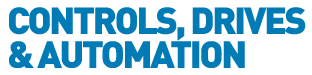
![]() |
Charlotte Stonestreet
Managing Editor |
Current sensors aid predictive maintenance
16 January 2018
Harting presented its HCME series of current sensors for extreme temperatures for the first time at the SPS IPC Drives Fair in late November. Andy Pye was there for the launch
Current sensors have measurement capabilities which can be deployed to improve the monitoring and quality of electrical equipment in automated production. Performance and miniaturisation have had a major effect on even simple types of current sensors. As a result, it is feasible to increase sensor density in production machinery. This means that what has been proven over many years in power transmission and conversion in the energy sector can also be useful in automation and mechanical engineering.
Current sensors offer a simple and compact solution when monitoring frequency inverters. The sensors measure the current consumption of a drive precisely, and by comparing the data over time and with other process parameters, this can provide information about impending malfunctions and therefore play an important role in the predictive maintenance of plants.
These transducers can:
- accelerate diagnosis by mapping the current consumption of all types of motors in industrial plants
- monitor the current flow of battery storage devices and plating systems
- help monitor temperature-critical processes in which electrical equipment plays a role
- trigger the use of grid replacement systems with their measuring results.
The HCME series (HCME stands for Harting Current Measurement Eco) includes seven measuring transducers for currents up to 5500A. They measure direct and alternating currents between 0 and 50kHz. This means they have also caught up with compensating current transformers, for which the bandwidth ranges from 0-100kHz.
Depending on the accuracy required, there are two measuring principles which may be used: Closed-loop (compensating) current sensors are available for demanding measurement tasks. Open-loop (direct-imaging) current sensors) are used for less demanding requirements.
Open-loop current sensors measure AC and DC currents and provide electrical isolation between the circuit being measured and the output of the sensor (the primary current is measured without electrical contact with the primary circuit, providing galvanic isolation). Less expensive than the closed-loop type, open-loop current sensors are generally preferred in battery-powered circuits given their low-operating power requirements and small footprint features.
Fast response
Closed-loop sensors measure AC and DC currents and provide electrical isolation. They offer fast response, high linearity, and low temperature drift. The current output of the closed-loop sensor is relatively immune to electrical noise. The closed-loop sensor is sometimes called a zero-flux sensor because its Hall-Effect sensor feeds back an opposing current into a secondary coil, wound on the magnetic core to zero the flux produced in the magnetic core by the primary current. Closed-loop sensors are often the sensor of choice when high accuracy is essential.
With HCME, Harting has developed a series of open loop current sensors devices in which the accuracy is comparable to that offered by considerably more expensive compensating current transformers (+/- 0.5%).
To supply operating equipment with power, plants also increasingly relies on power rails, which are often made of aluminium and which can be monitored using sensors. In the HCME series, to speed up installation and assembly, the open-loop sensor has been designed for installation on busbars. The devices are very compact: 6cm high and 14.5cm wide. The feedthroughs for the rails are up to 64mm wide and 21mm high (special formats also possible). In addition, mounting lugs on the housing can be used to fix the sensors directly to the current rail with two screws.
The wide temperature range from -40 to +85°C permits use even under extreme environmental conditions. Due to their high reliability, the sensors are ideally suited for use in frequency inverters and in the supply of power to high-performance loads. In addition, HCME current transformers are reliably protected against interference, such as that caused by the magnetic fields of external current carrying lines.
Key Points
- Performance and miniaturisation mean it is feasible to increase sensor density in production machinery
- What has been proven in power transmission and conversion in the energy sector can also be useful in automation and mechanical engineering
- Sensors measure the current consumption of a drive precisely, and by comparing the data over time, provide information about impending malfunctions
- HARTING presents the ix Industrial®, a miniaturised solution for fast Ethernet delivery
- Plug & play Ethernet switches
- Connectivity solutions for IIoT
- Battling big data bottlenecks
- Easy integration of RFID data
- RFID development kit
- Strong revenue growth
- Robust M12 module
- Direct sealing
- IIoT & virtualisation whitepapers
- No related articles listed