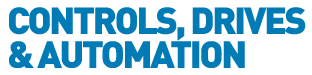
![]() |
Charlotte Stonestreet
Managing Editor |
Home> | CONTROLS | >Motion Controls | >HARMONIC CANCELLATION |
HARMONIC CANCELLATION
21 September 2012
Used to analyse unwanted frame motion during critical moves, Aerotech’s Dynamic Controls Toolbox includes Harmonic Cancellation, which is designed to improve performance by reducing the tracking error due to sinusoidal reference commands, motor force ripple and cross-axis disturbances
The growth of nanotechnology is one factor which has increased the need for the control of precision systems in high-speed, high-accuracy manufacturing and automation.
Aerotech’s Enhanced Throughput Module (ETM) is designed to increase dynamic performance and throughput for high-dynamic micropositioning systems. Unwanted machine frame movements are tracked using sensors and used to adjust the motion profile.
HIGH RESOLUTION
The ETM includes a very high resolution sensor that is simply mounted to the positioning system base or frame, in line with the axis of motion being corrected.When used with Aerotech’s Soloist, Ensemble or A3200 controllers, the ETM software works with the optional Dynamic Controls Toolbox to analyse unwanted frame motion during critical moves.
The Dynamic Controls Toolbox includes software tools to improve settle time, accuracy, in-position stability, and velocity stability, greatly reducing the effects of machine frame motion. These include Threshold Gain Scheduling, Dynamic Gain Scheduling and Harmonic Cancellation.
Harmonic Cancellation is designed to improve performance by reducing the tracking error due to sinusoidal reference commands, motor force ripple (or other positiondependent disturbances), and cross-axis disturbances such as those created in a linear axis by an unbalanced rotational axis. Periodic inputs are common in sensor-testing applications, where accelerometers, gyroscopes, geophones, and other inertial measurement units are shaken with a known profile in order to calibrate their response.
The harmonic cancellation algorithm can either reduce the unwanted higher harmonics in single frequency commands, or better track more complex arbitrary waveforms. The higherorder harmonics are usually due to non-linearities in the stage mechanics and power amplifiers. Machine tools, tracking and surveillance systems, spin stands for data storage, and semiconductor wafer processing all exhibit this behaviour. The harmonic cancellation algorithm can adapt to these disturbances that are periodic on the position of another axis, even if the speed of that axis, and thus the timebased frequency, changes.
Prescott Instruments recently introduced a new multi function rheometer for rubber and elastomer materials testing that uses direct-drive brushless servomotor technology for a sinusoidal motion technique that offers greater flexibility and a wider range of test conditions. The Rheo-Line Multi-Function Rheometer can provide tests at lower frequencies to improve the study of polymer processability. The new rheometer uses a single axis frameless and brushless torque motor with a peak rating of around 20Nm, with a high resolution optical encoder and Aerotech’s Soloist HPe integrated servo drive and motion controller.
LOW FREQUENCIES
The sinusoidal motion continuously oscillates the sample under test at selected low frequencies and is delivered in combination with a fast output pattern from the Soloist that gives the Rheo-Line the time vs. angular position information that is critical for the in-phase and outof- phase measurements recorded by the machine's sophisticated sensors. The synchronisation and accuracy between motion and output needs to be extremely accurate, with a working specification of the order of a just few thousandths of a degree.
Position Feedback data now shows a 100 times reduced error (Fig 3). The Fast Fourier Transform (FFT) of the Position Error showed that the original 33.5Hz harmonic had been eliminated and the third harmonic was now dominant (100.5Hz). To further improve the system response, Harmonic Cancellation was applied at 33.5Hz and 100.5Hz. This reduced the resulting position error +/-0.5 degrees to +/-0.0013 degrees, a 385 times improvement in position tracking from the original error and well within the original specification.
Key Points
- Harmonic Cancellation improves performance by reducing tracking errors
- The method has resulted in position errors being reduced from +/-0.5 to +/-0.0013 degrees at Prescott Instruments
- Precision ball-screw stage with Linear Encoder
- Bring your machine to life
- Geometric performance
- Bring your machine to life
- Piezo nanopositioning stages
- AEROTECH SIGN DISTRIBUTION DEAL WITH ALTECHNA
- Closed-loop servo control
- The basics of frequency response
- High-performance galvo scanner control
- Autotuning tool
- Integrated Motion Control
- New 4th Generation PH Series Servo Planetary Gears are Largest in Class and offer Engineers even more benefits
- Driving Trends & Developments
- EtherCAT I/O is Tightly Integrated into Aerotech's A3200 Automation Machine Controller
- Galvo and Controller Combination Offers Infinite Field of View and 24-Bit Resolution
- Control systems
- Rail Coupling Minimises Downtime
- Custom Motion System For CT Scanner
- Full Servo Motion Advantages At A Fraction Of The Cost
- KEB COMBICONTROL C6