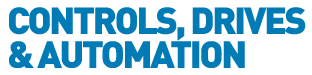
![]() |
Charlotte Stonestreet
Managing Editor |
1/4 (1 to 10 of 34)
Automating UK supply chain from the top down | 26/08/2025 |
---|---|
A collaborative, multi-tier approach is vital for overcoming challenges in automation adoption asserts BARA chair, Oliver Selby UK MANUFACTURING needs to bolster its domestic automation systems integration (SI) supplier base. Key to this is the formation of strategic partnerships between large corporations and the small and medium-sized enterprises (SMEs) within their supply chain. Large manufacturers also need to engage with SMEs within their component parts tier supply chain and push them towards automation solutions to boost their competitivity against imports. This collaborative, multi-tier approach is vital for overcoming existing challenges in automation adoption such as skills availability, a lack of commitment to invest and a lack of general ambition for advanced manufacturing. Large corporations and SMEs: a symbiotic relationship Encouraging large corporations to work with and mentor local SME tier suppliers’ partners could be a powerful catalyst for growth. Large corporations often possess substantial financial resources, market reach and established infrastructure. However, they can sometimes lack the agility, specialised niche expertise and innovative spark that characterises many SMEs. Conversely, SMEs, while innovative and nimble, frequently struggle with funding, scalability and market access. Partnerships between the two offer mutual benefits that strengthen the UK automation sector. For corporations, SMEs provide cutting-edge, bespoke solutions without the internal heavy R&D burden. Collaborating locally also enhances supply chain resilience, reduces dependency on global suppliers and supports efficiency through flexible, cost-effective solutions. Joint projects foster knowledge transfer, as larger firms share expertise in project management, quality control and scaling. Moreover, supporting SMEs aligns with Corporate Social Responsibility, boosting local economies and skills development. For SMEs, these collaborations could unlock access to capital, resources and advanced equipment, along with much-needed access to projects. Mentorship from established firms accelerates their growth and capabilities, while association with reputable corporations builds credibility and wider market access. Partnerships also spread project risk and encourage innovation by pushing SMEs to deliver more sophisticated and larger solutions. Help from Automate UK Work done over recent years by trade associations like Automate UK to accelerate automation adoption by acting as advocates and knowledge hubs has paid dividends. Through lobbying government for a robust industrial strategy, automation now forms part of multiple key pillars. We hope as an organisation this engagement will lead to tax incentives for SMEs, R&D and adoption grants, and multi-faceted workforce investment. Automate UK has also made new membership types available to different stakeholders – for example, manufacturing end-users of automation and education providers – to strengthen the ecosystem needed for partnerships to flourish. Government support However, challenges must be tackled for partnerships to thrive. Investment hesitancy will only be overcome by stronger government incentives, tax allowances and successful case studies. The skills gap demands more apprenticeships, vocational training and industry-led content in academic programmes. Risk perception can be reduced through best practice sharing and case studies of corporate success stories. By strategically fostering partnerships, the UK can create a dynamic ecosystem where large corporations and innovative SMEs collectively drive the development and delivery of advanced automation systems, leading to substantial productivity gains and a robust industrial future. For more information about partnerships and supply chain development, contact Automate UK via the website below or or join us at our conference in November. |
|
|
|
Risk mitigation | 18/06/2025 |
As with any capital expenditure purchase, risk needs to be carefully managed when investing in automation; BARA chair, Oliver Selby examines four key factors 1. Financial risk This presents itself in two ways: firstly, the internal risk of capital outlay for the business; and secondly, the risk of working within supply chains generally formed of SMEs. Capital outlay risk can take the form of either depletion of cash reserves or cash flow. This can be managed by weighing up expenditure and analysing the best form of finance for the project. More firms are moving away from fully financing a project themselves and are instead focusing on lease arrangements, thereby making automation an operational cost. This can certainly lower risk, offering a fall-back option should the project not meet expectations, or if you have shorter term customer contracts. Supply chain risk can be managed through contractual terms, for example staged payments for when a supplier hits certain performance metric such as design, procurement, build, or acceptance testing. Additional methods can also be considered, e.g. liquidated damages and bank guarantees. 