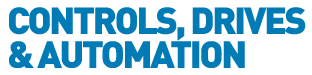
![]() |
Charlotte Stonestreet
Managing Editor |
The patchy case of maintenance in the Food & Drink industry
29 October 2018
In the UK, the food and drink sector employs approximately 900,000 people and has a manufacturing turnover of £20 billion a year.
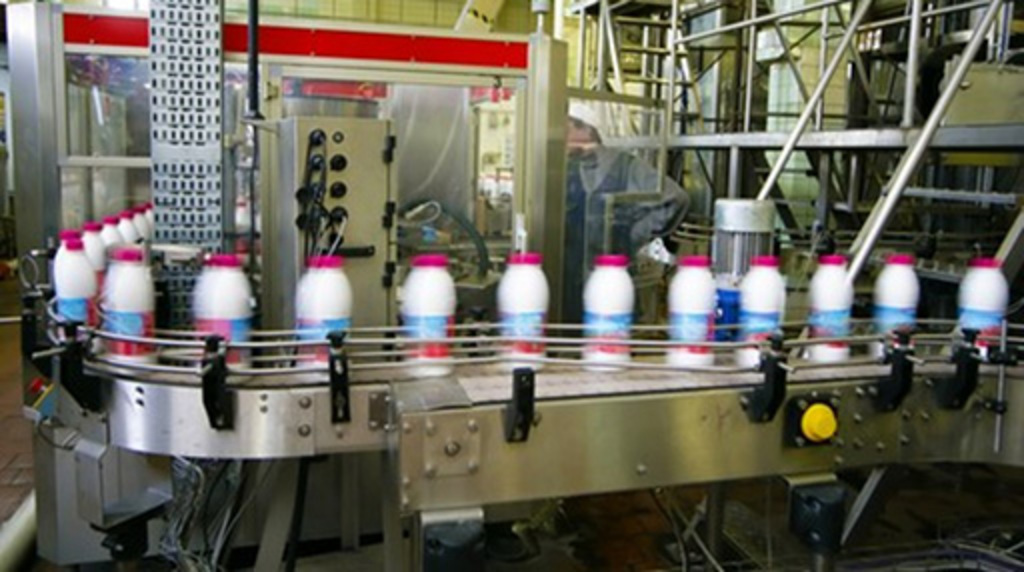
In September 2015, UKCES commissioned a consortium of research organisations led by the Institute for Employment Studies (IES) and SQW to prepare a series of a series of strategic labour market intelligence reports on the challenges and opportunities for increasing productivity in four sectors including manufacturing and food and drink.
The poor productivity performance of the UK economy, especially since the end of the recession of 2008-09, has become a major concern for economists and policy-makers. Productivity growth too has been very modest: as a consequence, the UK, which was already some way behind many other major developed economies, has fallen back even further. The overall level of productivity in the United States’ economy is now 31% higher than that of the UK, while Germany’s is 28% higher.
The study complemented the work of the Business Leadership Group for food and drink manufacturing through an assessment of the factors driving productivity growth in the sector. In particular, it identified the skills that the sector would need to acquire if the UK were to match productivity levels and growth in countries such as Germany, France and the Netherlands.
An additional difficulty faced by food and drink manufacturing is the skills it needs to drive productivity growth – typically science, engineering, and technology related ones - are in high demand in other sectors too, and therefore it needs to identify how it can develop its own talent pipelines if it is to match performance levels in competitor countries.
The penetration of advanced maintenance engineering practices within the UK food and drink industry is patchy. Much of the food and drink industry still operates a breakdown maintenance system and that the available technologies are not being used effectively. Most larger companies do take advantage of modern maintenance practices and technologies to improve their production responsiveness and flexibility. However, SMEs have been largely unable to implement such strategies.
But the price of downtime due to malfunction can be much higher than a good maintenance regime. In many cases, preventative maintenance is the smart economic choice. Even small improvements should result in significant benefits. This approach is less time-intensive than a regular inspection regime and can significantly improve the use of maintenance resources. As plants become more automated, monitoring technologies will be ever more integrated into the manufacturing process.
Traditionally, many SMEs are unaware of advances in engineering and maintenance methods and are reluctant to embrace them to improve their production process and competitiveness. Any novel technology or process tends to be well proven before becoming adopted by food companies.
Technologies such as vibration analysis and ultrasound have made it easier to measure the condition of equipment, giving an insight into the probability of failure during any given period. Thermographic imaging – which shows up 'hot-spots' in electrical installations – are also more widely available.
The move away from reactive maintenance to more proactive systems is not without its challenges. Careful consideration needs to be given to scheduling activities strategically and tactically, to ensure maintenance is as effective and efficient as possible.
Good record keeping is essential, so regular record audits are needed to check on quality. Maintenance workers tend to be hands-on people, so they are not always enthusiastic about completing piles of paperwork.
Preventive maintenance also requires advance planning of the ordering of component parts, to ensure they are in place ready for the scheduled work. Delay can be costly and delivery before work can start can have storage costs – getting the balance right is crucial. Though often neglected, the maintenance perspective can also be informative in determining the best choices for new equipment.
Maintenance and cleaning are two areas where there is a great risk of serious injury or fatality. Frequently, it will not be the company’s own staff carrying out maintenance. Contractors will often do higher-risk work. A risk assessment method statement (RAMS) is essential, and should be asked for by the food manufacturer where the contractor is working.
In this context, planned maintenance is better than the unplanned variety. The most obvious reason for this is that it can be scheduled in ‘down’ periods.
- Remote monitoring in the oil industry
- Faraday Predictive Launch combined Condition Monitoring and Energy Monitoring systems
- Ultrasound solutions for predictive maintenance
- Emerson confirm event partnership for Maintec 2019
- Klüber Lubrication receive prestigious innovation award
- Valuekeep launches a new analytics dashboard add-on to their offer
- Three top awards for Western Business Media
- New high temperature chain oil reduces energy consumption
- Bosch Rexroth confirms event partnership for Maintec 2018
- InVMA enables delivery of Connected Healthcare Devices.
- UK engineering professionals to tackle top technical questions live at Maintec 2018
- Smart monitoring for maintenance and part quality
- Modern Maintenance Matters
- Predictive maintenance pushes technology boundaries
- Five essential health & safety updates for business leaders in 2018
- Adapting the supply chain to maintenance needs
- Bosch Rexroth confirms event partnership for Maintec 2018
- Leading trade body BSIF announces support for Maintec 2018
- PTC and InVMA supporting a winning project at Birmingham City University Innovation Fest
- InVMA enables delivery of Connected Healthcare Devices.