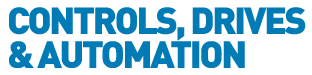
![]() |
Charlotte Stonestreet
Managing Editor |
Home> | AUTOMATION | >Sensors | >Sensors: The unsung heroes of a safer food chain |
Sensors: The unsung heroes of a safer food chain
25 August 2015
Western society’s love affair with sourcing and enjoying food at any time of year, from any part of the globe, has transformed the food processing and packaging industries over past decades, and sensors can play a vital role as this article by Glynn Edwards, SICK UK’s FMCG segment manager, outlines
Whether we are following a celebrity chef’s recipe, or need a meal that’s ready-cooked and chilled, we have the same uncompromising expectations of food safety. As consumers we demand assurances about the quality of the food products we buy, what they contain and where they were produced, packaged, stored and delivered. When food safety goes wrong, the consequences for manufacturers and retailers can be devastating in terms of commercial recalls and loss of reputation.
In the battle for more transparency, information sharing and production control – all necessary to support an ever-more global and complex food industry – one technology perhaps more than any other has been the ‘unsung hero’ that supports and enables the safe food chain. That technology is the sensor. Sensors that track, trace, quality-check and control production are endemic in every production, packaging and logistics process.
As the industry gathers for the 2015 PPMA Show, we’ll be reminded of just how complex and widespread sensors are in process and packaging applications. Visitors to our stand will want to know about the latest technologies and how traceability, quality checking and the highest hygiene standards can be achieved without loss of productivity or throughput. Developments like IO-Link –enabled Smart Sensors and Industry 4.0 connectivity are offering new choices. With such a broad range of options, our customers often need help from us in identifying the best choices for their applications.
Traceability
Manufacturers are legally responsible for recalling unsafe goods and products and must be able to trace back their products from the producer, through the processing stages, to retailers. In the worst case scenario, all affected foods must be withdrawn from circulation as quickly as possible.
Traceability and identification are therefore critical to highly-automated food chains. RFID technology with on-product transponder chips provide the reliability needed for high-value or safety-critical items and have the ability to record data on the chip as the product is processed. 1D or 2D barcoding, whether on labels or marked directly, is a simpler and less costly Ident approach, enabling laser or vision based scanning to record product progress centrally. At the higher performance end of the label reading spectrum, we have sensors that are now capable of combining Optical Character Reading, Optical Character Verification, 2D and barcode reading in a single device.
Process sensors are also essential for measuring key parameters such as temperature, pressure, level and flow in order to provide detailed insight and records of conditions at every stage of processing.
Quality
Sensors that validate product and packaging quality at high production speeds help to reduce waste and avoid costly machine downtime. Vision technology is used in the food and beverage industry to detect not only the position of goods and packaging and measure their dimensions, volume, and contours, but also to confirm the required quality. This technology generates a great deal of process data, enabling better monitoring and automation of production, processing, and packaging processes. Intelligent photoelectric sensors that are flexible and adjustable enhance the quality and efficiency of packaging machines.
Uncompromising hygiene
Just like any food processing equipment, sensor technology has to comply with hygiene requirements. Market globalisation has meant that sensor manufacturers must recognise both EU (e.g. EHEDG) and USA (e.g. 3-A Sanitary Standards) requirements in sensor development. Stainless steel construction, sealing to the appropriate environment standards, including for arduous cleaning and sterilisation procedures, and design of elements such as housings and mounts to avoid microbe traps and dirt retention are essential when supplying food and beverage processors with the instrumentation they need in today’s and tomorrow’s industry.
Developing sensing products for such complex conditions requires specialist industry knowledge and companies like SICK work closely with food and packaging industry colleagues to develop the product solutions the industry needs.
Key Points
- Traceability and identification are therefore critical to highly-automated food chains
- Process sensors are essential for measuring key parameters such as temperature, pressure, level and flow
- Sensors that validate product and packaging quality at high production speeds help to reduce waste and avoid costly machine downtime
- On-premise data intelligence platform
- Intelligent solutions showcased
- IO-Link master & control system in one
- Smart sensors & machinery safety
- Encoders Cut Costs
- I4.0-ready functional safety
- Marginal gains in machinery safety
- Distance sensor sets precision standard
- SICK's advanced IO-Link encoders streamline machine controls
- Picture this: Switching maintenance data to visual