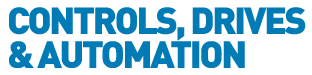
![]() |
Charlotte Stonestreet
Managing Editor |
Extending electric motor lifespan with better bearings
25 April 2014
High efficiency motors can bring significant savings but if budgets won’t stretch to motor replacement, energy efficient bearings offer a powerful cost-saving alternative, says Phil Burge, country communication manager for SKF
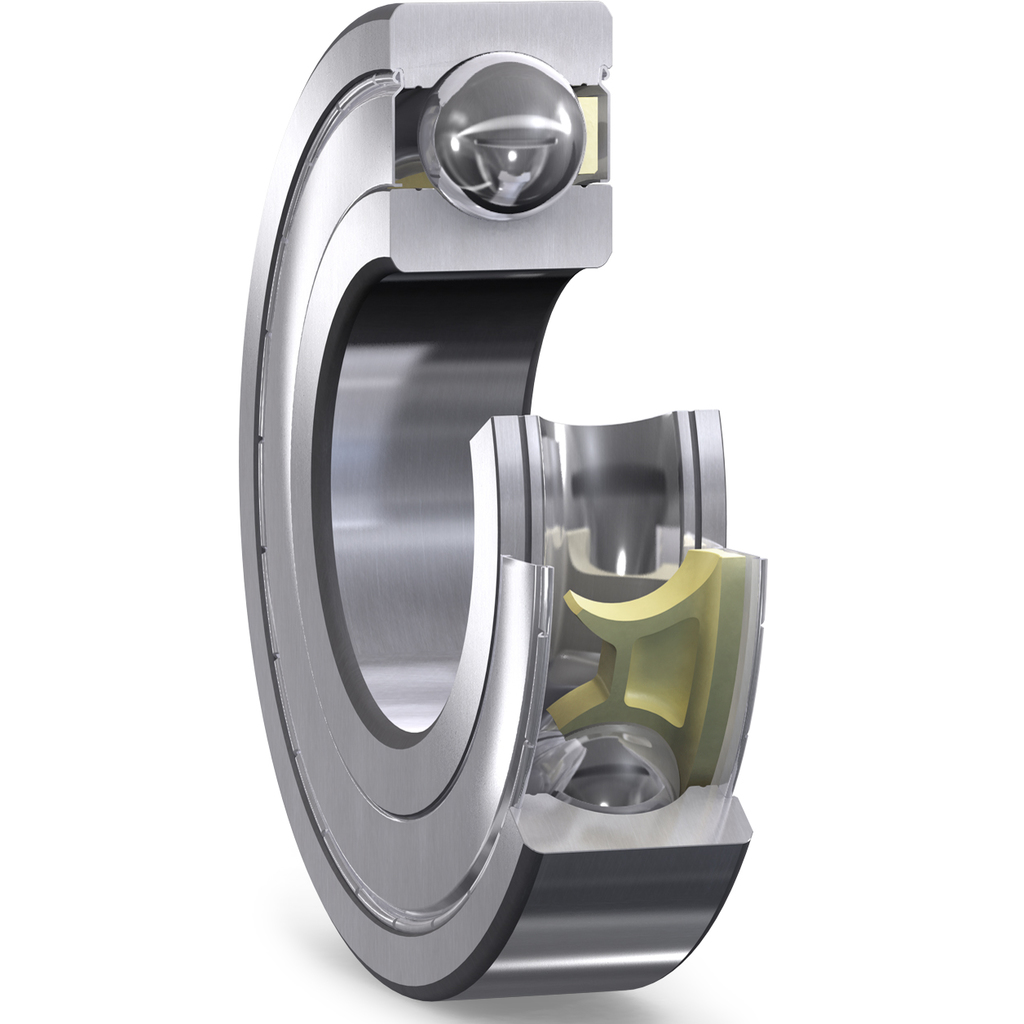
Up to 80% of all electric motors are rebuilt due to bearing failure. Yet, only a small number of failures are caused by true bearing steel fatigue. Most failures are caused by improper bearing use or inadequate maintenance. Research from SKF has shown that, with proper specification and maintenance, bearings in electric motors often function effectively for over 10 years.
The very best of today’s energy efficient bearings offer the potential to minimise frictional losses to such a degree that operating temperatures can be lowered by as much as 30°C, resulting in an improved lubricant viscosity that extends the operating life of moving parts. In addition, these innovative energy efficient bearings can last twice as long as their conventional alternatives, cutting the cost of purchasing as well as running the equipment at your plant. Developments such as these have proved that energy efficiency can be achieved even without the expense of replacing plant motors, boosting performance and productivity to the benefit of operators, while also satisfying environmental pressures to consume less energy.
No additional downtime
Another positive point to bear in mind is that replacing your existing bearings with energy efficient alternatives does not require additional downtime; they can be exchanged during routine maintenance. Deep groove ball bearings are dimensionally interchangeable with standard equivalents and available in a range of sizes, enabling the change to be made during planned downtime.
Without generating the considerable cost of replacing motors, energy efficient bearings can make a difference in all applications, and where energy savings are concerned, it’s not only a one-off benefit; any saving you make is being made day by day and year on year. To give an example of how this might be calculated in practice, take a typical electric motor, which can generally be fitted with energy efficient bearings in sizes of up to 37kW. If the best of the current range of energy efficient bearings are used in a single 37kW motor, running continuously at 3000rpm, that will make an energy saving of 270kW per year, and keep more than 150 kg of CO2 out of the atmosphere. The benefits are even greater on a larger scale: SKF helped a leading consumer healthcare company to reduce frictional losses by 46% by providing energy efficiency deep groove ball bearings in cold water pump motors (22kW) running at speeds of 2990rpm. Ultimately, this translated to energy savings of 4583kWh per year per motor.
Reduced wear
Today’s leading energy efficient bearings enable components to rotate more easily with minimum friction and heat, dramatically reducing wear and enhancing performance. For example, SKF Energy Efficient deep groove ball bearings feature a host of technical innovations that reduce friction. The internal geometry of the bearings has been optimised via the use of advanced modelling tools, which, in tandem with a new, fit-for-purpose polymer bearing cage, has brought a marked improvement in operating efficiency.
Most agree that a positive, long-term effect on the business can be achieved by replacing older motors with modern, high efficiency equivalents. However, this is not always feasible; when budgets are tight, even proven, long-term cost-saving options such as the installation of energy efficient motors may be tricky and cash flow problems may rule out the possibility altogether. And when you consider that up to 80% of all electric motors are rebuilt due to bearing failure it makes sense to consider how better bearing specification and maintenance can reduce wear on electric motors and increase efficiency.
Recent innovations in energy efficient bearings represent not only a positive step in the right direction for plant efficiency but also a significant opportunity for companies throughout industry to minimise the environmental impact of their operations.
Key Points
- According to SKF, with proper specification and maintenance, bearings in electric motors often function effectively for over 10 years
- Energy efficient bearings can minimise frictional losses, lowering operating temperatures by as much as 30°C
- Replacing existing bearings with energy efficient alternatives can be carried out during routine maintenance
- Induction heater for large bearings
- SECRETS OF THE DRIVE BELT
- SKF launches software centre for condition monitoring
- 'Cooper Roller Bearings' becomes 'SKF Cooper split bearings'
- SKF's 1000th S2M put into operation
- When is a hybrid bearing the best choice?
- SKF and EPTDA address the challenges of counterfeit bearings
- A BRAVE new world for bearings
- Makes bearings selection easier
- When the going gets tough
- No related articles listed