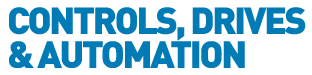
![]() |
Charlotte Stonestreet
Managing Editor |
How IIoT will deliver smarter factories
09 July 2017
The Industrial Internet of Things (IIoT) will digitise and interconnect factory environments. The fitting of myriad equipment with sensors, and the ability to collect, transmit and interpret data in real-time, will provide companies with far greater visibility of their assets than has ever been possible.
This new capability brings the potential for smarter factories based on preventative maintenance methodologies. It will also transform the way that equipment is monitored and repaired out in the field, leading to the emergence of new service-based business models. For maintenance professionals, the IIoT will prompt the use of new technologies such as augmented reality and wearable devices, changing the way they perform their daily roles, and moving them up hierarchical structures.
While much of the early focus on the Internet of Things (IoT) revolved around the development of consumer applications such as smart-home heating systems, it has become apparent that even greater potential lies with the promise of improved networked connectivity within industrial settings. Indeed, major industries like manufacturing, logistics, mining, utilities and agriculture have begun to apply IoT systems in imaginative ways, improving the efficiency and productivity of their organisations in the process.
When broadly described, the IoT refers to networks encompassing the use of standard Internet Protocol technologies to connect people, processes, and things to enable new cyber-physical systems. The Industrial IoT can be viewed as a subset of the broader IoT, where these connections exist mainly to improve the efficiency of production facilities and the way that physical goods are maintained. In an industrial context, the ‘things’ can be a long list of systems and machines that can be fitted with sensors which record data around pressure, level, flow, temperature, vibration and acoustics. This data, combined with sophisticated analytics, can be used to reveal patterns and problems within factories, or with equipment out in the field.
With machines and specialised sensors collecting data at every step of production, the potential gains from the Industrial Internet of Things (IIoT) are enormous. Instead of performing traditional calendar-based maintenance, with the periodic examination of equipment and fixing problems when they occur, the IIoT will help companies capture and analyse data, warning of potential problems before they happen. The tracking of patterns to indicate failure would be an enabler of condition based modelling, unleashing the potential of a truly predictive maintenance regime.
IIoT implementation
The implementation of IIoT, and the impact it will have on the way that maintenance is carried out within industrial organisations, has become a source of much research and demonstration. The SmartFactory programme, for instance, pulls together companies from across Europe to assess the ways that communication technology can merge with classic industrial processes. The goal of the SmartFactory initiative is to transfer new technologies and concepts into the environment of factory automation. These technologies are constantly being tested on a typical industrial production plant, and then further developed and expanded as required.
One of the partners in the SmartFactory initiative is Festo, which has positioned its Scharnhausen valves, valve terminals and electronics plant at the forefront of IIoT adoption. Sensors have been embedded in a vast amount of equipment across the shopfloor, effectively giving Festo a ‘digital map of the plant. This enables it to operate in highly advanced ways. For example, high levels of positional awareness enable employees to cooperate in safe interaction with a flexible robot, which takes over assembly tasks that are ergonomically disadvantageous. An energy transparency system means all energy flows and consumption in the factory can be tracked. And for maintenance engineers, alongside their usual tools, the tablet represents the principal working tool: with the help of an app, they are able to detect and rectify machine faults as soon as possible and directly on-site.
Another imaginative example of IoT-based architecture inside manufacturing environments comes with the ‘Track and Trace’ research project, involving Airbus, Bosch, Cisco, National Instruments and Tech Mahindra. In this case, the vision was clear: imagine a factory where all handheld power tools were connected so that their locations could be identified at the touch of a button. Then think of the possibilities that would be offered if those tools were clever enough to work out the immediate needs of the maintenance task at hand, ensuring for instance that those using the tools could only ever tighten bolts with exactly the force required.
Track and Trace envisaged a world where employees wouldn’t waste time hunting for the equipment they need to do their job. And it was a world where guaranteed repeatability would mean production and maintenance errors were avoided.
