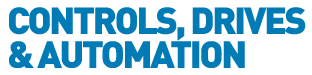
![]() |
Charlotte Stonestreet
Managing Editor |
Adapting the supply chain to maintenance needs
30 October 2018
Nearly every product that comes to market results from the efforts of various organisations that make up a supply chain. Although supply chains have existed for ages, most companies have only recently paid attention to them as a value-add to their operations.
A supply chain starts with the delivery of raw material and components from a supplier to a manufacturer, and ends with the delivery of the finished product or service to the end consumer. Components can range from bearings and power transmission components through to motors, gearboxes, pneumatics and hydraulics, chemicals, tools and health and safety products. With so many places along the supply chain that can add value through efficiencies or lose value through increased expenses, proper supply chain management can increase revenues, decrease costs and impact a company's bottom line.
Supply chain management is the art of streamlining of supply-side activities to gain a competitive advantage. The goal is to develop and implement supply chains that are as efficient and economical as possible. By managing the supply chain, companies are able to cut excess costs and deliver products to the consumer faster. This is done by keeping tighter control of internal inventories, internal production, distribution, sales and the inventories of vendors.
Central to a successful maintenance and asset management strategy is the effective sourcing and management of maintenance, repair and overhaul (MRO) spares. The supply chain for these engineering spares – and how it is managed - has a direct relationship on the ability of a company ability to optimise its manufacturing operation.
Having access to the right spares, when and where they are needed, is critical to maintaining continuity of production and avoiding costly downtime. Best practice is geared around both optimising inventory held at site, which should be routinely profiled to ensure accuracy and alignment with consumption of key components, and a focus on standardisation of key products and technologies throughout the plant.
The availability of spares needs to be balanced against other commercial considerations, such as the need to minimise inventory and therefore reduce working capital. Spares stock purchased ‘just in case’ often becomes non-moving stock, tying up cash at the time of purchase and then often ultimately becoming obsolete and requiring a balance sheet write-off.
Standardisation – identifying which machines require the same spares (even across different sites) and then sourcing these from a single supplier or specialist distributor – can radically reduce stockholding and working capital. A detailed review of what components are being sourced and from where, will highlight areas of duplication and allow the supplier list to be radically trimmed.
Data on stockholding and usage can be managed across multiple sites to ensure, for example, that numbers of a particular spare part are not accumulating in one location while the same product is being purchased at another to meet demand there - further reducing working capital.
Using a distributor may reduce lead times as it will hold many common items in stock, especially when the OEM may be overseas and may itself be importing the spares in question.
Shopping around to multiple suppliers may be a false economy if it builds in additional transactional costs and overhead inefficiencies. Avoid the acquisition of greater quantities of an item than are actually needed to obtain a volume discount, as this ties up cash in non-moving stock which may become obsolete and end up being written off.
Some companies are even outsourcing the whole MRO spares inventory management function itself to a third party, which takes responsibility for identifying which spares are needed and how frequently, and ensuring availability on site for plant-critical items.
- Smart monitoring for maintenance and part quality
- UK engineering professionals to tackle top technical questions live at Maintec 2018
- Maintenance in the digital world
- Valuekeep launches new Asset Management module on mobile offer
- Adding Value - Increasing safety and protecting valuable resources
- Klüber Lubrication receive prestigious innovation award
- InVMA acquires the Intellectual Property and Assets of IoT communications company AMIHO Technology Limited
- IMECHE Head of Engineering Jenifer Baxter and GSK Maintenance Strategy Manager Paul Adams announced as keynote speakers at Maintec 2018
- SOCIETY OF OPERATIONS ENGINEERS ANNOUNCES SUPPORT FOR MAINTEC 2018
- Conveyor and chain lubrication solutions for food and beverage applications
- UK engineering professionals to tackle top technical questions live at Maintec 2018
- Smart monitoring for maintenance and part quality
- Modern Maintenance Matters
- Predictive maintenance pushes technology boundaries
- The patchy case of maintenance in the Food & Drink industry
- Five essential health & safety updates for business leaders in 2018
- Bosch Rexroth confirms event partnership for Maintec 2018
- Leading trade body BSIF announces support for Maintec 2018
- PTC and InVMA supporting a winning project at Birmingham City University Innovation Fest
- InVMA enables delivery of Connected Healthcare Devices.