2. Technical risk This is this easiest risk area to mitigate, as process risks are generally covered by the integration partner or process solution provider. Most system integration partners will provide upfront proof of concept support for anything that: - Sits outside of normal known process risks - Represents a new process - Constitutes a combination of processes that rely on each other. Once the process risks are removed, a full User Requirement Specification is normally issued, which enables the integration partners to provide a quote. At this point, potential suppliers may simulate the process to prove cycle time and throughput, allowing some confidence in future OEE calculations. The final chosen solution partner should also demonstrate capacity and competence in the solution being offered. 3. External risk Anything external to your or your supplier’s ability to deliver the project on time and to the quoted price should be reviewed prior to commitment. Currently, the geopolitical challenges impacting tariffs and global supply chains have caused a few headaches, as have domestic changes to UK Government policy, such as National Insurance payments. These all affect decision making, and should be considered from both a short and long term perspective. 4. Human factors Managing employee risk can be critical to an automation project’s overall success and may also improve buy-in from the workforce in the longer term. Getting support from suppliers, trade associations and other manufacturers can help firms to introduce automation in a manageable way. Early education and involvement of key stakeholders within the organisation around the ‘why’ and ‘how’ surrounding an automation project can also help to minimise future challenges. Remember, no-one knows your processes or products like those currently making them. Make use of that knowledge! The most influential area when it comes to mitigating automation risk is communication. Talk internally with key stakeholders to define the financial risks, technical risks, external risks and human risks that will undoubtedly present themselves as part of the decision-making process. Talk externally to suppliers, trade associations and other firms who have automated. And finally, consider talking to third party consultants, who can bring experience and expertise to your automation investment plan. Talk to Automate UK about how they can point you in the right direction with accredited suppliers and consultants to reduce your investment risk. |
|
|
|
Why supply chain development is critical to automation adoption | 06/05/2025 |
With global competition being heightened due to tariffs and trade wars, it’s now more important than ever that UK manufacturers and their supply chains work together to gain a competitive advantage, asserts BARA Chair, Oilver Selby OVER RECENT months, I have spoken to numerous manufacturers and suppliers at events including the MAKE UK National Conference and the PPMA Conference. In contrast to what’s being said in the general media, I felt an air of optimism for 2025 and beyond. My roles as Head of Sales at FANUC UK and BARA Chair allow me access to data around both UK and global automation adoption rates and, whilst we are undoubtedly behind the global average, I believe the UK is poised for a surge in automation adoption – but only if the right environment can be created by the current government. Stability for investment Discussions around the UK Industrial Strategy at the MAKE UK Conference confirmed that what British manufacturers need is more stability in order to start investing in capital equipment. Following the Spring Statement and changes to policy from 1 April, they are now beginning to do so. At another recent event, held in the northeast with ten automation companies, attendees were clear that better collaboration is also needed between supply chains and end customer manufacturers. More projects would be won by UK automation suppliers if they knew who could support them within the domestic supply chain in regard to equipment or services outside of their own capability. This is one of the key aspects that Automate UK and BARA will be focusing on at Automation UK on 7-8 May at the CBS Arena in Coventry. Manufacturer engagement in developing their supply chain will be crucial to ensuring the right application and process skills are being developed by automation suppliers; whether in automotive, food, aerospace, or warehousing and logistics. Each sector requires different skills and knowledge, and has a different risk appetite, both technically and financially. Better understanding The elements of a project where an automation supplier may benefit from support from the end manufacturer include specific process knowledge, regulatory guidance (particularly in medical/food/ATEX applications), as well as working together to find solutions to financial challenges (eg cash flow). It’s not uncommon for procurement/purchasing departments to take over final negotiations, which can make it difficult for suppliers to plan for longer term engagement and future projects with a business. After all, the most suitable long-term supplier may not necessarily be the cheapest, or offer the quickest delivery time. However, a supplier developed alongside your business needs will better understand you and their importance within your supplier ecosystem. Automate UK and BARA welcome discussions with automation suppliers and end-user manufacturers on supply chain development. To share your opinions, contact [email protected] |
|
|
|
Automation influences | 24/02/2025 |