The research partners have brought this seemingly futuristic scenario to life, using the IIoT to drive forward tool connectivity and improve quality and efficiency across manufacturing. The system, which has been trialled at Airbus plants in Europe, uses indoor localisation technologies based on Wi-Fi to determine, to within a couple of metres, the position of a Bosch cordless nut-runner on a shopfloor. The advantages were clear: if the nut-runner was missing, the shopfloor worker could access a human-machine interface to pinpoint its position in the work cell. A second, ongoing phase would enable the tool’s position to be combined with the precisely determined location of the component or structure being worked upon, with backend software automatically delivering instructions that specify the exact torque needed to tighten bolts.
Such capability could help manufacturers to ensure repeatability, which is crucial in sectors such as aerospace. Modern civil airliners require 400,000 drilled holes in their structure, with more than 1,000 different tools used to fix nuts, bolts and rivets into their correct positions. There are additional benefits: for instance, the constant collection of data provides companies with a detailed overview of the condition of their tools at all times. This can enable the automation of routine tasks, such as the replacement of worn parts on power tools after a specified number of rotations.
In the future, instead of delivering positioning information to a human machine interface, a Track and Trace system might send data to wearable devices such as optical head-mounted displays. Shopfloor production and maintenance workers might, for instance, be able to look at a part, and receive exact tool positioning and usage instructions to their peripheral vision.
Power by the hour
End-user applications IIoT adoption isn’t restricted to the production plants of OEMs. Some blue-chip industrial organisations are already using it to transform the products and services that they offer. Aero-engine giant Rolls-Royce, for example, has long-since embedded its aircraft engines with sensors so that performance data can be collected and transmitted in-flight. If anomalies are detected, maintenance teams and spare parts can be mobilised for immediate action, once the plane has landed. This approach has enabled Rolls-Royce to expand from an being an aircraft engine maker to become service-based provider, allowing it to charge customers for ‘power by the hour’.
Rolls-Royce has now taken its IIoT capability one step further, moving beyond current levels of proactive monitoring of engine health and inflight performance. In a new arrangement with Microsoft, an expanded network of sensors will be combined with digital technologies such as advanced analytics and connectivity to enable Rolls-Royce to collect and aggregate data from disparate, geographically distributed sources, merging information on engine health, air traffic control, route restrictions and fuel usage to detect anomalies and trends. This additional insight will help airlines to fly routes more efficiently, and therefore reduce delays. It’s a transformative step in IIoT capability that will allow the aviation sector to integrate much broader quantities of operational data.
The ThyssenKrupp industrial group, meanwhile, is another traditional engineering name that has used IIoT technologies to transform the way it does business. ThyssenKrupp was an early adopter of predictive maintenance, installing its lifts with a suite of sensors that can collect and send real-time data to the cloud, with the information provided used to calculate the remaining lifetime of key components and systems, flagging issues before they occur. Valuable machine data, such as door movements, trips, power-ups, car calls and error codes, is collected from lifts located across the world, providing precise and predictive diagnostics to technical teams in real time, indicating where intervention is required.
A recent addition to this capability has seen ThyssenKrupp work with Microsoft to equip its on-site technicians with mixed reality HoloLens headsets, that will provide them with visual indicators in their field of view to assist with repairs. ThyssenKrupp says that its data-driven approach to maintenance has cut lift downtime by up to 50%, and that the introduction of the mixed-reality headsets has the potential to reduce the average length of its maintenance teams’ call-out times to a quarter of current levels.
Both Rolls-Royce and ThyssenKrupp are examples of major companies using IIoT infrastructure on sophisticated, high-tech pieces of equipment. But the increased use of sensor, data collection and connectivity isn’t restricted to such expensive pieces of kit. In the professional cleaning sector, for instance, German sweeper and drier manufacturer Kärcher has developed an IIoT-based fleet management service that gives its customers an overview of all machinery, its present deployment and status. Kärcher uses a range of Vodafone connectivity services, which sees SIM cards permanently installed in its machines, allowing them to transmit relevant information such as overview of operating conditions, charging cycles, runtimes, deployment locations and service needs. The data is delivered for display on customer dashboards, delivered through a web-based portal to smartphones or tablets.
The business benefits to end users are clear: cleaning companies can more effectively monitor and optimise the use of their sweeper and drier fleets, knowing where each piece of equipment is at any given time. Communication with the machines is bidirectional, so that machine settings can be made via the IIoT solution if necessary, better matching performance to particular environments. Machine use is increased significantly, as the detection of service requirements and planning of preventive maintenance reduces machine downtime.
