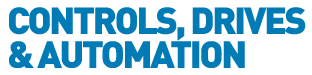
![]() |
Charlotte Stonestreet
Managing Editor |
Home> | AUTOMATION | >Sensors | >Packaging sensors that always see the light |
Editor's Pick
Packaging sensors that always see the light
06 August 2014
Is your packaging conveying line still living in the dark ages, with its sensors blind to transparency, bedazzled by reflectivity or groping for black matt packs and labels? Now, according to Phil Dyas, SICK (UK) industrial sensor specialist, new technologies mean sensors can ‘see the light’ no matter how challenging the pack design.
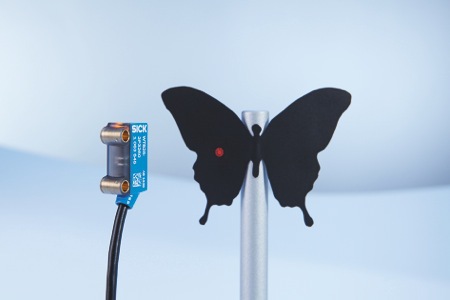
Advances in food and beverage packaging design and technology are providing manufacturers with a glittering new world of choices for packs, cartons and bottles. However, those same designs that test well in focus groups, can cause a major headache for packaging line operation. Yet, optimal productivity remains critical for food processors supplying the competitive retail market.
Sensors which identify individual packs for critical automated processes such as counting, picking or quality monitoring find many modern pack designs more or less invisible.
The use of transparent, reflective, dark or black matt packs could increase a line’s reject and wastage rates to a point where the operation starts to be uneconomic. Unusual, angled or rounded pack shapes are also becoming more popular but could cause stoppages and downtime. Similarly, the temptation to maximise capacity to increase throughput and reduce costs per unit could result in crowding packs so close together that many sensors miss the millimetre gaps between packs. The unpalatable solution might have to be spacing out the packs and losing an opportunity for increased profitability.
It could be that every time a sensor stops working on a 24/7 contract line, it is taking a couple of hours to replace, hours that can’t be made up when running the line continuously.
Are you gritting your teeth and recognising any or all of the above issues? If so, the volume sales generated by today’s and tomorrow’s ‘jump-from-the-shelf’ food packaging designs may be passing you by, or going to your competitors. Either that, or uncomfortably high reject rates could be dragging on your profitability.
Detect all
The solutions lie in sensing technology advances that allow you to say ‘yes’ to new packaging ideas from marketing, or to take on any variety of contract lines, knowing the margins that got you the job won’t be eroded in the final packing.
The answer is not one all-purpose, all-capable sensor, but in a range which offers the optimum price / benefit performance for a specific task, while providing enough capability to perform creditably outside the peak speciality.
Being able to detect anything is not an idle boast from Sick. It is an approach to sensing technology designed to meet demands for productivity in real industrial applications, where marketing and design conspire to shout louder in the supermarket and on the tablet computer screen.
The New Black
Take black as a background colour for a pack design. Tropical butterflies such as the Parides species from South East Asia use matt black on their wings as a way of hiding from their enemies in their jungle habitats.
The reflectance of light from these wings can be 1% or less thanks to the intricate surface structure. Even the most matt black cards and paints are around 4-5% reflectance. To the average sensor this is still like staring into a black hole.
So, up until now, despite being loved by the designers, matt black has been a virtual ‘no-no’ for high-speed pack conveying lines, as sensors struggle to detect packs, even under bright lighting.
Now a way has been opened to exploit the style, glitz and glamour of matt black designs, with the capabilities of SICK’s new W2S family of high power sub-miniature photoelectric positioning sensors. The W2S can cope with reflectance levels down to 1% with ease, so opens the way to a new family of pack design possibilities.
The four models in the W2S sensors range are contained in a rugged IP67-rated housing that measures only 7.7 x 21.8 x 13.5 mm. Based on the latest high-power PinPoint LED, a high visibility light spot is emitted at sensing ranges up to three metres. The high sensitivity multi- pixel array detector ensures unparalleled sensitivity and capability. There is no range difference in black or white surface detection (B/W shift), eliminating the need to adjust the sensor for pack changes.
The tightly-focussed spot offers precise leading-edge detection, and widely-visible LEDs indicate operating status. The range of models and the sophisticated background suppression software ensures high reliability and consistency whether detecting jet black, brightly coloured, matt, transparent or highly-reflective objects.
