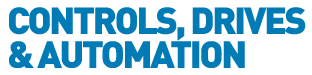
![]() |
Charlotte Stonestreet
Managing Editor |
TOO MUCH CONTROL PANEL HARD WIRING
18 September 2012
With a recent Frost & Sullivan report highlighting the convergence of PLCs and DCSs, Stuart Greenwood of Eaton's Electrical Sector, asserts that this trend is in fact well advanced and already delivering excellent results
As soon as remote I/O modules became available, convergence between PLCs (programmable logic controllers) and DCSs (distributed control systems) was underway. It’s hard to see the convergence of PLCs and DCSs as a new trend since it has already been with us for at least a couple of decades!
But, of course, convergence continues to spread and most modern automation systems of any size now incorporate intelligent devices in the field, such as variable-speed drives with builtin intelligence, and electronic operator interface panels.With all of these devices linked to the central controller via network or fieldbus connections, it does indeed become difficult and almost meaningless to distinguish between the PLC and the remainder of the automation system.
Except, that is, within the control panel itself. The wiring runs are, of course, much shorter inside the panel than outside, but that’s no longer a valid reason to ignore the benefits that bus-based panel wiring, which is perhaps better described as lean panel wiring can provide. This surprising omission in automation technologies has, however, finally been addressed, and at least one bus-based lean panel wiring system – SmartWire-DT from Eaton’s Electrical Sector – is now available.
This allows all of the devices within a control panel to be connected to the central controller, whether it’s a PLC or a smart relay, via a simple daisy-chain connection. Conventional control wiring is eliminated. Special components are not needed. Instead, inexpensive interface units are added to standard components in exactly the same way that an auxiliary contact block is added to a contactor. This cuts panel wiring time dramatically, for instance and, since it virtually eliminates the possibility of wiring errors, the time needed to test panels is also greatly reduced, as is the risk of problems during commissioning.Modifications can be made much more easily – all that’s needed is to daisy chain the new components to those already there.
The biggest benefit is that lean panel wiring facilitates the flow of information between components mounted in the panel. A suitably equipped motor starter could, for example, report the running current of the motor and the status of the protection device to the central controller, where this information could be processed and used to initiate further actions, such as sending a message to the HMI panel alerting the operator to an impending overload condition before a trip actually occurs.
TRANSPARENCY
Adopting lean panel wiring greatly improves the transparency of the automation system. Since fieldbus and network-based field wiring already supports information exchange, the addition of lean panel wiring means that any information about any aspect of the automation system’s operation and status can be made available wherever it’s needed.
This transparency is one of the key elements needed for lean automation, which is one of the reasons that the description ‘lean panel wiring’ for the new busbased panel wiring systems is preferred. This concept slims down control panels, simplifies wiring, increases data transparency and enhances performance, while reducing overall costs.
Key Points
- Traditional hard wiring is still very much the norm inside most control panels
- The uptake of lean automation and lean panel wiring is a more significant trend than PLC/DCS convergence
- No related articles listed