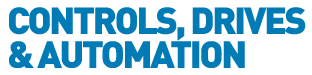
![]() |
Charlotte Stonestreet
Managing Editor |
Editor's Pick
Connected Services keeps robots on track
19 December 2016
ABB Robotics’ Connected Services will help UK manufacturing companies improve the economics and efficiency of operating and maintaining their robots
After a long period of lagging behind the rest of the world, the UK is finally starting to see a growth in the take-up of robotic automation, as an increasing number of businesses start to recognise their competitive potential.
There are 1200 large UK manufacturing companies and 87,000 SMEs (small and medium enterprises. Mike Wilson, ABB Robotics’ General Industry Sales and Marketing Manager, believes that between 10,000 and 20,000 of these are potential candidates for robotic automation and/or Industry 4.0.
In manufacturing, this may be:
- To speed up a high volume manufacturing process
- To make a process more flexible and reduce batch sizes and reduce changeover times
- To make a process more reliable
- To make a process safer.
“We need to bridge the skills gap by implementing more training; make robots easier to operate, maintain, supervise and own; and make the economic case for robotic automation more persuasively,” Wilson says.
As part of the momentum push, ABB Robotics has introduced Connected Services, a sophisticated suite of resources enabling UK manufacturers to maximise robot uptime through fast data access and problem resolution.
Delivered via an interface called MyRobot, Connected Services will make actionable data immediately available to plant engineers and maintenance staff via laptops, tablets and smartphones.
Connected Services comprises four elements:
- Condition monitoring and diagnostics
- Backup management
- Remote access
- Fleet assessment.
Through Condition monitoring and diagnostics, ABB robots can be accurately monitored at all times regardless of location in order to proactively maintain performance. Rather than responding to breakdowns once they’ve occurred, technical issues can be resolved at the earliest indication of problems through alarm notifications sent by e-mail or SMS. As well as immediate critical alarm notifications, Condition Monitoring includes a system snapshot which enables better service preparation for on-site calls and technical support.
Backup management provides a full copy of a robot program so that if lost or damaged, it can be re-uploaded quickly and efficiently, eliminating downtime needed for reprogramming. Automatic backups can be scheduled at any time and can be stored in the cloud or on any server.
Also part of the package, remote access provides quick and secure entry to robot controllers and connected equipment. This means that technical difficulties can be addressed by maintenance engineers without them physically visiting the factory floor, speeding up repairs and enabling them to manage the shop floor more productively.
Finally, many UK companies apply fleet management through GPS to monitor vehicles and their drivers distributing goods or services across the country. Fleet Assessment applies this logic to robots on the shop floor. Through identifying the hardest working robots in a company and benchmarking them against ABB’s entire population of connected robots, performance can be optimised and services applied to extend the lifetime of equipment. Collectively, Fleet Assessment could help the UK to match the most productive robots globally through the assimilation and analysis of global data.
Training upgrades
Backing up this initiative, ABB Robotics has invested over £250k in upgrading its UK training facility at Auriga House in Milton Keynes. It now features the latest generation of robots and controllers – additions include ABB IRB 1200 units in new cells which have also been refurbished with guarding. New robot controllers, together with the MultiMove and SoftMove programming software, allow UK manufacturers to improve safety and robot performance.
Collaborative robots (COBOTs), such as ABB's YuMi launched in early 2016, are becoming more significant in manufacturing, particularly in introducing small and medium-sized enterprises (SMEs) to automation. They can work safely alongside humans, doing repetitive or dangerous jobs, with no need for barriers, cages or zones. One of the courses added to the ABB portfolio covers installing a YuMi collaborative robot into a production cell within the shortest possible time.
Key Points
- Connected Services is a suite of resources to enable maximimum robot uptime through fast data access and problem resolution
- Using condition monitoring and diagnostics, ABB robots can be accurately monitored at all times regardless of location
- ABB Robotics has invested over £250k in upgrading its UK training facility to back up this initiative
- No reluctance to save energy
- White Paper on Control Theory
- ABB Robotics welcomes Expert Technologies Group to UK Value Provider network
- Energy costs cut
- ABB appoints UK partner for motion control products
- Powerful Savings
- It’s never too late to save energy using variable speed drives
- Higher throughput, lower energy use
- Total Plant Automation For Power And Water Sectors
- Emergency drive hire
- No related articles listed