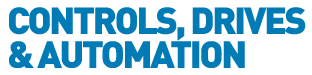
![]() |
Charlotte Stonestreet
Managing Editor |
Home> | CONTROLS | >Flow Control | >Valve body design turns a corner |
Valve body design turns a corner
27 August 2014
A new modular valve body design pioneered in Bürkert's latest INOX range of space saving modular valve bodies has increased the flow coefficient of a conventional angle seat valve, reducing energy requirements and improving system flow characteristics.
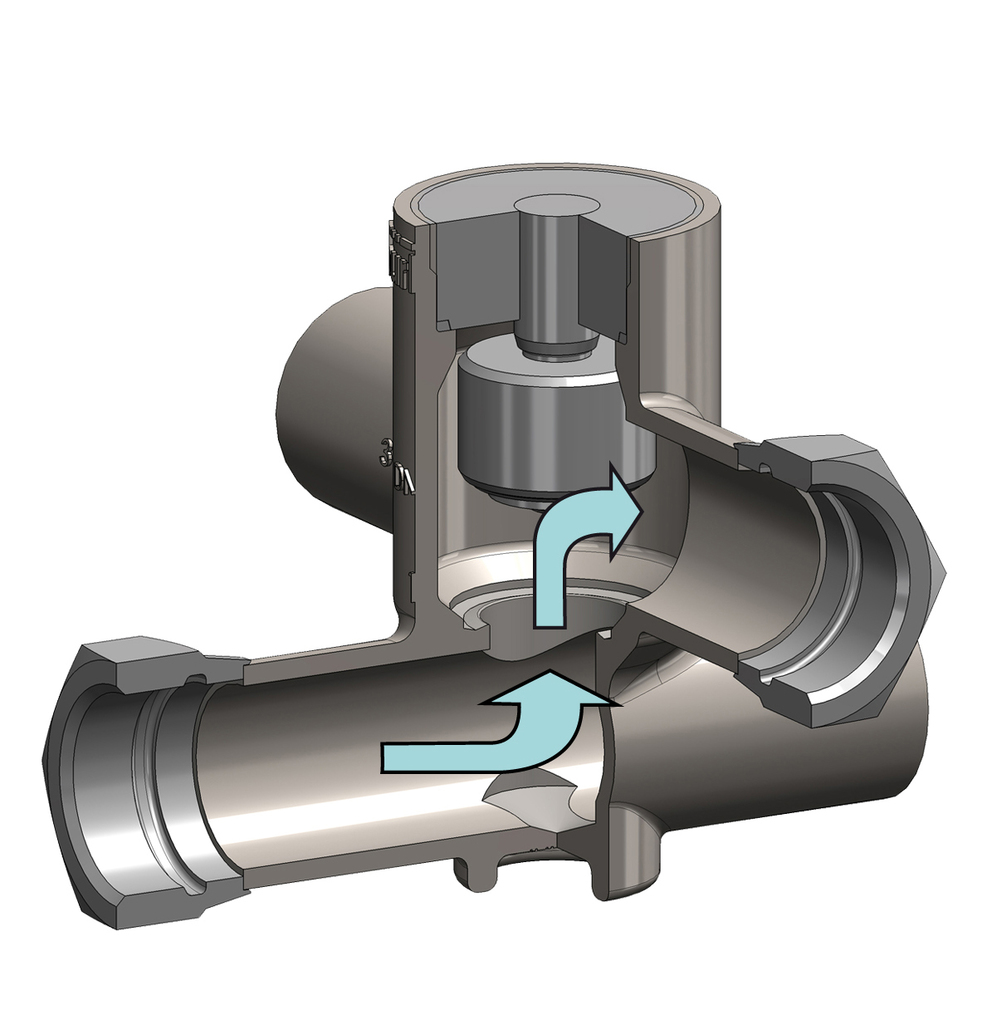
Conventional valve systems are designed so that the inlet to the valve and the outlet from the valve are at one level. Inside the valve, the fluid flow is conducted through a seat, which requires redirecting the fluid three times. This causes flow losses in the valve, which negatively affect the Kv value (flow coefficient for a valve).
In the new, modular basic body, the inlet level and outlet level are separate. Since the fluid flow now only has to be redirected once through 180˚, this increases the flow coefficient.
- Solenoid valves – an enduring design refined over time
- Simplifying industrial process automation with IO-Link
- Sustainability matters
- Kempston Controls becomes Midlands distributor for Bürkert valves
- Controlling hydrogen in fuel cells
- Take control of steam temperature
- Hazardous area pneumatics
- Keeping control valves clean
- Easy to service direct-acting solenoid valves
- Fuel-cell race car relies on Bürkert valve technology
- REGULATE FLOW
- FLOW CONTROL PRODUCT SEALS
- Verify Flow Controllers
- FUEL SAVINGS OF UP TO 30%
- ACCURATE POSITIONAL PERFORMANCE
- LARGE VALVE POSITIONER
- Fuel-cell race car relies on Bürkert valve technology
- Affordable Valve Management
- Multi-Finction Filtration Controller
- Air Flow & Pressure Switching Point Adjustment