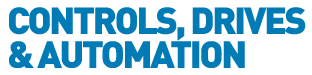
![]() |
Charlotte Stonestreet
Managing Editor |
Home> | AUTOMATION | >Machinery Safety | >Keeping safety in the loop |
Editor's Pick
Keeping safety in the loop
19 September 2013
The innovative SICK Flexi Loop is said to mark a major step forward in machine safety, providing a simple connectivity solution for safety and plant design engineers to meet recent regulatory changes.
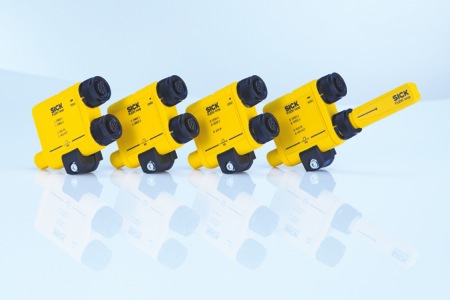
The SICK Flexi Loop offers high levels of scalability, diagnostic insight and I/O connection capacity within a compact space and at a competitive cost. It is ideal when upgrading automation, robotics and modern manufacturing processes.
"It has been fairly common practise to connect interlocks and other safety contacts in series but today’s engineers are faced with increasing demands to meet PLe levels of safety using the convenience of series connection,” says Dr Martin Kidman, Safety Specialist for Sick UK. "However, changes to key safety standards means that traditional hard wired series connection of switches using volt free electro-mechanical contacts is no longer advisable in higher risk applications. Having to accommodate all the equipment, cabling and connections required to comply can add to the cost and cause space problems.
"The new SICK Flexi Loop permits the series connection of dual channel devices, whilst allowing high diagnostic coverage and eliminating the potential for so called fault masking. It is a fully open system and can accommodate standard sensor/switch devices from any vendor. As a field I/O system, it allows a designer to connect any safety system in series with another without any compromise of the safety system performance to PLe integrity.”
With a capacity to cascade up to 32 safety sensors/switches on one loop and to create up to eight separate loops, the IP67-rated SICK Flexi Loop will provide up to 256 sensors on eight dual channel inputs, reducing the clutter of traditional connections. The Flexi Loop is simple to install as a fully cascadable system, using standard cable with M12/5-pin connectors. No special connections or shielded cables are required.
The SICK Flexi Loop provides intelligent built-in diagnostics without the need for a field bus or complex network addressing, resulting in a decentralised cost-effective solution to monitoring the status of each safety sensor/switch connected to it. As well as indicating which device has switched, and why, LED indicators on each node give live status information, and avoid referring back to a desk-based control point.
This diagnostic capability is an advance on SICK’s widely used Flexi Soft controller platform which allows status monitoring at the controller or via the HMI/PLC interface.
Each Flexi Loop module indicates loop status, plus each of the safe and standard inputs and standard outputs. There is a Flexi Loop module that will indicate the status of up to 31 modules and one which allows power injection to accommodate high power usage from devices such as laser scanners, solenoid interlock activation and light curtains.
"The operating range is impressive and measures up to the demands that will be made of it,” continues Kidman. "Each Flexi Loop can be up to 960m and the distance between Flexi Loop modules 30m apart. Each Flexi Loop module assures PLe as long as the sensor can fulfil that performance level, and makes calculating complex SIL or PL parameters for your safety system a doddle.
"The free SICK Flexi Soft Designer Software provides pre approved safety function blocks, simulation and all safety declaration documents at a press of the button.”
A SICK Flexi Loop system allows the user to cascade all devices in a loop reaching up to 960m to one safety shut off channel and still provide a PLe grade performance level. The functionality of the existing Flexi Soft system with Flexi Loop enables gateways to be integrated for remote diagnostics information to be passed to higher level control systems. Flexi Soft supports: Profinet, Profibus, CAN open, EtherCAT, SERCOS interface, Ethernet/IP, Device Net and CC-Link.
- OVERVOLTAGE PROTECTION
- MAKING THE MOST OF SAFETY BENEFITS
- EXTEND MOBILE INTO MAINTENANCE
- Electronic Locking
- Machinery Safety Roadshow
- Machinery Safety UCPD Courses
- GUIDE TO EX NA INSTRUMENTATION INSTALLATION
- Safety Relays Meet SIL3 Requirements
- IECEx Approval
- ARE YOUR SAFEGUARDS AS SAFE AS YOU THINK?