Oliver Selby, BARA chairperson and head of sales at FANUC UK takes a look at global and domestic trends influencing automation uptake IN THIS issue's column, I intend to focus on the new technologies that are being deployed in industry right now and what trends might influence automation adoption in the coming years. There are many global trends being reported from which we can gain insight, but which of these will solidify and show resilience in what is an ever-changing automation space remains to be seen. As reported by the International Federation of Robotics (IFR), artificial intelligence and humanoids are leading the technical discussion. While it’s clear to see that AI is becoming ever more present in our society and working practices, I believe that humanoids are some years off meeting the needs of industrial manufacturers compared with their industrial robotic counterparts, who are specifically deployed to do a certain task. While humanoids have a place in society, this is more likely to be outside of manufacturing and within the service industry. Digital twins One area that has been spoken about consistently over the past few years is the concept of digital twinning. Linked with IoT and Big Data, the idea of a true digital twin is being requested more at the point of equipment purchase and, interestingly, largely from SMEs that see it as part of their longer-term digitisation strategy. It’s clear that collating the right data to analyse can provide insight to help reduce waste, increase quality, reduce energy consumption and increase uptime. If a digital twin can help grow and maintain higher Overall Equipment Effectiveness (OEE) it can therefore directly improve a business’ bottom line. The key to success in creating a digital twin is to ensure the data that matters is being collected, so it can be used to drive those future insights that will affect your business. Other global trends that are driving automation growth are linked to challenges that we are seeing closer to home, such as the cost of energy and the drive towards sustainability. New markets including recycling, as well as existing industries like food and beverage, are looking for productivity gains and improved efficiencies. One of the biggest challenges many companies are experiencing is the skills shortage, in particular the lack of skilled employees to work in the manufacturing process (eg welders or painters). Adding to this are cultural shifts affecting who is available to work on production lines. A change in behaviour or culture of those new to work shows that fewer younger employees are willing to work on production lines with minimal opportunity for growth or development, for example in entry-level positions stacking pallets or filling boxes. Government polices Closer to home, we also have additional trends and government polices driving change. The forthcoming changes to National Insurance and minimum wage are having an effect on businesses’ growth strategies, prompting many to at least investigate what processes they can automate to ensure competitiveness in what’s becoming a globally aligned marketplace. Companies are beginning to turn their focus more towards operational costs (OPEX), ensuring they are running as efficiently as possible – and with the cost of people and the cost of energy two of the biggest outgoings affecting firms today, it is inevitable that these two factors are key drivers for companies developing automation strategies. Lastly, the government’s focus on developing and delivering an Industrial Strategy is being viewed as a positive step, and we have recently seen real engagement with stakeholders who can put forward the views of the SME community. Trade associations such as BARA have engaged with government officials and other organisations like MAKE UK to help support the productivity increases desperately needed to ensure UK manufacturers keep up with European and global competition. For more information and insights the Automation UK exhibition is being held the CBS Arena in Coventry on 7 and 8 May 2025. www.automation-uk.co.uk |
|
|
|
Supporting manufacturers to increase automation ambition | 02/12/2024 |
Having the ambition to automate allows for growth and company development, says BARA chair, Oliver Selby THERE ARE thousands of quotes from famous (and not so famous!) people stating that whilst you are standing still, you are actually falling behind. Whether that’s in relation to local, European or global competition, it’s my firm belief that the UK needs a wake-up call. We must start investing in our future production capability and then scale for capacity. This runs true for nearly all sectors of manufacturing, and whilst we’ve seen some level of automation, especially in those early adopter markets like automotive, we are now falling further behind our European and global competitors because of a lack of investment. I was recently asked what three factors support a higher rate of automation adoption. I immediately looked to those companies that are already deploying best practice and answered Ambition, Culture and Skills. Risk management Having the ambition to automate allows for growth and company development. It proliferates goodwill around investments within a firm and supports a more open risk appetite. The risk that new technology presents to a company as an early adopter can be managed with support from the equipment supplier, as well as internally with the right training and upskilling. These de-risking and risk management processes come in different forms and require different skills. In particular, there are three technologies or strategies that I believe will rise in value within engineering and procurement teams for future equipment adoption: 1. A wider use of VR Simulation and Analytic Tools for discrete event simulation and upfront technical de-risking. The ability to prove out the multitude of possible scenarios before production planning is invaluable, especially in high-speed production situations. Identifying potential bottlenecks