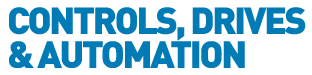
![]() |
Charlotte Stonestreet
Managing Editor |
Siemens collaborates with HVM Catapults
18 March 2019
Siemens is collaborating with a number of the High Value Manufacturing (HVM) Catapults across the UK to help support the growth and success of advanced manufacturing.
As part of its ongoing partnerships, the company’s digital technologies are playing an integral part in helping to bring new, innovative ideas to life and build value through the future commercialisation of new concepts.
‘FlexiFinish’ – helping to realise Additive Manufacturing potential
Additive Manufacturing (AM) is moving into series production, opening up unparalleled opportunities for suppliers, service providers and end-users. Unfortunately, despite the many advantages of AM, poor surface finish is a major barrier to adoption, particularly in demanding end-use applications, such as the civil aerospace industry.
To help overcome this issue, TTL, a leading industry name for CAD/CAM and CNC machining since 1987, with the support of the Manufacturing Technology Centre (MTC) and a range of technology partners including Siemens, is seeking to develop an effective commercial solution. Removing the need to use conventional post-processing approaches to the finishing of parts, which are traditionally costly, time-consuming and difficult to control.
Through a commitment to partnership and the use of smart technologies, including Siemens’ range of software tools and CAD/CAM robotics, TTL has developed ‘FlexiFinish’ – an automated, flexible, precise and comprehensive finishing solution for complex external and internal surfaces.
Advanced CAM and process modelling tools are employed to plan and control the finishing operations, selecting the most effective combination of finishing method for each surface from a comprehensive array of options, which, combined with carefully monitored in-process optical inspection, enable superior surface finishes.
Through the combination of multiple finishing and post-processing technologies (laser polishing, adaptive finishing and shot peening), FlexiFinish provides a robotic, fully automated system, which offers maximum flexibility to component geometries, while dramatically reducing the lead time for finishing.
One industry set to benefit from the innovation development being spearheaded by TTL is the civil aerospace sector. The sector struggles to exploit the benefits of Additive Manufacturing due to the stringent surface quality and integrity requirements for critical and highly stressed parts. However, the nature of the autonomous post-processing technique can also be exploited by the casting/forging industries to lower finishing costs and increase manufacturing efficiency.
With existing finishing methods unable to process the complex shapes that AM technology is most suited to within acceptable timeframe, cost and control considerations, the FlexiFinish system represents step-changing technology to make Additive Manufacturing a viable option for many manufacturers.
Simon Rogers for TTL, says: “Estimates show the Additive Manufacturing sector could be worth over £50bn by the middle of the next decade if current critical barriers to adoption, such as part finishing limitations, can be overcome. FlexiFinish aims to provide a proven, cost-effective and high-performing solution that will appeal to many commercial applications within the aerospace and medical sectors.”
Furthermore, the FlexiFinish post-processing database (a go-to finishing information catalogue) provides the ability to process a wide range of materials, geometries and initial surface roughness, making it a desirable alternative for many manufacturing businesses needing to implement complex finishing strategies.
Simon Rogers concludes: “Our collaboration with partners through the MTC has provided the foundation that has enabled the innovation at the heart of FlexiFinish to be created, tested and, ultimately, proven. For instance, our ability to utilise Siemens as a technical partner and access the company’s digital technologies and training support has been invaluable to progress FlexiFinish from its concept to demonstration status. Our subsequent challenge is to ensure it meets the commercial needs of production on the shop floor and this will be the next stage of the FlexiFinish journey.”
- Chemical manufacturer boosts production
- Scada software goes mobile
- Embracing a partnership approach to productivity
- Performance plus efficiency from Siemens' Tia Portal
- New solutions partner
- Siemens expands Sinamics G120P series
- Highly reliable power supply
- Fail-safe virtual controllers
- The changing world of motion control
- Breakdown Avoided Thanks To Condition Monitoring
- No related articles listed