Bridging the gaps
Another issue facing the packing line manager can be overcrowding. Cost pressure to fit more and more packs onto the conveyor can be self-defeating if the detector can’t tell when one pack ends and the next starts. The same sensor confusion often occurs with stylish rounded, radiused or facetted corners. Artificially increasing the spacing to help detection is an inadequate and expensive option.
Confronting and solving these problems is the remit of the new DeltaPac multitask photoelectric sensor which boosts packaging productivity by making gap-free pack conveying achievable. Without sacrificing accuracy or risking frequent pile ups, downstream quality and stoppages, it consistently detects a wide range of pack shapes at high production speeds and eliminates the need to separate packs on a line.
DeltaPac can also detect changes in packaging shape, whether folded, radiused or faceted corners, at line speeds of up to 3 m/s and 200,000 units an hour. The IP67 DeltaPac uses light beams from four PinPoint2.0 LEDs to track contours of packaging edges moved across them by the conveying line. As object radii from 1–20mm can be detected (within the 30-40mm range) and signalled to the controller at fast line speeds, a comprehensive variety of pack corner shapes can be handled, including edge-folded boxes.
Now you see me...
SICK’s sensor development engineers have also targetted difficult transparent, semi-transparent, shiny, highly-reflective and uneven packaging surfaces on high-speed lines.
Transparency allows attractively coloured contents, such as beverages, sauces or condiments, to shine through the bottles and jars, and can substitute for more costly all over printing or pigmentation. However, most sensors struggle to pick up a clearly-defined signal and heat shrinking on to packing trays can create further multi-reflective clutter.
The new TranspaTect photoelectric sensor delivers reliable and consistent detection of transparent packaging in pharmaceutical, food and beverage processes. A key development was removing the requirement for a traditional reflector for the light beam, which can be inconvenient and difficult to accommodate and replace this by using a matt surface of a convenient machine component as a reference surface.
For further usability, TranspaTect’s new Auto Adapt feature automatically compensates in sensitivity for sudden contamination of the lens or reference sheet, and then re-establishes the original threshold levels when they are cleaned up. In this way, false readings and line downtime are minimised and intervals between cleanings can be extended without sensor adjustment.
Based on a high-performance PinPoint LED, the TranspaTect detecting range for transparent objects is 0 – 400mm and the background reference range is 150-700mm. The compact sensor is IP66/67 rated, and TranspaTect has ECOLAB certification of its resistance to aggressive cleaning regimes, disinfectants and chemicals for a long, reliable working life.
The final click in place
One of the nightmares for a 24/7 high-speed line manager, whether at the end of a raw material-to-retail production process or as a contract packer, is unscheduled line downtime. A sensor that stops working has to be replaced but it can take many minutes to install and commission. The compact new SICK G10 photoelectric sensor family overcomes the problem with an innovative Q-Lock rapid mounting system.
The G10 meets today’s needs for versatile, cost-effective and high-performance sensing at many points along a process, conveying or handling line, or on doors, gates, access points and elevators.
The robust G10 housing has two holes through which passes a twin-pin mounting bar to click into the clamp, then the clamp is secured to a standard 12mm bar mount with a single click-twist. A row of photoelectric sensors can be installed and commissioned on a conveying line in minutes.
The SICK G10 photoelectric sensor range incorporates a high power PinPoint transmitter LED, with a tight light spot for easy, precise alignment, even on very dark objects and at up to 950mm. With excellent background suppression and the ability to ignore optical interference, reflection and glare, consistency and reliability are assured.
New possibilities for food packaging conveying
With these enhanced performance abilities, the new SICK sensor families could inject new life into conveying line efficiency, and free the constraints on the pack designers’ imagination. With their inherent reliability and comms network compatibility, these four new solutions to some long standing packaging issues should help the high speed packaging operation to make a profitable contribution to a plant’s bottom line.- Miniature vision sensor sets new 3D standards
- Achieve more with mobile robots using SICK modular sensor solutions
- Brings live sensor data to the Cloud
- Customisable photo-electric sensors
- Powerful and compact cube sensor
- How SICK robot safety enables machine tending on wheels
- Sensors showcase
- WHATEVER THE WEATHER
- RFID-monitored safety lock
- Hollow-shaft encoders open up universal compatibility