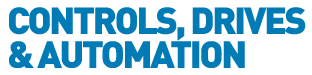
![]() |
Charlotte Stonestreet
Managing Editor |
Heavy duty actuators help improve mobility
11 October 2019
US-based Fenton Mobility holds numerous patents for personal mobility innovation, including a low-angle wheelchair ramp that enables safe, easy van access via the rear entrance. Smooth, reliable operation of this ramp is critical to the comfort and safety of passengers, and Fenton achieves this cost effectively thanks to smart, heavy duty electromechanical actuators
Demand for custom vehicles among urban paratransit services, nursing homes and other cargo van users is growing steadily. Manually raising the roofs and doors on Ford Transit vans to accommodate wheelchair access had become a significant part of Fenton Mobility’s business but was threatened in 2015 by the emergence of new European van designs that came right from the factory with raised roofs and doors.
“We actually saw the change coming around 2013 and went to work on ways to make it even easier for ambulatory and wheelchair clients to access these Euro-style vans which are also available in the US,” said Scott Fenton, President of Fenton Mobility Products. “The result is our patented AbiliTrax platform, a universal flooring platform that bolts into European-styled Dodge Ram ProMaster, Ford Transit or Mercedes Sprinter vans that are available in the U.S. The platform gives users more flexibility in locating seating and access ramps.”
Reducing angle of access
Installing the ramp in the rear of the van provided more convenient access in confined spaces such as garages and other tight parking areas. However, the fact that the European-style van still required a relatively steep angle of access presented a unique opportunity for Fenton designers. If they could enable a lower angle of access to the back of the van, wheelchairs could roll in more easily and safely.
Accomplishing this required mounting actuators inside the back of the van to apply thousands of pounds of downward compression force to the vehicle’s standard suspension. Fenton designers first considered using pneumatic actuators for this application but soon rejected the idea out of concern that condensation in cold weather could jeopardise reliability.
They then concluded that heavy duty electromechanical actuators would be the most effective solution. To meet Fenton specifications, these actuators would need to be compact while featuring higher force ratings than comparable hydraulic systems. With strength to apply at least 2200lb of compression force to the van’s rear suspension, the actuators would enable the vehicle to squat down, lowering the ramp by six inches.
After testing different electromechanical actuators, Fenton selected Thomson Electrak HD linear actuators due to their high load handling capability, environmental resistance and onboard electronics, which provide digital position feedback, advance diagnostics and CAN bus networking.
“We can connect the high voltage required to drive the actuator directly to the battery and use low-voltage switching to control it,” said Fenton. “Any time you can control high-voltage power with lower-voltage signals, it will be much easier, much safer, and less expensive because of the limited and reduced-size wiring needed to accomplish this. And it enables us to offer something that our competitors cannot.”
Low-level switching allows the actuators to be extended or retracted with a simple control signal, which is much safer than switching the full current required by the motor. Built-in end-of-stroke indicators inform users when the actuator is fully extended or retracted, and the actuator electronics also facilitate cycle count data on the Abilitrax system.
Fenton liked that the actuator’s electronics could be overridden manually during a power loss. “If we ever had a wiring issue or other problem that disabled the actuators, they are easily extended or retracted manually,” he said. “So, if the van experienced an electronic failure or loss of power while in squat position, the user could bring it right back to factory ride height manually.”
Fenton also liked that, compared to competitive models, Electrak HD actuators run at their rated power or, oftentimes, much lower, perform consistently from unit to unit, and feature simpler cabling. “You are only running one cable to the battery, and all switching is done in a water-tight enclosure,” he said.
Thomson Electrak HD linear actuators allow the AbiliTrax platform to lower the van’s rear, enabling the vehicle to squat down and lower the ramp by six inches.
Key Points
- To meet specifications, actuators needed to be compact while featuring higher force ratings than comparable hydraulic systems
- Thomson Electrak HD linear actuators were selected due to high load handling capability, environmental resistance and onboard electronics
- Electrak HD actuators run at their rated power or often much lower, perform consistently from unit to unit, and feature simpler cabling
- Size & select electric linear actuators online
- Achieving hazard-free linear motion
- Linear actuators now with encoding
- Energy saving switch
- Designing smart machines starts with smart tools that enhance automation control
- Off-highway actuator
- Why pre-engineered linear motion systems are a smart choice
- Energy efficient electric actuators on track
- High power can come in small packages
- Marine-grade corrosion resistance
- No related articles listed