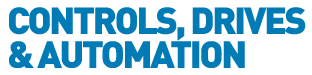
![]() |
Charlotte Stonestreet
Managing Editor |
Tata Steel on a mission to cut energy waste
22 April 2014
A major steel manufacturer is using ABB drives to make its processes more efficient and controllable
As an energy intensive industry, steel making has more potential than most to make energy savings. The UK’s largest steel manufacturer, Tata Steel, is keen to make its processes as energy efficient as possible and has enlisted ABB and several of its authorised value providers to work on a number of applications across its sites.
The company’s facilities in South Yorkshire are saving a combined total of nearly £900,000 a year in energy costs following the installation of ABB variable-speed drives (VSDs) fitted to some of its critical pump and fan applications.
Cutting out waste for a scarfer exhaust fan
The plant at Stocksbridge employs a scarfer, which uses a propane burner to remove impurities from the steel, which are then removed by an exhaust fan.
Originally, the fan was run constantly at full speed, with its output constricted by a damper that opened when more air flow was needed.
This wasted a lot of energy, so Halcyon Drives, an ABB authorised value provider, proposed a 132kW ABB industrial drive. This runs at two speeds, 30 percent on standby and 100 percent during scarfing. Running at 30 percent means there is minimum delay when the motor is ramped up to full speed to extract the gases from the scarfer.
As well as saving energy costs of around £9,700 per annum, the new drive saves 82,500kg of CO2, with a payback time of under a year.
Fume extraction cuts a quarter of a million in costs
Saving nearly £10,000 is a useful sum but even bigger savings came for other projects. Tata’s Aldwarke Bloom Caster complex saved £250,000 a year following installation of VSDs on its fume extraction system for the two casting machines and two ladle arc furnaces.
ABB system integrator Drives and Automation replaced existing fixed speed direct-on-line motors with low voltage motors, controlled by four ABB drives, two at 400kW and two at 570kW.
Other benefits included cutting maintenance by reducing wear and tear on the motors and strain on the duct work.
Flushing away waste
The Rotherham site produces speciality steels for demanding applications. ABB authorised value provider Halcyon Drives supplied, installed and commissioned three 90kW and two 75kW ABB industrial drives to control three flume flush pumps and two filter feed pumps. These form part of a system to remove scrap material from the billets.
All these pumps originally had no form of speed control. An investigation showed that with two pumps running, annual energy used was over 355,000kWh, costing over £46,000 per annum.
A VSD was installed on one of the filter feed pumps. Energy use fell to just over 131,000kWh per annum saving £37,600. For the flume flush pumps, costs fell from £73,500 to £42,000, a saving of over £31,000. Total savings were £68,000 a year.
Extracting excess energy costs
The main extraction system of Tata Steel’s Aldwarke melting shop was identified as being an area where significant savings could be made. This consists of five main extraction fans, which draw the fumes from the shop via a system of dampers and vanes.
The fans were driven by direct-on-line, fixed speed, 3.3kV motors. With no capacity to match speed to demand, these were a heavy drain on the plant’s electrical supply.
Tata Steel chose ABB to supply a complete solution. This included five 690 V regenerative drives with active front-end supply units, as well as five 1200kW motors. ABB adjusted the control loop to allow the VSDs to match the needs of the system, saving £570,000 in energy costs.
As well as these savings, Tata is continuing to investigate other applications with ABB and expects to save a lot more energy in the next few years.
Key Points
- Tata Steel has enlisted ABB and several of its authorised value providers to work on a number of applications across its sites
- VSDs fitted to critical pump and fan applications are saving a combined total of nearly £900,000 a year in energy costs
- Existing fixed speed direct-on-line motors have been replaced with low voltage motors, controlled by ABB drives
- Certified NEMA motor modifications
- Bag loads of programmability
- Flameproof motor
- Power transmission products covered
- ABB's YuMi robot celebrates five years
- Strong case for VSDs
- e-learning on IEC compliance
- Non-invasive temperature sensor
- Help maintenance planning & improve risk management
- Helps avoid unplanned downtime
- No related articles listed