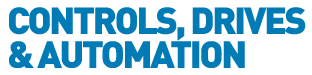
![]() |
Charlotte Stonestreet
Managing Editor |
High volume production of turbocharger ball bearings comes to Wales
08 March 2017
The Schaeffler UK automotive plant in Llanelli, South Wales has become the global location of choice for the production of turbocharger ball bearings. Start of production is planned for Week 21, 2017.
Due to changing market conditions, a shift in customer requirements and an increase in worldwide demand for turbocharger ball bearings, production has been transferred to Llanelli – a plant that is deemed more suitable to high volume, high speed, lower cost production of high precision components.
Mr. Klaus Cierocki, President Business Division Engine Systems at Schaeffler comments: “The trend in the automotive industry towards cleaner powertrain solutions requires multiple steps and technologies. The fundamental foundation in achieving CO2 reductions at an economical cost-benefit ratio is still by optimising the conventional internal combustion engine. Downsizing of the engine leads to more opportunities for turbocharger applications.”
Schaeffler UK’s world class manufacturing plant in Llanelli produces mechanical tappets for the automotive industry. The plant, which was established in 1957, employs 250 people. A recent investment programme in new plant and machinery worth tens of millions of Pounds has now allowed Schaeffler to supply surface coated engine components that lower fuel consumption and reduce CO2 emissions, whilst using an environmentally friendly vacuum process (no CO2 is produced). Of the 20,000 square-metres of floor space at Llanelli, around 5,000 square metres has been transformed into production space for turbocharger ball bearings.
As Dr Dave Bate, Plant Manager at Schaeffler UK Ltd states: “We expect the demand for turbocharger ball bearings to increase over the next five years to reach millions. This demand will come from multiple turbocharger customers worldwide. This is therefore a great opportunity for the Llanelli plant to secure its future by expanding its portfolio of products. This is just the beginning of the plant redefining and repositioning itself for the future.”
- World's most powerful wind bearing test facility
- World's Largest Bearing Test Rig Now Operational
- Condition monitoring helps prevent unplanned downtime
- Linear profile rail system replacement
- Increases bearing life
- New EV bearing solutions
- Schaeffler starts mass production of electric motors
- Bearing developments
- Pocket guide from Schaeffler
- SBTi validates Schaeffler Group's emissions targets
- No related articles listed