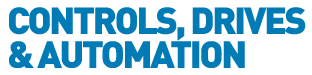
![]() |
Charlotte Stonestreet
Managing Editor |
Smart monitoring for maintenance and part quality
29 October 2018
The concept behind smart manufacturing is to increase process adaptability by benefiting from controlled computer systems. In injection moulding this can be translated to improved plant flexibility: running many products/moulds in parallel; and low material waste. Maintenance and product quality are interlinked and indistinguishable.
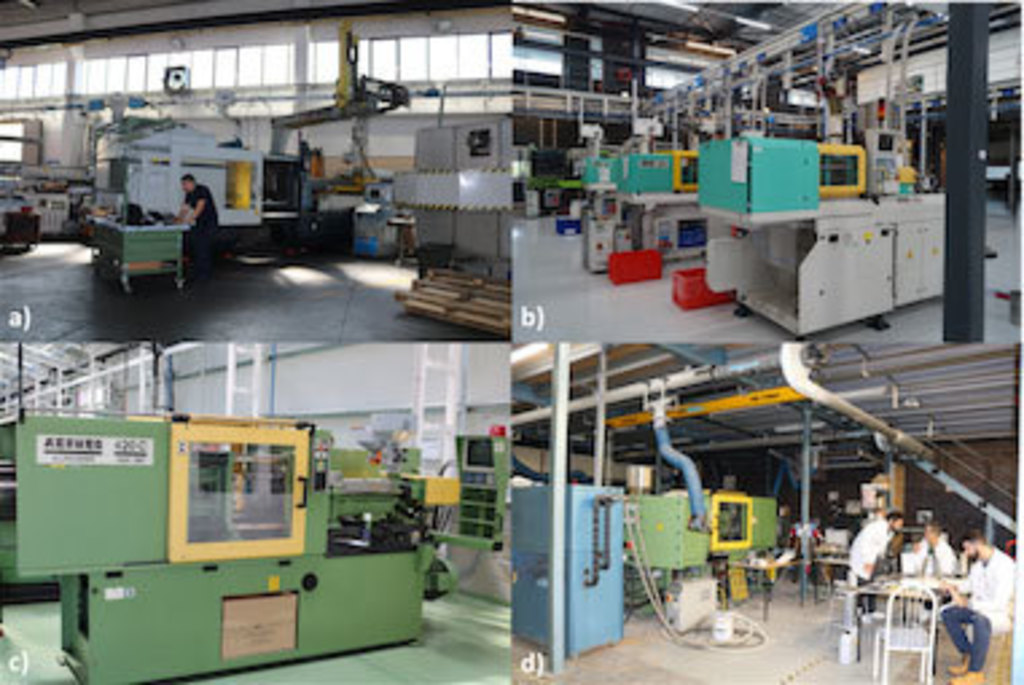
In injection moulding, a majority of reject parts produced by injection moulding are the result of temperature control errors. An exciting programme of work under the EU Horizon 2020 programme is currently drawing to a close. It is aimed at optimising the performance of injection moulding machines on the fly.
PREVIEW is a consortium of experienced European injection moulding manufacturers, leading technological industrial partners and academic research institutes, collaborating to explore merging state-of-the-art data acquisition systems with machine learning techniques to create a process for remotely monitoring and adjusting injection moulding processes. The primary project leaders were Eurecat (Spain), Smithers Rapra (United Kingdom) and Humboldt Universität (Germany).
PREVIEW is capable of recognising process variations and timely executing alerts notifications, suggesting corrective actions to the operator to preserve optimum part quality. By doing so, it makes it possible to keep the production process within part design tolerances, preventing unnecessary material waste, shifting injection moulding from traditional manufacturing to smart manufacturing.
Machine parameters control the cavity temperature and pressure experienced by the polymer as this enters the mould. The use of cavity sensors makes it possible to monitor these parameters, and when combined with the injection moulding parameters of the machine (such as holding pressure, injection speed, cycle time), very high levels of part quality control can be achieved.
A data acquisition system DAS allows operators to retrieve real-time information of the machine parameters. The process is optimised through numerical algorithms based on machine learning techniques that provide the operator with corrective measures to reset the injection moulding parameters and ensure the best possible process performance and part quality. The data collected from the DAS is transmitted via a wireless network and sent via WiFi to the operator’s mobile. A mobile app, downloaded from the PREVIEW website grants access to real-time statistics.
The user is then able to identify via their portable device if a specific injection moulding cycle is running efficiently. As machine operators receive a notification highlighting process inconsistencies they can readjust the injection moulding machine parameters to optimise the production process.
Over the last 12 months, PREVIEW has been positively tested in real manufacturing environments. Each end user represents a different set of challenges and levels of complexity, as the models of injection moulding machines vary, as do the dimensions of the factory floor.
- Klüber Lubrication receive prestigious innovation award
- Ardaunt Facilities Management appointed Valuekeep as their CMMS provider
- Kimberly-Clark, SSG Insight and Pruftechnik confirm participation for Maintec 2018
- InVMA to provide ESAB® Welding & Cutting Products with IoT services and consultancy
- Award winning Hydro Lubricants
- Adapting the supply chain to maintenance needs
- IMECHE Head of Engineering Jenifer Baxter and GSK Maintenance Strategy Manager Paul Adams announced as keynote speakers at Maintec 2018
- The Health & Safety Event to introduce Machinery Safety Zone
- The benefits of centralised lubrication systems
- New-look Maintec hailed a success
- UK engineering professionals to tackle top technical questions live at Maintec 2018
- Modern Maintenance Matters
- Predictive maintenance pushes technology boundaries
- The patchy case of maintenance in the Food & Drink industry
- Five essential health & safety updates for business leaders in 2018
- Adapting the supply chain to maintenance needs
- Bosch Rexroth confirms event partnership for Maintec 2018
- Leading trade body BSIF announces support for Maintec 2018
- PTC and InVMA supporting a winning project at Birmingham City University Innovation Fest
- InVMA enables delivery of Connected Healthcare Devices.