prior to committing to a project is a huge win and ensures a much higher success rate when meeting OEE 2. A broader range of off-the-shelf specialised automation and robot solutions. As manufacturing sites look to move towards common solutions, there will be a shift from traditional capital purchase to more rental or leasing options that better reflect operating expenses 3. A move towards Total Cost of Ownership (TCO) vs. Payback Return on Investment (ROI). This will support longer term capability levelling with European and global competition, increasing capacity and generating value for UK GDP. Skills development Inspiring a culture of continuous improvement within a firm is paramount and will lead to calculated risks being taken on future production capability and capacity. However, by committing to education and skills development across their internal stakeholders, businesses will be better placed to manage these risks. From shop floor operators and maintenance and engineering teams to sales and leadership departments, it is vitally important that everyone understands automation and how it affects them and their business. A strong business rarely reduces headcount through automating; instead, they will be best placed to continue developing new products, bringing new ideas to market or winning more business. I hope that Automate UK and BARA can help by becoming more visible to those manufacturers looking for the knowledge and best practice to improve their production. Some of the de-risking tools that will prove so useful are already in development, so keep connected with BARA and Automate UK to benefit from these throughout the coming year. |
|
|
|
Encouraging uptake | 14/10/2024 |
Newly appointed BARA chair, Oiver Selby, looks at the role of the association in promoting the adoption of robotics and automation in UK manufacturing IN MY first piece for CDA I have to say that I am delighted and honoured to have been elected by my peers for the post of chairperson at the British Automation and Robotics Association (BARA). I have sat on the committee for the past three years as a general member representative and have seen quite a change in how the organisation is supported by the rebranded PPMA Group, which is now Automate UK, under the steady helm of Peter Williamson. I think the passion and ambition Peter imparts to the three trade organisations under the Automate UK banner – the Processing & Packaging Machineries Association (PPMA); the British Automation & Robotics Association (BARA); the UK Industrial Vision Association (UKIVA) – is very exciting, and positive for the industry. My ambition within the role is to strategically align and deliver value to the membership and all the other stakeholders that the association supports. The new support structure put in place by Automate UK helps dramatically, and we have already taken big steps in the past two years with the delivery of the Automation UK tradeshow, which has gone from strength to strength and will again grow next year. Common value When we think about the value a trade organisation can deliver for its members it is sometimes difficult to appease everyone. We count large OEMs, small SMEs, dealers and equipment suppliers, among our members, in addition to education, and Catapult engagement entities. With such a broad selection of those engaging with UK manufacturers in different ways, I hope we can unite those parties through the association and find common value in the way we all work to increase the adoption of robotics and automation in UK manufacturing. A common thread in most discussions I have with my customers, and within the panel discussions I engage in for Automate UK is the fact that the UK falls some way behind our competition in Europe, and globally, in terms of the number of robots adopted into manufacturing processes. Currently, we sit in the top 12 nations globally for manufacturing output (MAKE UK), but down at 23rd for robotics density within manufacturing (IFR, 2024). There are many reasons for this disparity but I hope to see, that while we are behind the curve now, UK manufacturers soon looking to capitalise on the benefits automation and robotics will give them. Higher productivity, higher quality, and supporting workforce challenges are some that I am sure will drive growth over the coming years. I hope that by strategically supporting our members and becoming more visible to those manufacturers looking for the knowledge and best practice to improve their production, we can help. There are going to be many ways we can do that, and in future submissions to CDA I’ll look to outline those in more detail. Whether it be business case development, de-risking methods, workforce upskilling or finding a supplier, I’ll try and cover it! |
|
|
|
FANUC’s Oliver Selby announced as new BARA Chair | 01/10/2024 |