The flexibility of IIoT applications, and the multi-faceted nature of its impact on maintenance programmes, is underscored by its use in what previously has been the distinctly low-tech world of pest control. Rentokil has been collaborating with Google and PA Consulting Group to roll out a range of connected rodent control products particularly to customers in the tightly regulated food and pharmaceutical industries. The new digital pest control services use connected rodent devices with embedded sensors and mobile connectivity. The units communicate with Rentokil’s online ‘Command Centre’ and when they’ve caught a rodent, the technician is automatically alerted while customers are kept informed through myRentokil portal.
In a recent use case, Rentokil used the technology to remotely identify an emerging mouse problem and inform its customer, a large supermarket in the Netherlands, not only that it had a potentially damaging issue in one of its stores, but also precisely where it originated. In consultation with the customer, it agreed an upgrade to the service plan, increasing the service frequency of visits by the local Rentokil technician and targeted this increased activity to maximise impact.
Built on Google’s Cloud Platform, and delivered by PA using Agile software, the technology has proved highly scalable. In the field today, Rentokil has more than 20,000 digital devices running in 12 countries which have now sent more than 3 million pieces of data.
Transforming business models
These use-case examples provide clear indication of how IIoT is transforming companies, across myriad industrial sectors. The Rolls-Royce and ThyssenKrupp instances in particular show how it has the potential to change business models, moving companies away from being a traditional supplier of products and towards a more profitable position of being a solutions provider. That transformative journey is commonly referred to as ‘servitisation’ and involves firms developing the capabilities they need to provide services that supplement their traditional product offerings.
By coupling services to their product offerings, manufacturers put themselves in a far better position to meet the needs of their customers. In return, manufacturers get to offer a full solution, rather than just a product, which in turns brings greater financial stability and stronger customer retention. Essentially, manufacturers do not sell a product but instead enter into an agreement to help customers achieve their objectives. It’s about relationships, not transactions. And that will have a huge impact on maintenance frameworks and the role of the maintenance engineer.
ThyssenKrupp is clearly on the road to servitisation. Instead of providing lifts to places like shopping centres as a ‘products’ which are repaired when they break down, it is starting to servitise what it makes, opening the possibility of getting paid for uptime of even for each lift cycle. So, instead of making money repairing products when they have stopped working, manufacturers in the people-moving business enjoy bigger margins from the reliability of what they offer.
Potentially, then, servitisation could have a transformative effect on wide-ranging industrial sectors. According to Oxford Economics’ Manufacturing Transformation Report, last year the share of worldwide manufacturers using performance-based service contracts jumped to 65 percent. Meanwhile, almost three quarters of manufacturers now rely on services as a key product differentiator. Also, as we enter the era of the IIoT where products will be able to alert service technicians about their requirements in increasingly predictive ways, these sorts of business relationships are likely to get smarter and more rewarding.
Servitisation, then, can effectively be seen as perhaps the most important means of monetising the IIoT. It’s a business model that makes sense for the OEM and the end-user. Makers of equipment, be it lifts, pumps, aero-engines or bearings, are rewarded with a more locked-in business model which sees them better rewarded for the reliability of their products, while customers avoid forbidding upfront capital expenditure costs. Ultimately the producer of the goods manages more of the maintenance, enabling the customer to concentrate on its core business activity, whatever that might be.
Servitisation also has the potential to lead to the design of better performance next-generation products. Data collected by IIoT architecture from real-world operating conditions can be looped back into an OEMs research and development function, leading to smarter design and a shortening of time-to-market for new products.
This article is taken from a White Paper originally written for Maintec for Lee Hibbert.
- Schaeffler to close two UK manufacturing facilities
- Energy sector becomes UK's top target for cyberattacks
- Eight pioneers chart a sustainable future for UK manufacturing
- £37.6m UK Digital Twin Centre announced for Belfast
- CUPRA harnesses 3D printing to boost speed, safety & efficiency
- As Long As The Wind Blows
- Businesses given more time to apply new product safety marking
- New sensor can prevent defects in major structures
- Engineered to reduce emissions & operating costs
- Motor Driven Systems Conference
- No related articles listed