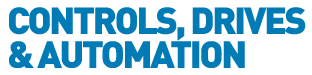
![]() |
Charlotte Stonestreet
Managing Editor |
Home> | AUTOMATION | >Systems | >From efficiency to eco-friendliness |
Editor's Pick
From efficiency to eco-friendliness
12 October 2023
Stephen Hayes explores how connecting automation to sustainability goals can transform businesses and help them contribute to a more sustainable planet

THE INTEGRATION of automation and sustainability is a pivotal step towards creating a more resilient and eco-friendlier world. Despite companies understanding the importance of sustainability, the majority still have a long way to go as only 60% of companies incorporate sustainability in their strategy, and just 25 per cent have sustainability fully integrated into their business model, according to a study by BCG/MIT. However, the integration of automation technologies can serve as a catalyst for progress, as they have the potential to go hand in hand with sustainable goals.
Numerous companies across various industries have embraced automation to advance their sustainability goals. For example, in the automotive industry, Tesla's Gigafactory employs automation extensively to streamline production and reduce energy consumption. By automating material handling and using energy-efficient equipment, Tesla has significantly minimised its environmental impact while increasing productivity.
Another example can be found in the food and beverage industry, where Coca-Cola implemented automation in its bottling plants. With the use of robotics, the company has achieved higher accuracy and consistency in its production processes, resulting in reduced waste and improved energy efficiency.
Real-time data collection
Several tools and technologies support the integration of automation in the pursuit of sustainability. Internet of Things (IoT) devices enable real-time data collection to facilitate better monitoring and optimisation of manufacturing processes. Advanced analytics and machine learning algorithms help identify energy-intensive activities and suggest energy-saving measures. Additionally, digital twins — virtual replicas of physical assets — allow manufacturers to simulate and optimise processes before implementing changes in the real world.
Automation also plays a crucial role in energy efficiency. Completing a power measurement chain from sensors to the cloud can simplify energy management approaches and improve the availability of machines and production facilities. Until now, continuous power monitoring involved a lot of effort, and external sensors would have to have been installed at great cost.
In such scenarios, power measurement terminals – such as Beckhoff's EtherCAT power measurement terminals – play a crucial role in helping achieve sustainability goals in the long term. By replacing external sensors and utilising standard components, these terminals can be easily integrated into existing machines and systems, including retrofitting projects. This seamless integration enables manufacturers to perform continuous, real-time power measurements, providing valuable insights for sustainable operations.
Trend monitoring
With permanent, system-integrated power measurement, manufacturers gain the ability to conduct extensive inline analyses. By monitoring power consumption trends, they can quickly detect deviations from normal patterns. For example, a steadily rising power consumption in a machine may indicate potential excessive wear on its bearings. Identifying such issues early on allows for timely maintenance or repair, preventing further damage and extending the machine's lifespan.
Conversely, a decrease in power consumption can be an indication of quality issues in the production process. By promptly rectifying these issues, manufacturers can improve product quality and minimise energy consumption. This proactive approach ensures that sustainability goals are met by optimising resource usage and minimising environmental impact.
Moreover, sudden drops in power usage can also trigger the need for urgent action within the production facility. It could signify a malfunction or breakdown that requires immediate attention to avoid costly downtime. By having real-time visibility into power consumption, manufacturers can swiftly respond to such situations — minimising production disruptions and maximising operational efficiency.
The data provided by power measurement terminals not only facilitates prompt corrective actions but also empowers manufacturers to make data-driven decisions towards long-term sustainability. By analysing the collected power data, manufacturers can identify areas of improvement, optimise energy usage and in turn, reduce carbon emissions. This comprehensive understanding of power consumption patterns enables manufacturers to make informed decisions that align with their sustainability objectives.
Stephen Hayes is managing director at Beckhoff UK
Key Points
- Numerous companies across various industries have embraced automation to advance their sustainability goals
- IoT devices enable real-time data collection to facilitate better monitoring and optimisation of manufacturing processes
- With permanent, system-integrated power measurement, manufacturers gain the ability to conduct extensive inline analyses
- The crucial role of I/O communication
- Seamlessly integrates machine vision into automation technology
- Revolutionary linear transport system
- Ultra-compact IPC
- New automation technologies
- FANLESS COMPACT PC CONTROL
- Expanded Toolset
- Take control of productivity
- Larger Movement Of Inertia
- Ultra compact IPC
- SWISSLOG SECURES MAJOR ORDER
- IMPROVED PERFORMANCE & RELIABILITY
- Engine Facility
- BULK AUTOMATION
- Integrated Packaging Solutions
- INTEGRATING ELECTRIC AND PNEUMATIC CONTROLS
- Rockwell Automation expands Midrange system portfolio
- Yokogawa joins Friends of the Supergrid
- Festo extends reach of VTUG and MPA-L valve terminals
- Siemens extends TIA Portal engineering framework