THE BRITISH Automation and Robotics Association (BARA) has named FANUC UK’s head of sales, Oliver Selby (pictured left), as its new Chair, effective 1 October 2024. Taking over from George Thompson (right), Selby will be supported in his new role by vice-chair Rosie Davies from Reeco Automation. Part of Automate UK, BARA’s remit is to promote and support the development and adoption of industrial robots and automation in the UK, providing a voice to government, industry and academia. With more than 20 years’ experience, Selby is a longstanding and vocal supporter of the UK automation sector, and of manufacturing more widely. In his role as Chair, he plans to drive the association’s activities forward, supporting BARA’s aim to increase automation uptake while placing members’ needs firmly front and centre. Peter Williamson, CEO of Automate UK, says: “Oliver is an influential voice within the industry, his passion for all things manufacturing, automation adoption and future skills, will be a key factor in developing BARA alongside the existing committee, and with the full support of Automate UK.” Increasing automation uptake One of Selby’s key pledges is to ensure the association delivers real value to its members. “I am excited to bring my knowledge, influence and passion for automation to a wider audience, and will be fully focused on delivering value to all facets of the BARA membership and other stakeholders – from OEM robot manufacturers and system integrators to companies in the supply chain, academic institutions and High Value Manufacturing Catapults,” he states. “It has been widely reported that, despite our status as a leading manufacturing nation, the UK is still lagging behind the rest of the world when it comes to automation adoption. Communicating the myriad benefits that automation can bring, including through events such as Automation UK (7-8 May 2025, CBS Arena, Coventry) is key to increasing uptake. It is essential that we highlight how automation can alleviate manufacturers’ key challenges by helping to mitigate labour shortages, increase productivity, boost sustainability credentials, and cut operational costs.” Supporting UK manufacturers Selby continues: “However, it is also important to understand the challenges that manufacturers – particular SMEs – are facing. At BARA, we will strive to offer the right tools to manufacturers of all sizes, to ensure they can make the right automation choice for their business, with the right partners, and with the right technology, to futureproof their manufacturing operations as risk-free as possible.” |
|
|
|
A fond farewell | 27/08/2024 |
George Thompson pens his final column for CDA as BARA chair THIS IS the article that I have been dreading… Before I get into why, I need to ask where have the last three years as BARA Chair gone? As with most business endeavours I had such big plans, some of which have been realised, some are still in progress and some just weren’t possible to achieve. In my opinion, one of our greatest achievements during my tenure as BARA Chair was the creation of the Automation UK exhibition, which had its inaugural event in 2023. Having attended both years of the event, I personally think that it feels like no other event that I have attended. Could there have been a higher footfall? Maybe… That being said, the people that attended were all looking for solutions for specific manufacturing challenges. The show attendance has grown in the second year when compared to the first year, and the show doubled its footprint at the same time. For 2025, the Machine Vision Conference will also fall under the banner of Automation UK, which we think will benefit both Automation UK and MVC as vision and automation work hand in glove. We have also continued to develop the format for our BARA Roundtable events, which have predominately been held as online webinars. We did hold a Live Roundtable at Automation UK back in June, which was such a resounding success, we are repeating it on 25 September at the PPMA show. The panel all agreed that it was such a broad and important topic, that we all could have spoken for hours on the subject. Handing over the reins So, if you haven’t guessed it by now, my time as BARA Chair is at its end. On 1 October, I will hand over the reins to Oliver Selby, who is also the Head of Sales for Fanuc UK. I have known Oliver for quite a while and can safely say that he will do an outstanding job and will drive the Association forward with his unwavering drive and passion for Robotics and Automation. I know that he will want to introduce himself properly in his first article, so I will leave that bit to him. I will say that, like me, he thinks that the key to making our economy stronger is reliant on making our manufacturing sectors more efficient and cost effective on the global stage. The key to this is to automate more of the Dull, Dirty and Dangerous applications, which in turn will assist in enabling UK Companies to reshore their manufacturing and in turn creating more jobs. We all know that there is a skills shortage here in the UK, and I know that Oliver is passionate about how we could potentially achieve this. Again, I do not want to pre-empt anything he may or may not promote, so I’ll fade quietly into the background – to some extent anyway. Don’t worry, I’m still going to be on the Council and hope to be able to take part in Roundtable discussions in the future. If you’re around PPMA 2024 or Automation UK 2025, I’m sure I’ll be found somewhere around the events. I guess the only thing left is for me to thank you for reading my mad ramblings over the last three years. Thank you for giving me the opportunity to express my opinions and hopefully get you to think more about how automation can help your business grow, become more efficient and most importantly become more sustainable for the good of us all. www.automate-uk.com/our-associations/bara |
|
|
|
It's a reshore thing | 14/06/2024 |
