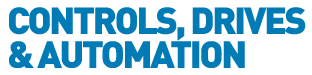
![]() |
Charlotte Stonestreet
Managing Editor |
Home> | AUTOMATION | >Handling & Logistics | >Line up the easy wins |
Line up the easy wins
17 April 2024
BARA chair George Thomson draws on his end-of-line experience

IN ONE of my recent columns for Controls, Drives & Automation, I mentioned the relatively quick wins around the End-of-Line solutions available. I thought that perhaps I should elaborate more on how this could work in a typical manufacturing environment. I have toured countless facilities in my career where I could see several opportunities for the elimination of manual handling through the introduction of relatively simple automation. There are others that I could see more complex solutions that would completely revolutionise their production!
Push pull risks
If I use a typical food processing company as an example, ingredients are moved around the facility in either wheeled totes or perhaps using a manual pallet mover where the products are manually depalletised. If we look at this first step, there are risks associated with the pushing/pulling of the moving the product tote or pallet coupled with the bending, twisting, lifting element of the depalletising – assuming the products are in a suitable container for a single person lift of course.
In an ideal world, the transfer of the product to the area for depalletising could easily be accomplished by using an AGV/AMR, which would eliminate the risk of the push/pull action used in the manual operation. The AMR/AGV could automatically load the pallet or tote into the depalletising cell, which could then load the ingredients into the appropriate machine. If this is a bagged item, there are existing solutions that are used in the Injection Moulding Machine loading applications that could easily be modified to depalletise, cut and decant the bags and deposit the empty bag into a bin / shredder / compactor ready for recycling, which perhaps the AMR/AGV could collect the completed bale on the return journey as part of its overall mission schedule.
The decanted product would then be dosed into the production cycle in a measured and controlled manner to ensure the recipe is followed exactly.
If we assume that the AMR/AGV doesn’t always pick a recycling bale, which it wouldn’t, perhaps on the return journey it could collect a completed pallet or trolley of product to be taken to goods out. Before we get to that stage, there are several areas that could also be automated relatively easily.
Another quick win is case packing, especially if this is coupled with a case or box erector and a box closer. Not all boxes are created equal, however most box styles can be loaded into the erector and closers.
Case in point
Case packing is another relatively easy win for most companies. The operators that are putting products into boxes, generally speaking, do not add any value to this process or the product. I know it is a necessity, but it would be far better to use automation to pack the cases and use the operators to conduct more value-added operations within the business.
The next stage is obviously End-of-Line (EoL) palletising where we have very similar manual handling concerns as I mentioned earlier for depalletising. Regardless of what type of EoL solution you pick, and there are numerous options, they will undoubtedly be more efficient than manual stacking pallets. Before the AMR/AGV collects the pallets, why not use an automatic pallet wrapper to ensure the pallets are secured and protected for transport. By the way, did you know that on average, an automatic pallet wrapper will use 30% less wrap when compared to most manual application of stretch film. This is not only good for the bottom line, but also better for the environment!
- Making the connection
- High Demand For Grant
- We need to automate more!
- Orchestrating with expertise
- Navigating the automation journey
- Why supply chain development is critical to automation adoption
- There's more to automation than robots
- To automate is to innovate
- Automation influences
- Encouraging uptake