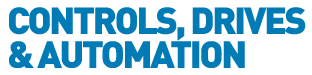
![]() |
Charlotte Stonestreet
Managing Editor |
Overcoming the barriers to logistics automation
30 November 2015
The traditional barriers to investing in warehouse automation are weakening in the omnichannel landscape, argues Dave Berridge, Secretary of the Automated Material Handling Systems Association (AMHSA)
The barriers to intralogistics automation have traditionally been the high capital investment involved and the perceived lack of flexibility. The view that automated systems are inflexible has, to a large extent, been undermined in recent years as logistics professionals have come to understand how automation can cope with the complex demands of omnichannel distribution. The matter of evaluating return on investment (ROI) remains, however, a vexed one.
In this era of fast-paced market change and general globalisation, all industrial sectors have had to face up to the challenges of controlling inventory, optimising material movements and eliminating errors in the supply chain. Today’s consumers demand choice and instant availability of goods in store and online, making retail supply chains highly complex. Space is at a premium and the constant focus on cutting costs, along with SKU (stock-keeping unit) proliferation, means that retailers simply cannot afford to maintain high stock levels at the point of sale. They have to manage their logistics in order to satisfy consumer demands or risk losing market share to more responsive competitors.
The modern retail distribution centre (DC) faces challenging demands for shorter lead times, more frequent deliveries and store-friendly consignments, as well as rapid response to e-tail orders. These are demands, however, that automated handling is inherently suited to meeting. Store-friendly deliveries, for example, are a relatively simple affair for a solution governed by a Warehouse Management System (WMS). Economic picking of low-volume e-commerce orders is relatively easy with automation. In addition, the ease with which automation can deal with returns is increasingly important – software systems allow returned goods to be viewed as saleable stock more quickly and automation can avoid the reintegration of returns, which can be stored in a dedicated returns area, as the WMS knows where they are and that is all that matters.
High capital cost
Perceptions of inflexibility may have been largely dealt with, but the high capital cost of investing in automation remains. With many British companies reluctant to buy any solution with a payback period of more than two years, the typically longer ROI of an automated warehouse is likely to be problematic. The ease with which an investment can be justified depends on the process of calculating the ROI. The return on – or benefit from – an investment is worked out and then divided by its cost to result in a percentage or ratio. The problem, of course, is how to calculate the return, as not all the benefits can be neatly quantified.
Labour & space savings
The potential savings resulting from automation can be divided into three categories – hard, soft and intangible. Hard savings are the ones that are simple to quantify such as labour savings, both direct and indirect. Automation allows manual forklifts to be replaced by conveyors and automatic stacker cranes. Its greatest impact, however, is on order picking, the most labour-intensive activity in the DC. Automation allows traditional person-to-goods picking to be replaced with goods-to-person systems that allow ergonomic and error-free fulfilment of up to a thousand orders per operator/hour.
Not limited by the dimensions of a conventional pick face, goods-to-person solutions can handle SKU proliferation and – by eliminating the ‘shoe-leather’ costs of time spent travelling between pick locations – they have the potential to increase productivity significantly. An indirect labour effect results from the fact automation makes picking less physically demanding, thereby making it easier to retain staff. Another example of a hard saving is the reduced space required for automated storage, allowing companies to avoid the need for new facilities or extensions by improving the use of their existing space.
Lower inventory & energy costs
Soft savings are more tricky to quantify – or, at least, more difficult to attribute to any one project. Inventory reductions – in terms of raw materials, work in progress and finished goods – fall into this category. The true cost of holding stock can be enormous: the cost of the capital, the inability to use that capital in more rewarding ways, the increased risk of stock damage and the higher probability of being left with obsolete stock. In an automated DC, the WMS automatically optimises the inventory and facilitates automatic reordering, FIFO (first in, first out) and stock control, which are difficult tasks to manage in manual DCs.
The intangible benefits of automation include factors such as better health and safety, enhanced working environments and improved corporate image through higher customer service levels. There are also a number of environmental benefits from automation that fall across the three categories. They include reducing the need to heat and light a warehouse by concentrating labour in specific areas; minimising energy consumption through the use of software to control highly efficient electric drives; and achieving optimum space utilisation and the most fuel-efficient drop route through computer control of vehicle loading.
Hidden advantages
Project managers needing to justify investment in logistics automation must work hard to uncover all the hidden advantages in their cost-benefit analysis, even if they cannot accurately quantify them. For example, will automation make the company more responsive to fluctuations in demand? Are competitors likely to invest in automation in the near future, meaning that investment now will reduce the business risk? What might be the savings in terms of dealing with fewer returns if picking accuracy were increased by just one per cent?
With the useful life of an automated handling system being 10 years on average – but with many providing 20 or more years of service – the case for automation is strong. It is just a matter of making the value of the benefits as clear as the stark cost of the investment. The key difficulty here is that stakeholders are not comparing like with like. The manual warehouse and the automated one are different in so many respects – concept, layout, processes and methods – that sensible comparison is extremely difficult. Investment in a material handling system is not simply purchasing machinery that automates your company’s existing procedures – it involves total rethinking of your supply chain, which may result in a radically different way of doing things. As Bill Gates put it, “The first rule of any technology used in a business is that automation applied to an efficient operation will magnify the efficiency. The second is that automation applied to an inefficient operation will magnify the inefficiency.”
Training Workshop
If you are thinking of introducing automation to your logistics, consider attending AMHSA’s next Training Workshop on 10 February 2016. Taking place at the association’s headquarters in Market Harborough, this all-day event is ideal for people who are new to the industry or want to have a wider overview of handling systems. It will feature a range of presentations on various aspects of automated and manual warehouses including system design, racking and shelving, pallets and totes, conveyors, cranes, picking solutions, AGVs, WCS/WMS, sortation and despatch systems. For more details, please visit the Events page of the AMHSA website.
AMHSA is committed to promoting excellence in the automated material handling industry in terms of solutions, after sales support, reliability and safety. AMHSA promotes the interests of its members, defines and upholds best practice in the industry and aims to be a leading example of excellence. It gives access to the latest information and industry intelligence, as well as superior technical knowledge and support.
With over 50 members supplying automated solutions, conveyor systems and associated equipment, AMHSA plays a significant role in the drafting of CEN and ISO standards affecting the automated handling sector, maintaining close contact with government organisations such as the Department for Business, Enterprise and Regulatory Reform (BERR - formerly the DTI) and the HSE.
- No related articles listed