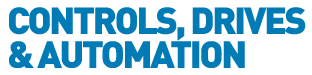
![]() |
Charlotte Stonestreet
Managing Editor |
Digital transformation brings productivity gains
28 June 2021
In recent years, Industry 4.0 has become vitally important to manufacturing, and while there are successes, many digital transformation projects do not live up to their promise. Organisations must learn to understand the fundamentals of digitisation and achieve the desired business results, writes Mark Yeeles
RECOGNISED BY by the World Economic Forum (WEF) as a Lighthouse manufacturing site, the smart factory in Batam, Indonesia, has used digitalisation to reimagine the role of the workforce. When the Batam factory began its transformation in 2015, many low value-added manual and administrative activities in its process operations were identified. By 2017, it was recognised that it was necessary not only to modernise technology, but, more importantly, to also leverage digitisation to drive employee enrichment. The transformation goals included improved work quality (allowing people to execute their work in a simpler fashion) and the enablement of faster and more accurate decision-making.
Digital transformation is not only about technology adoption; it's about people and culture change. The upskilling of people and rescaling of processes requires involvement of factory workers at the very beginning of the journey.
Getting employees on board can be difficult, and it requires a structured and disciplined approach. The goal is not only to gather inputs regarding how to improve workflow, but also to have them come away with the belief that digital technologies can help make processes easier. The emphasis should be on changing mindsets and breaking down workplace silos to empower shop floor personnel to work smarter and easier.
External ecosystem
To make digital transformation a reality, it’s important to significantly widen your circle of influence. Looking to outside sources such as local universities, the government and associations like the World Economic Forum can accelerate your transformation programme. For example, working with local universities provides the opportunity to recruit students who are seeking to learn and implement out-of-the-box ideas which, over time, contribute to achieving a digital mindset.
Using the Batam lighthouse factory as an example, efforts to use digitisation to reduce waste and energy consumption also dovetailed with the Indonesian government’s Low Carbon Development Initiative. By contributing to the goal of less carbon-intensive, more efficient energy systems, the lighthouse is helping the government to deliver on its goal of an average of 6 percent GDP growth per year through to 2045 – contributing to gains in employment generation, increased incomes, and poverty reduction. This strategy will help cut the country’s greenhouse gas emissions nearly 43% by 2030. The government now looks to the Batam lighthouse factory as a national showcase and actively supports efforts to drive business growth. Associations like the World Economic Forum also help to validate efforts and to provide guidance for future improvements.
Vertical & horizontal integration
Many organisations assume that digital transformation occurs in a vacuum, only benefiting those within a particular building or business organisation. The true benefits, however, come when efforts are made to link and connect vertically within the organisation (e.g. from the machine sensor, to the SCADA system, to the ERP) and also horizontally beyond the organisation to external partners such as upstream suppliers and downstream distribution centres.
Regarding horizontal integration, Batam’s lighthouse factory worked with key component suppliers to establish a list of shared product quality parameters for products that were coming into the factory. This avoids duplication of effort in quality control, only having to inspect for quality once instead of twice (assuring quality of the parts before they arrived in the factory). Certain systems were also linked to remotely monitor production of the machines that supplied parts, seeing up-to-the-minute what the supplier had in stock and how that matched up with company needs.
With an environment that’s both unpredictable and rapidly changing, global organisations must increase the resilience and agility of their operations. Modernisation and innovative use of digital tools has the ability to offer more certainty and assist organisations in positioning themselves for long-term, sustainable growth.
Mark Yeeles is VP industrial automation UK&I at Schneider Electric
Key Points
- Schneider appoints new VP for Secure Power division UK&I
- Software-centric
- Schneider launches new cobot
- Industrial automation architecture evolution
- Cutting-edge application control
- Schneider Electric & AVEVA extend partnership
- Young innovators take part in Primary Engineer programme in partnership with Schneider Electric
- Schneider’s commitment to sustainability recognised
- IIoT & AI solution for mining
- Combined balance & control
- No related articles listed