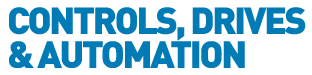
![]() |
Charlotte Stonestreet
Managing Editor |
Bring your machine to life
27 May 2015
Aerotech’s standard controllers are flexible enough to handle almost any control application. From the simple motion of this mechanical wasp’s head, to coordinating the motion of multiple axes in your machine, Aerotech automation controllers provide the flexibility and power required for today’s automation challenges.
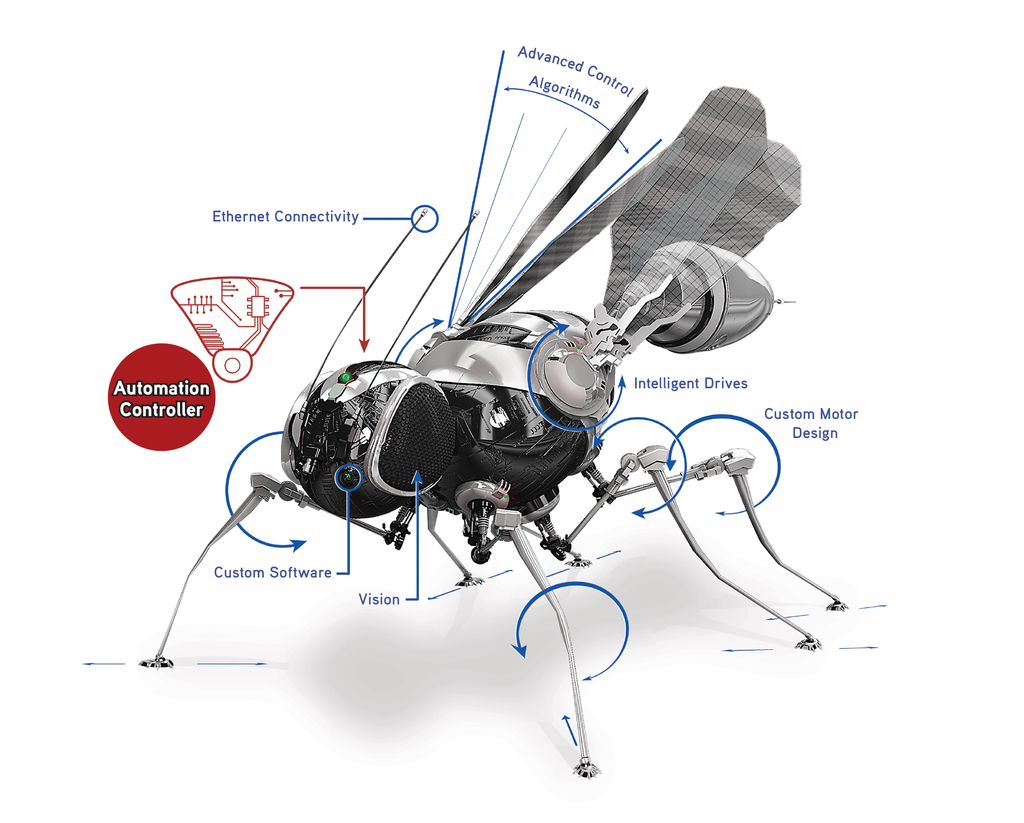
Superior motion is at the center of all controls development for Aerotech. Users can program in a variety of languages including G code, PLC (ladder, function block, and structured text), .NET (C#, VB.NET), C, MATLAB®, or LabVIEW®. All parameters and variables are settable or gettable at runtime and can be initialised statically with an off-line configurator.
If the standard product is not flexible enough for your application, Aerotech will customise the controller for your needs with our plug-in architecture that allows special algorithms to be placed at the firmware, real-time OS, or the application layers – for instance, a plug-in for a special algorithm to manage coordination of the motion of the wasp's legs. Plug-ins we already created include bar code algorithms, special encoder algorithms, and multiple settling criteria that can be monitored in your application code.
Some applications require very specific motion trajectories. The standard controller can control the motion in seven segments for precise position, velocity, and acceleration. However, if this is not enough, we can create special trajectories that you can call from your program and that meet the exact motion needs of your application. If you have a new application, even low volume, we can work with you to customise the software or hardware in our controllers to meet your needs.
- Custom motor design
- High power drive rack
- Autotuning tool
- Cost-sensitive planar performance
- High-performance galvo scanner control
- HARMONIC CANCELLATION
- Precision ball-screw stage with Linear Encoder
- AEROTECH SIGN DISTRIBUTION DEAL WITH ALTECHNA
- Bring your machine to life
- The basics of frequency response
- No related articles listed