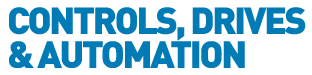
![]() |
Charlotte Stonestreet
Managing Editor |
Editor's Pick
Layered defence helps ensure compliance
02 September 2019
Machine safety should be high on the agenda of any manufacturing organisation. The best approach is a layered defence and underpinning management controls to ensure compliance and good practice, reports Richard Jeffers
Industrial machines are undoubtedly dangerous. In 2018/19, 26 UK workers were killed in manufacturing, of which 14 were killed by contact with moving machinery. Around a further 7,100 people suffered a RIDDOR reportable accident for the same reason, according to HSE accident statistics.
Machine safety is a subject particularly close to my heart after receiving a call in the middle of the night to report an accident at my factory – I’m pleased to say the individual recovered, but it was a long journey.
In all EU countries, machine safety is covered by the Machinery Directive 2006/42/EC, and enacted in the UK through the Supply of Machinery (Safety) Regulations, amended in 2011. The latter document calls out three fundamental principles that must be applied, in the order given, as Essential Health & Safety Requirements of the regulations:
- Eliminate or reduce risks as far as possible (inherently safe machinery design and construction)
- Take the necessary protective measures in relation to risks that cannot be eliminated
- Inform users of the residual risks due to any shortcomings of the protective measures adopted, indicate whether any particular training is required and specify any need to provide personal protective equipment.
The first of these is very much in the hands of the original equipment manufacturer, applying best practice around machine design and ensuring the asset achieves its CE marking. The second, to an extent, and the third, fully, are in the hands of the operator.
Optimising processes for risk elimination
Eliminating the risks is often addressed through fixed guarding, but in many instances, this creates its own issues in terms of access for maintenance, operations and cleaning. These in turn often create their own human factor risks, as people are tempted to bypass the guards. Care should be given to ensure that guarding cannot be removed without the use of special tools and, preferably, removal of fixed guarding should break the safety circuits.
Movable physical guarding allows better access to machines, but, particularly where a person can enter the guarded space and close the movable guarding, some form of twin key system should be fitted to ensure that the machine cannot be restarted with a person in the protected area. The challenge becomes greater here when machines need to be operated at slow speed during changeover and maintenance activity.
Light barriers and other non-physical systems are excellent tools in the guarding armoury, but it is essential that they stop the machine in a safe position, with the stored energy released. A number of fatal accidents have occurred where palletisers have been stopped and an operator has stepped under the load, which has then descended rapidly under gravity.
The last line of defence is to supply/use the correct PPE that is fit for purpose, meets the standards required for the application and are readily available.
The importance of training
A critical factor in machine safety is training to inform users about the residual risks and, equally as important, to ensure users understand how the safety circuit operates. Palletisers will have an access route into the danger area where the pallets are removed. There should be regular training to ensure that these are never used for man access, as it will defeat many of the safety systems. To ensure the training is embedded and complacency does not creep in, many organisations will conduct routine audits of how the operators interact with the safety systems through discussion and observation – allowing regular feedback where issues have arisen, or new risks have been identified.
Machinery safety is of critical importance to all of us who work in industry. Safety lies not just in the machine and the enclosure design, but equally, if not more so, in the human factors. If people do not understand the risks and the physical means of mitigating them, there is always the risk that the protection layers may be breached, potentially leading to a dreadful night time call.
Richard Jeffers is Technical Director for RS Components in Northern Europe
Key Points
- Eliminating machinery safety risks is often addressed with fixed guarding, but this can create issues in terms of access
- Twin key systems fitted to movable physical guarding help ensure machinery cannot be restarted with a person in the protected area
- The last line of defence is to supply/use correct PPE that is fit for purpose and meets standards required for the application
- Supporting engineers for 80 years
- RS sponsors Maintec Solutions Theatre
- 3D design software
- RS offers Omron Panel Solution portfolio
- RS PRO enclosure range extended
- Practical PCB design
- Electrocomponents acquires Monition
- Fast deep-learning IoT development
- Robot for educational markets & users
- Multi-purpose sensor products
- No related articles listed