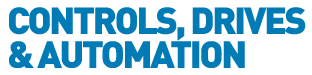
![]() |
Charlotte Stonestreet
Managing Editor |
Editor's Pick
It’s never too late to save energy using variable speed drives
07 August 2019
Variable speed drives are 50 years old and, therefore, can be classed as a mature, established technology. Herein lies a problem as ABB’s Stuart Foster explains
In their early days variable speed drives (VSDs) courted much publicity, in a similar way that the smart tablet or smart phone made people realise the benefits of something they didn’t know they needed.
Now smart devices are an accepted way of life. Likewise, the VSD has followed the same path. The excitement and curiosity as to how the magic of inverters, rectifiers, active front ends and pulse width modulation combined to regulate the speed of an AC induction motor are long gone. VSDs are an accepted commodity.
But only among those who are aware of them. Today’s graduate engineers and technicians appear less aware of a VSD‘s potential, as witnessed by a series of seminars held by ABB.
The company’s CPD accredited training course describes the energy-saving benefits of using VSDs. It starts with the fundamentals and explains how the Cube Law can result in energy savings between 20 to 60 percent, with a payback often in under two years. Yet often, despite its foundation-level, the audience is enthralled and totally surprised to hear what a drive can achieve.
Overlooked opportunity
If the front-line engineering community is not engaged, has switched off or been distracted by other technologies then the opportunity to save energy using VSDs is being overlooked. Those that pay the energy bills, the C-Suite executives and other stakeholders that have a vested interest in sustainability issues, risk being less informed and more disconnected from the massive energy saving potential.
The fundamental challenge is knowing where to look. All industries and commercial buildings use electric motors to power motor-driven applications like fans, pumps, compressors and conveyors. There can be hundreds of motors scattered throughout a building and assessing the energy saving potential of every application can be daunting.
To address this, ABB offers a short-form energy assessment in which it identifies up to five key applications and in just half-a-day can assess the energy saving impact. A customer’s own plant engineer, familiar with motor-driven applications, is encouraged to accompany the ABB engineer on the site assessment. By shadowing the ABB engineer, the customer will be shown what to look out for and how to unlock the energy saving potential, enabling them to independently check other applications when ABB leaves the site.
The output from the assessment is a report that is tailored to speak the language of those with an interest in energy efficiency. For instance, the assessment recognises three principle stakeholders: the financial community, energy managers and operations & maintenance engineers. A financial controller, for instance, does not need to know how a VSD works and what features can be activated to save more energy. They simply need the hard evidence of the money saved and the return on investment. For the operations & maintenance engineers, a VSD is a rich source of untapped potential. VSD technology has not stood still and there are numerous ways the maintenance team can tweak or fine tune a process if they know the capabilities of a VSD, not only saving energy but improving overall productivity.
But knowing what advances in technology are available and how best to apply them, requires regular training. Recognising this need has lead ABB to open a dedicated training school at Coalville, Leicestershire. ABB’s trainers and lecturers are also available to attend a customer’s own site. Alternatively, the company’s UK network of ABB Value Providers are equipped to host training courses at their premises throughout the country.
Among the VSD and motor technology training available is an insight into the future of the digital powertrain. A typical powertrain comprises a VSD, motor, bearing and load, such as a pump. Traditionally each item was relatively standalone, with little, if any data, ever shared across the powertrain. However, the arrival of smart sensor technology has changed all that.
Smart sensors are devices that attach, without wires, to motors, mounted bearings and pumps. By monitoring the vibration, temperature and other parameters, the smart sensors add to the operational understanding of the powertrain. Detailed information can be extracted into a company's own portal and systems, ensuring that the right person is exposed to the right information at the right time. Information on many aspects of the production process is available, with dashboards giving full transparency so that the stakeholder can take actions that lead to less downtime, extended equipment lifetime, lower energy costs, safer operations and increased profitability.
Key Points
- Today’s graduate engineers and technicians appear less aware of a VSD‘s potential, as witnessed by a series of seminars held by ABB
- If the front-line engineering community is not engaged, the opportunity to save energy using VSDs can be overlooked
- Knowing what advances in technology are available, and how best to apply them, requires regular training
- Definitive guide to the big six flowmeter technologies
- High performance motor control
- Touchscreen data recorder
- Emergency drive hire
- Turnkey Project
- Energy costs cut by 15%
- Drive-to-drive communication capabilities
- Group head for oil, gas & petrochemical
- Driving down energy costs
- ABB launches on-line tool for selecting MEPS compliant motors
- No related articles listed