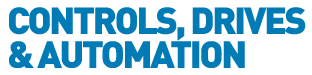
![]() |
Charlotte Stonestreet
Managing Editor |
Editor's Pick
Control signals - which option is best?
01 April 2014
As process control systems continue to advance and the use of complicated networked solutions develops, is there still a requirement for the simple analogue signal? Chris Hoey of Bürkert, provides an insight into selecting the correct control signals to produce the optimum process control system.

It is about twenty years since the industry ‘experts’ stated that 4-20mA would disappear from the market, to be replaced by digital networks or fieldbus solutions. Whilst there is some truth that networked systems have taken a large portion of market share, 4-20mA is still alive and kicking. There are two main reasons for this; firstly that higher-priced intelligent sensors, made for specific networks are not always the most cost effective options, nor are the ‘smart’ features on offer from intelligent field devices always wanted or required.
Secondly, the process control industry has changed significantly, with much more automation being installed into smaller plants, like food processing, water treatment, remote monitoring, etc. It could be said that 4-20mA was the last truly universal signal, accepted by every system, every vendor, and every control component. This means that single control loops, small plants and transportable skid-type equipment will always have a need for the simple, low-cost solution that 4-20mA offers.
Versatility
Let’s not forget just how versatile this ‘simple’ signal is. It uses just two wires to transmit the signal, it can power the field transmitter with its own supply voltage and it can run for long distances on standard cable. Using the live zero (4mA instead of 0mA) it senses a cable break or instrument failure, it is not overly susceptible to noise, it is highly accurate and low-cost. The downside is that two wires can only carry one variable or instrument.
However, as the number of control loops increases, the costs start to multiply, as you need individual cables, glands, terminals and inputs for every element. As well as the hardware, the space it requires and most importantly, labour to design, install and commission, which makes it uncompetitive versus fieldbus networks in applications with many sensors and feedback devices. It is different for every installation, but there is a point where the change from an analogue to a digital network becomes more cost effective.
Fieldbus
By using fieldbus networks, you can now have thousands of inputs and outputs on a single cable. This reduces the infrastructure that you would have needed for a traditional system and can save up to 50 percent of project costs, even though the actual hardware becomes more expensive. By using smart field equipment, the entire transmission of the signal is digitally accurate and generally there is configuration and often diagnostic data available. For large plant design, especially for heavy industry like petrochemical for example, this methodology is ideal.
The downside is the number of choices that a process designer has to make when designing these systems; the first being which network, as you cannot easily mix networks on site. Whilst the most popular networks used are not proprietary, they are still not available from all vendors, which starts to limit choices in components, even though they may be better suited to the application. For these reasons, it is rare to see a site that utilises only digital networks, however almost every larger site does use fieldbus technology. This leads us to the most common installation, the hybrid system.
Hybrid solutions
The hybrid system incorporates both technologies. The 4-20mA is used in the field, which keeps the components generic and lower cost, and then the signal is fed into a field Input/Output (I/O) panel where these signals are clustered and then transmitted to the central control via fieldbus. Without doubt, this system is the lowest cost to implement and simple to understand and maintain. The only downside for a network that is not fully digital is that you most likely won’t get configuration or diagnostic information from the field instrument, but the upside is that the instrument itself will be considerably lower cost. In order to clearly show where each communication option may fit, let’s look at an example:
Analogue in practice
Imagine a single flow control loop; say it’s the water feed to another process that needs to be maintained at the same rate. We would choose a flow meter based on the application requirements, with 4-20mA output. To control the flow, we’d choose a modulating control valve with 4-20mA input. But to close the loop, we need a Proportional Integral Derivative (PID) controller between these two instruments that can be configured to the application; this will need a 4-20mA input and output - done.
Now let’s say there are 15 of these loops, all identical, and the plant manager wants to monitor and record the flows in the system (assume a PLC & SCADA layer). Using 4-20mA, we would now need to send 15 signals to the PLC, plus 15 signals out, needing 6-8 input cards and as many as 90 terminals, 30 glands, cable tray, panel space, power supplies, signal isolation, etc. Now this option starts to become more expensive.
The digital option
Let’s try fully digital. We will choose a fieldbus protocol, such as Profibus. We will need to install a Profibus master at the PLC (unless it is incorporated) and then choose a flow meter that has Profibus, as well as a control valve that has Profibus. So now we have one slot in the PLC rack, one gland and one cable to all the devices. The PLC can now read the process signal and control the loop as well as log the data, via the 30 fieldbus nodes.
The only downside is that the field equipment is now more expensive, sometimes considerably, and specific to Profibus, so if the plant changed to Ethernet in two years, the field equipment would have to be discarded or a customized network-network gateway would need to be installed. This design is far more complex and may require highly qualified maintenance engineers.
The hybrid solution would be to use the original lower-cost field equipment, but to wire them directly to a local (field) I/O panel that converts them to Profibus and transmits them to the PLC. You get the cost savings of the installation, with lower cost field instrumentation, even allowing for the I/O cluster hardware. For this example the hybrid design provides the most cost effective solution.
Best practice
The really interesting thing is that Bürkert has solutions available for each of the options above. The customer can choose the installation that best suits them. But, what if this customer came to Bürkert with this application at the design stage? We would choose flow meters with 4-20mA output (8035) and feed these directly into our modulating valves (2301) with Profibus enabled positioner and optional inbuilt PID controller (8693). This device would control the flows directly as well as transmit process, output, configuration and even diagnostic data to the PLC, via just 15 fieldbus nodes. This ‘Bürkert’ solution, although being partly hybrid, would give all the functionality of the fully digital system, yet be around 30% lower cost than the cheapest option above; a good example of smart solutions.
Crucial advice
There is no perfect fit for all situations. There are many considerations that weigh into the correct selection of the site signal wiring, with cost being just one. Always seek competent advice and develop a tool that will estimate the total cost of the installation, including hardware, software and labour. Then consider whether it will be easy to commission and maintain, and whether you have the competence on site for fieldbus technology. As explained above, Bürkert has solutions for all options, so we have no bias towards one or the other, just a commitment to delivering the best value and long term reliability.
- Fuel-cell race car relies on Bürkert valve technology
- Take control of steam temperature
- Pipework & valve sizing for steam applications
- Controlling the brewing process
- Valve body design turns a corner
- Sustainability matters
- Simplifying industrial process automation with IO-Link
- Health care case study
- Solenoid valves – an enduring design refined over time
- Hydroformed diaphragm valve bodies
- Reduce Fault Times
- Vision Control Makes The Cut
- MULTIPLE PROTOCOL CONVERSION
- MAKE SURE YOU CATCH THE RIGHT BUS
- Smarter, Faster & More Compact Robot Controller
- What Does Windows 8 Mean For Test & Measurement?
- Thyristor Stack Controllers
- Easy To Automate
- Understanding Thyristor Control
- Introduction to embedded control and monitoring webcast