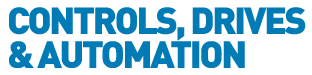
![]() |
Charlotte Stonestreet
Managing Editor |
PLC KEY TO MISSING LABELS DETECTION
30 October 2012
Capable of 0.1 microsecond per Boolean instruction, an ABB AC500-eCo PLC has been selected by a specialist machine manufacturer that wanted a detection system to control the operation of its servo controlled rewinder...
PLCs are one of the most versatile and capable items of control and automation equipment but even these devices are challenged by certain applications. One of these is on a missing label detection system on a label rewinder. Fast, accurate detection of labelling errors on a web is a vital component to maintaining quality of packaged items, particularly pharmaceutical products where accurate, legible labelling is critical.
In general, a PLC program is executed in a repeated cycle as long as the system under control is operating. Data from inputs is copied to an area of memory commonly known as the I/O image table. The program is then run from its first instruction down to the last. It takes some time for the PLC’s processor to evaluate all the instructions and update the I/O image table with the status of outputs.
HIGH SPEED CHALLENGE
Although label detection is not an unusual application for PLCs, the limitation imposed by program execution time does raise certain challenges. Within the industry production speeds are increasing, and an inspection rewinder can handle 2,000 metre long webs at speeds of up to 300 metres a minute. This means that the PLC has approximately 12 milliseconds to interpret the signal that tells it that there is an error in the label web. This requires a very high speed processor – not all PLCs are suitable and if they are not fast enough, they could struggle with the timing cycles involved. If the PLC’s processor responds too slowly, it may not be able to provide the level of accuracy required – for instance, 10 labels CONTROLS labels that still had matrix material attached to them.
The system used the PLC to detect faults on the label web via fibre optic sensors. When a fault is detected, the PLC must signal the motion controller to ramp down the motor speed and send the web to an inspection table at the side of the inspection machine for manual correction.
An ABB AC500-eCo PLC was selected for this application.
This PLC is capable of 0.1 microsecond per Boolean instruction, compared to 1 microsecond and above for other similar products. It offers both Ethernet and serial connectivity, giving maximum flexibility to communicate with other components in the system. The PLC is connected to the motion controller via Modbus TCP and to the HMI via the serial port.
CAPABILITY MATCH
With such a high speed, high throughput application as label inspection, the speed of the PLC must be matched by the capability of the motion controller. The main machine uses a motion controller which can control up to 16 movement axes simultaneously, rather than one after the other.
This means that the movement axes of the slitter rewinder never become out of synchronization with each other, allowing fast, accurate control of the web position.
WITH SUCH A HIGH SPEED APPLICATION,THE SPEED OF THE PLC MUST BE MATCHED BY THE CAPABILITY OF THE MOTION CONTROLLER
Easy, fast programming and set up is another must and the AC500 offers CoDeSys, the most popular programming language for PLCs, plus all four of the other PLC programming languages specified under IE61131. Another useful aspect of the PLC is its Control Builder Plus, a project management suite that combines all the tools needed to configure, program debug and maintain an automation project.
Key Points
• The PLC has approximately 12 milliseconds to interpret the signal that tells it that there is an error in the label web – this requires a very high speed processor
• When a fault is detected, the PLC must signal the motion controller to ramp down the motor speed and send the web to an inspection table
- Saves energy cooling costs
- ABB’s robot training masterclasses now available online
- Paint & OmniCore controller robot training
- ABB motion control guide
- SynRM motor & VSD packages
- White Paper on Control Theory
- Lunch 'n' Learn training puts pressure on water leaks
- Greater speed & torque control
- Eliminates gearbox failure
- VSD cuts saw stoppages