perishable products such as meats and dairy.
To ensure speed and precision in packaging, machinery manufacturers rely on servo motors that are coupled with a gear unit. However, not all these components are built equal. Careful consideration of the servo motor, the gear unit and the compatibility between the two is required to deliver the results necessary.
The right gear unit
Fundamentally, an effective packaging machine needs to be able to move at a consistent rate, with precise positioning and repeatability. Of course, the speed is controlled by the motor primarily, but it is heavily influenced by the weight of any load on the machine. For example, the speed of a bottling machine would be relative to the rpm of the servo motor and the total weight of the bottles passing through it.
Here, the torque of the gear unit must be considered. The torque of the gear unit affects the speed at which the servo motor runs, making it possible for the motor to run at much steadier speeds without significantly increasing motor size or weight. This is one of the advantages for packaging machines, where lower speeds can be assured in relatively compact footprints by selecting the right gear unit — often planetary gears.
Also known as epicyclic gears, planetary gears comprise a number of various sized gears — referred to as planets — that rotate around a central gear, known as the solar gear. This is all contained within an outer ring gear, or annulus.
The compact design of planetary gears means that they can provide a higher power density than typical gearing systems, as well as over 95 per cent efficiency and increased stability. Depending on the number of planets in the system, the torque density of the gear trains is relatively high as the load is shared between each planet.
Compatibility
However, it’s not as simple as simply choosing an ideal gear unit for a packaging servo motor. To ensure optimum performance, the servo gear unit and the motor must be compatible. This is a problem encountered by many packaging machine manufacturers that source motors and gear units from various suppliers, which can cause problems if they are not effectively mated.
At Beckhoff Automation UK, each of our planetary gear units are designed to be perfectly compatible with our wide range of servo motors. For example, our AG2800 planetary gear units, which offer up to 200 Nm of maximum acceleration torque and a maximum of 15 arcminutes of torsional backlash, are designed to be perfectly mated with the AM8800 family of servo motors for packaging applications.
This compatibility is key to motor and gearbox deployment in applications that demand high levels of precision and reliability. It can seem to be a high stakes decision, but engineers do not need to risk guessing or devote countless hours to intensive research.
Beckhoff Automation offers a motion designer software tool that engineers can enter their application data into, which not only identifies the suitability of motor and gear units but also the power requirements and other factors influencing how achievable a proposed application is.
In addition, Beckhoff offers a complimentary mating service to ensure that gear units and motors are ideally set up for success, with manufacturers able to specify the orientation of the mating. This also includes ensuring correct torque levels of clamps, correct sequence of tightening and threadlocking of the mating screws.
Not only does this ensure proper setup, but it reduces time for manufacturers in fitting the motor and gear unit to its location.
In an industry that prides itself on precision and accuracy, the correct selection of motion components is vital, and so too is the proper setup. With the right gearing unit and a compatible servo motor, packaging machines can continue to deliver the performance needed in an ever-growing, and always important, industry.
Stephen Hayes is managing director of precision automation expert Beckhoff Automation UK
Key Points
- Control network connection
- ‘Plug & Work’ bus terminals
- Ultra-compact IPC
- Beckhoff joins AMHSA
- Beckhoff helps develop CoroVent ventilator
- Revolutionary linear transport system
- New automation technologies
- Multi-touch functionality & high-end computing power
- Bridging the protocol divide
- Many-core machine control
- No related articles listed