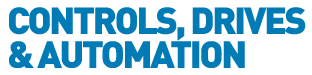
![]() |
Charlotte Stonestreet
Managing Editor |
Home> | MACHINE BUILDING & ENGINEERING | >Machinery Safety | >Disconnect in complete safety |
Home> | MACHINE BUILDING & ENGINEERING | >Materials & Components | >Disconnect in complete safety |
Home> | POWER TRANSMISSION | >Pneumatics & Hydraulics | >Disconnect in complete safety |
Editor's Pick
Disconnect in complete safety
22 April 2014
Many accidents are caused in factories and workshops by hose whip when disconnecting compressed air lines still under pressure. Craig Forrester, Stäubli Connectors UK manager, outlines how this danger can be eliminated.
What is hose whip?
Hose whip is the unrestrained movement of the compressed air line and attached connector caused by disconnection of the circuit while still under pressure. The rapid expulsion of compressed air causes the hose and connector to flail around rapidly, potentially causing serious injury particularly to the face and eyes. Hose whip speeds up to 90mph have been measured and the plug attached to the hose becomes a dangerous projectile.
Statistics provided by the Health & Safety Executive indicate that there have been 53 reportable accidents involving compressed air in UK manufacturing in the 2 years to March 2013.
How can hose whip be avoided?
The use of a safety connector can totally eliminate any chance of hose whip by ensuring that pressure in the circuit is reduced to a safe level before the plug can be removed from the socket.
How does the safety feature work?
This can involve a two stage disconnection process. The first push on the disconnect button allows controlled decompression of the downstream system, while the plug is retained safely in position. A second push allows the plug to be completely disconnected. In fact, Stäubli have recently made this sequence automatic requiring only one press on the button to start the safe disconnect process with automatic disconnection as soon as the pressure is low enough. Simply pressing the disconnection button once, triggers a controlled sequence of actions inside the coupling to allow disconnection in total safety. First the upstream compressed air circuit is closed, followed by decompression of the downstream circuit and finally automatic disconnection of the plug as soon as the pressure is low enough. Absolute safety is guaranteed since airflow is totally impossible as long as the plug is not connected.
Are there recognised Standards for this design of connector?
Safe connectors must conform to BS EN 983 and ISO 4414 standards and be designed to make it impossible to open the compressed air circuit if the system is still under pressure and the plug is not in a locked position.
Does this system make disconnection more difficult?
A safe compressed air connector should be as easy to use as any other. Buttons can be raised for use where gloves are being worn and automatic connect and disconnect features allow for one-handed operation.
Some designs include a swivel for easier handling and the facility to align the disconnect button in the most convenient position.
Do safe connectors come with any guarantee?
Warranty periods for quick release connectors, when provided at all, are usually for a maximum of one year. When a manufacturer introduces an extended warranty, it is a demonstration of confidence in the design, performance and reliability of their product. Stäubli provide a 5 year warranty period for their range of compressed air couplings providing that the plug and socket are of their manufacture. All couplings are individually tested for operation and tightness prior to despatch, the hardened stainless steel body and robust design ensures long and reliable operational performance.
What would be your advice to companies installing a compressed air circuit?
Determine compressed air requirements at the initial design stage if possible to ensure that a safe and reliable system is installed. Between 15% and 30% of compressed air is lost by leakage between the compressor and the tool so ensure all connections are leak free. Frequently in the development of the workplace environment compressed air requirements are addressed later in the project after many crucial decisions have already been made that could affect the installation. And most importantly make sure that safe connectors are used throughout to eliminate any chance of hose whip.
How can Stäubli Connectors help?
Stäubli’s range of products includes all the connectors needed by compressed air circuits in industrial environments. Their design introduces several innovative safety features to ensure reliable, safe, secure operation over many years and eliminate any chance of hose whip.
Experienced Stäubli engineers are available to provide advice on the most suitable installation and make recommendations on the equipment required for any compressed air application.- Faster, heavier, stronger
- Multi-Coupling connectors save time
- Electrical connectors for reliable, safe and durable solutions
- Clean break, flat face or double shut off?
- Installation-ready for simple integration
- Next generation of high speed pickers
- Robots go mobile!
- Immersing electronics
- Clean-break coupling
- Stericlean robots in food production