BARA chair, George Thompson looks at automation's role in reshoring I RECENTLY gave a presentation on how automation can help us collectively achieve our sustainability targets. We’ve all heard the arguments for and against any given product or way of life, and it depends on which piece of research that you read as to what is the largest contributor to the environmental changes that we are seeing. I think it is safe to say that we would all agree that we need to implement some changes to save our beloved Mother Earth! We all know that automation has well defined benefits such as better utilisation of space and energy, improved productivity, increased efficiency, improved utilisation and flexibility, better utilisation of staff, consistent quality, less waste, as well as the Health & Safety benefits as a result of the reduction of manual handling. These same benefits could also be directly linked to sustainability as they help to reduce waste. Automation strategy By implementing an automation strategy, we can collectively improve the UK’s overall competitiveness and productivity. Once we improve these, the draw to lower cost manufacturing countries would not be as financially attractive. Once we collectively have the automation strategy in motion, we can collectively use automation as the key enabler for companies to begin reshoring their manufacturing processes back to the UK. By reshoring, we can begin to become less reliant on long supply chains. I hope you would agree that if a company needed a part shipment of an order, they could just pick up the phone and arrange it with a supplier on more or less the same time zone! There is another HUGE benefit for Reshoring, which has a key environmental positive. This benefit is the reduction of container ships traversing the world’s oceans. As part of my research, I was astounded to learn that there are over 90,000 cargo ships currently in the global fleet. According to an article that was published in the Guardian a few years ago, one of these cargo ships would emit the equivalent of 50 MILLION cars throughout its serviceable life. In this same article, there is a reference to the level of pollutants that these ships contribute, and that level is truly staggering. More UK manufacturing Do not get me wrong, I am not suggesting for one moment that we should move everything to the UK. We should, however, be looking to reduce the number of ships bringing products from far flung destinations as much as practical and how we can manufacture MORE here in the UK. This will in turn helping our UK manufacturing companies be more competitive on the global stage. As we all know, the UK was once one of the greatest manufacturing countries in the world and we do not need to wait for the UK Government to wake up and create a manufacturing strategy. Each and every one of us can make a difference and buy locally manufactured products wherever possible. So, in summary, automation is the key to reshoring, which is the key to growing our economy as well as saving our planet. Manufacturing the products that we want in our modern lives, should not cost us the earth. Make local, Buy local! If you would like to start your automation journey, but don’t know where to start – I would highly recommend visiting the BARA website where we have outlined several topics under the Expert Advice section to give some initial information. Whilst you are there, why not watch some of our previous roundtables again as there is likely to be just the information you have been searching for and register for our next roundtable discussion. |
|
|
|
Cutting-edge automation and robotics | 17/04/2024 |
RECOGNISED FOR bringing industrial automation and robotics to life, Automation UK returns to the CBS Arena in Coventry on 18-19 June. From showcasing the very latest innovative technologies and solutions, to providing an abundance of thought-provoking seminars where visitors can soak up the knowledge and be inspired to improve their own businesses, the wide spectrum of features in the show ensures it delivers something for everyone. The free-to-attend event also provides many great networking opportunities where visitors can both develop new contacts and build on existing contacts. Automation UK provides a platform for automation and robotics technologies to be demonstrated throughout the hall, giving visitors a vast array of opportunities to see for themselves what can be achieved. An impressive list of well-known companies will be showcasing their cutting-edge products and services including robots, robotics systems, systems integration, automation control parts and systems, and sensor and machine safety. The leading experts from the exhibiting companies will be eager to answer questions, provide technical guidance and recommendations on the most suitable solutions for specific needs as well as highlight the advantages their solutions can bring to businesses. Integrating these remarkable technologies offers many benefits including enhanced productivity through accelerating production, increased operational flexibility, a safer work environment, an ability to manage routine tasks efficiently, an attractive return on investment, and innovative solutions to address labour shortages. When combined, all of these benefits can deliver significant business improvements and enable the business to thrive in the future. Throughout the two-day show, visitors will be treated to a broad range of inspiring seminar sessions delivered by the industry leading speakers. These captivating sessions will provide visitors with a wealth of knowledge and inspiration to take away and digest how it can be used to deliver benefits to their business. In between fascinating presentations, visiting numerous interesting companies showcasing their products and services, experiencing live demos, and hearing about new product launches, there are many opportunities to meet new contacts and develop existing business relationships. These can be mutually beneficial for sharing knowledge, industry insights and problem solving. |
|
|