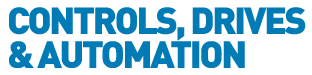
![]() |
Charlotte Stonestreet
Managing Editor |
Home> | DRIVES & MOTORS | >AC Drives | >Savings Galvanised |
ARTICLE
Savings Galvanised
01 November 2012
Medway Galvanising Company in Kent is set to save over £10,000 a year in electrical energy costs while also cutting CO2 by 60 tonnes a year following the installation of an ABB standard drive on its fume extraction system.

The new installation involves an ABB standard drive and a high efficiency 37 kW ABB motor. For most of the time, the ABB motor runs at half speed, or 25 Hz. A limit switch detects when the crane carrying the components to be dipped is over the zinc bath, signalling the drive to ramp up the motor to full speed to achieve the maximum extraction rate. This maximum speed is required for between 10 and 20 minutes, depending on the weight of the component being dipped.
The solution was provided by Mid Kent Electrical (MKE), an ABB Drives Alliance member.
MORE FROM THIS COMPANY
- Greater speed & torque control
- Drive for consistent mixing
- Drives floor energy costs for high rise
- Easy to select pH sensors with advanced analytical capability
- Tata Steel on a mission to cut energy waste
- Achieve EU MEPS compliance with IE2 motor-drive package
- Energy costs cut
- What your electrical system isn't telling you
- Water-cooled marine motor
- Reliability issues solved
RELATED ARTICLES
OTHER ARTICLES IN THIS SECTION