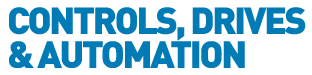
![]() |
Charlotte Stonestreet
Managing Editor |
Home> | AUTOMATION | >Handling & Logistics | >Controlling carbon footprint in the warehouse |
Home> | Guides | >MAD Guide | >Controlling carbon footprint in the warehouse |
Controlling carbon footprint in the warehouse
05 January 2015
Reducing energy use makes business sense – it saves money, enhances corporate reputation and helps to tackle climate change. When it comes to energy efficiency in industry, argues Dave Berridge, Secretary of AMHSA, there has been a tendency to focus only on the components specified within manufacturing and distribution environments, rather than looking at the bigger picture
According to The Carbon Trust, electric motors are estimated to account for almost two thirds of global industrial electricity consumption. It makes economic sense for users of electric motors to take care in specifying their equipment – in a single year, a running motor can cost up to ten times its purchase cost in energy, so the potential cost savings from energy-reducing initiatives across multiple motors can be huge.
In recent years, drive motor technology has advanced significantly, resulting in revolutionary reductions in energy consumption and thus helping to minimise carbon dioxide emissions. For example, the use of Linear Synchronous Motor (LSM) technology can result in a reduction in energy use in the order of 75% compared to a comparable system using a conventional Linear Induction Motor (LIM).
Optimisation of mechanical equipment is achieved by reducing friction through the use of high-quality bearings and gearboxes, as well as through reducing the weight of mobile parts, which also increases maintenance intervals and component life. Energy recuperation technology has also been playing an increasingly important role in reducing the energy consumption of automated handling systems. In a crane system, for example, energy-recuperating equipment can save about a third of the energy used in conventional cranes.
The role of logistics strategy
It is easy to see, then, why the focus has been on component technology in recent years. However, although this emphasis may be justified in the manufacturing sphere, when it comes to distribution there are other factors that should be considered. Typically energy use in a distribution centre comprises 15% for lighting, 35% for heating or air conditioning, 2% for other activities and a massive 48% for transport and storage techniques. Given the high figure attributed to transport and storage, it follows that the choice of logistics strategy within a distribution centre can have a huge impact.
For example, retrieval by a miniload crane of a tote bin requires considerably less energy than retrieval of a pallet load by a stacker crane. Within tote-based systems, retrieval of a bin in a shuttle-based automated storage and retrieval system (ASRS) – which features a dedicated shuttle on each level of the store – requires less energy than retrieval by a miniload crane.
As well as the choice of technology, the selection of techniques and protocols within that technology can have a dramatic impact. For example, dynamic slotting – where loads are allocated locations within the store according to their mass and order frequency – can result in significant reductions in energy consumption. Placing heavy goods on lower levels and lighter goods on higher levels, combined with locating frequently ordered goods near to the front of the store and slow-movers at the back, can result in significant energy savings. Of course, dynamic slotting is much simpler to implement in a computer-controlled automated solution. As well as optimising storage locations to minimise energy consumption, automation in the warehouse also reduces energy use in transport by optimising the material flows to reduce the overall number of goods movements.
Control is key
Another key factor in warehouse energy use is the extent to which intelligent control systems are used. Typically 80% of cost reduction in a warehouse is the result of smart control systems, rather than simply using more efficient components. For example, a conveyor system only needs to run when there is a load in transit. In fact, only the specific section of the conveyor where the load is located needs to be live. Control of drive motors is far superior now to what was possible just a few years ago. Sophisticated software can ensure that the drives operate only when required, and can also accumulate handling tasks for release in efficient batches.
Software can also be used to organise the loading of vehicles, ensuring both optimum space utilisation and the correct drop sequence for the most efficient route. The results are fewer transport journeys and fewer delivery miles, both of which reduce fuel costs and emissions. Many firms are now giving consideration to their return loads too, with some even co-operating with other companies to fill empty vehicle runs.
Lighting is another area that can be controlled so that it is only illuminated when required – for example, when people enter a specific area of the warehouse. In fact, full automation of processes such as storage and retrieval of stock means that these operations can take place without the need for any heating or lighting at all, as automated stacker cranes and robots – unlike human operatives – simply do not require them. Any staff that are needed – such as order pickers, supervisors and maintenance engineers – can be housed in heated and lit areas that are strategically placed within the facility. Of course, the more compact design of automated warehousing also reduces the energy required for temperature control.
Other environmental advantages that warehouse automation secures include reduced use of paper through paperless picking and simpler handling of reusable materials. Increased order accuracy and reduced product damage through automated picking secure additional green benefits in terms of lower returns. Last, but by no means least, automated warehouses require considerably fewer employees and thus avoid not only a significant amount of lighting, heating and water costs but also a huge number of journeys to and from work with their resulting carbon emissions.