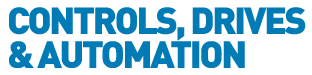
![]() |
Charlotte Stonestreet
Managing Editor |
10 reasons to choose PC-based control
08 July 2014
Despite the fact that PCs have been used for machine control just about as long as PLCs, amongst some there continues to be a misapprehension about their suitability for “real” machine control applications in terms of either reliability or capability. Lucie Thaxter, UK Sales Manager at Beckhoff Automation outlines 10 reasons to choose PCs as industrial control platforms
When we speak of PC-based control we are talking about an industrial control system that utilises a PC designed as a control platform. Not a "white box” office PC available from any number of commercial outlets for a very low cost. While functionally the same, the Industrial PC (IPC) is specifically designed to be rugged and is tested to be a reliable computing platform, with operating specifications for temperature, vibration and shock far exceeding that available for commercial-type PCs. Components used are qualified, standardised and long term available.
So, here are 10 reasons why PC-based control is a very good control platform choice.
1. PC control leverages mainstream computer hardware
Industrial PCs use the same technology used in the millions of PCs produced everyday around the world, including Intel CPUs and chipsets as well as standard memory and other open PC technologies. Manufacturers implement the latest PC technology by creating an industrial hardened version of a standard PC. This result is that the PC control platform is always modern and always current. PCs are familiar to everyone in the world today and industrial PCs are simply an extension of what everyone already uses daily for their work and everyday life.
2. PC control leverages mainstream software computing technology
IPCs, such as those from Beckhoff, use Microsoft operating systems for non-real-time control tasks. This means that the IPC can be used for multiple applications. Not only will it perform as a real-time control platform, but it can also be concurrently used as the HMI platform. It also provides connection to the enterprise network using standard Ethernet (NIC) connectivity. Other non-Microsoft operating systems (Linux, QNX) can also be used.
3. IPCs are lower in cost
Millions of PCs are produced every year and IPC manufacturers can take advantage of the economies of scale to produce lower-cost products. PLC manufacturers create a proprietary highly customised platform, which offers limited ability to grow and change as technology improves. It is very costly to make changes to custom devices. An IPC can be replaced anytime with a lower-cost more powerful model, reflecting the powerful dynamic in the PC world of "increased power at ever lower cost”. Since it is easy to change and upgrade, machines experience longer more supportable longer life.
4. IPCs are more powerful
An industrial PC today uses a multi-core, 64-bit architecture with many gigabytes of RAM and virtually unlimited mass storage, providing a tremendously capable computing platform. Compare this with the typical PLC’s computing capability. The PLC is designed for a single task and it is equipped with just enough processing power to perform that task. There really is no comparison. IPCs allow you to store as many recipes, program and data as you would like with no real limitation. Important files are easily backed up on media such as USB or directly onto network drives. Just like office desktop and laptop PCs.
An industrial PC today uses a multi-core, 64-bit architecture with many gigabytes of RAM
5. IPCs are future-proof
IPCs allow machine builders to migrate from older versions of Windows to the latest versions, while at the same time exploit the latest Intel processors. It is not necessary to re-write any software, you simply update to the latest and greatest processor and operating system. Combined with the use of IEC 61131 standard programming environment and an open connection to the latest I/O network platform, the control solution can be retrofitted at any time without re-writing the entire solution.
6. PC control protects Intellectual Property (IP)
A PC control solution is implemented in software abstracted from hardware! The customer’s investment is maintained in a truly "open” architecture that can be moved from one IPC to another with rarely anything more than a software re-compile being necessary. There is no need to re-invest and re-write already written software. Instead new developments focus on added features and benefits that the end customer can value. This can differentiate OEM machine builders from their competition and make the engineering efforts much more agile.
7. PCs are more maintainable
The IPC control solution uses technology known to the masses. The Windows environment is familiar and more comfortable to more people… and to more of today’s maintenance personnel. The IPC can be maintained using the same methods familiar to every IT professional. Standard backup procedures and media can be used to create complete backup images of every system.
8. PC control provides a simpler control architecture
The power of the IPC combined with a high speed, real-time control network, such as EtherCAT, means that the control architecture can be compressed to a single layer. There is no need for gateways, switches, protocol converters and data links. All control devices are on one Ethernet based CAT5e network.
9. PC control provides better diagnostics
The power of Microsoft is the number of applications available for the operating system. A PC-based control platform easily exports control information for offline processing by third party applications and tools. The result can be very powerful diagnostic and analytical tools that can in turn provide improved performance, maintainability and reliability. All machine documentation can be provided and maintained right on the machine and in multiple languages. Standard PDF and help files can be included right on the machine for the operator. Schematics can be called up directly at the HMI along with videos to demonstrate how to maintain the equipment.
10. PC control converts hardware "boxes” to software applications
Beckhoff’s design philosophy is: "Never do anything in hardware that you can do in software." Custom hardware or black box solutions perform an auxiliary function within the control system. The PC control platform has all the necessary computing horsepower to easily replace black box solutions. Beckhoff utilises extremely fast control network hardware. Therefore the necessary sensor inputs get connected as standard I/O. The special application can be implemented in powerful software either in real time using IEC6-1131 programming tools or in standard computing languages such as C++. This greatly reduces the effort to integrate complex third party black box devices.
And finally… a couple more
There are of course other reasons why a PC makes a better control platform than a PLC. For example, a PC control system supports more legacy hardware systems with standard, included hardware interfaces such as RS232/485 or TCP/IP on Ethernet… or PCs provide a remote maintainable system allowing support resources from anywhere in the world to provide technical assistance or software maintenance, without the need for additional devices or interfaces.
Key Points
- The Industrial PC (IPC) is specifically designed to be rugged and is tested to be a reliable computing platform
- IPC manufacturers can take advantage of the economies of scale to produce lower-cost products
- IPCs allow machine builders to migrate from older versions of Windows to the latest versions, and at the same time exploit the latest Intel processors
- Beckhoff strengthens North West presence
- The crucial role of I/O communication
- New multi-axis robot system
- Maximum process speed & precision
- Beckhoff introduces new Solution Provider programme
- Multi-touch advantages
- New addition to automation software package
- Battery production crucial for EV accleration
- Compact multi-touch design
- From efficiency to eco-friendliness
- No related articles listed